-
Posts
2,271 -
Joined
-
Last visited
About Dr PR
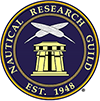
Contact Methods
-
Website URL
https://www.okieboat.com
Profile Information
-
Location
Corvallis, OR, USA
Recent Profile Visitors
The recent visitors block is disabled and is not being shown to other users.
-
ccoyle reacted to a post in a topic: USS Cape (MSI-2) by Dr PR - 1:48 - Inshore Minesweeper
-
ccoyle reacted to a post in a topic: USS Cape (MSI-2) by Dr PR - 1:48 - Inshore Minesweeper
-
vaddoc reacted to a post in a topic: USS Cape (MSI-2) by Dr PR - 1:48 - Inshore Minesweeper
-
Canute reacted to a post in a topic: USS Cape (MSI-2) by Dr PR - 1:48 - Inshore Minesweeper
-
woodartist reacted to a post in a topic: Lady Nelson by JGoff - Amati/Victory Models - 1:64 - First Ship Build
-
Canute reacted to a post in a topic: USS Cape (MSI-2) by Dr PR - 1:48 - Inshore Minesweeper
-
Coyote_6 reacted to a post in a topic: USS Cape (MSI-2) by Dr PR - 1:48 - Inshore Minesweeper
-
After the tape is removed there are raised ridges of dry paint that formed along the tape edges. I have dealt with this in several ways. 1. I have VERY carefully scraped the raised paint with the tip of a #11 blade. The paint should not be too hard to avoid chipping. You need a steady hand for this! 2. On the Cape model I used a small file with a narrow tip. It must be held parallel to the hull surface, and it is best to align the shaft of the file along the paint edge. Using very gentle pressure the high points in the paint are filed off. 3. I have sanded the hull after the paint is very dry with very fine grit (#600) paper. Allow at least a week for acrylic paint to harden. Sanding the paint edges is incidental to producing a very smooth surface prior to applying a finishing coat of clear varnish or shellac. I would use this method to produce a glass smooth surface like on the hulls of modern racing yachts, or boats with fiberglass hulls. **** I used a clear acrylic sealer (FolkArt all-purpose sealer49909) on all the wood on the hull. Even though the acrylic sealer is water based I didn't notice much raised "fuzz" after the first coat. The hull was sealed and sanded at least three times before the outer layer of sheathing was applied. That was sealed and sanded once (I didn't want to fill the cracks between the sealing planks). The deck was sealed and sanded at least twice. This produced a fairly smooth hull with visible planks like the original ship. It was all finished with #0000 steel wool before painting. I applied water based FolkArt satin varnish to the deck and then finished it with #0000 steel wool. I plan to apply this varnish to the entire hull to get a uniform satin finish. **** Many people avoid steel wool because it can leave tiny metal bits embedded in the paint. These can then rust over time in a humid environment. I always brush off the dust and loose steel wool fibers. Then I scrub with a stiff brush to remove any remaining metal, and wipe the surface several times with a damp rag. After this I rub a strong magnet over the entire surface - it is surprising how much metal "dust" remains. I have been doing this for half a century and have never had a problem with rusty fragments. This is in western Oregon where it rains from October to May. and people consider it a drought if the ground gets dry!
- 279 replies
-
- minesweeper
- Cape
-
(and 1 more)
Tagged with:
-
yvesvidal reacted to a post in a topic: USS Cape (MSI-2) by Dr PR - 1:48 - Inshore Minesweeper
-
AJohnson reacted to a post in a topic: USS Cape (MSI-2) by Dr PR - 1:48 - Inshore Minesweeper
-
Paul Le Wol reacted to a post in a topic: Steam Schooner Wapama 1915 by Paul Le Wol - Scale 1/72 = From Plans Drawn By Don Birkholtz Sr.
