-
Posts
45 -
Joined
-
Last visited
About baribeaujm
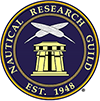
Recent Profile Visitors
-
baribeaujm reacted to a post in a topic: Speedwell Battle Station Kit 1752 by CiscoH - Syren Ship Model Company - 3/8" or 1:32
-
baribeaujm started following Martindale blades for Byrnes saw... , Beavers Prize 1777 by Mike Y - 1:48 - POF - Hahn style , HMS Winchelsea by scrubbyj427 - 1:48 and 1 other
-
baribeaujm reacted to a post in a topic: Le Chebec by Yvesvidal - CAF Model - 1/48
-
baribeaujm reacted to a post in a topic: Sloop Speedwell 1752 by Chuck - Ketch Rigged Sloop - POF - prototype build
-
baribeaujm reacted to a post in a topic: Chris Watton and Vanguard Models news and updates Volume 2
-
baribeaujm reacted to a post in a topic: L'Amarante by marsalv - 1:36 - POF
-
baribeaujm reacted to a post in a topic: Sloop Speedwell 1752 by Chuck - Ketch Rigged Sloop - POF - prototype build
-
baribeaujm reacted to a post in a topic: Sloop Speedwell 1752 by Chuck - Ketch Rigged Sloop - POF - prototype build
-
CaptMorgan reacted to a post in a topic: Sloop Speedwell 1752 by baribeaujm (Jean-Marc) - Syren Ship Model Company - 1:32 Scale - POF Sloop
-
davyboy reacted to a post in a topic: Sloop Speedwell 1752 by baribeaujm (Jean-Marc) - Syren Ship Model Company - 1:32 Scale - POF Sloop
-
JpR62 reacted to a post in a topic: Sloop Speedwell 1752 by baribeaujm (Jean-Marc) - Syren Ship Model Company - 1:32 Scale - POF Sloop
-
yvesvidal reacted to a post in a topic: Sloop Speedwell 1752 by baribeaujm (Jean-Marc) - Syren Ship Model Company - 1:32 Scale - POF Sloop
-
rcweir reacted to a post in a topic: Sloop Speedwell 1752 by baribeaujm (Jean-Marc) - Syren Ship Model Company - 1:32 Scale - POF Sloop
-
Chuck reacted to a post in a topic: Sloop Speedwell 1752 by baribeaujm (Jean-Marc) - Syren Ship Model Company - 1:32 Scale - POF Sloop
-
Freebird reacted to a post in a topic: Sloop Speedwell 1752 by baribeaujm (Jean-Marc) - Syren Ship Model Company - 1:32 Scale - POF Sloop
-
baribeaujm reacted to a post in a topic: Sloop Speedwell 1752 by Chuck - Ketch Rigged Sloop - POF - prototype build
-
Ryland Craze reacted to a post in a topic: Sloop Speedwell 1752 by baribeaujm (Jean-Marc) - Syren Ship Model Company - 1:32 Scale - POF Sloop
-
Ronald-V reacted to a post in a topic: Sloop Speedwell 1752 by baribeaujm (Jean-Marc) - Syren Ship Model Company - 1:32 Scale - POF Sloop
-
westwood reacted to a post in a topic: Sloop Speedwell 1752 by baribeaujm (Jean-Marc) - Syren Ship Model Company - 1:32 Scale - POF Sloop
-
Fire Heart Here I fellow the instruction steps with no major issue. I opted for the beaten up option. I used a Touch red geranium marker to color the bricks and soot and dark rust powders to season the bricks. I used the flour trick to enhance the mortar joints. I painted the hood with my go to Admirality's metal black and finished with soot and rust powder. A couple of vies below: Next is the aft platform beams and forthcoming Chapter 5.
-
Fore Platforms I first prepared paper templates of the lower and upper fore platforms and tried to position them on the model. It revealed the I needed to do a bit more fairing at the bow for the platforms to sit at the proper height. Once the firing was completed, I started the beam construction. I tried to use Chuck's height gauge, but found it tricky to position. Instead, I use cardboard height guides for each beam as shown below. This approach worked well for me. Next photo shows the completed beam structure. The platforms were assembled on a flat surface and their contour adjusted to fit my model. Their shape is virtually identical to the plan. Proceeding this way makes it easier to sand the planking and to cut the scuttle lids accurately. The platforms were then glued on the beam structure. A light coat of WOP was applied to enhance the planking joints. I then completed the breast hooks and riding bitts. The next photo shows the completed fore platforms (riding bitts not glued). Hopefully every thing is sitting at the right height and positioned correctly. Next is the fire heart and then Chapter 5!
