-
Posts
531 -
Joined
-
Last visited
About LyleK1
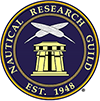
- Birthday 03/20/1961
Profile Information
-
Gender
Male
-
Location
Washington State, USA
-
Interests
Boating, model ship building, woodworking and computers.
Recent Profile Visitors
-
robert952 reacted to a post in a topic: Half Hull Planking Project
-
Mr Whippy reacted to a post in a topic: HMAV Bounty by fifthace - Caldercraft - 1:64
-
Scottish Guy reacted to a post in a topic: Professional Building Slip - Hobbyzone
-
Scottish Guy reacted to a post in a topic: Professional Building Slip - Hobbyzone
-
Scottish Guy reacted to a post in a topic: Professional Building Slip - Hobbyzone
-
Scottish Guy reacted to a post in a topic: Professional Building Slip - Hobbyzone
-
Scottish Guy reacted to a post in a topic: Professional Building Slip - Hobbyzone
-
Scottish Guy reacted to a post in a topic: Professional Building Slip - Hobbyzone
-
LyleK1 reacted to a post in a topic: HMS Bounty by Trond - Billing Boats - 1:50
-
LyleK1 reacted to a post in a topic: HMS Bounty by Trond - Billing Boats - 1:50
-
LyleK1 reacted to a post in a topic: HMS Bounty by Trond - Billing Boats - 1:50
-
yvesvidal reacted to a post in a topic: HMS Bounty by Trond - Billing Boats - 1:50
-
LyleK1 reacted to a post in a topic: HMS Bounty by Trond - Billing Boats - 1:50
-
AJohnson reacted to a post in a topic: HMS Bounty by Trond - Billing Boats - 1:50
-
LyleK1 reacted to a post in a topic: HMS Bounty by Trond - Billing Boats - 1:50
-
Clumsy and not paying close enough attention... it happens to the best of us! I appreciate your thoughts... no changes at home... unfortunately. However, I do have some help and wandered back to my workshop a few days ago! Although, I cannot spend as much time as I was on her... expect to see some updates again in the near future. The Bounty will get done!
-
LyleK1 reacted to a post in a topic: HMS Bounty by LyleK1 - Artesania Latina - 1:48 scale
-
They are on the stern... but I get your question. I used a brass tubing which is softer and easier to work... using a small amount of heat and a thread spool as a form, I just heated it up and bent it around the spool. As a side not, unfortunately, I bumped the starboard side tubing during some of the rigging work and broke the wire going to the light in the lantern... about made me cry!! I tried for several hours to get a piece of the wire pulled out to reconnect it... in the end, I had to give up... just is not possible. Makes me sick! But stuff happens!
-
Just a quick update... Some times in life we are dealt a hand that doesn't seem fair! I'm dealing with that right now as my wife is very ill and I am spending most of my days caring for her. The Bounty is on hold for now but not forgotten and I will finish her but priorities come first. Hope all of you have a Merry Christmas and a Happy New Year! I see you all then!
-
LyleK1 reacted to a post in a topic: HMS Bounty by LyleK1 - Artesania Latina - 1:48 scale
-
LyleK1 reacted to a post in a topic: Unboxing 15th century wooden boat by thibaultron - Ships of Pavel Nikitin - 1:48
-
LyleK1 reacted to a post in a topic: Unboxing 15th century wooden boat by thibaultron - Ships of Pavel Nikitin - 1:48
-
LyleK1 reacted to a post in a topic: HMS Bounty by LyleK1 - Artesania Latina - 1:48 scale
-
Takes a bit to get back into things! But after a few days of familiarizing myself, I got moving on finishing the main mast. I decided to furl the sails on the main mast. It keeps the sails and associated lines present but leaves the ship more open to viewing. And it still meets the look I am trying to achieve Here are a few pictures with top gallant and top sails essentially done and the course sail in progress with the lower yard just installed today: And off we go! More in a few days as I am focused on getting through the build by years' end... but not rushing it!
