-
Posts
989 -
Joined
-
Last visited
About mbp521
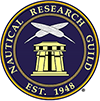
- Birthday 06/16/1968
Profile Information
-
Location
Far North Texas
Recent Profile Visitors
-
mbp521 reacted to a post in a topic: Lula by Keith Black - FINISHED - 1:120 Scale - 1870s Sternwheeler Supply Boat for Floating Pile Driver
-
mbp521 reacted to a post in a topic: Lula by Keith Black - FINISHED - 1:120 Scale - 1870s Sternwheeler Supply Boat for Floating Pile Driver
-
FriedClams reacted to a post in a topic: Lula by Keith Black - FINISHED - 1:120 Scale - 1870s Sternwheeler Supply Boat for Floating Pile Driver
-
Canute reacted to a post in a topic: Lula by Keith Black - FINISHED - 1:120 Scale - 1870s Sternwheeler Supply Boat for Floating Pile Driver
-
Keith Black reacted to a post in a topic: Lula by Keith Black - FINISHED - 1:120 Scale - 1870s Sternwheeler Supply Boat for Floating Pile Driver
-
Cathead reacted to a post in a topic: Lula by Keith Black - FINISHED - 1:120 Scale - 1870s Sternwheeler Supply Boat for Floating Pile Driver
-
Keith, My MSW time has been almost nonexistent over the past few months or so, but I finally found some time to catch up. I must say, Lula is looking magnificent! I am truly sorry to hear of your health issues, and wish the best for you on the 30th, and a speedy recovery. -Brian
- 732 replies
-
- Lula
- sternwheeler
-
(and 1 more)
Tagged with:
-
mbp521 reacted to a post in a topic: Lula by Keith Black - FINISHED - 1:120 Scale - 1870s Sternwheeler Supply Boat for Floating Pile Driver
-
Canute reacted to a post in a topic: Caroline N by mbp521 - Scale 1:64 - Mississippi River Towboat
-
Canute reacted to a post in a topic: Caroline N by mbp521 - Scale 1:64 - Mississippi River Towboat
-
FriedClams reacted to a post in a topic: Caroline N by mbp521 - Scale 1:64 - Mississippi River Towboat
-
FriedClams reacted to a post in a topic: Caroline N by mbp521 - Scale 1:64 - Mississippi River Towboat
-
yvesvidal reacted to a post in a topic: Caroline N by mbp521 - Scale 1:64 - Mississippi River Towboat
-
mtaylor reacted to a post in a topic: Caroline N by mbp521 - Scale 1:64 - Mississippi River Towboat
-
mbp521 reacted to a post in a topic: Caroline N by mbp521 - Scale 1:64 - Mississippi River Towboat
-
Thank you Kieth. I’m trying to make it look like some work has been done. Gotta keep things interesting. 😁 Good question Eberhard. Most of the time that is the case. If you closely at the second live photo I posted you can see the multiple lines tied to the tow. I’m no expert on these, but they use several tow lines secured to several bollards to distribute the tow. some are also tied to the cleats as well. I’ve watched several videos on tow operations and the crew is constantly going in and checking and resecuring the line tension every few hours to make sure nothing breaks loose. Dang, you caught me! I usually try to keep my mess out of the pictures, I just wasn’t as careful this time. 🤪 Most of the time it’s total chaos and needs a good cleaning every now and then. I’m just glad I didn’t get the whole bench in the photo. -Brian
-
mbp521 reacted to a post in a topic: Caroline N by mbp521 - Scale 1:64 - Mississippi River Towboat
-
mbp521 reacted to a post in a topic: Caroline N by mbp521 - Scale 1:64 - Mississippi River Towboat
-
Hello again everyone, the journey continues. Slowly making more progress as I find the time to work on the Caroline. I managed to get the cleats all painted up and installed. As I post the photos I can clearly see some of the imperfections in them, I'll need to go back and clean some of them up. The resolution on today's phone cameras is almost too good. Next was getting the motor painted up for the work/life boat. Still need to build the propeller, but I'll get there. I'm also going to put some decking in the floor to clean up the printer lines and add a few other details such as a fuel tanks and fuel lines and whatever else I can think of to throw in there. Moving on to some of the main deck details, I built the exhaust fan vents that flank each side of the engine room. These I made from thick card stock and ABS plastic. The ABS provided the black background for the vents then the frames and louvers were cut from the card stock. The louvers are hinged so that when the fans are off they swing closed and lay flat, I didn't like the way they looked closed so I decided to have the fans on and the lovers open. Adds a little more life to them. Once the vents were completed they were installed in their locations on each side of the main deck. The work continued on the main deck with the bollards. I used the laser cutter to design and build up a jig that would help me line the pieces of the bollards up while I built them. This was a simple tool made up of three layers of scrap wood glued together. The first layer had a hole cut in the center with room enough to fit a small dowel that will be used to push the completed bollard out of the jig. the second layer has a hole in the center for the smaller, center section of the bollard and the third layer has the hole for the top part of the bollard. All three layers had holes cut on the corners for dowel pins to help keep everything in line. All layers and centering dowels were then glued together. The center (smaller) ring of the bollard was place in the jig. A dab of CA. Then the top ring was glued in place. The bollard removal dowel was then used to push the completed bollard out and viola! perfectly centered bollards. 