-
Posts
4,415 -
Joined
-
Last visited
About Landlubber Mike
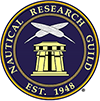
- Birthday 08/17/1973
Profile Information
-
Gender
Male
-
Location
Northern Virginia/Washington DC area
-
Landlubber Mike reacted to a post in a topic: HMS Huron by king derelict - Trumpeter - 1/700 - PLASTIC
-
Landlubber Mike reacted to a post in a topic: Slavic Warrior VII century AD by king derelict - FINISHED - Pegaso Models - 75mm
-
Canute reacted to a post in a topic: USS Alaska by Boeing774 - Hobby Boss - 1:350 - PLASTIC
-
Canute reacted to a post in a topic: USS Bunker Hill by modeller_masa - FINISHED - Flyhawk - 1/700 - PLASTIC
-
Canute reacted to a post in a topic: Fairey Gannet AS.1/AS.4 by AJohnson - Airfix - 1:48 - PLASTIC
-
Canute reacted to a post in a topic: Slavic Warrior VII century AD by king derelict - FINISHED - Pegaso Models - 75mm
-
Boeing774 reacted to a post in a topic: USS Alaska by Boeing774 - Hobby Boss - 1:350 - PLASTIC
-
Dave_E reacted to a post in a topic: Fairey Gannet AS.1/AS.4 by AJohnson - Airfix - 1:48 - PLASTIC
-
Landlubber Mike reacted to a post in a topic: Fairey Gannet AS.1/AS.4 by AJohnson - Airfix - 1:48 - PLASTIC
-
AJohnson reacted to a post in a topic: Slavic Warrior VII century AD by king derelict - FINISHED - Pegaso Models - 75mm
-
Old Collingwood reacted to a post in a topic: Slavic Warrior VII century AD by king derelict - FINISHED - Pegaso Models - 75mm
-
Old Collingwood reacted to a post in a topic: Fairey Gannet AS.1/AS.4 by AJohnson - Airfix - 1:48 - PLASTIC
-
Jack12477 reacted to a post in a topic: Fairey Gannet AS.1/AS.4 by AJohnson - Airfix - 1:48 - PLASTIC
-
Landlubber Mike reacted to a post in a topic: USS Bunker Hill by modeller_masa - FINISHED - Flyhawk - 1/700 - PLASTIC
-
Landlubber Mike reacted to a post in a topic: USS Alaska by Boeing774 - Hobby Boss - 1:350 - PLASTIC
-
Landlubber Mike reacted to a post in a topic: Titanic 1912 by Winnie - Trumpeter - 1/200 - PLASTIC
-
Landlubber Mike reacted to a post in a topic: HMS Hood by Paul Jarman - Trumpeter - 1/200 Scale - PLASTIC
-
Landlubber Mike reacted to a post in a topic: HMS Hood by Paul Jarman - Trumpeter - 1/200 Scale - PLASTIC
-
Landlubber Mike reacted to a post in a topic: Slavic Warrior VII century AD by king derelict - FINISHED - Pegaso Models - 75mm
-
Landlubber Mike reacted to a post in a topic: '34 Ford Chopped Top Coupe by CDW - 3D Resin Printed - 1/25 Scale
-
T-90 by Mikegr - FINISHED - AM - 1/72 - PLASTIC
Landlubber Mike replied to mikegr's topic in Non-ship/categorised builds
Nicely done Mike! -
stagecoach by kgstakes - FINISHED - 1/8th scale
Landlubber Mike replied to kgstakes's topic in Non-ship/categorised builds
Nicely done! -
Thanks Alan - turns out I was nervous about doing it for nothing. I assumed that the paint would come under the metal stencil since there isn't a perfect seal but it worked very effectively.
- 16 replies
-
- Five Star
- Akitsu Maru
-
(and 1 more)
Tagged with:
About us
Modelshipworld - Advancing Ship Modeling through Research
SSL Secured
Your security is important for us so this Website is SSL-Secured
NRG Mailing Address
Nautical Research Guild
237 South Lincoln Street
Westmont IL, 60559-1917
Model Ship World ® and the MSW logo are Registered Trademarks, and belong to the Nautical Research Guild (United States Patent and Trademark Office: No. 6,929,264 & No. 6,929,274, registered Dec. 20, 2022)
Helpful Links
About the NRG
If you enjoy building ship models that are historically accurate as well as beautiful, then The Nautical Research Guild (NRG) is just right for you.
The Guild is a non-profit educational organization whose mission is to “Advance Ship Modeling Through Research”. We provide support to our members in their efforts to raise the quality of their model ships.
The Nautical Research Guild has published our world-renowned quarterly magazine, The Nautical Research Journal, since 1955. The pages of the Journal are full of articles by accomplished ship modelers who show you how they create those exquisite details on their models, and by maritime historians who show you the correct details to build. The Journal is available in both print and digital editions. Go to the NRG web site (www.thenrg.org) to download a complimentary digital copy of the Journal. The NRG also publishes plan sets, books and compilations of back issues of the Journal and the former Ships in Scale and Model Ship Builder magazines.