-
Posts
659 -
Joined
About David Lester
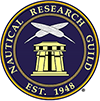
- Birthday 10/01/1952
Profile Information
-
Gender
Male
-
Location
Cobourg, Ontario
-
Interests
reading, woodworking, architecture
Recent Profile Visitors
-
wmherbert started following David Lester
-
David Lester reacted to a post in a topic: St. Roch by David Lester - FINISHED - Billing Boats - 1:72
-
CiscoH reacted to a post in a topic: St. Roch by David Lester - FINISHED - Billing Boats - 1:72
-
SiriusVoyager reacted to a post in a topic: St. Roch by David Lester - FINISHED - Billing Boats - 1:72
-
David Lester reacted to a post in a topic: St. Roch by David Lester - FINISHED - Billing Boats - 1:72
-
petervisser reacted to a post in a topic: St. Roch by David Lester - FINISHED - Billing Boats - 1:72
-
Harvey Golden reacted to a post in a topic: St. Roch by David Lester - FINISHED - Billing Boats - 1:72
-
Thank you everyone for all the kind comments and likes! Now I just have to find a place to put it; my collection is getting out of hand. Thanks again, David
- 61 replies
-
- St. Roch
- Billing Boats
-
(and 1 more)
Tagged with:
-
chris watton reacted to a post in a topic: St. Roch by David Lester - FINISHED - Billing Boats - 1:72
-
chris watton reacted to a post in a topic: St. Roch by David Lester - FINISHED - Billing Boats - 1:72
-
chris watton reacted to a post in a topic: St. Roch by David Lester - FINISHED - Billing Boats - 1:72
-
yvesvidal reacted to a post in a topic: St. Roch by David Lester - FINISHED - Billing Boats - 1:72
-
yvesvidal reacted to a post in a topic: St. Roch by David Lester - FINISHED - Billing Boats - 1:72
-
yvesvidal reacted to a post in a topic: St. Roch by David Lester - FINISHED - Billing Boats - 1:72
-
Thank you Harvey! Really appreciate it. I would like to visit it myself, but we never get to Vancouver anymore. Our son used to live there, so we were there quite often, but not so much these days. (We're over 2,000 miles away.) Thanks again, David
- 61 replies
-
- St. Roch
- Billing Boats
-
(and 1 more)
Tagged with:
-
David Lester changed their profile photo
-
Hello All, I believe I have finished! One of the attractions for me with this model was the limited amount of rigging, but it still caught me by surprise how quickly it wrapped up. There isn't too much to discuss about it either. It's very straightforward. From the 360 tour on the website, I was able to sort out a couple of details that aren't evident in the plans. So that's it for my St. Roch. This was quite a fun small build, not too challenging. The most fun was sourcing and making improvements on some of the poor quality fittings included in the kit. Thanks again for checking in. Much appreciated. David
- 61 replies
-
- St. Roch
- Billing Boats
-
(and 1 more)
Tagged with:
-
David Lester reacted to a post in a topic: The Mayflower by Knocklouder - Amati - 1:60
-
David Lester reacted to a post in a topic: The Mayflower by Knocklouder - Amati - 1:60
-
David Lester reacted to a post in a topic: 1921 Bluenose by John Ruy - Model Shipways Kit No. MS2130 - 1/64 scale - Canadian Fishing Schooner
-
David Lester reacted to a post in a topic: HMS Pegasus 1776 by Moonbug - Amati/Victory Models - 1:64
-
Good Morning, Well, I think it's about time to quite adding things to this boat - those decks and roofs are pretty much full! I've added many details that are not included in the kit, and I need to stop because I'm just about out of room. It's been fun improving what is really a very basic kit. While the kit omits many of the details, at least it was reasonably accurate so far as it went and I couldn't detect any really glaring errors in what was included. I did have a bit of trouble fitting some things in, due to scale, but I think it's ok overall. Here's how I made the fire hose. I started with a piece of sail fabric from another kit and painted it with watered down white glue to prevent fraying. I cut a strip 3/16" wide and then folded it in half lengthwise and glued it. This resulted in a 3/32" wide strip with one rounded over edge. I simply rolled it up and secured it with some glue. That was the easy part. I had a bit of trouble with the wooden frame that holds the hose. I tried to make the frame separately and then just slip the coiled hose into place. This wouldn't work for me as I couldn't get the tiny pieces of wood to stay together, especially with the odd angles at which they meet. Then I had another one of my 3 am epiphanies and realized I was going about it the wrong way. The answer was to glue the individual pieces of the frame directly to the coil, one by one. This was very easy to do and the result is much better than my failed earlier attempts. So that's the hull and all of its details done. Now it's on to the masts and rigging. With many models this is often only about the half way point, but this one has so little rigging, that it won't be long before I'm looking for a new project. I've started the shrouds. The shrouds on the real boat have serving in a contrasting colour, so that was a fun detail to add. That's all for now. Many thanks for checking in. David
- 61 replies
-
- St. Roch
- Billing Boats
-
(and 1 more)
Tagged with:
-
David Lester reacted to a post in a topic: The Mayflower by Knocklouder - Amati - 1:60
