-
Posts
632 -
Joined
-
Last visited
About CDR_Ret
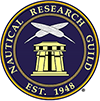
- Birthday February 1
Profile Information
-
Gender
Male
-
Location
Colorado Springs, Colorado, USA
-
Interests
The physical sciences; Worldview, science, and education; Technical and educational writing; Reading: Accurate historical fiction, classical science fiction, biographies; Wood carving and ship models; research projects relating to landform origins, especially the US East Coast Carolina Bays.
Recent Profile Visitors
-
CDR_Ret reacted to a post in a topic: Image Usage Rights -- Be Forewarned!
-
Beginner CAD recommendation
CDR_Ret replied to krith's topic in CAD and 3D Modelling/Drafting Plans with Software
You should visit the many threads in this CAD/3D Forum that address your question. For basic hull creation from plans, I believe that DELFTship Free will produce the most faired and smooth results. Then export the resulting model into other recommended programs to create the details. -
CDR_Ret reacted to a post in a topic: The Margheretta may have been found
-
TJM reacted to a post in a topic: Crew figures with Heroforge
-
thibaultron reacted to a post in a topic: Crew figures with Heroforge
-
Those guys all look pretty buff!. Aren't there any striplings in your crew? 🙂
-
CDR_Ret reacted to a post in a topic: 3D Naval Guns 1850s ~ 1870s
-
CDR_Ret reacted to a post in a topic: How were ballast stones held firmly in place to prevent them from shifting?
-
mtaylor reacted to a post in a topic: Downloading PDF files
-
CDR_Ret started following Nate's PANDORA in 3D , Downloading PDF files , Unidentified LTS Yard Support Rod and Attached Hardware-(1890s US Brigantine) and 1 other
-
Downloading PDF files
CDR_Ret replied to popeye2sea's topic in How to use the MSW forum - **NO MODELING CONTENT**
You might try these fixes: https://pdf.minitool.com/news/cant-download-pdf-files.html -
CDR_Ret reacted to a post in a topic: Nate's PANDORA in 3D
-
CDR_Ret reacted to a post in a topic: Decoration for 3D Victory printing
-
CDR_Ret reacted to a post in a topic: Albatros by Dr PR - FINISHED - Mantua - Scale 1:48 - Revenue Cutter kitbash about 1815
-
Keith Black reacted to a post in a topic: Ahoy!
-
And digital is even more forgiving and takes up zero space in the livingroom!😉 Terry
-
On submarines, we always slid down the main stairs between decks on the handrails with hands only. You controlled your speed with your grip. I even saw our COs do this on occasion! For vertical ladders, there were always hand grips positioned somewhere above the top rung to help the transition between ladder and the deck.
-
Hi Wefalck. Thanks for the pointer. In Underhill, Figure 44, there is indeed an image showing the lower topsail yard supporting rod/stay/strut. This is in the context of an iron and steel-sparred ship. The figure shows the upper end of the rod hinged to a hefty lug at the bottom of the center band, as stated earlier. The hinge plane was in line with the yard and vertical. The lower end of the rod terminated at the steel cross support at the base of the topmast. Scan from Figure 44, page 39, Masting and Rigging the Clipper Ship & Ocean Carrier, Harold A. Underhill, Reprint 1969; Brown, Son, and Ferguson, LTD Interestingly, all the diagrams of the LTS yard (including Fig. 44), show the LTS yard mainly supported by a swiveling crane arrangement, rather than the universal-jointed truss as in the lower yard (and as was the case for Galilee). So a crane plus a support rod for the LTS yard seems to be overkill except, perhaps, in larger ships. I finally found a side illustration of the LTS yard strut in Underhill, Plate 16, on page 80 (there is so much information buried in this book that it is easy to overlook things!). The plate illustration suggests that the lower end of the support strut is simply an eye-in-eye swivel, bolted through the forwardmost top platform crossbeam. So, lacking any other information, that's what I will go with. Plate No. 16, Ibid, showing the arrangement of the LTS yard support stay or strut. In Galilee's case, the entire weight of the LTS yard, hardware, rigging, and sail rests on this one rod! When the yard tilts, I'm still not sure how that motion is accommodated by this support system.🤔 Thanks for the prodding! Terry @wefalck @BANYAN
-
This is a plea for input from the general membership to identify the depicted iron hardware shown below and/or for direction to a source that illustrates (or at least describes) this object: What's it? The upper end of the rod is attached or hinged to the centerline band of the foremast lower topsail (LTS) yard. The bottom end of the rod is somehow attached to a cross-brace in the decking of the foretop platform. (Courtesy Carnegie Science Library, September, 1906) The ship it was used in was the US West Coast merchant brigantine Galilee, built at the Matthew Turner shipyard in Benicia, California, in 1891. The reference photos I am using are mostly from the period when the ship was chartered by the Department of Terrestrial Magnetism, Carnegie Institution, Washington, DC, between 1905 and 1908 for geomagnetic data collection in the Pacific Ocean basin. Captain Matthew Turner, by all accounts, was the most prolific shipbuilder on the West Coast during the latter 19th century, and he frequently incorporated in his wooden sailing ships innovations that were common to iron-masted sailing ships during this period. I have a variety of other images, all together indicating that this isn't some kind of running or standing rigging ropework. It's always absolutely straight and typically runs in a direction at an angle to all the other lines in its vicinity. At this point in the ship's life, virtually all iron standing and running rigging had been replaced with hemp in order to minimize the rigging's magnetic effect on the ship's instruments. Only structural iron that was absolutely necessary for the operation of the ship was retained. Other images: Various depictions of the LTS yard support rod. (Sources: left and right, Carnegie Science Library, c. 1905-1907; center, SAFR, prior to 1905) Any assistance would be greatly appreciated. Terry
-
I just noticed this problem tonight (3-Jan-25), but I was trying to add an image to a PM and noticed that all the usual buttons in the gray bottom margin for selecting and inserting images and attaching files to PMs and topical threads are missing. I can't even include a screenshot because this post is also missing the image/file controls. Is it MSW or my browser/computer? Terry
-
3D Printing Cannons in Resin
CDR_Ret replied to thibaultron's topic in 3D-Printing and Laser-Cutting.
