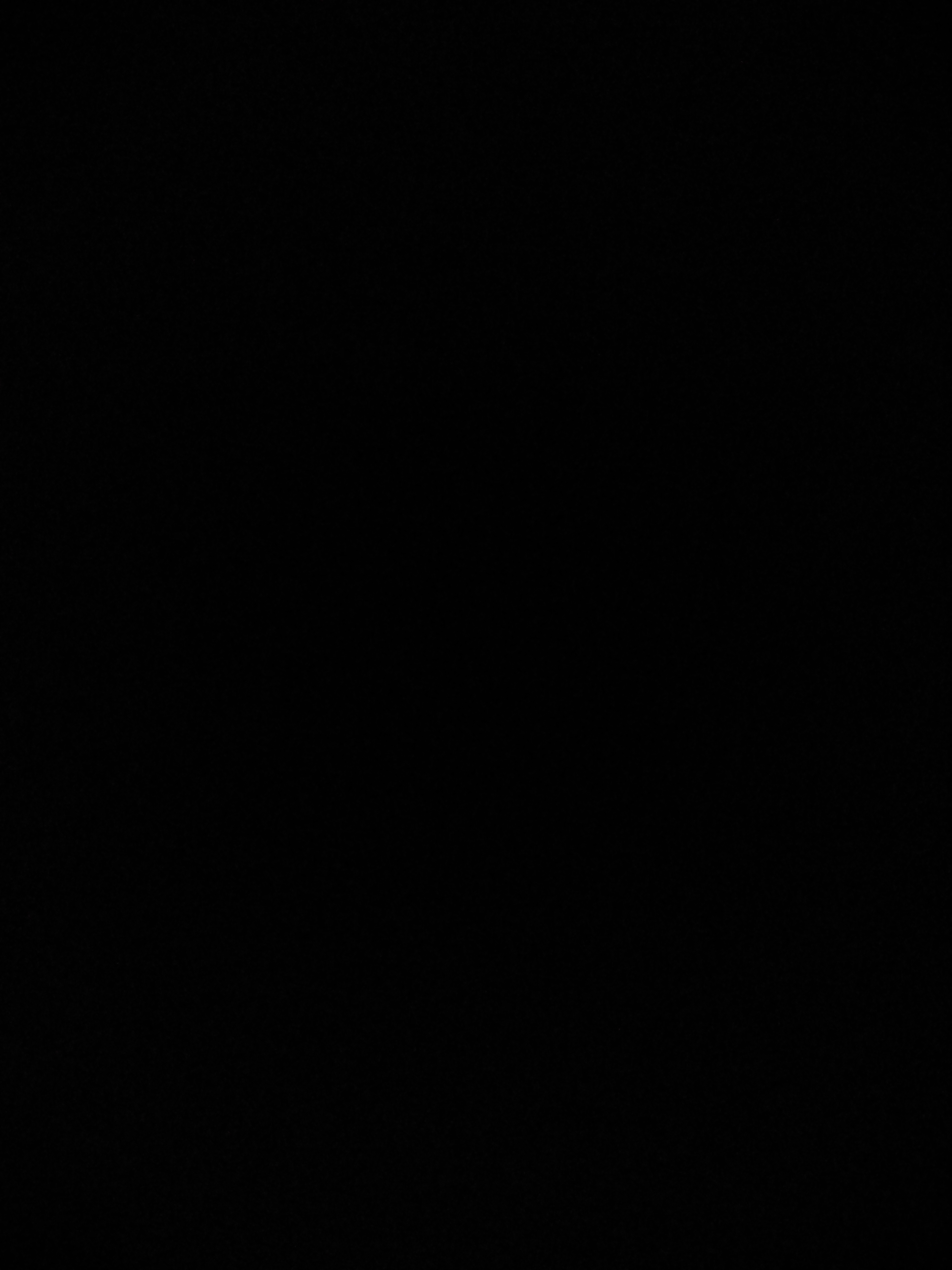
qwerty2008
-
Posts
552 -
Joined
-
Last visited
Reputation Activity
-
qwerty2008 reacted to michael mott in Bristol Pilot Cutter by michael mott - 1/8 scale - POF
Hi Nils thanks for your kind remark.