-
David Lester reacted to a post in a topic: 1921 Bluenose by John Ruy - Model Shipways Kit No. MS2130 - 1/64 scale - Canadian Fishing Schooner
-
David Lester reacted to a post in a topic: Mayflower by LCdr Dave - Billing Boats - 1:60
-
Good Morning, A short update, but what appears to be a lot of progress. Really just a few minutes of gluing the components on the decks and it almost looks like the model is done. What I found the most challenging so far has been the railings. The ones running along the rail are easy, but the ones on the roofs of the deck house and wheel house were much more difficult. In my naivete I thought I could use one piece of brass rod for each run of the railing, bending it in the appropriate places and feeding it through the stanchions. After about an hour I was about as bent out of shape as the brass rod! In the end, and after restraining myself from throwing the whole thing across the room, I used individual pieces, gluing them between the stanchions. There's a small platform on the starboard side of the hull. On the real boat, the stanchions are very thin and end in an "eye" through which the chain passes. I experimented with a small piece of dowel, drilling a small hole in the end for an eyebolt. This worked ok, but looked far too heavy. The stanchions need to be no bigger than the 1/32" brass rod to look right and there was no way I could drill into the end of that, so I flattened a small bit of the rod at the end with a hammer and drilled through that. Not 100% accurate, but I think it works ok. Just a couple more small details to attend to -the axe and fire hose and some paint touch-up, and then it's time to start working on the shrouds. Many thanks for checking in. David
- 61 replies
-
- St. Roch
- Billing Boats
-
(and 1 more)
Tagged with:
-
David Lester reacted to a post in a topic: Charles W Morgan 1841 by toms10 - FINISHED - 1:96 - POB
-
I see your problem. I believe that the bulkhead extensions needed to either be pared down to the same size as the false stanchions or else removed completely and a false stanchion put in its place. It's still not too late to do that, but, of course, the issue is this would leave gaps in your deck planking. I guess you could add a new plank on top of the existing planking and it would be like a waterway; slightly elevated from the rest of the decking, but that would entail cutting it around the false stanchions which would be very onerous. Another idea is to replace all of the railing with wider material and another would be to taper the bulkhead extensions so that they are full width where they meet the deck and narrower where they meet the railing. If it were me, at this point in the process, I think I would opt for this last approach. I think it would give the best overall result and shouldn't be too noticeable to the casual observer. Your workmanship is really great and the model is looking really nice. David
-
Good Morning, I have most of the bits and pieces ready to be added to the deck. Getting the size correct on these has been a bit of a challenge. The plans cannot be trusted. The drawings differ between the plan view and elevation view by as much as 10mm on some things! There is a measuring tool on the 360 tour on-line that works very well, but it's difficult to get every measurement needed and not always easy to get the same measurement twice. So it's been a matter of trial and error and discovering what fits and looks about right to the eye. I enhanced the kit provided windlass a little bit, relying on the on-line pictures and working only with the limited supplies and tools that I have. I'm not sure that it's completely correct, but it looks complicated enough to be believable 😁 Thanks for looking it and I hope everyone has a great Easter weekend. David
- 61 replies
-
- St. Roch
- Billing Boats
-
(and 1 more)
Tagged with:
-
This solves a mystery for me. A few years ago I bought some "boxwood" strips from Model Expo and received this same rough yellow stuff. I was at a loss to understand why everyone raved about boxwood so much. I could see no improvement over the basswood strips I was intending to replace. Now that I understand I want to try some of the real thing. David
-
Brief update for this morning - Bill, if you use the 360 tour and go to the extreme forward starboard side of the roof of the deck house, you can just get a glimpse of the rod arrangement running along the roof. It appears to be a complicated set-up and pretty hard, if not impossible to model accurately at this scale, at least without a better reference. So I'm just representing it with a simple single rod. I'm not going to add sails. I tend to prefer my models without them, but this model would be an ideal one to show furled ones on. Have you seen Tom Lauria's youtube video on making furled sails from silkspan? It's quite good. I've been working on the lifeboats. I don't like the fact that they're plastic, yet at the same time, I don't really like the idea of building new ones either and I can't seem to locate cast ones that are quite right. So my solution is to use the plastic ones and show them with their canvas covers. I use some sail material from another kit. I