-
I have been putting the finishing touches on the hull. First off was painting the hull. I used the laser level to mark off the top and bottom of the boot topping (black stripe at the waterline). Then I used yellow-green auto detailing striping tape to mask off the boot topping area. The upper gray part and the lower red parts were then painted. After the paint dried overnight I removed the striping tape. Then more tape was applied over the gray area just above the top of the boot topping. Another strip of tape was placed over the red paint at the bottom of the boot topping. This masked off the areas around the boot topping area. Then I painted along the edges of the boot topping, using gray paint along the upper edge and red paint at the lower edge. This paint sealed the edges of the tape. If any paint flowed under the tape it would be the same color as the paint already there. After this paint dried I applied the black paint to the boot topping, flowing over the edges of the tape slightly. It looks pretty sloppy at this point. After the black paint dried I removed the striping tape. This left nice clean edges for the boot topping. I still need to finish painting the transom. The areas between the guard timbers cannot be masked and must be painted by hand. I will wait until tomorrow morning to do this after a good night's sleep and my first cup of coffee. The blueprints say the gray was Haze Gray formula 5H. I couldn't find any supplier of this color - it has since been discontinued for a different formula. The original haze gray used in WWII was a much darker blue gray. After the war the US Navy changed to a much lighter neutral gray that was called "Ocean Gray" for a while. I think this was what we used on the Cape and the USS Oklahoma City CLG-5. But the name seems to have been changed back to Haze Gray, Then later on yet another Haze Gray formula was created and I think this is what is used today. But there seems to be a lot of confusion as to which "Haze Gray" was used and when. I gave up trying to match the 5H color and used a fairly neutral light gray. The red is supposed to be Anti-Fouling Red formula 121. Again I couldn't find this exact color, so I chose a moderately dark red. The blueprints call for Boot Topping Black formula 3. I just used some black paint I had in my paint box. The paints were all acrylic "craft" paints. They dry quickly and are water washable. DecoArt Slate Gray DAO68 DecoArt Primary Red DA199 craft smart Black 371081 These paints coat well and required just two thin layers applied a day apart. The only problem I had came when I removed the striping tape after painting the boot topping. The tape lifted the red and gray paints from the brass stem band. The brass was smooth and shiny, and apparently did not have enough "tooth" (roughness) for the acrylic paints to adhere to. However, the paint had only dried over night, and if I had waited a week or two before applying the tape it might have held up better. But it was easy to touch up the missing paints. With the painting mostly done I could install the propeller and rudder. The Bluejacket Shipcrafters propeller was a bright shiny silvery color, but the blueprints call for a bronze piece. I painted it with FolkArt Brushed Bronze metallic acrylic paint. It dried hard, and I have seen no chipping of the paint with handling. I left the sea chests for the propulsion engines and minesweep generator engines bare metal. The "zincs" around the sea chests, propeller and rudder are thin pieces of brass. I painted them with some ancient Chromatone silver enamel paint that I think I have had since 1977! I still need to apply some rub-on numbers for the draft markings at the bow and stern. And there is the hull number to be applied in true Cape fashion. Then I will seal everything with a satin acrylic varnish.
- 279 replies
-
- minesweeper
- Cape
-
(and 1 more)
Tagged with:
-
Dr PR reacted to a post in a topic: Pomeranian Rahschlup 1846 by wefalck – 1/160 scale – single-masted Baltic trading vessel
-
No matter how you do it 3 mm blocks are fiddly! Your stropping looks good.
- 82 replies
-
- Lady Nelson
- Amati
-
(and 2 more)
Tagged with:
-
Dr PR reacted to a post in a topic: Planking disaster
-
Dr PR reacted to a post in a topic: Steam Schooner Wapama 1915 by Paul Le Wol - Scale 1/72 = From Plans Drawn By Don Birkholtz Sr.
-
Dr PR reacted to a post in a topic: Sternwheeler From the Susquehanna River's Hard Coal Navy by Keith Black - 1:120 Scale
-
Thanasis, Good idea! The metal clip makes a good handle to control the sandpaper. The one problem I see with this is that the grit along the edge of the fold can remove material from the bottom of the groove, making it deeper. With the deck planking application it really won't matter much if the plank is a tight fit into the groove. I put glue on the bottom of the plank (you could put it in the groove) and press the planks into the groove most of the way. Then I use a wooden stick to press the plank down so the top of the plank is level with the tops of the neighboring planks. So the plank won't slide too deep in the groove. Druxey, You have hit upon the thing that worried me the most. There are several ways to widen the groove, and most have the potential to remove too much of one of the planks on the side that would make a very visible curve in the grout line. However, one method to widen the groove hasn't been mentioned yet, and it is just asking for trouble! I did use a new #11 blade to remove wood from the sides of the groove! I held the blade flat against the edge of the planks on the side of the groove, and then rotated it slightly to get the sharp edge angled into the wood - like the blade of a plane. Then I carefully shaved very thin slices off the plank edge, moving in the direction with the grain so the blade wouldn't cut too deep. This was a "high pucker factor" operation. But it worked! One of the problems I had with the thin planks was that they bent very easily, and if I didn't get the nibbing in deep enough into the nibbing plank the plank would develop a slight curvature. This happened a couple of times and I didn't notice until I had installed another plank or two. Looking along the length of the planks the curvature was obvious - the planks were supposed to be parallel to the centerline of the deck. I had to rip up a few planks and then "plane" away excess material from the remaining planks to straighten the edges. Nasty! A few of the planks do have a slight taper toward the nibbed end, but because the entire batch of planks varied in width so much you would have to look very closely to see it.
