-
Posts
749 -
Joined
-
Last visited
About Jond
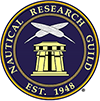
Profile Information
-
Gender
Not Telling
-
Location
Boothbay Harbor Maine
Recent Profile Visitors
-
ccoyle reacted to a post in a topic: Bowdoin by Jond - FINISHED - BlueJacket Shipcrafters - 1:48 - DIORAMA
-
ccoyle reacted to a post in a topic: Bowdoin by Jond - FINISHED - BlueJacket Shipcrafters - 1:48 - DIORAMA
-
ccoyle reacted to a post in a topic: Bowdoin by Jond - FINISHED - BlueJacket Shipcrafters - 1:48 - DIORAMA
-
SiriusVoyager reacted to a post in a topic: Beam Trawler Harvard 1926 by Jond - 1:96 - early steel hull by Rice Bros
-
GrandpaPhil reacted to a post in a topic: Beam Trawler Harvard 1926 by Jond - 1:96 - early steel hull by Rice Bros
-
Roger Pellett reacted to a post in a topic: Beam Trawler Harvard 1926 by Jond - 1:96 - early steel hull by Rice Bros
-
TBlack reacted to a post in a topic: Beam Trawler Harvard 1926 by Jond - 1:96 - early steel hull by Rice Bros
-
Jerome thank you for sharing that great reference. the more I look, the more I see i do not know much about fishing. One thing I learned through reading during this build is to visualize all those cables moving and fish jumping around on deck and the noise, the rolling and the cold and wet and the....it doesn't end. I am very grateful to drive about a mile to the local grocery store and find fresh fish right there. I just received 18 3 ring binders chocked full of the complete Rice brothers collection and will be fully focused on going through those and making up a slide show / talk series on their incredible history for our local historical society. I hope I can do them justices. cheers jon.
-
Jond reacted to a post in a topic: Beam Trawler Harvard 1926 by Jond - 1:96 - early steel hull by Rice Bros
-
Harvey Golden reacted to a post in a topic: Beam Trawler Harvard 1926 by Jond - 1:96 - early steel hull by Rice Bros
-
TBlack reacted to a post in a topic: Beam Trawler Harvard 1926 by Jond - 1:96 - early steel hull by Rice Bros
-
Mirabell61 reacted to a post in a topic: Beam Trawler Harvard 1926 by Jond - 1:96 - early steel hull by Rice Bros
-
11 deck work nearly done and it’s time for a punch list This posting includes the part of my builds where I may be getting to the end of the model part but have a similar effort to put together the story to tell in the summer months. First up though let’s see how far we have come… Since last time I have focused on the rigging and the stern. Also, more research on both fishing and on the yard. For planning I share three images 1 here is the fore mast as shown on the Rice brother’s plan. After looking at several photos of different versions of a dragger, I chose to follow these plans. I am still guessing if the hoist line from the boom as indicated is for two dropped blocks with the halyards back at the mast, of if the single line aimed midship is the one halyard going down near the winch. There was a smaller winch I believe connected to the ice chopper forward of the foremast, so I may take the lines there. I am not sure the big winch running this line would make much sense. 2 here is the mizzen mast. It is quite simple compared to others and I plan to keep it that way and add a sail for fun. 3 In my continued research of the yard, I found this great image of the dragger Fabia, she was a wooden dragger 132 feet built by Brother Frank Rice next door in 1920. I share her to show quite a variation in rigging and only built 100 feet away. Thus, my decision to stick to the plans. Work update. Here we are today looking at the rigging 4 looking at the foremast I need to complete the ratlines, mast light and figure out the hoisting lines. 5 looking at the mizzen we see our sail is up . I used grey thread for galvanized cables; lighter weight with no turnbuckles for the stack. 6 looking amidship we see the boats. Based on the photos they are on raised platforms pushed out to the bulwark line. This platform also provided a little more cover on the working deck. I found the idea of a single davit interesting and challenging for the users. A few details....Thanks to Jerome I did not continue with rope for the main two net lines. I chose to use thin annealed steel to give the look that was closer to spun steel. The problem with my limited skills is how to make it tight enough to look like it is in tension. 7 here we are on the reels. At a larger scale I might have tried braided picture hanging cable of some type of fishing leader. 8 here we are with the active otter board on the starboard quarter. 9 close up… It is still loose, and I need to figure what to do with copper chain etc. I ran out of good black tape and the shiny piece is awful. 10. This view is the inactive side and I am making the solution up. I spliced a heavy line to hold the otter board overboard on this inactive side. 11 here up forward I am gluing down the active gallows frame. 12. looking at the fore deck we see the cables are steel but a bit loose. I also need to figure out the ice machine foreword of the mast. I have decided not to include in this build......a guess at what the checkerboard type set up of compartments for sorting fish, missing quarter lines that would go from the end winches through multiple sheaves to the center of the net, stored net on deck[ after deck read], or any fish. I do, however, have a few figures and it is always fun to place them aboard too. The punch list is really straightforward. I will be shifting more time into preparing the powerpoint story, so the model and story are done in the spring. Being me however, I will start another build by then too. All for now.