was hoping to leave them unpainted, but did paint them in the end, because they looks just a bit too dirty by the time I finished. I first thought I could make each one from one piece of cloth, but soon realized that wouldn't work. The real ones, of course, are constructed out of several pieces, taking the shape into consideration. So, my solution was to use three pieces for each boat like this: I simple glued the side pieces on first. I used white glue which holds quite well. I didn't want to use CA in case I had to remove the piece and start over. I don't think the plastic boat would stand up to the acetone. (It may not have stood up to alcohol any better, had I needed to start over, but I thought the odds were better.) As it turned out, I didn't need to start over. This seems to work fairly well and with so little of the boat showing, it's hard to tell what it's made of. Next, I'm going to attack the windlass. Thanks for checking in. David
- 61 replies
-
- St. Roch
- Billing Boats
-
(and 1 more)
Tagged with:
-
I've been trying to figure out the complicated steering arrangements on this boat. The kit provides some, but not all of the parts that are required and absolutely no mention of any of it in the plans or instructions. However, I've managed to decipher enough of it from the on-line 360 tour to make an acceptable representation of it. It seems really odd to me that considering that this boat spent most of its life in the Arctic, exposed to snow and ice that so much of this gear would be external, rather than internal. It appears to me that either cable or chain (which is encased and not visible) connects the wheel to rods that in turn connect to chain that runs down the aft side of the deck house, then runs aft along the deck to the rudder which is located beneath a deck fitting; a table or bench (not sure what it should be called.) Now I'm mulling over how to handle the two winches and windlass. The ones provided in the kit are over-simplified and mostly plastic. The winches shouldn't be too hard to re-imagine, but the windlass is a complex piece and will be more difficult. At least, too difficult for my evening brain; more suited to my morning brain. All I'm good for by this time of night is a detective series on BritBox! (my favourite is Vera) David
- 61 replies
-
- St. Roch
- Billing Boats
-
(and 1 more)
Tagged with:
-
Good Morning, Bill, those models look great. Just saw your post now; we've been away for a couple of days. A Saturday morning update - Lately I seem to have the attention span of a gerbil and have been working on all kinds of different things. First, the four vent pipes: They're made out of 1.5mm brass rod, bent into shape. I wanted to indicate the joints. First I tried some Evergreen styrene strips, .01" x .02" but it was much too large to be in scale. Then I tried some rigging thread. By trial and error I discovered that both .5 mm and .25 mm lines were too heavy. I settled on ordinary sewing thread and it seems about right. Next, I was concerned that the supplied piece of dowel was not going to be quite right for the funnel. Taking measurements from the on-line 360 tour, I discovered that at 16mm diameter it was spot one. It was just a matter of flattening the sides to about 12mm. Finishing the funnel is probably next in my peripatetic approach to the details. The biggest challenge for me has been the four metal ladders. The ones provided are brass and are not bad quality, but don't look anything like the actual ones on the boat. It took me several attempts, but I have come up with something that I think is acceptable and are a pretty close approximation of the real ones. The three that mount on the deck house have curved tops, flat sides and round rungs. So I used some 1/64" x 1/16" brass strips for the sides. I made a small saw kerf at about the place where I wanted it to bend, and then just bent it using two pairs of pliers. It buckled a little, so using my best blacksmithing skills, I just hammered it flat. It's not very elegant, but once painted gray, it's going to work just fine. The rungs are .5mm wire. I'm really bad at soldering, but I discovered that one of the secrets is to hold the parts very firmly. I made two parallel grooves in a piece of wood. Once I had the holes drilled and the wire rungs inserted, I just placed the sides in the two grooves and gave the whole thing a tap with a hammer to seat it. This worked really well, and it wasn't too difficult to solder each rung in place. The ends of the rungs are snipped off and they've had some cleanup ready for paint. I think these will work, and besides, it's the best I can do, and once I know I've reached that point, I can live with it. The fourth ladder that mounts to the wheelhouse doesn't have a curved top and I'll cut it to length when I get to that point. The final item for today is the railing that extends out from the wheelhouse on both sides. These pieces were easy to make and I added the detail to the back side to match that of the real boat. So that's it for now. Again, many thanks for checking in, likes etc. David
- 61 replies
-
- St. Roch
- Billing Boats
-
(and 1 more)
Tagged with:
-
