-
Posts
146 -
Joined
-
Last visited
About flutlo6180
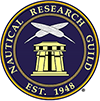
Profile Information
-
Gender
Male
-
Location
United States
Recent Profile Visitors
The recent visitors block is disabled and is not being shown to other users.
-
PaddyO reacted to a post in a topic: Fair American by flutlo6180 - Model Shipways - 1:48 - Brig
-
PaddyO reacted to a post in a topic: Fair American by flutlo6180 - Model Shipways - 1:48 - Brig
-
JLong reacted to a post in a topic: Fair American by flutlo6180 - Model Shipways - 1:48 - Brig
-
ccoyle reacted to a post in a topic: Fair American by flutlo6180 - Model Shipways - 1:48 - Brig
-
Thanks. I didn't like the way the metal windows looked and thought making my own would force me to have patience and pay attention to detail - both skills I know I need to work on. I've continued the work on the transom and counter with the window frame installed and the planking installed. When I started planking the counter I realized that instead of the stern blocks stopping 1/32" short of the wing counter that I had them extending 1/32" beyond. What made the error even more frustrating for me was I had shaped the blocks to fit correctly, thought I had made an error, and shimmed them to extend a bit from frame 16 and beyond the the wing counter (must have been tired that day). You can't see it from the photo, but I did get them carved back so the hull planks will align properly. Then on to planking the inboard side of the transom. It was easy to see every slight misalignment of the frames and required some additional shaping of the transom extensions to get a smooth run so the planks would lay flat. The instructions state that you need to heat bend the hull planking at the stern so I purchased one from Model Shipways. I've never used heat bending but I thought it was needed to shape the bends in the transom cap. There is definitely some technique involved to get the proper shape and not split the piece at the bend. I did several trial runs with some scrap planks from an earlier build and am glad I did. I had the same issue with splitting the cap on the first 2 trials, and then decided to soak the piece overnight. My third trial looked good and gave me confidence to move on the actual cap piece. With the curve for the port side shaped, it was a matter of getting the piece to lay properly while the cap dried. A thick rubber band and a clamp did the trick. My plan is to let the piece dry overnight and glue it on in the morning. I've yet to shape the starboard cap bend, but I have a piece soaking and will work on that tomorrow. I am a bit worried about making a hash when cutting the scarf joint and made the tail after the bend is left a bit long so I'm not trying to cut the scarf on the curve. I'll practice on the pieces from my earlier heat bend trials and if these practice runs go badly I probably go with a butt joint.
-
Matt D reacted to a post in a topic: Fair American by flutlo6180 - Model Shipways - 1:48 - Brig
-
CiscoH reacted to a post in a topic: Fair American by flutlo6180 - Model Shipways - 1:48 - Brig
-
yvesvidal reacted to a post in a topic: Fair American by flutlo6180 - Model Shipways - 1:48 - Brig
-
yvesvidal reacted to a post in a topic: Fair American by flutlo6180 - Model Shipways - 1:48 - Brig
-
yvesvidal reacted to a post in a topic: Fair American by flutlo6180 - Model Shipways - 1:48 - Brig
-
yvesvidal reacted to a post in a topic: Fair American by flutlo6180 - Model Shipways - 1:48 - Brig
-
Slow but steady progress on the build over this last week. I completed the framing for the transom. It took me several attempts to get the outer frames placed for a smooth flow for the planking but persistence and patience paid off and I am generally pleased with result. The plan sheets show the transom with a smooth arc but with the wing extensions installed it didn't look correct and I decided to shape the top for a look closer to the diagrams in the plans. It's not quite the smooth arc I planned but I am concerned that if I make the arc at the top of the transom more pronounced I will need to take off too much material. And then on to the windows. I decided not to use the metal windows from the kit and opted to make my own. The photo below shows the completed frame and 2 windows at different stages of construction. I've included one of the metal windows for reference. After I finish making the windows and gluing on the window frame I plan to plank the inboard and outboard faces of the transom before I make and install the transom cap. The cap is suppose to be flush to the inboard face and I think it will be easier to get that alignment with the planking in place. I'll paint the windows gold off the model and install them when I get ready to paint the inboard bulkheads.
-
Progress on the build continues. After both bow filler blocks were shaped and installed I moved on to the timberheads and knightheads. The shaping of the knightheads from the drawing on the plan sheet was difficult for me to envision how the final piece should look and I'm not satisfied with the end results so I haven't yet glued any of these pieces in place. The build instructions indicate that it is ok to use timberheads for both positions and I am considering changing out the knightheads. The camera angle in the second photo makes the bulkheads look out of alignment but that is not the case. While I consider about replacing the knighthead pieces, I moved on to the stern. As I did with the bow filler blocks, I shaped the stern fillers off the hull with frequent test fittings until I got the result I wanted. The first photos shows the progression from block shape through rough shape and then final shape. The second photos is a closer view of the rough and final shapes and the third shows both finished blocks side by side. I'm now working on the stern frames. The two frames either side of centerline (SF5 and SF6) and the next frame to port (SF4) came out fine, but SF3 on the far right in the photo turned out to be canted when I went back to recheck positioning and spacing between the frames. To keep the frame true and vertical with the same SF5-SF3 gap width as between SF6-SF4 I fashioned a spacer from scrap and used the spacer and a Lego block to keep the frame aligned in both axis while the glue dried. I'll shape and insert the top and bottom frame supports next and then work on the outer frames, supports and wings.