Hi Andy thanks for the comments I did have a look at the web images I am not sure I fully understand you comment though about sister blocks.
Hi John good to see you back from holidays, I am going to make a saddle for the wire span, just haven't got there yet.
I did make a twisted shackle yesterday it allows the block to stay in line with the one on the mast.
I made a better one today after a lot of mucking about with form tools for the brass turning.
Michael
-
qwerty2008 reacted to JerryTodd in R/C ...WHAT TYPE OF GLUE SHOULD BE USED???
I use Tightbond III for wood-to-wood joints, and epoxy everywhere else.
-
qwerty2008 reacted to michael mott in Bristol Pilot Cutter by michael mott - 1/8 scale - POF
Akutansin, Elmir, thanks for your kind words.
I have been chipping away at the gaff, literally
using the shrink tubing i made a wire strop for the gaff
and was pleased with my stops set into the gaff they are boxwood
And now I know that the drawing in John Leathers book was correct and that the chock stops face the same direction
The wire is too stiff though so I need either thinner softer wire or I will use rope, I prefer the wire so will look at what options there are for that.
I did haul up the gaff using the blocks it was fun threading the halliards, I did a quick and dirty job of tying the halliards with hitches, I keep running out of shackles and blocks! and I take my hat off to all you folk building and rigging fully rigged three masters, that would send me to the loony bin.
It is interesting thinking about the different types of blocks needed for the rigging to function properly though.
The thing I need to address now is some cleats and belaying pins.
Earlier in the day I was working on the other boat.
Michael
-
qwerty2008 reacted to michael mott in Bristol Pilot Cutter by michael mott - 1/8 scale - POF
The .024" plastic coated Beadalon 49 strand wire works well. This is with the boom hanging loose and no extra tension, I need to get some smaller diameter black heat shrink. and make the loops bigger but I am happy with the way it is hanging. Also I need to reverse the inside chock. I think I will also make a small saddle for the wire to attach to the block rather than just the shackle.
Michael
-
qwerty2008 reacted to JerryTodd in Byzantium by qwerty2008 - Scale 1:20 - RADIO - based on the Pride of Baltimore
BTWY: You should resin the inside thoroughly before attaching anything inside the hull. Deck clamp, mast steps, framing, etc can all be epoxied in after, but if resined after attachment, there's a place for water to get in. If water gets in, even a small amount, it will swell the wood causing joints to open, the glass to separate, and make more places for water to get in.
Holes in the hull, for prop shafts and the like, ought to be over sized, filled with epoxy and redrilled to the correct smaller size to prevent any wood from being exposed.
You might consider painting bare wood with Ethylene Glycol (automotive antifreeze - not Propylene Glycol). Glycol soaks into the wood and crystallizes which doesn't allow in water or mold which causes rot. All my models get this treatment. Allow it dry thoroughly and then resin it. If you look close you'll see the wood has little sparkles in it because of the crystals. A lot of wood objects recovered from shipwrecks are preserved this way it keeps out water without shrinkage. Be very sure to follow the safety precautions on the container, I had a neighbor whose dog lapped up a puddle of it from a leaking bottle and it later died as a result - they thought it was rabid until it was tested.
-
qwerty2008 reacted to DSiemens in Mercury by DSiemens - FINISHED - BOTTLE
Well the rigging is coming together. I got some Uni 0/8 fly tying thread. Its great stuff. Very little stretch in the line. I do wonder though if my stay lines are to thin. I'm open to suggestions on that. Part of me thinks well it's probably close to scale but then it's also hard to see. That may change once I get the rat lines on them though.
-
qwerty2008 reacted to JerryTodd in Byzantium by qwerty2008 - Scale 1:20 - RADIO - based on the Pride of Baltimore
That's a lot of thick ribs in a hull that even at that size, doesn't offer a lot of space. With the outside glassed and the inside given a coat or two of resin, you really only need a couple of those. I kept one to brace the dagger-board trunk, and one for the motor mount. The thing that really made the hull solid was the deck clamp and beams.