-
baribeaujm reacted to a post in a topic: Sloop Speedwell 1752 by Chuck - Ketch Rigged Sloop - POF - prototype build
-
baribeaujm reacted to a post in a topic: Le Chebec by Yvesvidal - CAF Model - 1/48
-
Stern Details It has been a while since I reported on my progress. For the stern details I followed the instructions. For the bottom molding, I used a fairly similar pattern as the one starboard and port. The frieze was then glued with little tweaking to adjust the width and size. The upper molding in two layers was scraped and glued on. Here is a general view: The columns and carved transom were done next. The laser parts fit quite nicely and only little tweaking is needed here. Here is another view: I painted the top of the transom with a mix of black, burnt sienna and blue, trying to match the frieze's background. Once everything was glued in place, I noted the some of the background black was showing between the carved transom and the windows. I may have to scrape that paint or move the carving down slightly. I will address that later. I then proceeded to complete the molding to wrap around the stern and provide a base for the two standing figures. This is a rather tricky operation and there are a lot of angles to adjust. The next photo shows details of this construction: The last step is to carve the figure bases and glue the standing figures. I dry fitted these and realized that there is very little area available to glue the figures on. Therefore, I decided to postpone this step for now. I doubt that I could complete the project without knocking those off a few times... Limber Strakes As chapter 4 was not out yet, when I reached this point, I decided to make the limber strakes from scratch. I created the rabbet by gluing two 3/64" planks shaped according to the plan. A bit time consuming, but no char to deal with! I received Chapter 4 just in time to carry on with the project. The mast steps were added next. Next I will report on the platform construction.
-
Fancy Molding and the Frieze - Starboard Side Work on the starboard side is completed. I tried to keep a good symmetry between port and starboard. Here are some pictures: Anchor Lining I found that using individual planks worked better for me. It allows more accurate positioning with respect to the hull planking and it is easier to conform with the hull curvature. Here use of CA glue helped a lot to maintain individual planks in position while being slightly bent to follow the hull curvature. This completes chapter 3. While waiting for future chapters, I plan to do a bit more work that requires no laser cut parts (transom and some framing) to keep the project going.
-
The Stern Lights The build continues. There was no particular issues with the stern lights. The fit is very tight and it cannot be emphasized enough how important it is to use the blanks provided when building the transom. The image below shows the result. (A good dusting of the windows will be needed). Inboard Sheer Planking and Final Cap Inboard planking is straightforward using the pre-cut planks provided. Before gluing them on I had to do a light inboard sanding to insure a final width of 1/4" of the hull at the sheer. With the inboard planking in place, a light sanding of the sheer line using the long sanding stick described in the instructions was done to insure that the final cap was horizontal. Once in place, I sanded the final cap to get nice joints and no irregularities. I found important to reduce the width of the cap in the waist section as much as possible so that the last 1/8" fancy molding is flush to the cap. Fancy moldings and the frieze The fancy moldings were scraped using a razor blade. For the lower molding I chose a very simple profile that mimics that of the quarter badge as shown here. For the upper molding I used a slightly more detailed profile. As discussed above and in the instructions , it is important that this upper molding meets the final cap at the waist. This requires making slight adjustments to the frieze width to account for the cap thickness and width of your final strakes. In my case I printed the frieze at a 110% magnification to get a nice fit. The above photos also show the fancy moldings at the drifts. I found the char marks on those can be lightened slightly by soaking in water and brushing. The anchor lining was then added. I found I got a nicer fit using individual strakes rather than the one laser piece provided. Need to complete the starboard side now in anticipation of chapter 4.
-
Treenailing This step was faster than anticipated. I used a no. 78 bit and 10 lb. monofilament. The fishing line used is burnt orange, which softens the contrast with the yellow cedar planking. I found that for this repetitive task it is better to work in short sessions. After a half hour of marking, drilling, etc. it easy to loose concentration and make mistakes. Better to stop and return to it later...I inserted the fishing line directly into the drilled hole. It was a tight fit and no glue needed. Completing the Planking The final two strakes and drifts were added next. This is again fairly straightforward. The only tricky step here is to cut holes in the planks where the sheaves are positioned. Shaping and gluing the drift at the bow is also a bit tricky since it is above the rabbet. Here are a couple of views. in these shots you can see that WOP was applied up to the 1/8" stakes and that the second layer of the wales was completed. I decided to paint the wales before gluing them on. I used Admiralty Matt (Metal) Black, which I always use for wales, spars, etc. Applied in several dilute coats it produces a superb finish. Finally, I dare to show a front view of the bow. The overall result is not too bad. The strakes are slightly pointing upwards at the bow, which suggests insufficient fairing close to the stem. There are small strake height variations from starboard to port. Fortunately, a lot of this will be hidden when additional elements are added at later stage of the build. Preparing the qbadges and fancy moldings For these, I used the fruitwood gel stain method. I am more or less happy with the result. The staining is not uniform and a showing too much orange shades and build up in some areas (stain too old?). I will experiment with IPA to see if the coloring and uniformity can be improved before I glue those on the model. I welcome suggestions here.
