
dunnock
NRG Member-
Posts
479 -
Joined
-
Last visited
About dunnock
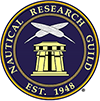
Profile Information
-
Gender
Male
-
Location
Derby UK
-
Interests
Birding, Backpacking, Mountaineering, Model ship building
Recent Profile Visitors
-
Thanks for the compliment on the deck planking Maurice; much appreciated. And thanks for the warning about the potential for issues of thicker planking. I checked the carronades both for the width of the area to plank and for the height of the gun port sill which look fine but I didn't think to check the spirketting. Having just had a look, I think that I may need to trim 0.5mm off the spirketting which I hope won't be noticeable.
-
dunnock reacted to a post in a topic: HMS Harpy 1796 by dunnock - Vanguard Models - 1:64
-
Blue Ensign reacted to a post in a topic: HMS Harpy 1796 by dunnock - Vanguard Models - 1:64
-
Blue Ensign reacted to a post in a topic: HMS Harpy 1796 by dunnock - Vanguard Models - 1:64
-
Blue Ensign reacted to a post in a topic: HMS Harpy 1796 by dunnock - Vanguard Models - 1:64
-
RossR reacted to a post in a topic: HMS Harpy 1796 by dunnock - Vanguard Models - 1:64
-
Oboship reacted to a post in a topic: HMS Harpy 1796 by dunnock - Vanguard Models - 1:64
-
dunnock reacted to a post in a topic: HMS Sphinx 1775 by Ronald-V - Vanguard Models - 1:64
-
dunnock reacted to a post in a topic: HMS Sphinx 1775 by Ronald-V - Vanguard Models - 1:64
-
dunnock reacted to a post in a topic: HMS Harpy 1796 by Glenn-UK – Vanguard Models - 1:64 scale
-
dunnock reacted to a post in a topic: 18th Century Longboat by Desertanimal - Model Shipways - 1:48
-
SiriusVoyager reacted to a post in a topic: HMS Harpy 1796 by dunnock - Vanguard Models - 1:64
-
Richard44 reacted to a post in a topic: HMS Harpy 1796 by dunnock - Vanguard Models - 1:64
-
Nearshore reacted to a post in a topic: HMS Harpy 1796 by dunnock - Vanguard Models - 1:64
-
hollowneck reacted to a post in a topic: HMS Jason by Beef Wellington - Caldercraft - 1:64 - Artois-class frigate modified from HMS Diana 1794
-
brunnels reacted to a post in a topic: HMS Harpy 1796 by dunnock - Vanguard Models - 1:64
-
Planking the Gun Deck The tricky centre section between hatches is finished. I’m using mainly 3.5 and 4.0 x 1mm boxwood strip. I’ve already run out of 4mm strip so now I’m cutting down 5 and 6mm strip. I have also had to use some 5mm strip along the edges of the after hatches to make a fair run. The planks are all straight but I have begun to taper the last planks fitted at the stern. I used the etched deck as a pattern to mark the cut-outs and eye-bolt points. There are still some cut-outs to work on but this section is substantially finished. I now move on to the bow and stern sections before finishing with the runs up to the bulwarks, I will leave as much of the lower deck exposed as is feasible.
-
dunnock reacted to a post in a topic: HMS Harpy 1796 by Glenn-UK – Vanguard Models - 1:64 scale
-
dunnock reacted to a post in a topic: HMS Harpy 1796 by Richard44 - Vanguard Models - 1:64 - FINISHED
-
dunnock reacted to a post in a topic: HMS Harpy 1796 by Glenn-UK – Vanguard Models - 1:64 scale
-
dunnock reacted to a post in a topic: HMS Harpy 1796 by Richard44 - Vanguard Models - 1:64 - FINISHED
-
dunnock reacted to a post in a topic: HMS Jason by Beef Wellington - Caldercraft - 1:64 - Artois-class frigate modified from HMS Diana 1794
-
Thanks to all for the likes and encouraging comments. Preparation for Deck Planking I will not be using the supplied etched deck preferring the look of my own boxwood strip. Before I can begin there are a few things that need doing. First I add the inner counter and transom pieces. These required a fair bit of trimming and sanding to get them to meet closely and to fit between the two stern compartments. They were painted off model with Admiralty Paints Red Ochre. I made up the hatch coamings and gratings a while ago while I was waiting for some parts and managed to remember where I had put them. The kit pieces for the ledges are rounded. I soaked the gratings and shaped them to match the curve. The forward and main hatches will sit directly on the beams but the capstan and hatch forward of it are made to sit on the deck. I have cut a piece from 0.8mm fret and glued it to the base so that it will now sit on the beams and I can plank up to it. Others have commented (@Blue Ensign, @AON, and @Richard44) on the small forward hatch, which is either a steam grating or with cut-outs for the hawsers (or maybe both). To have the hawsers running tight against the riding bitts and immediately forward of the stove looks unusual and awkward so I have scratched another from 4x1mm pear for the coaming and some Caldercraft grating pieces. The hatches are aligned and glued in place using the etched deck. The margin planks are the first to be placed. I made them in three pieces. The forward two pieces are cut from boxwood sheet to cope with the curve at the bow and the third from 4mm stripwood. I can now move on to the main planking but I will need to order some more boxwood from Hobbymill before I can complete it. David
