
Nick 843
NRG Member-
Posts
54 -
Joined
-
Last visited
About Nick 843
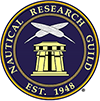
Profile Information
-
Location
Montreal
Recent Profile Visitors
The recent visitors block is disabled and is not being shown to other users.
-
Nick 843 reacted to a post in a topic: HM Armed Cutter Sherbourne 1763 by Nightdive - Vanguard Models - 1:64 - First Build
-
Nick 843 reacted to a post in a topic: HM Cutter Sherbourne 1763 by Pinenuts - Vanguard Models - 1/64
-
Rich Sloop reacted to a post in a topic: HM Armed Cutter Sherbourne 1763 by Nightdive - Vanguard Models - 1:64 - First Build
-
Nightdive reacted to a post in a topic: HM Armed Cutter Sherbourne 1763 by Nick 843 - Vanguard Models - 1:64
-
Nightdive reacted to a post in a topic: HM Armed Cutter Sherbourne 1763 by Nick 843 - Vanguard Models - 1:64
-
Mr Whippy reacted to a post in a topic: HM Armed Cutter Sherbourne 1763 by palmerit - FINISHED - Vanguard Models - 1:64 - First Build
-
Nick 843 reacted to a post in a topic: HM Cutter Sherbourne 1763 by Pinenuts - Vanguard Models - 1/64
-
Nick 843 reacted to a post in a topic: HMS Portland 1770 by Trussben - Portland Scale Ship Co. - 1:48 - 50 gun 4th rate
-
palmerit reacted to a post in a topic: HM Armed Cutter Sherbourne 1763 by palmerit - FINISHED - Vanguard Models - 1:64 - First Build
-
Terrific model! Congrats on finishing! Nick
- 176 replies
-
- Sherbourne
- vanguard models
-
(and 3 more)
Tagged with:
-
Nick 843 reacted to a post in a topic: HM Cutter Sherbourne 1763 by Pinenuts - Vanguard Models - 1/64
-
Nick 843 reacted to a post in a topic: HM Cutter Sherbourne 1763 by Pinenuts - Vanguard Models - 1/64
-
Nick 843 reacted to a post in a topic: HM Armed Cutter Sherbourne 1763 by Nightdive - Vanguard Models - 1:64 - First Build
-
Nick 843 reacted to a post in a topic: HMS Indefatigable 1794 by Clark - Vanguard Models - 1:64 scale
-
Nick 843 reacted to a post in a topic: HMS Harpy 1796 by Glenn-UK – Vanguard Models - 1:64 scale
-
Nick 843 reacted to a post in a topic: HMS Sphinx 1775 by Ronald-V - Vanguard Models - 1:64
-
Nightdive reacted to a post in a topic: HM Armed Cutter Sherbourne 1763 by Nick 843 - Vanguard Models - 1:64
-
Nightdive reacted to a post in a topic: HM Armed Cutter Sherbourne 1763 by Nick 843 - Vanguard Models - 1:64
-
KurtH reacted to a post in a topic: HM Armed Cutter Sherbourne 1763 by Nick 843 - Vanguard Models - 1:64
-
SiriusVoyager reacted to a post in a topic: HM Armed Cutter Sherbourne 1763 by Nick 843 - Vanguard Models - 1:64
-
Pitan reacted to a post in a topic: HM Armed Cutter Sherbourne 1763 by Nick 843 - Vanguard Models - 1:64
-
Three planks a side on now. Virtually no clinker effect, which I'm very happy with. Just a bit of unevenness here and there which some light sanding should take care of. I'm noticing that the change in contour is very subtle. All of a sudden, after 3 planks (and the third didn't really need it), edge-bending on the outer bulwark form gives too much curvature in the plank. I'm finding for now anyway that I can just "iron" the plank in as-is. Nick
-
I'm cooking with gas now on second planking. The system of edge bending and then dabbing some water on a section of plank and working that section with my travel iron, then going on to the next section, is working really well for me. I only have two planks glued on at this point, one each side, but two more just about ready. I'm doing two at a time to match them up either side. My steps (just what works for me): Nip the two planks to match the angle for the rabbet. Sand a bit on the rabbet end as needed. Mark one for the taper cut; double/line up with the other plank in the Dremel vice (metal jaws without the rubber covers). Then it's easy to plane both planks at the same time. The mini plane works great for this. Bevel the plank edges. Edge-bend the planks to the outer bulwark contour. I clamp the end of the plank (first pic in my earlier post) and then just wet the plank in sections and work along with the mini iron. Then, one plank at a time, dab a bit of water on the section of plank nearest the rabbet, but without getting water on the rabbet insert, get it just wet but not dripping so as not to drip water on other planks/model. Insert the rabbet end and lay the plank in place. Work the wetted section with the mini iron. The mini travel iron is working great, for the edge bending but also for this; I'm finding it heats up almost instantly versus the soldering-iron -type plank bender, and is way more manoeuverable and precise. It only takes a few seconds to work the particular section. Repeat 8 as needed. Continue along the plank in other sections to get the bow curve, same as 8-9. So far anyway, I don't need to work the middle section of the plank as the edge bending has done the job there. Work the stern section of the plank to bend and twist to fit. Here I'm using steam from a kettle and bending with pliers. After a final fit check and any adjustment/repeat, it's ready to glue. I'll have to adjust once I get further down towards the keel, but I think it will be much the same, with just garboard and it's neighbours a bit different. Nick
-
Hey Robert, It's way less complex than I made it sound I think; I used Chuck Passaro's videos (link in my earlier): I also use the electric plank bender; just my take that edge bending is better to eliminate or reduce clinker effect at bow. Also have to use "regular" bending where needed. Cheers/Nick
-