2 down, 23 more to go. All of the bollards have been built and ready for sanding. All sanded up, now to shoot some paint on them. Next was cutting the rings that will form the bottom of the bollards. These I also made from ABS plastic. Here is one of the setups temp installed on the deck to see how they look. Having the ABS rings separate also allowed me to get a clearer measurement for proper placement of the bollards by being able to see the measurement lines through their centers. It was much harder to try and line everything up with the completed assembly. I just glued the rings in place then came back in and placed the bollard tops in the rings. So much easier. More bollards on the tow knees. There are two bollards on each side that are built up or elevated and slightly angled. I think these are setup this way to allow for tows that are either empty or sit higher in the water than the boats deck to keep the tow lines from slipping off. Here are a couple of photos of the bollards on the actual Caroline (aka Titletown USA) The first shows the angle of the bollard, located right in line with the forward part of the main deck structure. The second photo shows the angled tow line secured to the bollard. Here is the completed construction of the angled bollards. Here is an overall view of the bow with all bollards and cleats in place. I also started work on the tow knee railing, but have not entirely figured out how I want to do them (and got a bit frustrated with them, so I moved on to something else). That is the reason you see the vertical railing supports installed. Right now they provide a good place to snag my sleeve or hands when working on other parts of the forward deck. Finally, while I contemplate the tow knee railings I got started on the deck ladders. These were just a standard build, I din't take many pictures of their construction, I just cut them out on my laser cutter, glued the runners together and painted them up. Here are a couple temp installed to make sure the angle is right. Here is another, painted up. The only bad thing about these is that they require more railing. I am really starting to not like railing. That is all for now. I appreciate all of the likes and comments. Thanks to all for stopping by. More to come. -Brian
-
mbp521 reacted to a post in a topic: Lula by Keith Black - FINISHED - 1:120 Scale - 1870s Sternwheeler Supply Boat for Floating Pile Driver
-
mbp521 reacted to a post in a topic: Lula by Keith Black - FINISHED - 1:120 Scale - 1870s Sternwheeler Supply Boat for Floating Pile Driver
-
mbp521 reacted to a post in a topic: Lula by Keith Black - FINISHED - 1:120 Scale - 1870s Sternwheeler Supply Boat for Floating Pile Driver
-
Hello again everyone, I have finally returned to working on the Caroline. It has been a while, but I finally got around to sitting down and getting a few things done over the last couple weeks. First thing, I fired up the 3D printer and made up the lifeboat/work boat. Not really sure of what it would be called in this instance. I tried my hand at designing and printing this time, and I am quite please with the results. I wasn't able to get the runners on the hull to come out right due to the small scale of the boat so I ended up just printing it out with a flat bottom and glued some styrene strips to get the effect. The outboard motor was a little more of a challenge. I managed to find a predesigned version, but couldn't get the prop to print. Again due to the small scale, my printer just wouldn't do it. I'll see if I can make up a small version with some of the materials I have on hand. Here are the results. Still need to paint things up. Next up were the life rings. These were pretty straightforward, just printed them up, gave them a coat of orange paint and finally the white details. And one of them in place. While the 3D printer was warmed up, I went ahead and printed out the cleats as well. A little more clean up to do on these, but they came out nicely. All I need to do now is to get them painted up and glued into place. Lastly, it's about time to start nailing down the main deck so I formed up and installed the vents that run along the walls. I'll get these all painted up and glued into place shortly then work on gluing down the main deck walls. That is all for this update. I realize it is not much, but I'm just getting back into the groove of things and wanted to get something out there. I appreciate everyone sticking with me, and hopefully I can keep a steady rhythm with the progress and updates. Thank you all for stopping by. -Brian
-
