-
Posts
2,210 -
Joined
-
Last visited
About EdT
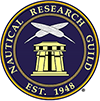
Profile Information
-
Gender
Male
-
Location
Pennsylvania USA
Recent Profile Visitors
-
daHeld73 reacted to a post in a topic: HMS Bellona 1760 by SJSoane - Scale 1:64 - English 74-gun - as designed
-
daHeld73 reacted to a post in a topic: HMS Bellona 1760 by SJSoane - Scale 1:64 - English 74-gun - as designed
-
daHeld73 reacted to a post in a topic: HMS Bellona 1760 by SJSoane - Scale 1:64 - English 74-gun - as designed
-
FrankWouts reacted to a post in a topic: French 74-gun ship by matiz - scale 1:56 - Tiziano Mainardi
-
daHeld73 reacted to a post in a topic: HMS Bellona 1760 by SJSoane - Scale 1:64 - English 74-gun - as designed
-
daHeld73 reacted to a post in a topic: HMS Bellona 1760 by SJSoane - Scale 1:64 - English 74-gun - as designed
-
daHeld73 reacted to a post in a topic: HMS Bellona 1760 by SJSoane - Scale 1:64 - English 74-gun - as designed
-
daHeld73 reacted to a post in a topic: HMS Bellona 1760 by SJSoane - Scale 1:64 - English 74-gun - as designed
-
daHeld73 reacted to a post in a topic: HMS Bellona 1760 by SJSoane - Scale 1:64 - English 74-gun - as designed
-
daHeld73 reacted to a post in a topic: HMS Bellona 1760 by SJSoane - Scale 1:64 - English 74-gun - as designed
-
EdT reacted to a post in a topic: Young America 1853 by EdT - FINISHED - extreme clipper
-
Thanks guys, for your nice comments. First, the question of ventilators. I would say no, I saw now trace or reference to them on the ship or even on others of her class and period. Crew quarters were on deck and I am sure that at the prices for goods claimed in California at the time, the entire hold was likely stacked up to the hatch covers. Their is a hatch that could be opened over the passenger accomodation aft. I do not know if the model is on display at Mystic. I was always hopeful, but there were no guarantees. I am not in regular contact with them. My main motive in donating the model was to see it in a good home where it would be taken care of. The Mystic model store is first rate. Naiad and Victory should be so lucky. Cheers, Ed
- 3,612 replies
-
- young america
- clipper
-
(and 1 more)
Tagged with:
-
Mr. Tosti, I recently purchased your three book set and plans for building a model of the clipper ship Young America. The books were not cheap, but well worth the price of admission. Your books and modeling techniques have inspired me (after my illness) to get back to building my Flying Fish model. Thank you for writing these books.
John
Wawona59 on MSW
-
Hello Richard, I do believe that volume 2 is out of print, but cannot advise you how to get a copy. You might try writing to the published, Mike Ellison, (Mike@seawatchbooks.com) but I doubt there is any inventory. You might also try Amazon. I have seen a copy or two of my books show up there used. You might also, post requests on MSW. Perhaps someone may be able to sell you one. Sorry, I could not be more helpful. Ed
-
EdT reacted to a post in a topic: Young America 1853 by EdT - FINISHED - extreme clipper
-
Rick, You are testing my memory because I know longer have the model, but I am sure that one of the blog posts shows what I did. If there are hoops on the model, I am sure I had a reference basis. As far as the need or desirability of hoop on single tree masts, I would think that hoops would contribut strength and limit splitting in either case. I cannot offer advice on your model. What to do? I suggest research. I found many contemporary documents on line when reserching for YA. Reading through these can be difficult, sometimes frustrating and often inconclusive, but having done it you will be able to defend your choice with some confidence. Fincham is a good place to start. There are others. Ed
- 3,612 replies
-
- young america
- clipper
-
(and 1 more)
Tagged with:
-
I acually use a paper cutter depending on the thickness. Also, make sure to get uncoated material. Some craft sources sell coated material that does not tarnish, but also does not react to darkening. Ed
- 3,612 replies
-
- young america
- clipper
-
(and 1 more)
Tagged with:
-
EdT reacted to a post in a topic: Young America 1853 by EdT - FINISHED - extreme clipper
