-
Posts
2,205 -
Joined
-
Last visited
About chris watton
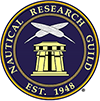
- Birthday 11/21/1966
Contact Methods
-
Website URL
www.vanguardmodels.co.uk/
Profile Information
-
Gender
Male
-
Location
Forest of Dean, Gloucester, UK
-
Interests
Ships and cars.
Recent Profile Visitors
-
dafi reacted to a post in a topic: HMS Adder Rudder/Tiller/wheel.
-
CiscoH reacted to a post in a topic: Chris Watton and Vanguard Models news and updates Volume 2
-
gjdale reacted to a post in a topic: Chris Watton and Vanguard Models news and updates Volume 2
-
DB789 reacted to a post in a topic: Chris Watton and Vanguard Models news and updates Volume 2
-
Pitan reacted to a post in a topic: Chris Watton and Vanguard Models news and updates Volume 2
-
Mike_H reacted to a post in a topic: Chris Watton and Vanguard Models news and updates Volume 2
-
Canute reacted to a post in a topic: Chris Watton and Vanguard Models news and updates Volume 2
-
PaddyO reacted to a post in a topic: Chris Watton and Vanguard Models news and updates Volume 2
-
TJM reacted to a post in a topic: Chris Watton and Vanguard Models news and updates Volume 2
-
chris watton reacted to a post in a topic: HMS Sphinx 1775 by Ronald-V - Vanguard Models - 1:64
-
chris watton reacted to a post in a topic: HMS Sphinx 1775 by Ronald-V - Vanguard Models - 1:64
-
chris watton reacted to a post in a topic: HMS Harpy 1796 by Richard44 - Vanguard Models - 1:64
-
cotrecerf reacted to a post in a topic: Chris Watton and Vanguard Models news and updates Volume 2
-
chris watton reacted to a post in a topic: Chris Watton and Vanguard Models news and updates Volume 2
-
It's going well! The more complex the designs, the longer these things take. A lot of CAD work, so nothing to show as yet. I can tell you the decal sheet is done and has been delivered, and most of the resin print production is done. It is quite a large and complex kit with many pre cut and pre engraved parts, the latter more than even Indy, and all of this takes time to develop. Once I start cutting my final designs and build it up, for Jim to follow, I can post pics of my final prototype build, but until then, it is all just on CAD, on my PC. This applies also to the photo etched files. I need to complete these at the same time the laser cut designs are more or less cooked, and those are 90% done. Rest assured though, this is all I am working on, although I do get side tracked a lot due to having to produce more stock for current kits....
-
chris watton reacted to a post in a topic: HMS Harpy 1796 by Richard44 - Vanguard Models - 1:64
-
chris watton reacted to a post in a topic: Santìsima Trinidad by Kevin - Artesanía Latina - 1/84 - started June 2025
-
chris watton reacted to a post in a topic: Duchess of Kingston by Pitan - Vanguard Models - 1:64
-
chris watton reacted to a post in a topic: Duchess of Kingston by Pitan - Vanguard Models - 1:64
-
chris watton reacted to a post in a topic: Gun Port Lids
-
chris watton reacted to a post in a topic: HMS Harpy 1796 by dunnock - Vanguard Models - 1:64
-
My fault, I really should have added an explanation in the manual. The tiller that you see is auxiliary - there is another tiller arm a little further down the rudder. If you look at the rudder, you can see I simulated the start of the lower tiller arm (a little stub near the top, but lower than the deck tiller arm) If you also showed a picture of the actual rudder, the lower tiller stub would be seen.
-
Very beautiful job you have done. I have sad many times, I am always amazed at the very high quality of work I see on this forum, and your Alert is right up there!
- 38 replies
-
- Alert
- Vanguard Models
-
(and 1 more)
Tagged with:
-
Very well done, Kevin, you should be proud!
- 443 replies
-
- Indefatigable
- Vanguard Models
-
(and 1 more)
Tagged with:
-
Zvr started following chris watton
-
Vanguard MDF
chris watton replied to hornet's topic in Building, Framing, Planking and plating a ships hull and deck
I did already email you with my answer, so here is a portion of that emial I have already sent you you: I have used MDF for the past 18 years, starting at Amati - I am very surprised you did not know this! As I have explained countless time now, for some of the more complex designs, ply was no good, why? Because the tolorances on the thicknesses are comical, they can be anything between 2.7-3.4mm for a 3mm thick sheet. This is OK with very simple kits (just a simple keel and a few bulkheads), but not when so many parts need to slot and interlock well - using ply would be a disaster, as batches can vary a lot in thickness. Also to add, when sanding the bulkheads, it is much easier as the material is all the same. -
NW Ship Builder started following chris watton
About us
Modelshipworld - Advancing Ship Modeling through Research
SSL Secured
Your security is important for us so this Website is SSL-Secured
NRG Mailing Address
Nautical Research Guild
237 South Lincoln Street
Westmont IL, 60559-1917
Model Ship World ® and the MSW logo are Registered Trademarks, and belong to the Nautical Research Guild (United States Patent and Trademark Office: No. 6,929,264 & No. 6,929,274, registered Dec. 20, 2022)
Helpful Links
About the NRG
If you enjoy building ship models that are historically accurate as well as beautiful, then The Nautical Research Guild (NRG) is just right for you.
The Guild is a non-profit educational organization whose mission is to “Advance Ship Modeling Through Research”. We provide support to our members in their efforts to raise the quality of their model ships.
The Nautical Research Guild has published our world-renowned quarterly magazine, The Nautical Research Journal, since 1955. The pages of the Journal are full of articles by accomplished ship modelers who show you how they create those exquisite details on their models, and by maritime historians who show you the correct details to build. The Journal is available in both print and digital editions. Go to the NRG web site (www.thenrg.org) to download a complimentary digital copy of the Journal. The NRG also publishes plan sets, books and compilations of back issues of the Journal and the former Ships in Scale and Model Ship Builder magazines.