-
The bulkheads are installed and glued in to place. My square isn't small enough to fit between the bulkheads to get alignment, so I used a lego block which worked just fine as a substitute. It took me longer than I anticipated but I also finished fashioning and gluing the bow fillers in place. I completed most of the shaping before installation. The rough shape was carved with a knife. Once I achieved a reasonable outline I shifted to a Dremel, files and sandpaper. The approach worked well and allowed me to take small amounts of material and test fit frequently to match the rabbit and curve of bulkhead 1.. I expect there will be some final tuning of the fillers when I get to planking but the amount of additional work should be minimal.
-
As noted in other Fair American build logs, the keel length was about 1/4" too short leaving the stern post protruding beyond the end of the keel. I thought about 3 ways to fix the issue - add a filler block, cut a new keel from the scrap basswood sheet, or cut the stern post and shape to fill the gap. Because I had already glued the keel in place, I opted to cut a new stern post which I felt was easier then cutting a new keel piece. After the bottom is painted I don't think my fix will be at all noticeable. In the photo I've placed the original piece next to the repair to show the difference. The bulkhead dry fit shows that other than #1 and #16, they all end short of the bearding line. As I get to shaping the hull for planking I'll see if I need to add some small fillers. You can see in the first photo above and the photo below that I've glued a small piece of scrap wood aft or bulkhead #3 (on both sides). I added the pieces to strengthen a repair when I had to glue back the tab which broke off during dry fitting. I forgot how soft the wood is and pushed a bit too hard when slotting the piece in place. I had the same issue with the tab between #14 and #15 and used the same method to strengthen the repair. My next steps are to pre-shape the bulkhead edges and then gluing them in place.
-
I've started my next build, the armed brig Fair American circa 1788. This build is going to more challenging for me because the model is more complex and the build directions contain no pictures and fewer drawings which will require more interpretation of the plans. Fortunately the plan sheets are all full size. The bearding line was already lazar marked which allowed me to jump right in and cut the rabbit. The bulkheads are removed from the sheets and I've started with laying out the markings for the bevels. On my prior builds the bulkhead tapers were all done with files and sanding after they were installed and glued in place. For this build the instructions call for starting the bevels before installation using a crafting knife. I've laid out the bevel lines a bit short of the plans because I'm worried about taking too much off the edges. I'll finish shaping the bevels for a smooth planking run with sanding after installation but with some of the material already removed there should be less sanding needed. I'm starting with bulkhead 16 and working to get it shaped so the bottom stops at the bearding line. The next 2 photos show the current dry fit. Before I continue, I will glue the keel, stem and stern post into place, and will resume bulkhead work while the glue dries.
-
FINISHED!! While I haven't posted in a while I have continued to work on the build and finished it yesterday. I really enjoyed working with the Vanguard Alert 1777 kit. The build instructions and photos were excellent and overall at the right level of complexity for my capability level. Thanks to everyone who dropped in and provided comments and encouragement during my journey. I am especially appreciative for the advice and tips provided along the way. I learned so much and I am pleased with the results. I am looking forward to applying what I learned with Alert to the Fair American after I tidy up the shipyard. Ken
- 59 replies
-
- Alert
- Vanguard Models
-
(and 1 more)
Tagged with:
-
flutlo6180 reacted to a post in a topic: Rattlesnake by CapnJack43 - FINISHED - Model Shipways - 1/64 - American Privateer
-
flutlo6180 reacted to a post in a topic: Rattlesnake by CapnJack43 - FINISHED - Model Shipways - 1/64 - American Privateer
-
flutlo6180 reacted to a post in a topic: HMS Mercury 1779 by Mr Pleasant - 1:64 - based on Shipyard paper model
-
flutlo6180 reacted to a post in a topic: HM Cutter Trial 1790 by BrochBoating - FINISHED - Vanguard Models - 1:64
-
Thanks for the kind words Eric! One of the things I love about this forum is the support and encouragement that keeps me motivated and helps me to improve.
- 59 replies
-
- Alert
- Vanguard Models
-
(and 1 more)
Tagged with:
-
flutlo6180 reacted to a post in a topic: HM Cutter Alert by flutlo6180 - FINISHED - Vanguard Models - 1:64
-
Thanks again Allan, What a great suggestion which puts my decision in an entirely different light. I'm going to give your approach a try.
