
Doug McKenzie
NRG Member-
Posts
216 -
Joined
-
Last visited
About Doug McKenzie
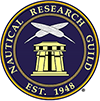
Profile Information
-
Gender
Male
-
Location
New Jersey, USA
Recent Profile Visitors
-
berhard reacted to a post in a topic: Leon by Doug McKenzie - 1:300 - Ship-in-a-bottle
-
berhard reacted to a post in a topic: Leon by Doug McKenzie - 1:300 - Ship-in-a-bottle
-
ccoyle reacted to a post in a topic: Leon by Doug McKenzie - 1:300 - Ship-in-a-bottle
-
Landlubber Mike reacted to a post in a topic: Leon by Doug McKenzie - 1:300 - Ship-in-a-bottle
-
AON reacted to a post in a topic: Leon by Doug McKenzie - 1:300 - Ship-in-a-bottle
-
berhard reacted to a post in a topic: Leon by Doug McKenzie - 1:300 - Ship-in-a-bottle
-
Well, a couple of days has turned into 2 months but whose counting. At least the ocean is done now! My friend Marty and I managed to get the epoxy resin into the bottle without making too much of a mess and the neck of the bottle is quite clean. The basic technique used I saw in a YouTube video about a year ago but I can not find it again so I can not properly give credit other than say thank you. We used the MAX CLR products of The Epoxy Experts of Canada. A 45 minute phone conversation with them was instrumental in the successful creation of the ocean. The first problem was that epoxy normally generates an enormous amount of heat as it cures. When thin films are involved there is no problem as the heat can dissipate easily but in this application a very thick glob of epoxy is curing and the heat could easily damage the bottle. To prevent this, equal parts (by weight) of a Calcium Carbonate Epoxy Filler is mixed with the resin. This filler conducts heat apparently and solves the problem. After mixing these two components we mixed in the hardner (1 part by weight of hardner to 2 parts of resin or 1 part of hardner to 4 parts of resin + filler). All this mixing, by the way, was done with little plastic stirrers driven by an electric drill. Lastly, the blue dye is mixed in. We had about 750 grams of epoxy and we used less than 1 drop of dye to acheive the color in the photo. We broke off the tip of a toothpick and stuck the blunt end into the bottle of dye so that about 3/16" of the toothpick was covered in dye. That was enough to acheive the color in the photo. One alert here- when mixing the dye into the epoxy, it took almost 30 seconds before the epoxy had any coloring at all. The first time I tried this, I thought I was going to have to add more dye - If I had, the color would have been much too dark. Now to getting the epoxy into the bottle. The tools used, in order of use, are 1) the red funnel (the big open part of the funnel is not shown - it screws in to the long narrow part shown), 2) the clear plastic tubing 7/8" ID, 3) the plunger made out of wooden dowels and lastly 4) a strip of aluminum foil bent around the plastic tubing that fits into the neck of the bottle. 6 of these strips were made before starting to insert the epoxy. The aluminum foil covered about 1/2 of the circumference of the tubing. A lot of square pieces of paper towel were made available to assist in any cleanup necessary. Loading the Tubing - The plunger was pulled out of the tubing right to the end (roughly as shown in the photo). The funnel was inserted into the othe end of the tubing and the tubing was held near verticle over a garabage can. The epoxy was slowly added to the funnel and the tubing was filled up with an 1" or 2" to spare. Inserting the Tubing into the Bottle - The aluminum foil was wrapped around the tubing and the tubing extended about 1" further than the aluminum foil. The end of the tubing is wiped clean of any epoxy that may have stuck to it. The tubing was inserted into the neck of the bottle until the end of the tubing was about in the middle of the bottle. The plunger is pushed in to the tubing ejecting the epoxy out to fall to the bottom of the bottle. Extracting the Tubing from the Bottle - Problem - we don't want any dripping of the epoxy to get in the neck of the bottle. Before extracting the tubing, we push the aluminum foil forward so that it captures any drips from the tubing. Then the tubing is extracted, pulling aluminum foil with it. The aluminum foil is tossed into the garbage. It took 5 injections to bring the ocean up to the required level. The working time of the epoxy mixture is beteen 1 and 2 hours so we had no difficulty finishing the job. The surface of the ocean is actually quite flat whereas the picture makes it look concave. There are two little bubbles that are not supposed to be there. Also note that the bottle has been clamped to the workbench. This turned out to be a really good idea because with all the inserting and extraction of the tubing, there would have been problems if it had been loose. Leon is ready so it just remains to fold her up, insert her into the bottle and then raise her up again!