-
Dr PR reacted to a post in a topic: Red Jacket by John Ruy - Marine Model Company - 1/16”=1’ (1/192 scale) - Vintage Solid Hull Clipper Ship Kit
-
Johnny, I think Thanasis' suggestion to use sandpaper is a good one. If the paper was wrapped around something a bit narrower than the groove, so the sandpaper was a slip fit into the groove, it would remove material from both sides in equal amounts, keeping the sides more or less parallel lengthwise. That is a potential problem because I want the planks/grooves to have straight edges and more or less the same width through their entire length. Making the grooves "\_/" shaped runs the risk of having different widths at the top edges (edges not straight), and that would be visibly noticeable in this application (deck planking). For what it is worth, I did file the bottom edges of the paper "grout" to make the bottom of the plank a bit narrower. This helped get it started in the groove. But I didn't want to make it too tight because the paper is easily distorted if you force the plank into the groove, pushing the paper up and possibly out of the groove. If that happens you have to start all over again to replace the distorted "grout." So you really need a groove wide enough for the plank to easily slip fit in place. I should also say that I really didn't have this problem when planking my topsail schooner deck because the planks were 5 mm (about 1/4 inch) wide. They did not bend easily. These 1/6 inch planks bend like wet spaghetti! And I was able to place straight runs of planking that were nibbed only at the outboard edges - no tapering to fit around a deck house with non-parallel sides. The MSI built posed some new challenges.
-
Good ideas! If you look at the second photo in my original post you will see two hobby knives with #11 blades. The blade on the right has been ground down to make a narrow chisel about 1/2 plank width. I used it to make the initial cut in the nibbing strake where the plank end is nibbed into the strake. I also used the sides of the "chisel" to scrape the edges of the groove to widen it. It did work, but it was slow going. On the other hand, I did want to remove material gradually until the plank just fit into the groove with a slip fit. So slow was good. I didn't mention this at first because I didn't want to bias answers. I do have a set of wood chisels that I use to remove material from grooves (but none as narrow as 1/16 inch). Usually I use a saw to define the width of the channel and a narrower chisel to gouge out material between the saw kerfs. I don't know that I have a steady enough hand to work a plank width chisel between the adjacent planks and keep a straight edge along the sides of the channel. Any other suggestions?
-
Thanasis and Druxey, Thanks for the suggestions. I don't want to shape the plank - it is already shaped to the desired width, and has the paper grout glued to it. I am looking for ways to widen a narrow groove, preferably keeping the more or less vertical sides of the groove. I suppose I could glue sandpaper to a thin enough stiff object so it could fit down into the groove.
-
I have been planking the decks on my MSI model and ran into a challenging problem. The planks are pretty thin (1/16 x 1/16 inch or 1.6 x 1.6 mm) and flexible. They are nibbed into a nibbing strake along the edges of the deck. The deckhouse sides are not parallel, so the planks have to be tapered to fit along the house sides. Planking at the bow and stern is pretty simple, but these deck sections meet along the house sides. Keeping the decking pattern straight and parallel to the centerline was pretty tricky in this area! The planks have 0.005 inch (0.13 mm) black paper "grout" glued along the edges. The last plank between the forward and aft planking is nibbed into the nibbing strake and sandwiched between two neighboring planks. Because it is the last plank it has paper grout along both edges. It is a very tight fit into the groove between the neighboring planks. And because the planks actually varied quite a bit in width it was a problem getting the last plank to fit into the groove. Here are a couple more photos to illustrate the problem. QUESTION: How would you go about widening the groove so the last plank would fit? This is a pretty narrow groove! The small file shown in the pictures was 0.055 inch (1.4 mm) thick, only slightly thinner than a plank. It didn't remove much material and I had to be careful not to foul the opposing top edge of the neighboring plank. And it tended to remove more material from the bottom of the groove (not good) than along the sides. What other method would you suggest to remove very small amounts of wood from the sides of the planks along the groove?