-
Coppering – Finishing Touches Thanks for the encouragement with likes and comments. Positively the final mention of coppering. I have added some boxwood trim around the waterline edge of the plates using 1mm square strip. I have thinned it back and rounded off the edges to make it less prominent and maybe I will darken it off with some stain to reduce the contrast with the pearwood. To finish the trim at that level I have also added pieces 111 and 112 between counter and tuck. A few coats of dilute matt varnish protects the wood and brings up the colour of the planking. Thanks for looking in David
-
Coppering Completed After10 days, I have finished coppering the hull. Diana it isn’t but even so there are over 800 plates to glue in place. The final row to the waterline involved a lot of small pieces which took some time. Any ragged edges will be covered by a boxwood strip. The final piece of this 3D jigsaw is the prow. I ran the side pieces first, continuing down from the keel to the waterline. I overlapped the plates by about 1mm onto the hull and then finished with the vertical plates down the cutwater, again overlapping onto the horizontal plates by 1mm each side. While looking over my work, I noticed that some plates had lifted at the corners so I have been checking and re-glueing those that weren’t firmly stuck down. Thanks for looking in, the likes and comments. David
-
Coppering Continued Just an update on progress. I’m about 2/3 of the way along and beginning to reach the waterline and the need to cut plates. I mark the line with a pencil, score several times and then bend it until it breaks along the line. Minor adjustments and smoothing the edge is done with a fine file. I continue plating towards the stem. I'll get to the same stage on the other side before going back to finishing plating at the waterline. I also have some small pieces to add at the stern David
-
Thank you Jeff and Bob, that's very kind of you David
- 310 replies
-
- Diana
- Caldercraft
-
(and 1 more)
Tagged with:
-
Many thanks Ron and Mort for your very kind comments. It's much appreciated David
- 310 replies
-
- Diana
- Caldercraft
-
(and 1 more)
Tagged with:
-
Coppering the Hull The waterline is marked up based on measurements taken from the plans at stem and stern post and from lower edge the wale directly below the centre of each gunport. To begin with I marked the edge using white pvc graphing tape but it’s not very sticky so I’ve redone it using masking tape. This is my set of tools for coppering. A scrap of dowel with Bluetac to hold and place the plates. Itried’Tacky Wax’ but couldn’t get on with it. Bluetac holds better and I’ve yet to replace it. A burnishing stick; again from scrap dowel, a tool for scoring plates and a cotton wool swab dipped in acetone for cleaning up excess CA. I’m using Rocket Odourless CA glue. The sheets of copper are easily split into individual plates by flexing. I found that the separated horizontal strips can be split into individual plates by flexing 3 strips at a time. Individual plates are cut to shape at the sternpost by scoring and then flexing to split it along the score line. I applied copper tape to the bottom of the keel and sternpost before staring to apply plates from the sternpost at the keel. It's probably overkill but I apply a spot of CA at each corner and a few spots across the rest of the surface to be sure of good adhesion. A rub with the burnishing stick and then every 3 or 4 plates I clean up excess CA with acetone. I have used nearly a complete sheet thus far. There are three sheets in the kit so should be some spares. David
About us
Modelshipworld - Advancing Ship Modeling through Research
SSL Secured
Your security is important for us so this Website is SSL-Secured
NRG Mailing Address
Nautical Research Guild
237 South Lincoln Street
Westmont IL, 60559-1917
Model Ship World ® and the MSW logo are Registered Trademarks, and belong to the Nautical Research Guild (United States Patent and Trademark Office: No. 6,929,264 & No. 6,929,274, registered Dec. 20, 2022)
Helpful Links
About the NRG
If you enjoy building ship models that are historically accurate as well as beautiful, then The Nautical Research Guild (NRG) is just right for you.
The Guild is a non-profit educational organization whose mission is to “Advance Ship Modeling Through Research”. We provide support to our members in their efforts to raise the quality of their model ships.
The Nautical Research Guild has published our world-renowned quarterly magazine, The Nautical Research Journal, since 1955. The pages of the Journal are full of articles by accomplished ship modelers who show you how they create those exquisite details on their models, and by maritime historians who show you the correct details to build. The Journal is available in both print and digital editions. Go to the NRG web site (www.thenrg.org) to download a complimentary digital copy of the Journal. The NRG also publishes plan sets, books and compilations of back issues of the Journal and the former Ships in Scale and Model Ship Builder magazines.