-
berhard reacted to a post in a topic: Leon by Doug McKenzie - 1:300 - Ship-in-a-bottle
-
berhard reacted to a post in a topic: Leon by Doug McKenzie - 1:300 - Ship-in-a-bottle
-
pmckenzie reacted to a post in a topic: Leon by Doug McKenzie - 1:300 - Ship-in-a-bottle
-
AON reacted to a post in a topic: Leon by Doug McKenzie - 1:300 - Ship-in-a-bottle
-
2 changes bring Leon to the point where she is ready to go into the bottle - the bottle, of course, is not yet ready for her! The first change is that the main topmast, previously made of wood and broken in three places, has been replaced by a brass rod which looks much better. The second change is that the braces have been added and require some explanation. All 5 braces are single with no tackle at all. My thinking is that the likelihood of tangling when trying to raise the mast with double or triple braces was just too great. The two lower braces run to the bulwark (not to the mainmast) and so could be installed in a loop fashion - yard arm to yard arm still allowing the two masts to be lowered and raised independently. For the three upper yards, the braces lead to eyes on the mainmast but are only fastened to the port yard arms. This allows the two mast to operate independently. Then when the masts are raised the braces can be fastened to the starboard yardarms. All 5 yards will be able to be braced appropriately and then the braces can be glued in place and the excess cordage cutoff. I've sent off for the 'equipment' needed to 'pour' the ocean so I'll be able to do that in a few days.
-
I realized that there might be interest in a few details so I took a couple of closeups: Pic 1 shows how the shrouds were handled at the foremast top. An 1.0 mm hole (blue arrow) was drilled through the heel of the fore topmast. All 5 shrouds were made from a single thread which was taken up from a notch at the waterline, through the lubber's hole of the top, through the hole in the heel of the fore topmast, back down through the opposite lubber's hole and down to a notch at the waterline, under the bottom (Pic 2) and the pattern repeated. The 2 backstays on the foremast were also included in this single thread. The problem with the backstays was that the topgallant mast and royal mast were so thin that I couldn't drill a hole that the backstays could pass through. I had the same problem with the topgallant and royal yard lifts which need to slip freely at the mast so that the yards can be canted to slip inside the bottle and then be put level again after the ship is in the bottle. Pic 3 show the little wire eye that serves to support both the lifts and the backstays. It's not accurate, of course, but it works pretty well!
-
Things are getting ready for the bottle. Pic 1 shows the masts vertical with the 4 main stays and 5 fore stays rigged to the stick that keeps them neat. The main stays pass through holes in the foremast and then go to the stick. The main stays will be glued and cut off on the forward side of the foremast. The fore stays pass through 1 hole in the anchor deck and 4 holes in the jibboom and then to the stick. The fore stays will be glued and cut off on the bottom of the jibboom. I left out the fore topgallant stay. The missing rigging is the 5-on-a-side fore lower shrouds, 2-on-a- side fore backstays (there are supposed to be 4) and the 5 pairs of braces. The clamp at the foot of the foremast holds it inplace until the shrouds are installed. Pic 2 shows the masts folded aft. Pic 3 shows the yards canted to be more or less parallel the the foremast Pic 4 shows the collapsed model inserted into the neck of the bottle After the rigging is completed, it will be time to 'pour' the ocean. I'm going to be using Max EPC (Electronic Potting Compound) because it generates much less heat than other epoxies.
-
Alan, Thanks for your comments! I used Ships-in-Bottles by Don Hubbard and some youtube videos for my instruction. It is my first ship in a bottle and it is my first ship model to such a small scale. The hardest part, of course, is doing the spars and rigging to scale which is the point of the whole effort. The running rigging already in place will have to be replaced with some new stuff that I just got. Presumably you'll see that in the next post. I've also never made a point of sharing my mistakes the way I have on this blog. Those lovely thin masts have broken 5 times so far but CA glue (thick and medium) have always come to the rescue. Thanks again for your interest, Doug PS the 1:8 sailing 'model' was the dream of a 12 year old building his first wooden shipmodel (Model Shipways Young America) 65 years ago - talk about a labor of love.
-
This will be a short posting. The three lowest yards have been mounted using the same technique: A fine wire is wrapped around the mast, crimped and glued. That wire is threaded through a hole in the yard and it is bent to prevent the yard from coming off. This allows the yard to rotate for entry into the bottle and then rotated back to the horozontal position. The upper and lower topsail yards have a tiny block of wood between them at their centers and the pivot hole is drilled in that block of wood. This was necessary because they are both metal. The lower yard and the upper topsail yard have lifts which pass through athrawtship holes in the mast. Without these holes the yards would not be able to rotate as described above. I haven't figured out yet how to let the topgallant and the royal yards rotate with their lifts yet because the mast is way too thin to take a hole.
-
Pic 1 shows the mainmast folded down and in the neck of the bottle. There appears to be plenty of room for the foremast and its yards (thank heavens!) Pic 2 shows a few new things: 1) A block of wood fastened to the bottom of the hull which allows it to be clamped - I'm using a clamp designed for a drill press. All the instructions that I've seen use a block like this but I didn't use it until I finally saw how useful it is for parts of the rigging process. 2) The foremast is complete (but not hinged) and 3) the head gear is started. Oh and 4) you can see a sailor leaning against the port bulwark rail. The bowsprit is wood but the jibboom and martingale are 1mm brass rod that have been flattened so that 0.50mm holes can be drilled in them Pic 3. I've rigged a single bobstay rather than the correct double because I just could not figure out how to get the second one in there and it might look too cluttered anyway. The martingale stays are in but I won't be installing any head stays below the jibboom - they'll just end at the jibboom after they have been used to raise the foremast. I haven't figured out what to do with the guys yet because they may look too bulky and I can't fit whisker booms because they won't fit in the neck Lastly for this post is the yards Pic 4. Wood is used for the fore yard but wire is used for the upper four yards as they would be just too fragile if made from wood. I'll taper the fore yard but the other four will have to be straight.
