-
Posts
302 -
Joined
-
Last visited
About RossR
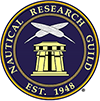
Profile Information
-
Gender
Male
-
Location
Elk River, MN
Recent Profile Visitors
-
Scottish Guy reacted to a post in a topic: Type of glue to use planking a hull
-
dunnock reacted to a post in a topic: 18th Century Merchantman Half Hull by dunnock - FINISHED - NRG -1:48
-
ferretmary1 reacted to a post in a topic: Are you an NRG Member???
-
RossR reacted to a post in a topic: 18th Century Merchantman Half Hull by dunnock - FINISHED - NRG -1:48
-
Fantastic job. This will look great hanging in your home.
- 15 replies
-
- half hull
- Half Hull Planking Project
-
(and 2 more)
Tagged with:
-
KurtH reacted to a post in a topic: Frigate Diana by RossR - OcCre - 1:85
-
cajunrandy214 reacted to a post in a topic: Cutty Sark by Richard Dunn - 1/40 scale - scratch built semi-kit prototype
-
RossR reacted to a post in a topic: HMS Pegasus 1776 by Moonbug - Amati/Victory Models - 1:64
-
RossR reacted to a post in a topic: Frigate Diana by RossR - OcCre - 1:85
-
CiscoH reacted to a post in a topic: Frigate Diana by RossR - OcCre - 1:85
-
Gregory reacted to a post in a topic: Frigate Diana by RossR - OcCre - 1:85
-
Frigate Diana by RossR - OcCre - 1:85
RossR replied to RossR's topic in - Kit build logs for subjects built from 1751 - 1800
With the standing rigging complete except for the top gallant back stays, I have started making the yards. The yards on this kit are fairly simple. They all have a slight taper from the middle towards the end and then a step down to a diameter roughly half the diameter at the center about 1/4 to 1/2 inch from each end of the yard. I start by cutting a dowel about 1 inch longer than the finished yard, and marking the center, the point that the diameter steps down and then each end of the yard. I leave the extra inch of material on one end to put in the chuck of my drill for the tapering. Since the taper from the middle is very slight 1mm - 0.5 mm depending on the starting diameter of the yard, I just use sandpaper to create the taper. After getting the taper right, I use a knife to cut a small slit at the point of the step on the far end of the yard from the end that is in the chuck of the drill and then with a small chisel or knife I cut away material to rough in the smaller diameter after the step. The piece goes back into the drill and I use sandpaper to round the end. I then use the knife and chisel to create the step at the other end leaving the extra material for the drill chuck alone. Then back in the drill and more work with the sandpaper to round the step near the drill chuck. I then cut the extra material off and clean up the ends. I will paint these brown after getting a code of shellac to seal them. I need to make a total of 12 yards. Then attach all of the blocks that will be needed. -
mtaylor reacted to a post in a topic: 18th-Century Merchantman Half Hull Planking Kit by JacquesCousteau - NRG - 1:48
-
dunnock reacted to a post in a topic: Frigate Diana by RossR - OcCre - 1:85
-
RossR reacted to a post in a topic: HMS Indefatigable 1794 by Glenn-UK - Vanguard Models - 1:64
-
Chuck reacted to a post in a topic: HMS Beagle by brunnels - OcCre - 1:60 - first build
-
I have had a similar experience as Brunnels. No issue with it unwinding. I always cut it with a newer sharp blade. I keep a separate exacto knife for cutting the rope and only use it for that so it stays sharp.
- 63 replies
-
RossR reacted to a post in a topic: HMS Beagle by brunnels - OcCre - 1:60 - first build
-
Seeing your progress makes me anxious to get started on my half hull that is sitting on the shelf. Great job.