What ever you decide to do, remember to make it possible for water to get through fore and aft. Water WILL get in, if only a little, and you want drain holes in any bulkhead so it all goes to the lowest point where it can be pumped and dried out - otherwise you get mold in there and that gets really disgusting really fast. It'll be a very hard hull to reach into and clean.
Consider too keeping the hull as light as you can. That gets more weight onto the removable ballast which is deeper and stiffens the boat more, and allows you to trim her easier with internal ballast. It also makes handling the model a easier if the 20-30 pounds of sailing weight can be shed when she's not sailing.
-
qwerty2008 reacted to DSiemens in Mercury by DSiemens - FINISHED - BOTTLE
Thank you Michael and Popeye for your compliments they mean a lot coming from such experienced builders.
Well the hull is done finally. I guess I still have to drill holes in the chain plates but I'll do that when I start the rigging. For now I've go the masts up and the gaff and boom on for the spanker. Just need a few spars and it's off to the rigging yard.
-
qwerty2008 reacted to ccoyle in Part VI: Building V108 - The Superstructure
OK, now it's on to the bridge! This will be an interesting part of the build, because it has numerous tiny parts and also presents a number of options for improving the model.
We start with parts 25a (top of bridge deck) and 25b (bottom of bridge deck). Glue these together with some contact cement.
Notice that on the bottom of the bridge deck, there are three very small white spots; these are locator marks for the bridge deck supports to be added later. To make these marks more functional, we need to drill them out a bit. I use a small finger drill I made by gluing a #73 wire-sized drill bit into a short section of bamboo skewer. Drill carefully so as not to drill all the way through the card - we want just a shallow socket (drilling 25b before gluing the two parts together would avoid this difficulty).
Next we'll add the bridge wall, part 25c. The back of this part needs to be colored, so before removing it from the sheet, I gave the reverse side a coat of gray primer (you can see the scored fold lines through the paint).
At this point, you need to decide if you want to use the basic part as-is, or make some modifications. These are completely optional, so don't feel any pressure to add them - it's supposed to be fun after all. The first option I will show you is glazing the bridge windows. First you'll need to very carefully remove the printed windows. Remember to cut away from the corners! Also, note that there is some subtle, printed shading on the windows - there's the obvious, light-gray portion of the frame, but there's also a far less obvious, dark gray portion of the frame that is almost identical in color to the 'glass' portion of the window. Take care to remove only the glass areas, or the frames will be unnecessarily thin and delicate (they'll be delicate enough already!). The insides of the frames need to be colored. The space is too cramped for a marker, so I colored these with acrylic paint - the bottle says "Japanese Navy Gray", but I've modified the color at least once in the past, so I don't know what shade it is now.
The next option to decide on is whether to use the printed bridge railings or not. If you study the part carefully, you'll see that the railings are actually meant to portray railings covered by storm canvas. You can either go with the printed railing, or you can choose to replace them with either bare railings or more realistic storm canvas railings. I'll be adding scratch-built storm canvas railings; that being the case, the next step is to remove the railings portion of 25c (but don't discard them - we'll need part of them later). Skip this step if you use the printed railings. I'm also removing the side entrance fascias at this point, since it will be easier to add them later as separate pieces.
The bridge wall needs to be formed before glazing the windows, else we'll damage the glazing. Here I'm rolling the bridge wall over the handle of my hobby knife.
Now, what to use for glazing? There are numerous materials that can be used for glazing. In the past, I have used microscope slide slip covers (great material, but stiff and therefore ill-suited for curved surfaces), clear report covers (flexible, but don't glue well), window envelope panels (crinkle easily), and clear acetate overhead projector sheets (flexible, but don't like to hold a curve). Microscale makes a glue called Crystal Clear that dries clear and can be used for glazing small windows like these, but I don't have any. I'm a big advocate of the card modeling philosophy of "use whatever you can find around the house", and in this case what I found was my teenage daughter's top coat nail polish.