- 59 replies
-
- Alert
- Vanguard Models
-
(and 1 more)
Tagged with:
-
Thanks Allan! I appreciate the explanation and the sketch which does make it much clearer. You are correct, I've installed all the blocks thus far the same way - upside down. As you say, it is a small detail, and I'm not sure if I will go back and redo them, but I will give that some thought, Regardless, I will make the change going forward.
- 59 replies
-
- Alert
- Vanguard Models
-
(and 1 more)
Tagged with:
-
Based on Thukydides guidance, I've started to redo the deadeyes. Doing so did mean I needed to replace several shroud lines and I am finding it less daunting that I originally thought to be working on building the mast while it is stepped. With all the rework I've done on this build it seems like I am building her twice, but I am learning a lot and enjoying the journey.
- 59 replies
-
- Alert
- Vanguard Models
-
(and 1 more)
Tagged with:
-
flutlo6180 reacted to a post in a topic: HMS Beagle by Firs49 - OcCre - 1:60 - First Build
-
flutlo6180 reacted to a post in a topic: HM Cutter Alert by Thukydides - FINISHED - Vanguard Models - 1:64 - first build
-
flutlo6180 reacted to a post in a topic: HM Cutter Alert by Thukydides - FINISHED - Vanguard Models - 1:64 - first build
-
flutlo6180 reacted to a post in a topic: HM Cutter Alert by Thukydides - FINISHED - Vanguard Models - 1:64 - first build
-
Thanks. Your pointers are very much appreciated and are helping to build my catalog of knowledge and repertoire of techniques.
- 59 replies
-
- Alert
- Vanguard Models
-
(and 1 more)
Tagged with:
-
flutlo6180 reacted to a post in a topic: HM Gun Brig Adder 1797 by DB789 - FINISHED - Vanguard Models - 1:64
-
The first item of rigging is complete with the driver boom install. I rigged the boom with the mast off the hull which turned out to be a good idea. During my first attempt at raising the boom I realized that the parrels would not slide above the lower mast cleats and the block for the main yard so I had to remove the block and retie the parrels. With the boom in position, I wound up running the line the wrong way through a couple of blocks and had to pull the line back and rerun through the blocks in the correct orientation. Redoing my work was much easier without the mast stepped. The sheets for the boom are hanging loose for now. I did change my mind and decided to step the mast prior to installing the yards. With the mast seated I am now working on rigging the main shroud deadeyes. The results of my first attempt were dreadful so I did some quick research on rigging deadeyes. That led me to a picture of a deadeye rigging jig in a post in the Masts, Rigging and Sails forum by hornet (https://modelshipworld.com/uploads/monthly_01_2017/post-1505-0-68284800-1483318896.jpg).. I had the materials on hand and made one of my own. Using the jig to place the upper deadeye in to position, grabbing the shroud line with hemostats just above the deadeye and resting the handle base of the hemostat on the chain plate was a much easier approach. The end result turned out much better than I had anticipated. With the deadeye connected to the shroud I connected the two together in 0.5mm rope. I'll clip the rope later. The building sequence in the manual seems to show the shroud cleats installed after all the shrouds are connected. I think it may be easier to install the cleats after I finish connecting each shroud and am wondering if there are any drawback to using this sequence.
- 59 replies
-
- Alert
- Vanguard Models
-
(and 1 more)
Tagged with:
-
Thanks. Your craftsmanship is far above my level and I find that wanting to work too quickly is often one of my challenges. Being able to see the finish line has motivated me to find more hours for the build.
- 59 replies
-
- Alert
- Vanguard Models
-
(and 1 more)
Tagged with:
-
- 59 replies
-
- Alert
- Vanguard Models
-
(and 1 more)
Tagged with:
About us
Modelshipworld - Advancing Ship Modeling through Research
SSL Secured
Your security is important for us so this Website is SSL-Secured
NRG Mailing Address
Nautical Research Guild
237 South Lincoln Street
Westmont IL, 60559-1917
Model Ship World ® and the MSW logo are Registered Trademarks, and belong to the Nautical Research Guild (United States Patent and Trademark Office: No. 6,929,264 & No. 6,929,274, registered Dec. 20, 2022)
Helpful Links
About the NRG
If you enjoy building ship models that are historically accurate as well as beautiful, then The Nautical Research Guild (NRG) is just right for you.
The Guild is a non-profit educational organization whose mission is to “Advance Ship Modeling Through Research”. We provide support to our members in their efforts to raise the quality of their model ships.
The Nautical Research Guild has published our world-renowned quarterly magazine, The Nautical Research Journal, since 1955. The pages of the Journal are full of articles by accomplished ship modelers who show you how they create those exquisite details on their models, and by maritime historians who show you the correct details to build. The Journal is available in both print and digital editions. Go to the NRG web site (www.thenrg.org) to download a complimentary digital copy of the Journal. The NRG also publishes plan sets, books and compilations of back issues of the Journal and the former Ships in Scale and Model Ship Builder magazines.