-
I'm back! I was occupied for about 2 1/2 weeks auditing the books for a non-profit that I am Treasurer for. I was checking every penny coming into and leaving the organization for 13 years, including restricted and unrestricted funds. I found a few errors, and after corrections everything balances for every month of the entire 13 years! Then I finished laying all of the deck planking on the Cape model. Don't ask how many individual planks there are - I have no idea! But there are a lot! Just aft of the superstructure are two grouts running perpendicular to the plank lengths. This was a "portable" or lift out deck section directly above the main propulsion engines. This is still a rough planking. I have scraped, filed and sanded a bit, but the final smoothing and finishing is still to do. The planks varied in width and height between 0.052 and 0.072 inch (1.3 and 1.8 mm). I carefully measured distances from centerline to deck edges all along the length of the ship - and they were the same everywhere (I was pretty careful with this when I put the plankshears and nibbing strakes on). I figured random choices for planks would even out to port and starboard, but it didn't work that way (Murphy again). The starboard side at the stern gained about 1/4 a plank width at the edge of the deck well. From there I used thinner planks on the starboard side and thicker planks to port. The port side came out perfect with a full plank width finishing out the planking along the stern planksheer. But the starboard side was still almost a half plank too wide and had to be cut into the nibbing strake. But I doubt anyone would notice, and that area will be covered with minesweeping gear anyway. The next time I plank a deck - especially if the planks are so thin that they bend easily - I will draw a series of lines parallel to the centerline and equally spaced on either side. These will serve as references to catch any planking "creep" wider or thinner on one side from the other. The deck planks are about 1/16 x 1/16 inch (1.6 x 1/6 mm) and that is pretty small to be making nibbing. Because the deckhouse sides are not parallel, and the nibbing strake curves along the deck edge, the planking pattern was pretty complex along the sides of the deckhouse. This led to a problem with tapering planks along the deckhouse sides and nibbing planks into the nibbing strake. Bringing the decking from the bow and that from the stern together caused a problem, and this was exacerbated by the varying plank widths. The starboard side came out almost perfect, but I had to do some creative planking on the port side to make things come out right. The last plank on the model ended up sandwiched between outboard nibbed planks and inboard tapered planks. It had to fit into a one plank wide groove - and was nibbed into the nibbing strake. And because it was the last plank it had paper grout strips down both sides. I picked a pretty narrow strip (about 0.060 inch or 1.5 mm) but it was a tight fit with the paper grout glued on. This called for some creative widening of the groove between neighboring planks. But it finally dropped into place with a bit of pressure. I know some people think the grout between planks on a model should be more imagined than seen. But the Cape's decks were holystoned and bleached, and the grout stood out very visible. The "grout" on the model is black paper 0.005 inch (0.13 mm) thick, and that is 0.24 inch at 1:48 scale. The blueprints say the grout was 1/4 inch wide in the ship's decks.
- 279 replies
-
- minesweeper
- Cape
-
(and 1 more)
Tagged with:
-
By all means do start a build log! No build is perfect, and our explanations of how to do things aren't always clear. Another log will just provide more information for others to follow.
-
Dr PR reacted to a post in a topic: Sternwheeler From the Susquehanna River's Hard Coal Navy by Keith Black - 1:120 Scale
-
Dr PR reacted to a post in a topic: Mary Day by jdbondy - 1:64 scale (3/16" to 1 foot) - Schooner
-
Your last photo shows the outer edge planks with "hooks" that the next plank fits into. But the drawing above it shows only one plank "hooked" where a separate "nibbing strake" fits into. The subsequent planks are nibbed into this nibbing strake. In some plans the nibbing strake is called a "margin plank."
About us
Modelshipworld - Advancing Ship Modeling through Research
SSL Secured
Your security is important for us so this Website is SSL-Secured
NRG Mailing Address
Nautical Research Guild
237 South Lincoln Street
Westmont IL, 60559-1917
Model Ship World ® and the MSW logo are Registered Trademarks, and belong to the Nautical Research Guild (United States Patent and Trademark Office: No. 6,929,264 & No. 6,929,274, registered Dec. 20, 2022)
Helpful Links
About the NRG
If you enjoy building ship models that are historically accurate as well as beautiful, then The Nautical Research Guild (NRG) is just right for you.
The Guild is a non-profit educational organization whose mission is to “Advance Ship Modeling Through Research”. We provide support to our members in their efforts to raise the quality of their model ships.
The Nautical Research Guild has published our world-renowned quarterly magazine, The Nautical Research Journal, since 1955. The pages of the Journal are full of articles by accomplished ship modelers who show you how they create those exquisite details on their models, and by maritime historians who show you the correct details to build. The Journal is available in both print and digital editions. Go to the NRG web site (www.thenrg.org) to download a complimentary digital copy of the Journal. The NRG also publishes plan sets, books and compilations of back issues of the Journal and the former Ships in Scale and Model Ship Builder magazines.