-
Need thread about 0.1mm in diameter
Doug McKenzie replied to Doug McKenzie's topic in Masting, rigging and sails
Thanks all! I found some on Amazon - I don't know why I couldn't find this the first time I was looking. -
I have only been able to find thread down to 0.3mm and I'm working on a Leon-in-a-bottle model at 1:300 which requires some 0.1mm tan thread for running rigging. Does anyone know of a source for thread this fine? I've attached a picture that shows the peak halyards as 0.3mm black and you can see that it is way to heavy. The hull is about 4" long. Thanks in advance. Doug
-
Pic 1 shows the hinged mast vertical. Pic 2 shows it folded down. Pic 3 shows the hinge - wire through the base of the mast bent down along the mast and inserted into two holes in the deck just aft of the gallows, Pic 4 shows the shrouds in place. These are all one piece of thread wrapped around the hull and passing through one relatively large hole just above the trestle-trees between the lower mast and the topmast. The two backstays will be placed correctly later. The peak halyards pose a pretty big problem because they are too thick, 0.30mm, they should be 0.10mm. In addition, they should be tan instead of black. I am going to ask one of the forums for help on finding finer thread because this just doesn't look right.
-
Folks, It used to be that I could start to build a posting and then quit MSW and when I came back my work was saved. I could continue to build the posting and then eventially submit it. Now my work is deleted. Is there some way I can have the old functionality back or is this a permenant change? Thanks Doug
-
The main top, consisting of trestle-trees and cross-trees along with the cap (made of thread), is shown in Pic 1. Pic 2 shows most of the rigging for the mainmast as it will appear in the finished bottle. There are only two classes of rigging that are not included yet. One is the main lower shrouds which can't go on until the mast is hinged to the hull. The other is the fore braces. I haven't decided yet whether to put the braces on the mainmast before hinging or after. To have another 10 braces hanging around before they can be fastened to their respective yards seems to be too messy - we'll see. I also haven't decided whether to build the foremast next with its five yards or whether to hinge the mainmast and rig the main lower shrouds and the backstay next.
-
We are starting with the mainmast for two reasons -First, It is thinner than the foremast and therefore a good way to test construction tecniques. The second reason to start with the mainmast is that it folds down independent of the foremast whereas the foremast folds down on top of the mainmast. I sanded a 3/32" x 3/32" piece strip of balsa down to the 1.6mm size at the parners using a sanding stick. My gut says that balsa wood soaked in very thin CA glue will be a) Easy to size and taper and b) Also have plenty of strength, so that is my first try. That same guy Marty suggested using the thin CA to make the card bulwarks strong so we just adapted the idea to the spars. Having tapered the lower main with a square cross section down to 1mm at the head, I realized that drilling the various holes might be easier if I kept the square cross section. Unfortunately, this increases the visual diameter by 41% (the diagonal of the square being the new visual diameter. So what I'm going to try is leaving rougly the top half square, breaking the corners for a bit below and in the lowest part, rounding it off. Making the main topmast the same way and joing them at the doubling gives Pic 2 which is before soaking the mast in CA glue. The toothpick is 1.8 mm in diameter (5/64'). After the very thin CA is applied and sanded, the nice yellow color seems appropriate (Pic 3) for the final appearance of the spars. The glue brought up a lot of the balsa fiber and so a good fine sanding was needed because I imagine that to raise the masts in the bottle easily, we don't want the rigging to be catching on rough fibers on any of the spars. Next we'll be constructing the main top and then start rigging the mainmast.
About us
Modelshipworld - Advancing Ship Modeling through Research
SSL Secured
Your security is important for us so this Website is SSL-Secured
NRG Mailing Address
Nautical Research Guild
237 South Lincoln Street
Westmont IL, 60559-1917
Model Ship World ® and the MSW logo are Registered Trademarks, and belong to the Nautical Research Guild (United States Patent and Trademark Office: No. 6,929,264 & No. 6,929,274, registered Dec. 20, 2022)
Helpful Links
About the NRG
If you enjoy building ship models that are historically accurate as well as beautiful, then The Nautical Research Guild (NRG) is just right for you.
The Guild is a non-profit educational organization whose mission is to “Advance Ship Modeling Through Research”. We provide support to our members in their efforts to raise the quality of their model ships.
The Nautical Research Guild has published our world-renowned quarterly magazine, The Nautical Research Journal, since 1955. The pages of the Journal are full of articles by accomplished ship modelers who show you how they create those exquisite details on their models, and by maritime historians who show you the correct details to build. The Journal is available in both print and digital editions. Go to the NRG web site (www.thenrg.org) to download a complimentary digital copy of the Journal. The NRG also publishes plan sets, books and compilations of back issues of the Journal and the former Ships in Scale and Model Ship Builder magazines.