Hi Dave, I hope you don't mind my chiming in. I honestly just don't get including plastic parts in a wooden kit. It they're going to do that, then why not just make the whole thing out of plastic and be done with it. My build log probably won't be of too much help, because I built the Model Shipways version, not the Billing version and they seem to differ a fair bit. There seems to be a problem with the way your grating is sitting on the stem piece. The grating appears to be sitting up against the hull quite well, but by the time you get to the end of the stem piece, the grating is sitting well to the port side. I'm not sure what needs to be adjusted to get the grating centred on top of the stem piece for its entire length, but if you can do that then that should go a long way to getting the side pieces to fit. If you don't like the plastic side pieces, I don't think it's too big a job to make new ones out of wood. Is there some billet material of the same thickness that's big enough? If so, I would use that; if not, I would just glue up some strip material of the right thickness. Sometimes glued up stripwood will tend to split or come apart, especially if you have to cut close to a seam or against the grain. I sometimes glue the strips to a piece of paper which gives the whole thing a surprising amount of strength. If the piece is to be used in such a way that the paper side won't show, I leave it on. If it's going to show, (as it would in this case) I just sand the paper off after the piece is cut out.You can use the plastic pieces as templates, trace them and cut the new pieces out. Another big advantage to replacing the parts, besides appearance, is that there is always a lot of flexibility with wood to make minor adjustments to make them fit. (I don't believe I have ever been able to build a truly symmetrical model; fortunately you can only ever see one side at a time, so I don't worry about it.) Plastic doesn't give this kind of flexibility. Not sure if that's of any help or not, but hopefully it is. David
-
Bill - I didn't use the plastic for the windows. I have never used it on any of my models. I always just leave the opening. For some reason, I find it distracting to look at and difficult to install without getting glue all over it (at least in my case) so I always just opt to leave it off. I did paint the interior of the wheel house. I used a dark brown. I haven't had a good look at the stack yet, but I do know that the supplied piece is pretty far off from being the right shape. I'm not sure how I'll approach it just yet. The small vents on the bottom of the stack will be pretty hard to do as the scale makes them only about 4mm long. I don't think I would try building them, I think I would be inclined to used a small piece of wood, the correct size, and suggest the vent slots by scoring the wood horizontally. These type of things I tend to experiment with and if the result looks ok, I use it and if not, then I omit it. The box on the back of the wheel house is an easy detail to replicate, so I will probably add it. The ladders! I have spent the better part of the afternoon trying to make ladders that look better than the provided ones, but I'm having a lot of trouble. I've tried some small brass strip for the sides. I drilled a series of holes and then soldered in brass wire representing the steps. Unfortunately I am the world's worst solderer and the result was quite a mess. I then tried using brass wire for the sides, soldering smaller brass wire across for the steps. Again, quite a mess. There are always two possible outcomes for me - a joint that fails or a glob of solder the size of a golf ball. So, I am still contemplating my options and waiting for another one of my 3 am revelations. 😄 David
- 61 replies
-
- St. Roch
- Billing Boats
-
(and 1 more)
Tagged with:
About us
Modelshipworld - Advancing Ship Modeling through Research
SSL Secured
Your security is important for us so this Website is SSL-Secured
NRG Mailing Address
Nautical Research Guild
237 South Lincoln Street
Westmont IL, 60559-1917
Model Ship World ® and the MSW logo are Registered Trademarks, and belong to the Nautical Research Guild (United States Patent and Trademark Office: No. 6,929,264 & No. 6,929,274, registered Dec. 20, 2022)
Helpful Links
About the NRG
If you enjoy building ship models that are historically accurate as well as beautiful, then The Nautical Research Guild (NRG) is just right for you.
The Guild is a non-profit educational organization whose mission is to “Advance Ship Modeling Through Research”. We provide support to our members in their efforts to raise the quality of their model ships.
The Nautical Research Guild has published our world-renowned quarterly magazine, The Nautical Research Journal, since 1955. The pages of the Journal are full of articles by accomplished ship modelers who show you how they create those exquisite details on their models, and by maritime historians who show you the correct details to build. The Journal is available in both print and digital editions. Go to the NRG web site (www.thenrg.org) to download a complimentary digital copy of the Journal. The NRG also publishes plan sets, books and compilations of back issues of the Journal and the former Ships in Scale and Model Ship Builder magazines.