
Paul Le Wol
NRG Member-
Posts
887 -
Joined
-
Last visited
About Paul Le Wol
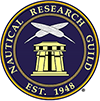
Profile Information
-
Location
Mount Hope, Ontario
Recent Profile Visitors
The recent visitors block is disabled and is not being shown to other users.
-
Paul Le Wol reacted to a post in a topic: Muscongus Bay Lobster Smack by JacquesCousteau - Model Shipways - 1:32 - Rescaled and Modified
-
Paul Le Wol reacted to a post in a topic: Mary Rose by Baker - scale 1/50 - "Your Noblest Shippe"
-
Paul Le Wol reacted to a post in a topic: USS Constitution by Der Alte Rentner - Model Shipways - 1/76
-
Paul Le Wol reacted to a post in a topic: Sternwheeler From the Susquehanna River's Hard Coal Navy by Keith Black - 1:120 Scale
-
Paul Le Wol reacted to a post in a topic: Sternwheeler From the Susquehanna River's Hard Coal Navy by Keith Black - 1:120 Scale
-
Paul Le Wol reacted to a post in a topic: Muscongus Bay Lobster Smack by JacquesCousteau - Model Shipways - 1:32 - Rescaled and Modified
-
Paul Le Wol reacted to a post in a topic: Muscongus Bay Lobster Smack by JacquesCousteau - Model Shipways - 1:32 - Rescaled and Modified
-
Canute reacted to a post in a topic: New BlueJacket Shipcrafters kit in development: West Coast lumber schooner
-
Paul Le Wol reacted to a post in a topic: PHOENIX 1787 by ccoyle - Master Korabel - 1/72 - Russian brigantine of the Black Sea Fleet
-
Paul Le Wol reacted to a post in a topic: PHOENIX 1787 by ccoyle - Master Korabel - 1/72 - Russian brigantine of the Black Sea Fleet
-
Keith Black reacted to a post in a topic: Muscongus Bay Lobster Smack by JacquesCousteau - Model Shipways - 1:32 - Rescaled and Modified
-
JacquesCousteau reacted to a post in a topic: Muscongus Bay Lobster Smack by JacquesCousteau - Model Shipways - 1:32 - Rescaled and Modified
-
Keith Black reacted to a post in a topic: Muscongus Bay Lobster Smack by JacquesCousteau - Model Shipways - 1:32 - Rescaled and Modified
-
Keith Black reacted to a post in a topic: Muscongus Bay Lobster Smack by JacquesCousteau - Model Shipways - 1:32 - Rescaled and Modified
-
Keith Black reacted to a post in a topic: TWILIGHT 2007-2009 by MAGIC's Craig - Scale 1:16 - RADIO - Pacific Northwest cruising powerboat
-
MAGIC's Craig reacted to a post in a topic: Steam Schooner Wapama 1915 by Paul Le Wol - Scale 1/72 = From Plans Drawn By Don Birkholtz Sr.
-
MAGIC's Craig reacted to a post in a topic: Steam Schooner Wapama 1915 by Paul Le Wol - Scale 1/72 = From Plans Drawn By Don Birkholtz Sr.
-
MAGIC's Craig reacted to a post in a topic: TWILIGHT 2007-2009 by MAGIC's Craig - Scale 1:16 - RADIO - Pacific Northwest cruising powerboat
-
Glen McGuire reacted to a post in a topic: Steam Schooner Wapama 1915 by Paul Le Wol - Scale 1/72 = From Plans Drawn By Don Birkholtz Sr.
-
Hi Steve, thank you for posting the photo of your beautiful Willapa. I hope to see more. I had noticed the metal attached to the corners in Phil’s photos but for some reason I thought that they were added when she became a museum ship. I appreciate the information about the hardwood corners. There may be a few things that I let slide but overall I will try to be accurate. ( something I am not known for 😀) . Thank you so much for your Comment, I appreciate it very much!
-
Hi Everyone, hope you are all doing fine. Thanks to all for the Comments and Likes! This update starts with the making of the waterways for the foc'sle deck. They were cut from a sheet of 1/16" AYC and sanded to shape. The coamings are made by layering three 1/16" x 3/16" strips. The waterways were scribed to show where the center plank is located and pins were placed to support it while it was attached with CA. The outer plank was glued to the center plank and the waterway with white PVA The inner planks were glued to the center planks and the waterways also with PVA. The thickness of the inner plank was tapered to 1/32" because the coaming gets narrower towards the aft end. I made a sanding stick long enough to span the deck and sanded the tops smooth The coaming across the aft edge of the deck was installed and after some sanding it went to the paint booth The deck planking was laid out to where it stops at the pad for the anchor winch. The 18" x 18" bitt slides into the hole that was left in the bulkhead former The planking from the winch pad aft and the forward planking didn't match in width so the next planks on either side of the pad needed a width adjustment. The smaller bitts port and starboard were the next obstacles. A small pad was glued to the bottom of these bitts to to help them sit vertically when they are glued to the horizontal bulkhead spacer just below the subdeck The last planks go and get all fancy. They will be covered in the next update Hope to see you then
-
Kevin, Mike and yourself did a great interview. Thank you
- 1,082 replies
About us
Modelshipworld - Advancing Ship Modeling through Research
SSL Secured
Your security is important for us so this Website is SSL-Secured
NRG Mailing Address
Nautical Research Guild
237 South Lincoln Street
Westmont IL, 60559-1917
Model Ship World ® and the MSW logo are Registered Trademarks, and belong to the Nautical Research Guild (United States Patent and Trademark Office: No. 6,929,264 & No. 6,929,274, registered Dec. 20, 2022)
Helpful Links
About the NRG
If you enjoy building ship models that are historically accurate as well as beautiful, then The Nautical Research Guild (NRG) is just right for you.
The Guild is a non-profit educational organization whose mission is to “Advance Ship Modeling Through Research”. We provide support to our members in their efforts to raise the quality of their model ships.
The Nautical Research Guild has published our world-renowned quarterly magazine, The Nautical Research Journal, since 1955. The pages of the Journal are full of articles by accomplished ship modelers who show you how they create those exquisite details on their models, and by maritime historians who show you the correct details to build. The Journal is available in both print and digital editions. Go to the NRG web site (www.thenrg.org) to download a complimentary digital copy of the Journal. The NRG also publishes plan sets, books and compilations of back issues of the Journal and the former Ships in Scale and Model Ship Builder magazines.