-
Nils thank you for your kind comment. I regularly watch your work and I must say it inspires me especially at this small scale. cheers
-
thank you John and Jerome Jerome you caught me just in time. I was already yesterday to connect the first line to the otter board chain at the aft gallows. Now I need to decide how best to replicate used but not rusty steel cable, I used the grey thread for galvanized shrouds and stays. If I use black, where is the shine. Perhaps it it new? I will think on it but not too hard...smile I appreciate the catch however and the "rope" will go away. cheers
-
Jond reacted to a post in a topic: Beam Trawler Harvard 1926 by Jond - 1:96 - early steel hull by Rice Bros
-
10 update on the deck work This update does not reach any milestone; it just ticks a few more boxes. I wanted to start forward and work my way aft. I must say reading more about these trawlers simply amazes me about how tough the work was, and in some cases still must be. What I hope to show will cover the main control of the nets. I have looked at several photos but keep going back to the Rice Brothers plan when deciding what to build. 1 here is the blow up of our only photo of Harvard as a fishing vessel. The ovals are looking in the shadows to determine the size of the main cable reels. 2 this image is another internet sourced photo of an older beam trawler. The reels seem a bit smaller, but the lines are clearly steel cable. I don’t plan to include more images from the 1912 model by Erik Ronnberg but there is much information on how these things were set up and his interpretation of a deck lay out. He pointed out that he too had no deck drawings and few useful photos to use. His diagrams and explanation though were incredible as usual, and they make up my limited understanding. 3 here is a blow up of the Rice Brothers drawing that I have annotated. I felt I could do that after reading all of Erik’s articles, so I gained a beginner’s knowledge. Differences from his conclusion include: • The side bollards to take the main cable aft to the aft gallows are forward and parallel to the main four bollards. Set up is the same for the 4 main bollards. • There were two fish hatches not one. • The gallows braces go to the mast and fore deck as there is no center cabin enclosing the foremast. • The ice crusher/ hatch is forward of the mast. Similarity includes…. I plan to assume rope for the main lines. If I learn that I am wrong I will hopefully be able to paint the exposed line dark to simulate ugly used steel cable…..smile. back to work 4 to make the reels I fell back to my non machinist approach that started making winches on the Boothbay Harbor One Design RC racing sloops I built years ago at 1:24 scale. Copper and brass washers of multiple sizes. The small end winches for the quarter ropes are two open brass open rivets. The shaft is combination of nested brass tubes going from the smallest holding the rivets to the largest holding the washers. There was flux and stuff all over it after soldering so I dropped it in a pickling bath thinking it would clean up. Oops that was not the right solution….see the salting. Anyway, after several attempts they cleaned up. I used Costello wood for the end frames. 5 here is an overview of the large reels with rope coiled. The two hatches are in; just styrene on a block. The bollards are turned dowels set into a small block of poplar. 6. looking forward my rail method of cut off pins and tied painted line is clear to see. I am not ready to electro or is it resistance solder tiny pieces, so hopefully this method continues to work for me. The block for the ice crusher is a place holder now. The gallows are under way and are the main feature to come next. I was glad to read that the name breakwater is the right name for the curved plate. 7. just an overall shot. The cabins are in place, the rigging has started and the after deck work is next. All for now
-
9 fore deck and cabin work As we complete 2023, I wanted to have the basic “canvas” [ hull, decks, and cabins] done so next year I can focus on learning how they fished and what a trawler was all about. I also wanted to fit my work into the story I am forming to tell next summer to include the work of the Rice Brothers and how their inspiration of introducing steel hulls made such a change to this market. Meeting with Robert Rice, heir to the famous shipyard, has opened an incredible source. One example is how he helped me decide on one of the options I shared in making alternate mockups for the main cabin/ pilot house. As I previously posted, I was wondering about the difference in the shipyard drawing with the undated photo of Harvard within which there is a raised platform around the deck house. Robert told me that in the earlier days, unlike today, changes to the work in mid-stream were less often and less significant. Looking at the Harvard photo he concurred that the platform was likely a later change, not original. I decided not to add the raised platform around the pilot house. That decision also means I am most likely keeping the build to match the other draggers of the same design built earlier, 1918-1921 in the same yard. I share below my process to decide then build the foredeck and cabins. 