This I worked into each window until a film filled the entire window space. The top coat dries fairly quickly. It doesn't dry perfectly clear, but it does dry clear enough to suggest real windows are there, and that's the effect we want. Here's the finished windows:
Notice there's top coat residue around the windows - this is why the clear coat is applied only from the inside of the bridge wall. Once it dries, the area around the windows can be touched-up with paint. The finished bridge wall is glued to the bridge deck with contact cement, although I had to tack the outermost corners with a spot of CA to get them to stick tightly.
Next: adding interior bridge details.
-
qwerty2008 reacted to ccoyle in Part VI: Building V108 - The Superstructure
At this point, if you set the bridge assembly atop the conning tower, you'll notice that the radio room floor partially covers the locator for the foremast (the red spot).
We'll need to fix this before going further. Either carefully cut or drill out the foremast step on the conning tower roof, along with the corresponding bit of the radio room floor (the aft end of the bridge deck).
We'll also take a few moments to apply the edging to the bridge deck wings. This edging is the bottom part of the portions of part 25c we removed earlier (if you're not modifying 25c, you'll just be attaching the entire part 25c to the bridge deck; however, take note that the red portions of 25c - where the navigation lights will be placed - should be removed before gluing 25c to the bridge deck). Remove this bottom edge of the part 25c wings and glue these, one section at a time, to the bridge wings.
We're going to do some things out of sequence again. Following the parts numbers sequence would require us to add the radio room and bridge roof at this point, followed by the stacks, but that would make it difficult to get at the bridge interior, so we're going to add the interior details first. These will be some very tiny assemblies, but fear not! Tiny card assemblies require some care, some special techniques, and some tools, but they're not especially harder than larger assemblies. The interior parts are parts 31-33.
We'll start at the bridge wall and work aft (makes sense, doesn't it?), so the first assembly will be the compass, parts 33a (stand) and 33b (compass rose - albeit sans printed rose!). Part 33a needs to be rolled into a very small diameter tube. This presents a number of difficulties. First, very narrow tubes are almost impossible to roll from regular card stock, so in this case it will be easier to roll the part printed on 20# bond (remember waaaay back when I suggested you print the parts on both card and regular paper?). The second difficulty is the joiner tab; it will create an overlapping seam and isn't really necessary. You can remove the tab and close the tube by running a narrow bead of CA along the seam and squeezing the tube closed.
OK, so here's another stupid warts story. In this next picture, I'm rolling the 20# bond version of 33a around some styrene rod. What you can't see is that I moistened part 33a with my tongue - but the part stuck to my tongue and got too wet. It subsequently got all smooshed during the rolling process.
I destroyed the part! What do I do!? Fortunately, this little disaster presents the perfect opportunity to introduce a second way of dealing with part 33a! You see, card stock is made of multiple layers of paper fibers, and it is possible to separate the layers. I used the tip of my #11 blade and gently teased apart the paper layers at one corner of the card stock version of part 33a.
Once I have enough of the exposed layers to grab onto, I can then gently peel the two layers apart, and voila! I now have the equivalent of a 20# bond part. Now, it so happens that this particular tube I'm rolling has the same inside diameter as the styrene rod I'm rolling it with. So, for this tube, I'm going to actually wrap and glue the printed part to the styrene rod, then trim the rod to match the length of the tube. This makes a much sturdier base for the compass. Finishing the compass is a simple matter of cutting out and edge coloring the compass rose, gluing it to the stand, and gluing the finished compass to its spot on the bridge floor.
-
qwerty2008 reacted to Tarjack in HMY Royal Caroline 1749 by Tarjack - 1:50 - bone model
The carriages
The guns of the Caroline where same as on the Bounty ex. Bethia.
This has reinforced my decision at the gun carriages to not change anything and they are placed on the ship.
But now I get a folder from the decryption department placed on the table. Many thanks to the team, keep it up, you do excellent work.
On the cover "Top Secret, only for official use"
After evaluating the documents and photos, with super secret camera photographed
May I present to you, worth audience, more secret weapons production practices of smithy of his Majesty of England.
The carriages are in the style of Engl. Cannon built.
The sides of the carriage consist of two parts, which are bolted together.
In the lower part are the cutouts for the axles, at the top are the cutouts for the trunnion.
