
rtropp
NRG Member-
Posts
936 -
Joined
-
Last visited
About rtropp
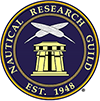
Profile Information
-
Gender
Male
-
Location
Atlanta
-
Interests
Member: The Nautical Research Guild,
Atlanta Model Shipwrights
Current builds - The Siren by Model Shipways
Recent Profile Visitors
-
Knocklouder reacted to a post in a topic: OCCRE White Wood Putty
-
rtropp started following Table saw accessories , OCCRE White Wood Putty , Is it better to plank the hull and then attach the bow stem or plank and then attach the bow stem? and 3 others
-
OCCRE White Wood Putty
rtropp replied to mrsamimi's topic in Building, Framing, Planking and plating a ships hull and deck
I used white Model Lite filler on my Occre ship model. To get the color depth I added Occre's Sepeli dye. (I'm sure there a colors in the local hardware store that will match. but i recommend water based.0 I wanted to get it dark but too much liquid weakens the filler. So I would add a very little at a time and let some of the liquid dry out before adding more. It took a number of tries, and some time, but I did get a pretty good match for small spaces. Richard -
I find it more straight forward to attach the stem, make sure it is properly seated and trimmed, and the insert/attach the forward part the plank, finally gluing the rest of the plank as you move towards the stern. I suspect that there are certain build conditions that might dictate the sequence and am curious to learn about any and hear the preferences / suggestions of others. thanks Richard
-
Kurt, I have found a replacement. Its only about $27. It's called the Miter Cut from a company called Fourmost. They seem to focus on model car racing accessories. I ordered on to to see if it is the one I am trying to replace. Then see if it is as well built. Honestly, !175+ vs. $27. I have high expectations for the Miter Cut. Hope it lives up to them or I will talk myself into getting the Ultimation cutter. I am curious. What do you use when you are cutting planks to size? Thanks for all the help folks. Richard
-
ok, new info for me. Where I could not find the information on my existing miter cut tool, I used one of the new AI tools and found the manufacturer is still in operation. The replacement for my cutter/chopper, which I have used for years, is $28 with $7.50 shipping. So, for that price, I ordered one. They also had a similar device to saw small items. For the heck of it I ordered one of those ( since there is a flat shipping charge and it would not change if from the U.S.) One of the things I liked about the cutter was that it was small, and used readily available, cheap, hardware store blades and I already have boxes of those. I do not know about the saw blade but requested the manufacturer let me know if replacement parts were available. If you all would like I can do a quick review when they arrive. I came close to pulling the trigger on the Ultimate cutter but it is expensive and seems to take up a lot of worktop space. Thanks for your help Richard
-
I prefer the electric sander so I can use two hands to manipulate the item... but then, that is just clumsy me. Palmerit, do the blades of the ultimation last, say through a ship or two, or do they constantly constantly need to be replace like the blade on my Fourmost Products, Miter Cut Tool? Non-proprietary blades very much change the balance of the decision, as do the availability of replacement parts. Did you find a replacement source and if so, can you share it? Thanks, Richard
-
Thank you for responding. I have the Byrnes Saw, along with the Byrnes Thickness Sander, for a number of years now. I do not use it often, but when I do its great. But, I felt it was too powerful to use on very thin, i.e. second planking wood strips. I have a very old chopper that, after years, is starting to wear where the blade touches the black circular cutting stop. I looked at taking it apart to try and smooth or replace it but it seems to be one piece with the angle arm. It still works but I'm not always getting a clean cut at the bottom. Anyway, I am considering trying my hand at a scratch build and thought to look for a replacement or even a more accurate, and faster way of chopping. The chopper II is on Amazon for $85, a bit steep. There is a great looking machine that miss Olga showed on her YouTube videos, but it is well over a hundred dollars, and uses proprietary blades. Being honest with myself, I can get fairly decent cuts, with a flat tip Exacto knife... if I am careful and work very slowly. So this purchase becomes a luxury more than a necessity. The little electric chop saws I saw are pretty inexpensive compared to the manual ones, but not sure if I will end up with shredded cuts. So I was wondering if any of them would be good for very thin cuts, or should I bite the bullet and continue to look for manual cutters/choppers. Any ideas would be appreciated Thanks Richard
-
Does it make sense to use the Byrnes saw for the very thin second planking of most models? Are there special precautions required? I am just wondering, my Chopper is no longer usable so should I try to use the Byrnes. it is a powerful little saw and not sure that crosscuts using a sliding table would be a good idea? If not, what, at a reasonable price, would best replace the Shortline Chopper? thank you, richard
-
Gregory reacted to a post in a topic: sources of 4.5" x 1" sandpaper for microlux belt sander 15229.