1 here is a great drawing from the Erik Ronnberg article explaining the cross section of the typical dragger of this size and era. I note the fore cabin for the crew in this version goes fully below the main deck level. In the Rice Brothers drawing the crew quarters are all above the main deck. The plan here raises the foredeck with a rounded deck line [ seen is previous posted photos] . it is not the same. Also confirmed with Robert Rice the Boothbay built draggers did not have aft below deck captain cabins. 2 here is the Rice Bros drawing. We see the portholes and the full height of the deck. There is a rail and a breakwater [ not sure of the breakwater is the right name of that feature, same as on lightship], and the anchor winch. 3 here is the Harvard alongside the dock after launch. The high square foredeck is clear. 4 here it is hard to see, but I believe visible enough to clarify three points. Red oval: the fore deck has rails and wood surface in the center and curved breakwater just like the Ronnberg model that I shared in an earlier post. Green oval: the profile of the bulwarks is what I am trying to follow. The raised deck starts before the main cabin running aft as the bulwark suggests. Blue rectangle shows the configuration of the lower main cabin in steel with brackets for the top deck. 5. here is the Rice brother’s drawing cropped for the cabin profile and deck rails. I used this for the build. To work I decided to make the upper deck, stack and rail stanchions using brass. 6. here is a dry fit. Also noted the wood decking portion of the foredeck. 7 in this closer view the styrene angles are used for the bulkhead stanchions. I use the angle not because I know that it’s right, it just looks more like steel and not wood. 8. ,9. Here are two New Year’s progress photos. Looking forward I need to learn more about how the draggers worked. Happy New year
-
Jond reacted to a post in a topic: Lightship #112 NANTUCKET 1936 by Jeff Preisler - FINISHED - BlueJacket Shipcrafters - Scale 1/8" = 1'
-
8 progress on the hull Just a few bits of progress heading to the end of the year. I need to complete the stern and bow and then with a sub deck in place get the bulwarks done. 1 here I am building up the fantail using 1/64-inch plywood. 2 as we see clamping is tricky. 3 here I am building up the bow. I have chosen to follow the photos of the real Harvard at launch. 4 here is the Erik Ronnberg bow. Note the rounded affect. I like the wood deck insert but do not follow this curved profile. 5 here we see Harvard being launched and the fore deck is clearly as high as a man. A second meaning is there is clearly room for the crew area under the foredeck. The design drawing I have varies a bit but includes three portholes for three births in this area. As I mentioned before, I was not happy with my first rudder assembly as it ended up off center. This new set up used the aluminum foil to raise the little tube gudgeons and rudder hopefully to meet the centerline of the post. 6 here is the set up. It came out better, but still not on center. I may go one more time to try to get this right. Now time for the sub deck and bulwarks. As I shared before I goofed by making the bulkheads too high in such a small model. I roughed them down and to recover and decided to cheat. I added a 1/64 plywood sub deck to mitigate the issue. 7 here we are gluing down the plywood sub deck. 8 in this view I am gluing on the reraised bulwarks to meet the profile. And here are two photos for the xmas progress. 9, 10 the little wood blocks are still mock ups of configurations from different sources, since I have yet to find good photos of the completed vessel. I am still looking. I also have confirmed in the photos, but not the drawing, that there was a breakwater across the top of the fore deck to hold back water from coming on board. The question is, was that installed when built or added later. More on that subject next time Happy Holidays
-