The axis sections of the lower bars are sawn on the circular saw
The semicircle is pre-cut to the circular saw and then filed
The upper parts are adapted and shaped
Now for the axles and wheels
All parts of the carriages without wheels and axles
The carriages are being built together
Ready gun carriages with guns
Guns on board
The next report on the arming of Caroline is in work and follows soon
Have Fun
-
qwerty2008 reacted to ccoyle in Part VI: Building V108 - The Superstructure
That's certainly possible -- I downloaded mine years ago. Makes me wonder what else may have been updated.
-
qwerty2008 reacted to Piet in Hr. Ms. O 19 1938 by Piet - FINISHED - scale 1:50 - submarine of the Royal Navy Netherlands in service 1939 - 1945
Thanks for your "likes" folks and Ian, yeah, cramped indeed but this was the largest, most modern and most comfortable sub going. Then to think that I was actually in this boat sometime at the end of 1941 at an open-house visit.
Okay, I took a few pics of the stern deck fairing this afternoon. I'll also indicate where the stern tube doors are located and compare my build with photos of the original build of this sub. I hope you like the photos of the original build. It does bring back memories
side view if the stern fairing, annotated where the stern position light will be.
side view of the stern with annotation where the stern torpedo tube doors are.
Stern view with the aft deck fairing installed.
This picture was most likely taken in 1943 when the O 19 was overhauled and refurbished in Scotland. I shows the aft deck fairing best.
This picture was taken at the commissioning of the O 19 in 1939. It also shows the aft deck fairing and all the other "stuff" that needs to be installed yet. The bulged areas on the sides are for the diesel engine exhausts.
This picture was most likely taken when docked at the Naval Base in Den Helder in 1939 just prior to sailing to the Netherlands East Indies with my father on board.
This was just prior to the launch in 1939. I indicated where the stern torpedo tube doors are located.
another view of the O 19 on the stocks just prior to launch in 1939. Here too I indicated where the stern torpedo tube doors are located.
Stern tube compartment during early stage of build
This is the stern tube compartment of the O 19 at the final stages of the build. My father would have been present at that time of the build of the O 19.
Stern tube compartment during intermediate stage of build.
This shows the framing of the stern torpedo tube compartment.
Cheers
-
qwerty2008 reacted to ccoyle in Part VI: Building V108 - The Superstructure
Before starting the superstructure, take a few moments to study the diagram for that assembly. The cover sheet artwork also has a nice view of that part of the ship.
Assembly of the superstructure starts with wrapping the walls (23b) around the deck piece (23a). Score the fold tabs on 23b, along with the two fold lines where the wall wraps around the aft corners of 23a; after cutting it out, add the hatch door on the port side (part 55), Now here's another tip - if you apply contact cement to only one surface to be joined, it doesn't grab as tightly as when both surfaces are coated, but it does allow a small amount of working time. I glued 23a and 23b together with contact cement in the following order, applying the contact cement incrementally only to 23b: starboard rear corner, starboard wall, front of the bridge, port wall, port rear corner. When I got to the rear port corner, I discovered that the wall, 23b, was about 0.5 mm too long; if this happens to you, just trim the overage away from the end of the wall, crimp a new corner where the wall and corner meet, and then finish attaching the wall. After the wall is completely attached, the superstructure roof (23c) can be added using PVA. The finished assembly looks like this:
If you study the last image carefully, you can spot a minor error. While I was dry-fitting 23b around 23a, the assembly slipped from my fingers. It is a very rare person who can suppress the reflex to grasp at a dropped object, and I'm not that person! As a result, there occurred a crease in the forward bridge wall (it runs down through the front porthole). When card is creased like that, the crease is pretty much there forever.
Next, the superstructure assembly needs to be mounted to the main deck. The kit supplies a couple of joiner strips for this task (parts 23d).
I happen to dislike such joiner strips for this job. When paper is folded, the fibers in the paper have 'memory' - they want to return to their previous shape. As a result, folded paper acts like a weak spring. In this case, the folded joiner strips will have a tendency to push the superstructure assembly upward. To avoid this, and to do a better job of positioning the superstructure walls, I prefer to add locator strips to the model. These can be made from leftover chipboard or strip wood, if you have any lying around (what ship modeler doesn't?). Here, I've sliced some ~1 mm wide strips from the edge of a chipboard sheet.