-
Hi, I am beginning to use the microlux 15229 more frequently but would like to find a more reasonable source for premade sanding belts. I'm pretty sure I have seen comments somewhere but for the life of me cannot find them either in the forum or online. I would appreciate any leads. thank you, Richard
-
rtropp reacted to a post in a topic: Removing Char from bulkheads
-
Proxxon mini lathe verdict
rtropp replied to Srenner's topic in Modeling tools and Workshop Equipment
For me, the proxxon worked well for shaping masks and spars. It’s not a metal forming lathe, your getting a wood lathe for light use. The key that got me going was the process I ended up using to get some degree of accuracy. 1. Measure points along mast or spar from, hopefully, the 1-1 plans 2. Transfer to dowel. 3. Mounted on the lathe, cut small “rings” to the measured depth for each location where Thickness changes. 4. Use the cuts to control depth of sanding/filing on dowel 5.I use mostly sand paper on blocks of wood or small files to shape the mast or spar on the lathe. (Easier to control than chisels). 6. Once you have the series of cuts on the dowel it becomes almost like connect the dots. A tip from another member on using shrink tube (like in electronics use) led me to buy a small box of them. Anyway, I slide the grip end of the dowel into the three jaw chuck and use the shrink tube to help protect the wood. hope this helps. R -
I am becoming a big fan of CA in my modeling and don't write off thin CA. Many parts are difficult to clamp, and my hands are not as good as they used to be at holding parts and waiting for them to hold with slower drying glues. There are various applicators that are sold for thin CA that give a lot of control. Instead of trying to control from the bottle I use tiny containers (from amazon and primarily for nail or tattoo artists). I put a small amount of thin CA into the container and use the applicators giving very fine control and the ability to place tiny/precision amounts of the CA. The thin CA leaches into the wood joints and for most, does a fine job of holding almost instantly. My process has increasingly become holding parts in place on the model and apply tiny amounts of CA. The parts hold in a few seconds and a lot less fumbling with clamps. If I make a mistake (and I do, often) I use a little debonder or acetone and I get to try again. I do not use the spray hardener often. I find I don't really need it and the odor is obnoxious. My takeaway is that I reduced the need to hold or clamp parts which is tough on the arthritis. Really it is mainly second planking that I use other glues. Thanks
About us
Modelshipworld - Advancing Ship Modeling through Research
SSL Secured
Your security is important for us so this Website is SSL-Secured
NRG Mailing Address
Nautical Research Guild
237 South Lincoln Street
Westmont IL, 60559-1917
Model Ship World ® and the MSW logo are Registered Trademarks, and belong to the Nautical Research Guild (United States Patent and Trademark Office: No. 6,929,264 & No. 6,929,274, registered Dec. 20, 2022)
Helpful Links
About the NRG
If you enjoy building ship models that are historically accurate as well as beautiful, then The Nautical Research Guild (NRG) is just right for you.
The Guild is a non-profit educational organization whose mission is to “Advance Ship Modeling Through Research”. We provide support to our members in their efforts to raise the quality of their model ships.
The Nautical Research Guild has published our world-renowned quarterly magazine, The Nautical Research Journal, since 1955. The pages of the Journal are full of articles by accomplished ship modelers who show you how they create those exquisite details on their models, and by maritime historians who show you the correct details to build. The Journal is available in both print and digital editions. Go to the NRG web site (www.thenrg.org) to download a complimentary digital copy of the Journal. The NRG also publishes plan sets, books and compilations of back issues of the Journal and the former Ships in Scale and Model Ship Builder magazines.