07 what should the deck house look like? The last week has included more searching while I peck away at completing the hull. I received a few pieces from my friends at Bluejacket, so we can add anchors and the like. I am also fretting over my deck support dilemma. I am trying out a short cut and will see if it works...... 1 First up…. here is photo of the construction paper on the hull before paint that I forgot I had taken before painting. It should have been in the last posting. 2 Second... we look at the master’s Erik Ronnberg rudder and propeller. 3. Here is my first attempt. It came out with some defects that I will have to rebuild. I need to figure out a really thin shim that will not attract solder to hold the rudder at the center of the thicker post. I had set a aluminum sheet under the brass rudder , but unfortunately, I ended up with the rudder off center…opps I share the good side …smile Now to the study of deck house 4 here we see a blow up of the only photo I have been able to find of Harvard in at some point in her 20 year fishing career. Note the platform surrounding the pilot house. It looks like the top level roof goes back toward the stack [. This is the critical point discussed below] 5. this view is blow up of the Erik Ronnberg model of similar design. The pilot house is very small, no captain cabin behind. The lower-level cabin is much in head room etc., and the stack is forward and through the deck house. The view is invaluable for detail but not our configuration. 6 this blow up is from the 1920 +/_ Rice Bros drawing for the four trawlers. It should be noted that they were launched 1919-21. There was a recession in 1920 and many fishing companies were in trouble and cancelled orders. It was not until 1925 that Harvard was contracted again and was completed. Thus, it would have been possible for a different configuration. The two capt and mate cabins may have been squeezed it. It is hard to determine from the photo. The whole upper level was raised and I feel it is clear it ran aft behind the pilot house door, but for one or two cabins would be a guess on my part. 7 finally here is a photo of a trawler at Maine maritime Museum. I find it interesting of the similarity. It clearly includes a captain’s cabin behind the pilot house. It also has a small second cabin behind. We are definitely in the right family of vessels. Now what to do?? 8 here is sketch showing the three options. I have determined to follow the plan for the long complete Lower deck house as drawn. There may be a variation in doors, but something needs to be decided. 9 here is a mockup of what the configuration would be if I build to the plan. 10 here is a mockup of what the configuration would be if I build to the photo. I will need to decide which way to go. I will have access to more of Robert Rice documents soon I hope, and that, along with talks with Robert will be used for my decision. In the meantime, I need to continue to peck away at the hull, solve the deck so i can get the bulwarks figured out. The fantail has been roughed in with 1/64 plywood. I need to see if I can make that work too. plus it is the holidays cheers
-
Thank you Gary and Roger Gary. watching your builds inspires us amateurs to give fishing vessels a try. the big winch that runs everything is well over my pay grade and will take some more study. Roger I have a friend here who is a machinist and he said to me he uses both, so I am sure I will be off to Amazon again for a sponge. My brass rudder is off center, as the aliuminum shim was too thick, so I will show the good side in the next post but know I need to re build it....smile cheers
-
6 let’s figure out the top rails and hull plating. Sometimes I think I am so smart… then I suffer. In this build I made the top of all the bulkheads to be at the deck line. I used this method in larger models where one has reasonable access to sand, remeasure and adjust. I was thinking this is a shortcut, as the deck can then just sit there. Well, it was not that smart. Unlike a 4-foot RC sailor with 10-inch-wide deck, or even a 27-inch schooner with 5 inch beam, I have less than 3 inches across the deck. There is no convenient way to get in there with control to sand down multiple bulkheads for that nice surface needed to directly place the decking. If I had made them all just 1/8” lower, I could have made up deep deck beams and glued them to one of each bulkhead. In one day, all would have been done. Now who knows… In the meantime, we need to figure out where we raise the bulwarks to fit the profile and set top rails. We have several sources to use: • The Ronnberg profile drawing is our starting point. The rounded “domed” fore deck shown in his work was not evident in the photos of the Maine Trawlers • The Rice Brothers photos are the goal. A few adjustments may be good enough. • Internet photos of Harvard then Bellefonte then Albatross III. Unfortunately, the vessel was extended 20+ feet all in the forward area so interpretation is required. These all together should however be enough to cry uncle. 