These are then cut to the appropriate length and glued down to the main deck just inside the superstructure outline. The idea here is that the strips will position the walls exactly where they need to be, right on top of the outline. Notice I've cut and shaped a piece for the curved forward bridge wall as well. By the way, those colored patches on the deck are where I tested some markers for color matches to the kit.
I used ordinary white glue to mount the superstructure, because the fit with the locator strips is tight, and I wanted as much time as possible to get all the walls down over the locator strips. The mounted superstructure should look like this, with nary a bit of white peeking from beneath the walls:
Back to Part V: Building V108 - The Hull
-
qwerty2008 reacted to ccoyle in Part VI: Building V108 - The Superstructure
Next up is the conning tower. The first thing to take note of is the parts are misnumbered. This is not an uncommon error in card models, where the model, the diagrams, the parts sheets, and the instructions are often all produced by one person -- without the benefit of a proofreader and perhaps also without the hindsight of a beta build. So, no big deal. The misnumbered part is 27d, which should be 24a. You'll also need 24b. 24c are the bridge wing support girders, which we won't need right away.
Normally, I would tell you to cut out 24b after scoring the fold lines and form it, but here's where you get the benefit of my building the model first. There's a big error with part 24b -- once it is cut and folded properly, it doesn't fit!
So here's how I fixed the problem. Cut part 24b apart along one of the rear fold lines. Measure and remove the excess part of the rear panel. We're going to put this excess colored panel to work. Notice that at the back of the conning tower portion of the parts 23 sub-assembly, there are two glue tabs; those should actually be part of the conning tower wall. Use the scrap piece from part 24b to make two rectangular panels to cover those glue tabs. The finished task will look like this:
Part 24b is now in two pieces. Glue the part with the rear wall to part 24a (the misnumbered '27d'). Now, use some scrap card to create a joiner tab for the two parts of 24b. Attach it thus:
Add the rest of 24b (don't forget to color edges as you work!).
So -- problem fixed. Next, add some joiner strips to the outline on top of the superstructure.
Glue the conning tower down with some white glue.
This assembly is a good example of the relative ease with which fit problems like this can fixed in the card medium. I don't think plastic or resin would have been as easy!
One other thing to take note of in this section is what happens when you create a 90 degree fold in card:
The ink layer is only on the very surface of the paper; very sharp bends will tend to crack this layer. Make sure to color the resulting exposed card fibers, either by painting or running a marker along the fold.
-
qwerty2008 reacted to ccoyle in Pt. V: Building V108 - The Hull
Ack! Almost forgot a few hull details.
Parts 21 are the propeller guards. Small parts like these that have substantial cut-out areas are flimsy once removed from the sheet, so it helps to do some of the prep work while they're still on the sheet. Start by coloring the reverse sides of the parts. Then, cut out the inside white areas, but leave the outer edge attached. You can then edge-color the interiors of the parts. When the interiors are done, remove the parts from the sheet and color the outer edge. Glue the guards to the hull with small amounts of PVA. Note that the guards follow the curvature of the stern, so the left and right guards are not interchangeable.
The rudder (part 22) introduces a new kit feature, the two-sided part.
Score the fold line, then cut out the entire rectangle containing the part. Apply glue to one-half of the back side of the part, then fold the rectangle in half. You now have a rudder colored on both sides! Remember, though, we're only using the part above the waterline, so go ahead and remove the red portion. Color the trailing edge and then glue the rudder to the stern; there's a locator mark there to help you. The rudder post will stick up above the deck just a little.
Here's the guards and rudder installed:
Okay, now we can move on to deck structures!
On to Part VI: Building V108 - The Superstructure
-
qwerty2008 reacted to Piet in Hr. Ms. O 19 1938 by Piet - FINISHED - scale 1:50 - submarine of the Royal Navy Netherlands in service 1939 - 1945
Hello all and thank you Popeye, Kevin and Sjors for stopping by the boat yard, really appreciate it.