- 23 replies
-
- half hull planking project
- half hull
-
(and 1 more)
Tagged with:
-
RossR reacted to a post in a topic: 18th-Century Merchantman Half Hull Planking Kit by JacquesCousteau - NRG - 1:48
-
Frigate Diana by RossR - OcCre - 1:85
RossR replied to RossR's topic in - Kit build logs for subjects built from 1751 - 1800
I now have the top mast backstays added for all three masts. These are .018 rope. I served the section at the top that wraps around the mast. I added the top gallant backstay to the fore mast, but I am a little concerned that it will make accessing the pin rails for the running rigging difficult. For the main and mizzen masts I will plan on waiting to attach the lanyard until after the running rigging is in place. If I need to I can remove the lanyards on the top gallant backstays for the fore mast and re-attach later if it helps adding the running rigging. see below fore my concern on the access to the pin rails. -
RossR reacted to a post in a topic: HMS Pegasus 1776 by Moonbug - Amati/Victory Models - 1:64
-
Can’t wait to see your build log for Sherbourne.
- 177 replies
-
- Perseverance
- Modellers Shipyard
-
(and 1 more)
Tagged with:
-
RossR reacted to a post in a topic: 18th-Century Merchantman Half-Hull Planking Project by mtaylor - NRG
-
RossR reacted to a post in a topic: 18th-Century Merchantman Half Hull Planking Kit by JacquesCousteau - NRG - 1:48
-
RossR reacted to a post in a topic: 18th-Century Merchantman Half Hull Planking Kit by JacquesCousteau - NRG - 1:48
-
Did you drill the hole for the bowsprit. You will need to drill through the planking. I attached a couple pics from the instruction where you can see the hole. Not great pics of this in the instructions. If I remember, there is a gap between two filler pieces on either side of the bulkhead former that you will drill into.
-
Are you an NRG Member???
RossR replied to Chuck's topic in How to use the MSW forum - **NO MODELING CONTENT**
I really appreciate that we, as users of this web site are not monetized the way most for profit (and even some not for profit) website would do. Since Model Ship World is sponsored by the NRG, keeping these organizations financially secure is important to me. That is one of my primary reasons I for joined the NRG. The magazine does have features on 20th century subjects, but I will let others chime in regarding yachts specifically. The magazine is very well done and the print version is of a quality you don’t see very often these days in our digital world. Sometimes it is still nice to read something that isn’t on a screen. -
Frigate Diana by RossR - OcCre - 1:85
RossR replied to RossR's topic in - Kit build logs for subjects built from 1751 - 1800
I have continued my work on the stays and made quite a bit of progress. After posting my method for making the mouse, I have to admit that I am surprised that nobody asked why I used square stock instead of a round dowel to make the mouse? I have no idea why I used square stock. I keep all my little scraps of wood and I guess I grabbed the first thing I saw that would work. I did switch to using a round dowel when it occurred to me that I was making a little more work for myself. As I started making the stays higher up the masts and the lines got smaller, I struggled with splicing the line to create the loop. At .018 inch diameter line, I really struggled. After trying and failing a few times I started to get the hang of it and in the end I am really happy with the result of the splices I used to create the eyes on the stays. I also have completed the bowsprit by adding the dolphin stryker. With all of the stays now done, the next step will be adding the backstays and starting to build the yards, boom and gaph. Thanks for all the views and likes. -
Frigate Diana by RossR - OcCre - 1:85
RossR replied to RossR's topic in - Kit build logs for subjects built from 1751 - 1800
I have made some progress on the stays. I have to thank Thukydides for sharing his techniques. Both for the mouse and for splicing the lines to create the loop. I started with the fore stay and main stay. Both of these are made from .044 inch line. This line has four strands and being a little thicker made the splicing a little easier than I experienced with some of my earlier attempts. I start by serving about 1/2 inch of the line. It is hard to see the serving in the photo, but it is the section between the arrows. I then cut the line about an inch from the end of the serving and separate the strands on that section. I then create a small loop and start to pass the four strands through the line below the loop. I try to pass each strand through the line 2 -4 times staggering how far down the line each strand goes. I hope to get a smooth taper after the line is served below the loop. I am creating a false splice and it will not hold under tension on its own. I tie a loop of thin thread around the splice below the loop to secure it. I then serve the line from the loop down to just below the spot that the mouse will go. I add some diluted varnish to help hold the bend in the loop. Next is fabricating the mouse. I start with a 4mm x 4mm peice of wood. I drill a small hole just big enough for the served line to fit through with as snug of