1 here is the detail line drawing from the Ronnberg article that sets the designed bulwark dimensions for vessel. I have annotated a few elements to give heights for the bulwarks. The deck line is also shown on the profile drawing to check as well. 2 here is a detail photo of the Ronnberg model trawler fantail. Mine will never look this good but it is something to aspire too. I thought I would first try to do this in 1/64 birch plywood and if no good, do it in styrene. Let’s see where it goes. Just last week I began a series of interviews with Robert Rice. At 85, he is the last remaining Rice brother heir that worked in the plant around 1950. He chose not to stay there, and he spent 28 years in the army. When he retired in 1976 and began building houses. After a few years, he realized no one had memorialized the family history. He decided to do that and spent the next 40 years accomplishing an amazing library of photos, models and records. He joined with Jim Stevens, an East Boothbay Shipbuilder in his own right, who started the local Boothbay Region Historical Society where much of their work resides. In his home he has a 5-foot shelf of photo and memorabilia albums showing every vessel. He has great models too. He looked at the model I recently made of the Lightship Overfalls and instantly showed me an error…oops. I will post that over on that log next week as it is fun, and I will include a photo of his model of Columbia and the story of the major design changes that Rice Brothers had done to the two ships built around 1950. Back to the trawlers. Quite a story. Jacob Stevens, who a few years later opened his own yard, was working as the designer for Rice brothers when they won these Trawler contracts and the first lightship Poe. Unfortunately, a fire in 1951 destroyed all the stored drawings. A few survived including a profile and deck plan for these trawlers. I include here a photo of the photo in Robert’s album of the Beam trawler blueprint profile. There were 6 variations of them built but here is the plan…..wow what a find. 3 the plan profile as developed by Jacob Stevens who worked at Rice bothers for years before starting Goudy and Stevens yard in 1920-24 Now let’s do some comparisons. I cropped and blew up each portion to compare and plan. 4. here we see the bow area. I show both the Quincy Ma [ via Erik Ronnberg] cropped profile with the Robert Rice photo. I will do my best to replicate the Rice Bros drawing but note the lack of high foredeck visible in the photos. 5 here we see the stern on a red color version of the blueprint Robert had. This red version is clearer, and I am using it for dimensions. I scaled it in Turbo Cad for that purpose. It seems the Rice Bros profile had less rise than what I have built. I need to acknowledge that, but we have followed the Quincy, Ma. lines and have what we have. 6. here I share the whole profile. I am thrilled to now have drawings of the on-deck features to follow and that is key to getting where we want to be. Any work going on? If I have learned anything in the 10 years of this work is get the sequence right. I am trying to finish 4 things at the same time and some impact the others. I think I figured our my “path”. 7 here we see the blue tape indicating the top of top outer plate. I cannot complete the added bulwarks until I remove the stands, as they are used to maintain the waterline dimension. The lower tape is the water line. I need to get the out plates on, then the waterline painted then remove the stands and complete fixing bulkheads for deck and bulwarks for rails. Following the tip from Roger, I bought spray shellac and applied it to construction paper before cutting strips on a paper cutter. I then cut both 8 foot and 12 foot in scale pieces and laid out the out “strakes”.[ not sure what one calls a line of plates]. I then cut vertical lines in the remaining hull to represent the same type plate spacing. I used simple diluted white glue to adhere the paper and then rattle can red and black. I suppose I could have applied a double layer of paper but decided at this scale not to do that. I would add plating to both inner and outer if trying 1:48 or bigger scale. Here in three pictures, we see the result. The Satin label on the cans failed me as there is a definite shine. We all know there will be another paint job after all the remaining work, so I will dull it down a bit. 8. stern view 9 bow view 10. over exposed but whole view to see the plating. Next up will be to complete the bow stern and raise the bulkheads and get ready for the deck. All for now
-
Andy. thanks and interesting. I have read several references as well that the big four,five six master schooners often needed tugs too. I recently learned of a whole new niche of schooner barges that combined old schooner and even ship hulls with the big tugs tugs looks like they may deserve more headlines than they get . I ll save that rabbit hole for later. back to fishing
-