I have completed the roughing in of the deck structure. The photos revealed a few ares that need some minor trimming but overall I'm satisfied. We are talking of fractions of m m's but it's important for the side panels to lay nice and flat and even.
It seems that my VOC ship is taking a backseat but I'll get back to it shortly.
I took a bunch of pics from different angels, primarily to see where I need to do some shaving with sandpaper. I made a 10 inch sanding block that seems to work really nice.
Final check for level of all the stations of the deck frame. I have put 4 brass nails in the side of the hull at water line 7, two on each side. This allows me to check the hull for level and consequently also all the structures and components for level.
Kinda like a bird's eye view of the completed deck structure. I already suspected a few areas that needed some trimming and the photos confirmed it. I'll note them and sand them down a little.
A shot along the port side from the bow. The dark area on the center of the top stringer seems a little high but that's an optical delusion
A shot along the starboard side from the bow. Same optical illusion is seen here.
A bird's eye view of the completed deck structure from the bow.
A profile shot of the port side.
Cheers,
-
qwerty2008 reacted to ccoyle in Pt. V: Building V108 - The Hull
Thanks for your comments, guys! It just so happens I have the next installment ready to go.
Once the laminated parts have had adequate time to dry, it is time to start cutting. Here's the complete set of hull framing parts cut from their sheets.
Cutting leads right away to a serious question: Do I cut on the line, outside the line, or inside the line? This might seem like a silly question, especially considering that this kit has very fine line borders. However, not all kits have such fine artwork, and (worse perhaps) there is no consensus among designers about whether the line is part of the part or not. Moreover, if you use headband magnifiers while cutting, which I do because of my bad eyesight, you'll discover that even with very fine lines it is possible to cut on, outside, or inside. So, how am I treating this particular kit, you ask? Answer: I tend to cut along the inside edge of the line. Be advised that if you use chipboard, the stuff is like rock compared to ordinary card. My #11 blade tip broke on the second part, but have no fear - the remainder of the blade actually cuts chipboard better without the missing tip (the tip is essential for controlled cutting on plain card, though). In fact, I only needed one blade to cut out all the 1 mm parts.
And now we can start gluing! First thing to do is to glue the two halves of the hull base plate together. I'm using Elmer's yellow wood glue -- it grabs pretty fast. Glue the butt joint first, then use two pieces of scrap chipboard to reinforce the joint.
Once this is done, it's time to fix the hull base former to a temporary working base -- something rigid that will keep the hull from warping during construction. I use a small piece of plate glass. I used a spot of rubber cement at the bow, midships, and stern. The rubber cement should allow the hull to be easily removed later (hopefully).
Next, start dry fitting the hull formers. Remember -- fit twice, glue once! It is important that the bulkhead formers sit flush with the longitudinal former. Trim where necessary.
Some of the formers will need to be beveled where they meet curved portions of the hull. The bow end of the longitudinal former will also need beveling.
Once all the formers are correctly trimmed, they can be glued to the hull base plate, starting with the longitudinal formers (two parts), then adding the eight bulkhead formers. It is more important that the bulkhead formers are flush with the edges of the base plate than perfectly sitting on the locator lines, but they should be close. Once all the formers are glued in, I add some extra weight to the hull so the finished model will have some 'heft' to it. Here you can see where I've glued in some lead fishing weights.
Next comes the main deck. Note that there are some red portions on these pieces -- these are to be cut or drilled out before assembly. I don't worry too much about the drilling, because that is easily done on the assembled hull and isn't always necessary in any case. The cut-out portions, however, should definitely be removed in advance.
At this point we may as well talk about edge coloring. Cut paper has edges, obviously, and there are three schools of thought on how to treat these. Some modelers don't color edges; to them, it's a badge of honor of sorts that indicates the model is made from card. Personally, I find uncolored edges ghastly. The second school are those that go to any length to find or mix watercolors, acrylics, or gouache that match the printed colors exactly. These people will also fill and sand any gaps in the seams where necessary. The Poles are masters at this technique, but it is a lot of work. If that floats your boat, go for it. I subscribe to the third school, the one that believes edges should be visually minimized. The idea is to make the seams and exposed edges less obvious but not necessarily completely unnoticeable. Thus, for this model, most any shade of gray felt-tip marker will suffice for edge coloring, since a gray edge on a gray model is far less obvious than a white edge on a gray model. If you go this route, test your markers to make sure they don't bleed excessively into the paper fibers.