I started not long after my last post with a view to second planking. I discovered it's a bit different from first planking because I'm way more fussed about gaps, clinker effect and so on. And also trying to figure out edge bending. I've been through about three iterations of edge bending. See the pics below; I still don't know how to intersperse pics with text. First iteration. I started with the description from Chuck's videos. That was good, but I wasn't being accurate enough. I'd get e.g. too much of a bend in one area, have to correct it etc. And I had a hard time getting in with either the mini travel iron I bought or the electric plank bender. I see now that if I'd persevered it probably would have been ok, but I'd moved on to the second iteration. The second was a peg with a notch in it to keep the plank flat. That was ok but accuracy was still a problem. Then I went to the third iteration just today, and so far that's working a charm. I cut out a template of the outer bulwark and glued it to a piece of junk pine. Then I was able to clamp it at the bow end and bend it to conform to the outer bulwark shape. I dabbed on some water over a section, and used the iron on it it, then went to the next section. I had no problems with the plank wanting to jump up. After a couple of passes, I had a good shape to match the outer bulwark; it's given me a nice compound curve all the way along. I still had to work on getting it flush at the bow without a clinker effect. I decided to try holding the plank in place, then dabbed it with water and worked the iron on it. That's forced it down flush with virtually no clinker effect. I think one or two more passes tomorrow will have it just right. The pic looks like there are gaps, but it's shadow. Nick
-
Sanded, filled, and sanded; ready for second planking now. Just have to attach stem and keel finish pieces. The rabbet is good, and the first planking in way of the rudder/stern area is thinned to allow for second planking there to be flush to the finish keel and stern/rudder post. I had to thin the first planking in that area down to paper thin to do that, and the second planking there will have to be sanded down pretty thin, but it shouldn't be an issue. Nick
-
Back into this after a long and partly forced break. I have the first planking on now. The pic shows her after some initial sanding, more to do. Also some filling will be necessary. I struggled here and there, but gradually got more used to it. The clinker effect in the bow area was a bit frustrating; wish I'd come across Chuck Passaro's videos before .... Nick
-
I'm well advanced on getting the new hull build back to where it was before my blunder. I've gone more slowly and carefully this time. I spent a lot more time fitting the subdeck, which is what caused the problem last time. I trimmed the notches, and again and again, until a got a good dry fit, and the "satisfying click" per the instructions. At that point, I decided to leave well enough alone, and to glue the subdeck down from underneath using blocks (pic below); it just works for me. So far the subdeck is glued from forward to about midships with blocks. This time I used small pine blocks cut from scrap instead of mdf, which I fount can flake off. You can see some of the blocks in the pic. At the stern, I slipped in some wedges to be able to get glue into the hull/frame intersection; that's worked well. I just have to finish the other blocks tomorrow. Everything is good and square. Dry-fitting the outer bulwarks ply parts has already shown that they line up perfectly. Aside: I think there's a truth to all modelling: 1 your workspace is never big enough, and 2 however big your workspace is, it gets smaller all the time as you accumulate tools etc around what you're working on. In the interim before getting all of the replacement parts, I started to look at the 3-pounder cannon. Pics below, just dry-fitted; quoin not in; I drilled out the tubes. I want to rig them, and have been looking at some photos online. Rigging "secured" seems the way to go so far. I also want some colour, as previously mentioned, and for now am thinking about painting them ochre yellow, whether or not that's historical on this ship, it was done at the time. I also want to thin down the capsquares. Nick
-
He starts on the bulwarks at 22 minutes. Doesn't talk about the lineup with the bulkhead ears much, just basically says what the manual says, but it may be helpful. John 😄 Yep, the videos are great. Nick
- 24 replies
-
- First build
- Cutter
-
(and 2 more)
Tagged with:
About us
Modelshipworld - Advancing Ship Modeling through Research
SSL Secured
Your security is important for us so this Website is SSL-Secured
NRG Mailing Address
Nautical Research Guild
237 South Lincoln Street
Westmont IL, 60559-1917
Model Ship World ® and the MSW logo are Registered Trademarks, and belong to the Nautical Research Guild (United States Patent and Trademark Office: No. 6,929,264 & No. 6,929,274, registered Dec. 20, 2022)
Helpful Links
About the NRG
If you enjoy building ship models that are historically accurate as well as beautiful, then The Nautical Research Guild (NRG) is just right for you.
The Guild is a non-profit educational organization whose mission is to “Advance Ship Modeling Through Research”. We provide support to our members in their efforts to raise the quality of their model ships.
The Nautical Research Guild has published our world-renowned quarterly magazine, The Nautical Research Journal, since 1955. The pages of the Journal are full of articles by accomplished ship modelers who show you how they create those exquisite details on their models, and by maritime historians who show you the correct details to build. The Journal is available in both print and digital editions. Go to the NRG web site (www.thenrg.org) to download a complimentary digital copy of the Journal. The NRG also publishes plan sets, books and compilations of back issues of the Journal and the former Ships in Scale and Model Ship Builder magazines.