Thank you Eric & Keith. I’m hoping the new year will bring new photos of progress on the Caroline. The past few months have been a little rough, the bench has been collecting dust (unfortunately not sawdust) and my MSW time has been neglected. We lost our daughter in law in an automobile accident and a lot of my (our) time has been helping my son and granddaughter get through things. Life is a strange being at times. It can be sublime and it can be cruel, but we do the best we can to deal with what it gives us and move on. I have made myself a promise to get back at it after the holidays, so new material will be headed this way soon. Thank you all for following along and sticking with me. This voyage is far from over and we will reach our destination. -Brian
-
Holy cow Keith! It’s amazing the amount of realism the pastels bring out. You also have me convinced the shaker roof is the right decision. I think it looks great. However, if you are proceeding with the metal roof I will be anxiously awaiting those results as well. This is such a true statement. When I first started painting my Cairo, I chose black for the topside color. I found out real quick that it was not the route to go. After several attempts I found that the dark bluish-gray was perfect. It gave everything the perfect depth and helped highlight certain features. The same holds true with your build. Fantastic work on the weathering! -Brian
-
Thank you Gary! My grandfather always told me, “why pay someone to do something for you when you can do it yourself cheaper”, and I have lived by these words most of my life. I do know my limitations and there have been times where I just have to get someone else to do it. It’s not for lack of trying, but it would be cheaper in the long run for fear of screwing it up and having to redo the project. I took these words into consideration when ordering the printer, now I can build the parts myself and not have to pay someone else for them. I’ve been in the technology field for almost 30 years and have been using CAD software for almost the entire time. Many of the software packages these devices use are based on CAD so the learning curve is fairly easy. Most of them come with a free version that is simplistic and scaled down for the standard user. There are other programs out there that are more robust and allow for much better renderings and manipulation of the project you are working on, but I’ve found the free ones get the job done for what I need. Not to mention the better programs are stupid expensive. My 3D printer is a Bambu Labs P1S and came with its proprietary software Bambu Studio, but like many of the other programs out there it uses the standard file types, and there are several sites out there that have free files that you can upload to the device, and you can scale them to the size you need as well as make alterations to them. Somewhat like my laser engraver/cutter, there were a few days of beating my head on the table trying to figure it all out but it didn’t take too much time before I was off and running. -Brian
-
Thank you Eric! Dabbling away is a perfect way of putting it, it’s definitely been a slow process, but I am making headway. I really hadn’t planned on getting into 3D printing either, but like I said in my post, it was way more cost effective to get a printer and build the pieces myself than ordering them online. The printer was less than $500 and the filament is dirt cheap, a 1000g spool runs about $14 and goes a long way. The grand kids get a kick out of it as well. I think so far we’ve printed several dragons and numerous fidget toys for them. -Brian
-
Thank you Keith for the kind words. After reading your reply, I realized that I never actually gave it that much thought that many of us are dependent on suppliers for some of the pieces and parts of our builds. I’m just somewhat eliminating the middle man in a way, and the creativity of designing and printing my own pieces is just my own method of building my models. I do appreciate the enlightenment. After purchasing the printer, I now understand that the cost for the 3D printed parts that I have previously ordered online is not so much in the materials, but in the design process (and equipment costs)that goes into the pieces. The quarter that I used for scale in my photo above covered the cost of material for all the pieces I printed with change leftover and only took about 20 minutes to print. So feel free to send me your order any time! 😁 -Brian
-