-
Removing the JIGS Before removing the jig, I decided like others to reinforce the frames by inserting fillers at the sheer. This is probably not needed, but should add some rigidity when fairing inside the hull. Removing the jigs was straightforward. No issues here. As instructed, I used a long sanding sticks to create a smooth even sheer line. The hull template is useful here to tweak the sheer. The fairing Cap and Inboard Fairing I added the fairing cap making sure I do not mix the two middle sections. Then came fairing inboard... This is a long process. It took me several tens of hours to complete this. I used only sandpapers and sanding bars of various grits. Fairing at the bow is especially tedious because that section is quite concave and hard to reach. I also added the keelson as you can see. Planking Above the Wales I completed the planking up to the 1/4" strake. Here the planking template is very useful to shape the planks at the bow. I tried to follow the plan as much as possible trying to match the strake height with respect to the gun/seep ports. I found it important to check the exact width of my 7/32 planks and make adjustments where necessary. Errors are cumulative and it does not take much to deviate from the plan. A few photos follow: The next step is treenailing. I will report on this in hopefully a not too distant future...
-
Hull Planking I proceeded with the hull planking as per the instructions. The paper template is crucial for adjusting the position of the sweep ports and gun ports. The height of a few gun ports sills had to be corrected (never more than 1/32") to conform to the template. Some sweep ports were a bit off and this could be taken care of by tracing their exact position using the template. I guess these slight adjustments are unavoidable given all the possible variations in frame construction and positioning. Adjusting the upper wale height at the bow is a bit tricky. For this I positioned a 1/8" guide as shown here. With the upper wale position established, I proceeded with the planking. For shaping the planks I used the travel iron and air dryer technique. I used a combination of CA and PVA for gluing. I typically would apply CA to 10 consecutive frames and ten PVA on the following 2-3 frames. The CA glued section is position carefully and once the glue is cured, the PVA glued buffer gives me easy access and time to apply CA glue to the next 10 frames. I found this approach insured that all frames were glued to the plank, avoided CA messes, and minimized the risk of opening gaps at the joints when CA is used at once over the whole length of the plank. Before planking above the wales, I checked the width of my 7/32" planks. My planks were a hair too thick (0.225" instead of 0.219"). I used my Varitas mini plane to narrow the planks down to the correct width. Slightly thicker planks would have led to complications when planking around the ports and shifted the position of the fancy molding. I completed the first three rows plus part of the fourth. A milestone has been reached. It is now time to remove the jig!
-
CHAPTER THREE The Square Tuck And Counter Planking Because of a Canada Post strike, delivery of Chapter Three parts was delayed. I wanted to carry on with the project by scratching these parts. For the square tuck I used 1/8" thick AYC billet for the planking. The border was shaped with files and sanding sticks from a 1/8" AYC sheet. It is tricky to get good symmetry between the two sides and reproduce the run from the plan. If you want to make your own square tuck, the width of the planks needs to be very accurate. The planks should be 0.248-0.250" wide, except for one plank (second from the top) that is 0.225". It really does not take much to offset the planking pattern. For tree nailing I used 15 pound fishing line and the taper was adjusted to fit my framing. Overall, I am quite please with the result. For the counter planking, I cut planks from a 3/64" AYC sheet. These planks were shaped according to the drawings with very little tweaking needed.
-
Stern Framing Merry Christmas to all! For the stern framing I followed the instruction. The notches on the jig really help to position the stern frame accurately. This is something I struggled with in previous builds. Here everything went smoothly. The fillers were useful to position the light sills. The angles of the provided parts fit closely to the model with only minor tweaks required. Note that an additional slight taper is needed to fit the outer edges of the sills where they meet the quarter pieces. For gluing the transom, I proceeded with caution as recommended. Not much issues here. The final step was to glue the triangular pieces on top of the quarter pieces. I left enough room for later adding the fairing cap and final cap. The last item not discussed here is the adding of the upper port sills. When doing those I realized that some of my lower sills were slightly off (angle and height). The variations are small (typically 1/64"), but it is bugging me. I will do minor adjustments before planking. More about this in Chapter 3.