thank you Roger Andy and John for dropping in Roger. following your work I have been watching a few more soldering tip videos. I have ordered a brass tip cleaner and when it comes will work on tinning and maybe some brass work. I currently work woth a blow torch. very amateur . Andy I agree with keeping a bit of a gas motor before heading out too far..... the anxiety reminds me of Robert Perry who had chartered a steam powered bark named Windward for his 1898 voyage. under power it only did 3 knots so he waved good by in New York city and took the train to Sydney, Nova Scotia to meet up with her. Early stream did not enhance travel speed in sail other than with no wind or direction etc. I agree with your thought that perhaps fishermen were nervous to go cold turkey all engine. It is interesting if one simply googles trawlers and especially adding in the search "models" one quickly is in the world for sail power trawlers. hardy soles to say the least. John. would love to hear about trawling down under. did the market follow the British model and go to steam before 1900? cheers
-
Jond started following SS Benjamin Noble by Roger Pellett - 1:96 - Great Lakes Freighter
-
Roger like many other of your followers I am reading your posts more than once. I am learning much as you tackle the many challenges of working to replicate on deck details. Your brass work is wonderful and inspiring. I may try a little. the hatch covers introduced your use of the 'NRG thin rig guide , and has encouraged me to buy one. I find ripping less than say 3/32 against the normal guide from a sheet gets me some variation. Thanks for sharing that tip jon
-
Thank you Andy Roger and Jerome. Andy. there are images in the Erik Ronnberg articles that show sails fore and aft on the two masts. Those plans were for the Boston market 1905-1912. I will add those images later when I hopefully get to rigging. presumably they were for either stability or emergencies. Roger. I remember being entertained and learning of the competition and jokes amongst Finn. vs Swede in that part of america. My relations were Swedes of Wisconsin and I had a college friend, a Finn from Minnesota. I am also holding my breath as I study your decision to go all brass above the deck in your build. wow. Jerome. always a pleasure and I will be asking more help again once I get to go above the deck work. I may try some brass we'll see. I also have my supply of styrene. cheers
-
Roger Thank you for dropping in. Also, thanks again as it was your tip that got me to Erik Romberg’s articles. thanks for this hint as it answered my exact question.....I had read much of your blog previously ands went back last night to reread. Somehow [ though it was over a year ago] I had missed the entries you referred to here about using spray shellac on paper before installing. I did remember the part of having a bowl of warm water handy…funny how common sense helps. Wow great tip again and exactly what I am trying to figure out. Running through your blog again and seeing all the great lake mariner’s input I have one too. My father-in-law grew up in Superior, Wisconsin. His dad was an ore boat captain named Anderson. My father-in-law learned to dislike the water and escaped first to college in southern Wisconsin and then moved to west Virginia in the 30’s. Then one day in 1940 he joined the navy and became the engineering officer on a tin can destroyer all over the Pacific. His stories were not filled with fond memories of Oceans. Anyway, thanks for your help and inspiration through your own work.
About us
Modelshipworld - Advancing Ship Modeling through Research
SSL Secured
Your security is important for us so this Website is SSL-Secured
NRG Mailing Address
Nautical Research Guild
237 South Lincoln Street
Westmont IL, 60559-1917
Model Ship World ® and the MSW logo are Registered Trademarks, and belong to the Nautical Research Guild (United States Patent and Trademark Office: No. 6,929,264 & No. 6,929,274, registered Dec. 20, 2022)
Helpful Links
About the NRG
If you enjoy building ship models that are historically accurate as well as beautiful, then The Nautical Research Guild (NRG) is just right for you.
The Guild is a non-profit educational organization whose mission is to “Advance Ship Modeling Through Research”. We provide support to our members in their efforts to raise the quality of their model ships.
The Nautical Research Guild has published our world-renowned quarterly magazine, The Nautical Research Journal, since 1955. The pages of the Journal are full of articles by accomplished ship modelers who show you how they create those exquisite details on their models, and by maritime historians who show you the correct details to build. The Journal is available in both print and digital editions. Go to the NRG web site (www.thenrg.org) to download a complimentary digital copy of the Journal. The NRG also publishes plan sets, books and compilations of back issues of the Journal and the former Ships in Scale and Model Ship Builder magazines.