Yessir, to virtually any number of decimal places you desire in either imperial or metric units. I use Blender mainly as a free 3D CAD program after Sketchup was no longer free to hobbyists. As others have mentioned, Blender has a steep learning curve, but there are helpful, experienced users in our community. Terry -
3D Printing Cannons in Resin
CDR_Ret replied to thibaultron's topic in 3D-Printing and Laser-Cutting.
Or you could move to the Dark Side for free and try 3D printing using the Blender extensions.🙂 -
Cold War madness
CDR_Ret replied to Martes's topic in CAD and 3D Modelling/Drafting Plans with Software
Brings back memories as a young USN air intelligence officer doing ship recognition briefings for the carrier pilots 'way back during the Cold War. Kotlins and Kashins involved in "shouldering" incidents in the Med. Krestas shadowing the CBGs. Fun times--not! -
Paviljoensjacht 1733 | Blender
CDR_Ret replied to Robska's topic in CAD and 3D Modelling/Drafting Plans with Software
Robska, You may have already noticed this, but there are some glaring errors between the various views in these plans: At the bow in the halfbreadth view, there appears to be a very wide rail wrapping around the bow of the vessel. But if you look at the profile elevation view, the planking of the bow wraps up and back toward the stern, forming a very cheeky profile. The upper railing is well aft of the forward edge shown in the lower view. The two views simply don't match (unless the railing details were omitted for some reason in the lower view). At the stern, referring to profile elevation, the intersection of the poop deck's side railing and the molding around the stern windows corresponds to the extent of the deck planking in the lower view. So, unless the deck planking is flush with the railing (unlikely), there is a problem with the drawing in this area. What is the provenance of this drawing? How old is it and from what was it taken? Terry -
Paviljoensjacht 1733 | Blender
CDR_Ret replied to Robska's topic in CAD and 3D Modelling/Drafting Plans with Software
One of the more difficult aspects of getting started in DELFTship for the novice user is inserting the background reference images. May I suggest that you download the tutorial I created several years ago (attached). I haven't updated these files for the current version of DELFTship Free, so the manual references and illustrations showing program controls will not reflect the latest version. You should be able to sort things out, since the background image insertion feature hasn't changed much, if at all. I recommend reading all five parts of the tutorial before starting a model. Please message me if you run into issues getting started. The tutorial is quite wordy, I'm afraid, but it does the job the Manual does not. Just take your time working through it. If you find any mistakes, please let me know so I can correct them. No one has reported any issues in the past two years! This is how a complete hull appears displaying the Gaussian surface ("Gauss") tool. I used my 1891 brigantine Galilee model for this example. Surfaces that are either flat or curve in only one direction (like a cylinder) are green. Surfaces that curve in more than direction shade toward yellow, orange, and red, depending on the rate of curvature. This tool takes some practice to interpret the fairness of the hull shape—and how to make corrections. The image also shows the station, waterline, and buttock "intersections" with the outer hull surface. You can add as many intersections as you like to help define the hull shape. Just remember that you are trying to match the intersection lines to the corresponding lines in the plans, not the control net nodes! The "Zebra" and "Environmental map" surface reflections shown on the tool bar are more helpful in surfaces that are geometrically smooth, like fiberglass (think: racing yacht). The Gaussian tool is fine for wooden hulls. Don't be surprised if you find that the as-drawn plans aren't smooth and fair in this program. The plans reflect their age, drafting methods, and provenance. You will have to decide how great a departure from the plans you will accept to obtain a smooth hull! DELFTship is a mathematical program. Wooden ships are handcrafted. Terry Part 1-DELFTship_Bkgrd_Images.pdf Part 2-DELFTship_Bkgrd_Images.pdf Part 3-DELFTship_Bkgrd_Images.pdf Part 4-DELFTship_Bkgrd_Images.pdf Part 5-DELFTship_Bkgrd_Images.pdf
About us
Modelshipworld - Advancing Ship Modeling through Research
SSL Secured
Your security is important for us so this Website is SSL-Secured
NRG Mailing Address
Nautical Research Guild
237 South Lincoln Street
Westmont IL, 60559-1917
Model Ship World ® and the MSW logo are Registered Trademarks, and belong to the Nautical Research Guild (United States Patent and Trademark Office: No. 6,929,264 & No. 6,929,274, registered Dec. 20, 2022)
Helpful Links
About the NRG
If you enjoy building ship models that are historically accurate as well as beautiful, then The Nautical Research Guild (NRG) is just right for you.
The Guild is a non-profit educational organization whose mission is to “Advance Ship Modeling Through Research”. We provide support to our members in their efforts to raise the quality of their model ships.
The Nautical Research Guild has published our world-renowned quarterly magazine, The Nautical Research Journal, since 1955. The pages of the Journal are full of articles by accomplished ship modelers who show you how they create those exquisite details on their models, and by maritime historians who show you the correct details to build. The Journal is available in both print and digital editions. Go to the NRG web site (www.thenrg.org) to download a complimentary digital copy of the Journal. The NRG also publishes plan sets, books and compilations of back issues of the Journal and the former Ships in Scale and Model Ship Builder magazines.