-
Aft Cant Frames More progress to report. The aft cants are assembled and mounted the same way as the fore cants. No major issues here. On some frames I had to do some adjustments to get a good fit on the apron. This is probably because some of my apron wedges were not perfectly centered or slightly off vertical. The shorter half cant frame at the last gun port is a bit tricky to adjust, but the templates greatly helps for proper alignment. The above photos show the aft cant frames before fairing. Fairing requires s lot of sanding, specially at the apron. The main challenge here is to obtain a clean profile where the cant frames meet the lower apron. As you can see, more sanding will be required when I do the final fairing. The Wing Transom I proceeded as described in the instructions. Here the main difficulty is to glue the wing transom so that it is perfectly horizontal, perpendicular and centered on the keel. I found that dry mounting the quarter pieces helped in that regard. I also used a combination of squares aligned to the build board plan as instructed. Once the transom wing is well positioned, it is easy to permanently glue the quarter pieces to aft cant frame 24. As mentioned by others the cant frames need to be faired to do a proper alignment of the quarter pieces. The Fashion Pieces and Last Aft Frames Here I followed the instructions and had no major issues. Thee was a lot of adjustments needed to get all the angles right before gluing the fashion pieces. The last aft cant frames also required some angle adjustments. I noted that my frames were an hair thicker than the 0.25 inch prescribed. A bit of sanding was required to get them to nicely fill the gap between the fashion piece and frame 24. I struggled a lot to get a good fit with frame 29. The bevel markings on the pieces is a good start for shaping those pieces, but a lot of adjustments were required. After several hours of testing, I was able to get a decent fit. The photos below show the results before and after fairing. I was able to improve the joint at the apron, but more sanding may be required to get a perfectly smooth transition. I believe the small inaccuracies in the positioning of the apron wedges is making fairing difficult here. It should look better once WOP is applied. The last photo shows a view of the stern after fairing. A bit more fairing may be required.
-
The Fore Cant Frames Work continues on the Speedwell. Preparing the cant frame is a long process. Lots of char to remove, joints to adjust, tree nailing to do, etc. I found the cant frame jig work very well. Once the jig is positioned properly, adding frames one after the other is relatively straightforward. As suggested in the instructions, I first installed the first three fore cant frames and then switched to frame 11 and worked my way towards the bow. Some tweaking was needed at the lower joint between the frames and the lower apron, suggesting my apron wedges were not perfectly vertical. The above photo shows the starboard cant frames after some preliminary fairing. I tried to keep the bottom joint as clean as possible with minimum gaps. The Bow Timbers I shaped the bow timbers as instructed. I found that my bevel lines were systematically lower than the edge of the forward cant frame. This was probably because I had some initial fairing done on the frame. Anyhow the assembling went smoothly. No particular issues here. The above images show views of the bow timbers after assembly and fairing. There is a bit more fairing required near the keel and at the sheer. It is quite tricky to get the hull profile right where the frames have an inward curve (concave). I will address this later.
-
Mounting the Frames and Fairing I finally completed the square frame installation. Once you got the hang of it, I progressed fairly quickly. Here is one side view: I found it important to check verticality whenever a frame was added. Some frames were slightly off, possibly because of minor misalignments when frame parts were assembled. The seven-piece frames on each side of the gun ports are the most susceptible to this. A few remarks: I opted to sand the frame sides and apply WoP. This represents a lot of work and it is arguable that this is needed at all. The gun port template is very useful to position the sweep ports and sills. However, it works best if the upper section of the hull is faired. As indicated in the instructions it is important to shape the sweep ports so they nicely follow the fairing. I also partially faired the inside as I progressed. I decided to treenail the frames prior to installation. It is easier to get the distances and angles uniform. The following images show starboard and port views after fairing. For the most part I used Vallejo flexi sanders of various grits (see photo below). I found these work very well. Contrary to emery sticks those flexi sanders do not gum up and last forever. There is some residual fairing to do, but only after the cant frames are installed. It this time to start Chapter 2!
About us
Modelshipworld - Advancing Ship Modeling through Research
SSL Secured
Your security is important for us so this Website is SSL-Secured
NRG Mailing Address
Nautical Research Guild
237 South Lincoln Street
Westmont IL, 60559-1917
Model Ship World ® and the MSW logo are Registered Trademarks, and belong to the Nautical Research Guild (United States Patent and Trademark Office: No. 6,929,264 & No. 6,929,274, registered Dec. 20, 2022)
Helpful Links
About the NRG
If you enjoy building ship models that are historically accurate as well as beautiful, then The Nautical Research Guild (NRG) is just right for you.
The Guild is a non-profit educational organization whose mission is to “Advance Ship Modeling Through Research”. We provide support to our members in their efforts to raise the quality of their model ships.
The Nautical Research Guild has published our world-renowned quarterly magazine, The Nautical Research Journal, since 1955. The pages of the Journal are full of articles by accomplished ship modelers who show you how they create those exquisite details on their models, and by maritime historians who show you the correct details to build. The Journal is available in both print and digital editions. Go to the NRG web site (www.thenrg.org) to download a complimentary digital copy of the Journal. The NRG also publishes plan sets, books and compilations of back issues of the Journal and the former Ships in Scale and Model Ship Builder magazines.