-
Welcome back!
-
So for this update, I thought I would go through how I mount a sail to the yard and then mount the yard and run the rigging for that sail. The sail I'm working on is the Main Top Sail. I begin by cutting several small ropes about 2.5" long to tie the sail to the yard. Once cut, using a needle, I attach each piece to the sail: ... and tie it to the yard using a simple overhand knot. After all are attached and the sail positioned equally side to side, I cut the excess rope and use a dab of CA glue on the knots to ensure nothing comes loose: Next, I layout the position of the blocks to be added to the sail and tie the block needed: The blocks are attached with a simple overhand knot and the loose ends removed, again, using a spot of glue on each: I cheat a little when hanging my yards! Trust me, it makes thing soooo much easier in the long run. There is so much work that goes into each and every sail that it is nearly impossible to get the yard to stay put! I cut a small piece of brass rod and drill a hole into the mast and the yard in the position that I plan to mount the yard. A dab of CA is used on the mast side of the rod only... I do not glue the yard to the rod. This allows me some freedom of movement but not so much as to be frustrating: The yard is mounted: Let the rigging begin! I do the yard lifts first. I run the lines to their end points but I do not tie them off until I have the lines run for each type. So, for example, I run all the bunt and leech lines before tightening and tying off: And then I realized I had forgotten to attach the Parrel to the yard before hanging! Not too difficult to recover! But would've been a whole lot easier to have done it on the table: Once all the lines are run, I begin drawing them up to shape my sail. As noted, I'm displaying my Bounty with the sails in a dry-set configuration. The sail is shaped but still needs some finesse! In this case, I'll leave the lines loose until I have the Main sail up and can figure out what will look best: It looks similar to the Fore mast top sail... maybe to much... dunno yet! I am going through rope so fast! I have to stop and make more before moving on. Be back in a month or so! Off to Europe for a month!
-
LyleK1 started following USS Constitution by Unegawahya - Model Shipways - scale 1:76
-
What a great summer! Lots of boating, sunshine, good friends and good food! Back in the work shop for a few weeks before heading to Europe for a month later this month! After tying a whole lot of blocks, I've completed the main mast and mizzen mast yards. Additionally, the mizzen booms are done too: With all of them completed, I'll be concentrating on aging the sails (method shown in a previous post) and hanging them on the yards and boom. Hoping to get this work done before leaving... again! Still hopeful of finishing her by years' end! We'll see!
-
My final update for a few months... off on the boat until late August! Just about finished with the yards and booms for the main mast and mizzen mast: Some quick pictures of the current state of the Bounty: Be back at it in September! Expecting to finish by years' end. Have a great summer and thanks for hanging with my log!
About us
Modelshipworld - Advancing Ship Modeling through Research
SSL Secured
Your security is important for us so this Website is SSL-Secured
NRG Mailing Address
Nautical Research Guild
237 South Lincoln Street
Westmont IL, 60559-1917
Model Ship World ® and the MSW logo are Registered Trademarks, and belong to the Nautical Research Guild (United States Patent and Trademark Office: No. 6,929,264 & No. 6,929,274, registered Dec. 20, 2022)
Helpful Links
About the NRG
If you enjoy building ship models that are historically accurate as well as beautiful, then The Nautical Research Guild (NRG) is just right for you.
The Guild is a non-profit educational organization whose mission is to “Advance Ship Modeling Through Research”. We provide support to our members in their efforts to raise the quality of their model ships.
The Nautical Research Guild has published our world-renowned quarterly magazine, The Nautical Research Journal, since 1955. The pages of the Journal are full of articles by accomplished ship modelers who show you how they create those exquisite details on their models, and by maritime historians who show you the correct details to build. The Journal is available in both print and digital editions. Go to the NRG web site (www.thenrg.org) to download a complimentary digital copy of the Journal. The NRG also publishes plan sets, books and compilations of back issues of the Journal and the former Ships in Scale and Model Ship Builder magazines.