Once the deck edges are colored, the two halves are glued and reinforced in the same manner as the base plate.
Once that's dry, we can then glue the main deck down on the hull formers. Apply glue to the tops of the formers, slip the deck over the two stack profiles that fit through the previously cut out slots, and make sure the tops of the formers are flush with the edges of the deck.
Ta-daaaa!
Finally, it helps to add some weight on top of the deck while the glue is drying. Here I've added a couple of small but heavy books. That's Ships of the Royal Navy on the right, a perfectly useless book in my opinion, and Retribution by Max Hastings on the left, a much more enjoyable volume chronicling the final year of the allied war against Japan.
Till next time!
-
qwerty2008 reacted to michael mott in Bristol Pilot Cutter by michael mott - 1/8 scale - POF
Greg thanks for stopping by and your kind words.
Today while out picking up some lumber for the other model I also stopped in a Michaels Store and purchased some Hemp beading cord. I am going to try the fine weight in the rope machine to see what sort of rope it makes.
This heavier stuff might work for making some rope fenders.
Michael
-
qwerty2008 reacted to DSiemens in Mercury by DSiemens - FINISHED - BOTTLE
Thanks guys your comments are much appreciated.
I admit those darn capstan bars about put me over the edge.
Got the starboard deck stanchions in. Just have to do the Port side and the cat heads and anchors and the hull is done.
-
qwerty2008 reacted to ccoyle in Pt. II: Start for FREE!
First of all, never download a model from a third party file sharing site. Always download models from the designer's own web site or a site authorized to host them. Second, never buy CD's claiming to have "hundreds of models" from auction sites like eBay -- these are inevitably scans of commercial kits. If you shop at eBay or somewhere similar on-line, make sure the seller displays a photo of the printed kit booklet; it should have an artwork cover with the publisher's name plainly visible.
-
qwerty2008 reacted to Piet in Hr. Ms. O 19 1938 by Piet - FINISHED - scale 1:50 - submarine of the Royal Navy Netherlands in service 1939 - 1945
Hello everyone,
Well, today is our Fourth of July celebration and after doing a little yard work I managed to do some more work on the O 19.
I cut the corners out of all the deck frames to receive the reinforcing strips. This also allows a firm glue foundation for the side plates and the deck plates.
After this was done I drilled two additional holes in each frame for bamboo pins to attach the deck frames more securely to the hull.
I was able to complete just half a dozen and transferred the locations of the extra pins to the top of the hull and drilled the receiving holes.
The pics below show the progress.
Looking aft starboard side.
Looking aft port side.
Another view looking aft port side.
Here I am drilling the extra two holes for pins to help secure the deck frames to the hull.
Frame 117 is just entering all three holes in the hull for a show and tell.
Cheers,
-
qwerty2008 reacted to willz in dummy cannons by william butler
before we cut the pieces off the beam we will shape the carriages, the first pic shows just one cut dow the steppy shape of the carriage with a razor saw, this is all thats needed with a model with no lights but again its simple to carry on and add more detail. second pic. when happy with shape cut them both off the piece leaving you with two identical halves
-
qwerty2008 reacted to willz in dummy cannons by william butler
some ships have full decks thoughout only to be covered up by the black wall of dummy cannons,
here is a tutorial on how to rid the ugly dummies
all we well use is the timber thats used for the dummy cannon beam, this tutorial is for the deag or AL HMS Victory so all using this method will have to adapt accordingly
first we half round the top of our material and drill a 2 mm hole (the 2 mm being the size of the dummy cannon pin (in my case)
-
qwerty2008 reacted to willz in dummy cannons by william butler
no need for this extravagance you can just slice them off with a razor saw at the thickness needed, then just glue to sides flush with the bottom, you dont want the wheels lifting the carriage off the floor, finally you can drill a hole in the base for a secret steel or brass dowel to decure the carriage in place