Hello again everyone, Finally back with a small update. This summer has been a crazy busy one on projects other than shipbuilding. I managed to steal away for a few hours over the past couple of months to get some work done, but not a whole lot. First thing that I was able to get completed was the AC unit installed. Not a big step, this part was completed way back when, but I am just now getting around to gluing it in place. I still need to add the support brackets, but it is place for now. Next I was able to get the tow knee bumpers built and installed. It was only until I posted this picture that I realized that you can't really make them out due to the lighting, but they are there. I finally took advantage of a rainy weekend (a rarity here in north Texas during the summer) and did some work on the lift booms. These are used to load and offload equipment, supplies and the Zodiac. For the main support posts I started out with a dowel and cut the gussets and caps on my laser engraver. Next it was on to the booms themselves. I made up a simple jig to get the angles the same on each boom, then glued the pieces together. Then I cut the gussets from some scrap ABS plastic that I had laying around and glued those in place. The hinges were built and installed next. These were made from styrene tubing. The other half of the hinges were made from aluminum materials I had leftover from my Cairo build and the hinge pins were temporarily made from scrap brass rod, leftover from the railing. I used the brass rod to help line up the hinge pieces while they were glued in place. The brass rod was removed and replaced with styrene rod of the same diameter so that I could heat the ends to create the crown on the top and bottom of the hinge pin. Both booms partially completed. Next I stared work on the winches that are attached to the booms. These were made from several different sizes of styrene tubing. The largest tubing was slotted to make the opening for the cable, the smaller two pieces were used to create the winch hub. I wrapped the hub with some rigging thread to simulate the cable wound up on the winch. I coated the thread with CA to hold it in place and give it a more steel cable like look. Then I inserted the hub into the winch housing. Then I made the hanging segment of the cable and used brass wire for the hook. The whole assembly is temp installed on the boom to get an idea of how things will look. It was time to apply a little primer to the boom assembly. And the final product. I made up the wiring harness for the control box from some plastic coated wire and finagled it through all of the attachments on boom. I started working on some of the deck details, such as the bollards and cleats, but I just couldn't get them to look right. While I was having a conversation with my son (while working on one of my other projects around the homestead) he mentioned that wouldn't it be easier to 3D print some of these deck details. Well after mulling it over I decided that he had a good point, that would be much easier. There have been a few build logs where I have read of people using 3D printers to create some of their pieces and I have used 3D printed parts on may past two builds so I looked into websites that sold 3D printed parts. Well, I was able to find a few pieces that I was looking for but I was somewhat worried that the scale wouldn't be just right and after shipping the parts weren't really worth it. So I did the next best thing, we invested in a 3D printer. Now I can make anything and everything that I need for the deck features. Some truest may think this is cheating, but since most of this build has been created on my laser cutter, why stop cheating now. Besides, these printers and filament have gotten so cheap that we could make good use of it making toys for the grandkids along with model parts. My first attempt at making life rings, barrels, cleats and trash bins. So that is as far as I was able to get this time around. I still have a lot of work to finish up with on the property before the weather turns cold, but I'm hoping to find a few hours here and there (or another rainy weekend) to get more work completed. I do appreciated everyone sticking with me on my extremely slow progress of this build. Until next time, thanks for stopping by. -Brian
About us
Modelshipworld - Advancing Ship Modeling through Research
SSL Secured
Your security is important for us so this Website is SSL-Secured
NRG Mailing Address
Nautical Research Guild
237 South Lincoln Street
Westmont IL, 60559-1917
Model Ship World ® and the MSW logo are Registered Trademarks, and belong to the Nautical Research Guild (United States Patent and Trademark Office: No. 6,929,264 & No. 6,929,274, registered Dec. 20, 2022)
Helpful Links
About the NRG
If you enjoy building ship models that are historically accurate as well as beautiful, then The Nautical Research Guild (NRG) is just right for you.
The Guild is a non-profit educational organization whose mission is to “Advance Ship Modeling Through Research”. We provide support to our members in their efforts to raise the quality of their model ships.
The Nautical Research Guild has published our world-renowned quarterly magazine, The Nautical Research Journal, since 1955. The pages of the Journal are full of articles by accomplished ship modelers who show you how they create those exquisite details on their models, and by maritime historians who show you the correct details to build. The Journal is available in both print and digital editions. Go to the NRG web site (www.thenrg.org) to download a complimentary digital copy of the Journal. The NRG also publishes plan sets, books and compilations of back issues of the Journal and the former Ships in Scale and Model Ship Builder magazines.