a fit as possible. I used a 1.2 mm drill bit for the .044 line and a 1mm bit for the .030 line. After using a knife to create a very rough shape, I put the wood into a drill and use sand paper and a file to round the mouse and refined the shape. After sliding the mouse on the line I add a few half hitches with a thread above the mouse to be sure it doesn't slide up the the line by accident. Thukydides then coated his mouse with a thin fabric to give it a more realistic texture. Since I have trouble seeing the serving at this scale sometimes, I decided to just paint the mouse. I have fore stay, main stay, fore preventer stay and main preventer stay added. I am a little confused as to which is the preventer stay. I am assuming the preventer stay is the one on top. I have that wrong I apologize. The main and fore stay are made from .044 inch line and the preventer stays are from .030 line. I do not think that my results are as good as Thukydides and I would encourage you to check out posts 334 and 434 from his HM Cutter Alert build log. I will be adding the other stays over the next week or two. I also added the gun port hatches. The kit supplied metal frames and hatches. I briefly considered trying to build my own, but I choose to move forward with the kit supplied items. I did choose to paint them. The small size and detail needed pushed my eyesight to its limit. I ended up using a 3x magnifier on my work light. After getting through the ratlines I am really enjoying the rigging process again. Looking forward to starting on the yards. -
Frigate Diana by RossR - OcCre - 1:85
RossR replied to RossR's topic in - Kit build logs for subjects built from 1751 - 1800
I have the bowsprit done less the dolphin stryker. I will hold off attaching that as long as possible. I am convinced I will break it off while working on another part of the ship. If anyone is interested, I thought I would share how I seize a block. There are others, such as Johan on his French Corvette, that produce unbelievable results, but I am not able to duplicate his results with my skill and maybe partially due to the scale I am building at. Here is how I am seizing the blocks. I sometimes use a helping hand device, but usually I just use self closing tweezers. I create a small loop in the line. for purposes of scale the grid on this cutting mat has 1 cm squares. In this case line is .018 mm line from Syren. I then make three loops with loops of thread and tuck one end through the loops. I am Mara thread from Gutterman. It is the 120 size, but I can't explain what those numbers mean. The sizing on thread is a mystery to me. The loop is placed of over the line that is being held in the tweezers and tightened on the line. I will add a couple of overhand knots alternating the sides on the overhand knots to ensure the knot stays tight. I will slide the knot up a little to create an opening just big enough to accommodate the block the place the block in the loop and then use a pair of tweezers to slide the knot up tight against the block. A few more alternating overhand knots to ensure tightness. Then remove the line from the self closing tweezers and create a second loop. I add a couple more overhand knots to create the loop that will go over the spar or yard or what ever you are attaching the block too. Remove the block from the tweezer and place in the item you are seizing it too. Pull both ends of the line tight and add a couple more alternating overhand knots to secure the block. Trim off the excess line and use some diluted varnish or diluted PVA to secure the knot. Use as few overhand knots as you can and still secure it tightly to avoid looking too clunky. Not sure if this is the best way to secure a block, but it works for me and I thought I would share it.
About us
Modelshipworld - Advancing Ship Modeling through Research
SSL Secured
Your security is important for us so this Website is SSL-Secured
NRG Mailing Address
Nautical Research Guild
237 South Lincoln Street
Westmont IL, 60559-1917
Model Ship World ® and the MSW logo are Registered Trademarks, and belong to the Nautical Research Guild (United States Patent and Trademark Office: No. 6,929,264 & No. 6,929,274, registered Dec. 20, 2022)
Helpful Links
About the NRG
If you enjoy building ship models that are historically accurate as well as beautiful, then The Nautical Research Guild (NRG) is just right for you.
The Guild is a non-profit educational organization whose mission is to “Advance Ship Modeling Through Research”. We provide support to our members in their efforts to raise the quality of their model ships.
The Nautical Research Guild has published our world-renowned quarterly magazine, The Nautical Research Journal, since 1955. The pages of the Journal are full of articles by accomplished ship modelers who show you how they create those exquisite details on their models, and by maritime historians who show you the correct details to build. The Journal is available in both print and digital editions. Go to the NRG web site (www.thenrg.org) to download a complimentary digital copy of the Journal. The NRG also publishes plan sets, books and compilations of back issues of the Journal and the former Ships in Scale and Model Ship Builder magazines.