-
Posts
5,185 -
Joined
-
Last visited
About michael mott
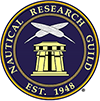
- Birthday 04/06/1948
Profile Information
-
Gender
Not Telling
-
Location
Edmonton, Alberta, Canada
Recent Profile Visitors
-
billocrates reacted to a post in a topic: Bristol Pilot Cutter by michael mott - 1/8 scale - POF
-
billocrates reacted to a post in a topic: Bristol Pilot Cutter by michael mott - 1/8 scale - POF
-
billocrates reacted to a post in a topic: Bristol Pilot Cutter by michael mott - 1/8 scale - POF
-
billocrates reacted to a post in a topic: Bristol Pilot Cutter by michael mott - 1/8 scale - POF
-
billocrates reacted to a post in a topic: Bristol Pilot Cutter by michael mott - 1/8 scale - POF
-
billocrates reacted to a post in a topic: Bristol Pilot Cutter by michael mott - 1/8 scale - POF
-
billocrates reacted to a post in a topic: Bristol Pilot Cutter by michael mott - 1/8 scale - POF
-
billocrates reacted to a post in a topic: Bristol Pilot Cutter by michael mott - 1/8 scale - POF
-
billocrates reacted to a post in a topic: Bristol Pilot Cutter by michael mott - 1/8 scale - POF
-
michael mott reacted to a post in a topic: SS Benjamin Noble by Roger Pellett - 1:96 - Great Lakes Freighter
-
michael mott reacted to a post in a topic: SS Benjamin Noble by Roger Pellett - 1:96 - Great Lakes Freighter
-
michael mott reacted to a post in a topic: SS Benjamin Noble by Roger Pellett - 1:96 - Great Lakes Freighter
-
Hi Nils one method I have found for creating curved U channels is to first anneal some thin wall brass tube then fill it with the appropriate diameter of styrene rod then bend it to the curve with finger’s then use a torch to burn out the styrene the file away the top slowly. And it would also work by just filing the top without the burning anyway. Michael
-
michael mott reacted to a post in a topic: SS Benjamin Noble by Roger Pellett - 1:96 - Great Lakes Freighter
-
michael mott reacted to a post in a topic: SS Benjamin Noble by Roger Pellett - 1:96 - Great Lakes Freighter
-
michael mott reacted to a post in a topic: SS Benjamin Noble by Roger Pellett - 1:96 - Great Lakes Freighter
-
michael mott reacted to a post in a topic: SS Benjamin Noble by Roger Pellett - 1:96 - Great Lakes Freighter
-
Hi Nils just finished going through your build, wonderful creative work. I’m amazed by how fast you get the work done. Michael
-
Great little sanding block
michael mott replied to Papa's topic in Modeling tools and Workshop Equipment
Now that's thinking outside the border! Michael -
Starting the back of the galley now. It is easier to work on it outside of the hull, l am amazed at how nice the maple that I cut from the big log 50 years ago still works and planes up with such a lovely lustre. I’m guessing it is because it has been air dried. Michael
- 2,196 replies
-
Thanks Tom I appreciate that. Thanks to everyone for your kind comments. I did some more work on the galley and have soldered the top to the sink and used the sheet metal drill for the drain pipe. I have given the wood a good coat of tung oil and will give it another coat later. Michael
- 2,196 replies
-
- 2,196 replies
-
Looks like another great build about to start. I do enjoy all the historical context that you add Eric. Michael
- 255 replies
-
The lip is now cut and rounded on the edges I will be raising the top when I get it back in the boat. Michael
- 2,196 replies
-
Lovely work Richard also the cabinet in your earlier post. I am always on the lookout for salvageable wood for my model projects, it always breaks my heart to see an old house being crushed into matchsticks by huge machinery when much of the wood used could still be salvaged! The time is money myth will become apparent one day, but I digress. I am still using some of the eastern sugar maple that I acquired in 1973 as a six foot long green log after slabbing it up into quarters after taking a three inch plank from the centre for a coffee table and air drying the rest. It is what I am using for the interior of my Bristol pilot cutter. The deck is close grained salvaged old growth clear Douglas Fir. michael
-
Keith , having spent the last hour and a half starting at the beginning, it looks like a marvelous project. I will most certainly be following along and gleaning tips from your ingenious problem solving skills. The comment about the breakfast counter made me laugh. It looks like you will have some fun with the bright-work and all those panels. Good to hear you are well, and getting stuck into the prep for the start of keel laying. Michael
-
Just need to solder the top lip on and drill the hole for the drain the the sink should be ready, presently the countertop is at 28 1/2 inches I am wondering if it is a bit too low. Michael
- 2,196 replies
About us
Modelshipworld - Advancing Ship Modeling through Research
SSL Secured
Your security is important for us so this Website is SSL-Secured
NRG Mailing Address
Nautical Research Guild
237 South Lincoln Street
Westmont IL, 60559-1917
Model Ship World ® and the MSW logo are Registered Trademarks, and belong to the Nautical Research Guild (United States Patent and Trademark Office: No. 6,929,264 & No. 6,929,274, registered Dec. 20, 2022)
Helpful Links
About the NRG
If you enjoy building ship models that are historically accurate as well as beautiful, then The Nautical Research Guild (NRG) is just right for you.
The Guild is a non-profit educational organization whose mission is to “Advance Ship Modeling Through Research”. We provide support to our members in their efforts to raise the quality of their model ships.
The Nautical Research Guild has published our world-renowned quarterly magazine, The Nautical Research Journal, since 1955. The pages of the Journal are full of articles by accomplished ship modelers who show you how they create those exquisite details on their models, and by maritime historians who show you the correct details to build. The Journal is available in both print and digital editions. Go to the NRG web site (www.thenrg.org) to download a complimentary digital copy of the Journal. The NRG also publishes plan sets, books and compilations of back issues of the Journal and the former Ships in Scale and Model Ship Builder magazines.