-
EdT reacted to a post in a topic: Young America 1853 by EdT - FINISHED - extreme clipper
-
When in doubt, Amazon. There's always Micromark. I got brass and copper wire, strips, plate, sheets etc from a variety of places - not one or even a few. A lot of hardware stores - like Ace - have K&S displays. The search for stuff is part of the fun. Ed
- 3,612 replies
-
- young america
- clipper
-
(and 1 more)
Tagged with:
-
EdT reacted to a post in a topic: Young America 1853 by EdT - FINISHED - extreme clipper
-
Hi Randy, On the scuppers, I probably just followed Crothers. Any pictures posted here would be much appreciated. I do not know if my model is on dislay at Mystic, but if you find out, let me know. Ed
- 3,612 replies
-
- young america
- clipper
-
(and 1 more)
Tagged with:
-
Ah, thank you Randy. Much better. Looks lovely - and very familiar. Ed
- 3,612 replies
-
- young america
- clipper
-
(and 1 more)
Tagged with:
-
Randy, Thanks for the photos. I don't seem to have the software to open these. I will try to get it later. Ed
- 3,612 replies
-
- young america
- clipper
-
(and 1 more)
Tagged with:
-
I remember making the decision and definitely had a reference, but cannot recall it, specifically. Suggest you look in the Bilbliography. It should be in one of those references. It certainly would have been cheaper at that time to use copper-zinc, ie yellow brass, than copper. If you have doubts, you may have do some of your own research. If my recollection improves I will advise. Ed
- 3,612 replies
-
- young america
- clipper
-
(and 1 more)
Tagged with:
-
Randy, If you have a reasonable basis for the scuppers I would go for it. I can't recall how I decided on these. I don't know if the model is on display. Ed
- 3,612 replies
-
- young america
- clipper
-
(and 1 more)
Tagged with:
-
Thanks for asking, Rob. The model is at Mystic Seaport. Ed
- 3,612 replies
-
- young america
- clipper
-
(and 1 more)
Tagged with:
-
Hello Randy, Seems like I neglected to show these on Drawing 1. Apologies. If you look closely at drawing 5, you will find small circles representing scuppers through the waterway between frames D and E, and 16-17. The third pair are obscured on the drawing by other construction but should be located between frames 32 and 33. I no longer have the model, so I cannot double check that, but in any event, these were located fairly arbitrarily in the model design. I made these by drilling at a slight downward angle thru the waterway, then inserted small brass tubes shaped flush at both ends. I am sure we would all appreciate your sharing some photos of your model. Good luck. Ed
- 3,612 replies
-
- young america
- clipper
-
(and 1 more)
Tagged with:
About us
Modelshipworld - Advancing Ship Modeling through Research
SSL Secured
Your security is important for us so this Website is SSL-Secured
NRG Mailing Address
Nautical Research Guild
237 South Lincoln Street
Westmont IL, 60559-1917
Model Ship World ® and the MSW logo are Registered Trademarks, and belong to the Nautical Research Guild (United States Patent and Trademark Office: No. 6,929,264 & No. 6,929,274, registered Dec. 20, 2022)
Helpful Links
About the NRG
If you enjoy building ship models that are historically accurate as well as beautiful, then The Nautical Research Guild (NRG) is just right for you.
The Guild is a non-profit educational organization whose mission is to “Advance Ship Modeling Through Research”. We provide support to our members in their efforts to raise the quality of their model ships.
The Nautical Research Guild has published our world-renowned quarterly magazine, The Nautical Research Journal, since 1955. The pages of the Journal are full of articles by accomplished ship modelers who show you how they create those exquisite details on their models, and by maritime historians who show you the correct details to build. The Journal is available in both print and digital editions. Go to the NRG web site (www.thenrg.org) to download a complimentary digital copy of the Journal. The NRG also publishes plan sets, books and compilations of back issues of the Journal and the former Ships in Scale and Model Ship Builder magazines.