-
Posts
2,125 -
Joined
-
Last visited
About JSGerson
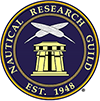
- Birthday 11/04/1946
Profile Information
-
Gender
Male
-
Location
Aiken, South Carolina
Recent Profile Visitors
-
schooner reacted to a post in a topic: USS Constitution by Avi - BlueJacket Shipcrafters - 1:96
-
BruceWayne426 reacted to a post in a topic: USS Constitution by JSGerson - Model Shipways Kit No. MS2040
-
SUBaron reacted to a post in a topic: USS Constitution by BruceWayne426 - Mamoli - 1/93
-
mtbediz reacted to a post in a topic: USS Constitution by mtbediz - 1:76
-
USS Constitution by mtbediz - 1:76
JSGerson replied to mtbediz's topic in - Build logs for subjects built 1751 - 1800
Need I repeat myself, beautiful workmanship!! I'm curious, do you plan on covering the complete hatch coaming area with the hatch work, or are you going to leave one half uncovered so the observer can look down to gun deck like I've seen others do? Jon -
mtbediz reacted to a post in a topic: USS Constitution by SUBaron - Model Shipways (MS2040) - 1:76
-
mtbediz reacted to a post in a topic: USS Constitution by BruceWayne426 - Mamoli - 1/93
-
Gregory reacted to a post in a topic: USS Constitution by BruceWayne426 - Mamoli - 1/93
-
I saw your comment to mtbediz today and thought I would give a welcome aboard from a bunch of us USS Constitution active builders. We've been sharing our knowledge and comments with each other and we range from beginner to the more experienced. Although, as near as I can determine, there aren't many Mamoli builders for the Conny at present. There is one active (last post in January) builder, Oscardeuce and an excellent builder, Bill Edgin (Robnbill) who completed his Mamoli kit in 2021 that you might want to check out as you work on yours. Good luck and have fun Jon
-
JSGerson started following USS Constitution by BruceWayne426 - Mamoli - 1/93
-
Geoff Matson reacted to a post in a topic: USS Constitution by Der Alte Rentner - Model Shipways - 1/76
-
Stevenleehills reacted to a post in a topic: USS Constitution by Der Alte Rentner - Model Shipways - 1/76
-
SUBaron reacted to a post in a topic: USS Constitution by Der Alte Rentner - Model Shipways - 1/76
-
USS Constitution by mtbediz - 1:76
JSGerson replied to mtbediz's topic in - Build logs for subjects built 1751 - 1800
Peter, I found the images of this model by Mark Antczak on Shipmodel.com, a company that sells boat models. Unfortunately, this model is not displayed any more at this site. However here is a limited blurb about this model from this Shipmodel.com at the time I down loaded the images: I will post the seven addition photos of this model that I have on your blog so as not to intrude too much on Mustafa's beautiful instructive blog. -
Here is my work area. It's the "bonus room" above my garage. What is seen in the photo is about 1/3 of the room. My major power tools are my Byrnes saw, Byrnes thickness sander, 50 yr year old Dremel scroll saw (very noisy and vibrates), and a small wood lather which are in the garage. You may also notices my astute "assistant" sleeping on my chair who periodically allows me to sit there and work.
-
USS Constitution by mtbediz - 1:76
JSGerson replied to mtbediz's topic in - Build logs for subjects built 1751 - 1800
Those pumps were not easy. I had a lot of false starts making those. Jon -
Getting back to the gun rigging, I decided to plunge in and complete the rigging once and for all. I just wanted to get it over and done with. Adding 22 fully rigged guns was no simple task. I made the following calculations and was staggered by what it revealed. From start to finish, adding eyebolts to the interior of the gun deck, to fabricating and assembling the gun trucks, and then rigging them, I got the following numbers: There are 235 separate parts per gun port or 5,170 parts for 22 fully rigged guns not counting brass blackening, painting, and do-overs. Most of these had to be fabricated from scratch. That breaks downs as follows: Gun & Truck = 26 pieces/gun = 572 pieces total Item Quantity Gun 1 Sides 2 Axials 2 Wheels 4 Transom 1 Breast Piece 1 Quion 1 Quion Handle 1 Quion Bed 1 Trunnion cap 2 Eyebolts 8 Rings 2 Gun Ropes (including excess waste) Ropes/gun: 10 cut pieces/gun = 220 pieces of rope total Recoil Rope. 1-6” piece 0.030” (0.76mm) dia./gun x 22 guns = 66 pieces = 132” = 11’ = 3.6 yds total Tackle Ropes w/coils 7” piece 0.018” (0.45mm) dia. + 1.5” (for double block)/tackle + coil = 8.5”/tackle + 1 rope coil x 3 tackles + coils/gun” = 7 pieces of rope/gun = 3 Tackles +3 coils/gun @ 25.5”/ gun = 154 pieces of rope = 561” = 47’ ~ 16 yds total for 66 tackles + 66 coils = 3,388 pieces total Rope Seizings/gun: = 21 rope seizings/gun = 462 seizings total = 3 yds thread total Recoil rope seizings 6 seizings/piece = 24” of thread = 2’ total/recoil rope Tackle seizings 5 seizings (@4”/seizings) /tackle = 20” thread/tackle rope 3 tackles/gun = 15 seizings = 5’ thread/gun = 3 yards thread total Note: rope coils made from excess rope and supplemented with additional rope 3 Tackles/gun = 6 blocks/gun = 132 blocks total 3/32” Single blocks 1/tackle @ 3 tackles/gun =3 blocks/gun = 66 blocks total 3/32” Double blocks 1/tackle @ 3 tackles/gun = 3 blocks/gun = 66 blocks total Block hooks 6/gun = 132 hooks total Gun Ports = 12 parts/port = 222 total Eyebolts: 10/port = 220 total: Recoil Rope eyebolts/port 4 = 88 total Tackle double eyebolts/port 2 = 44 total Idle eyebolts/port 3 = 66 total Deck tackle eyebolt 1 = 22 total Recoil rope bulkhead pins 2/port = 44 total All gun deck guns are now rigged!!! Whew!!! As I promised, an OSHA nightmare.
-
While continuing to work on rigging the guns, I took a diversion from this tedious task and once again went looking for figurines to be placed on the model later to add some scale. I added figurines to my 1:64 scale Rattlesnake which I finished in 2017 which worked out quite nicely and I want to do the same thing with the 1:76.8 Constitution which I started in 2017, but I’ve had no success finding any suitable figurines. For a typical 5’6” (165cm) tall man, I needed something around 0.841” (21.34mm) at scale. I was seriously considering modifying HO train figurines when I finally found five 22mm 18th (?) century sailor figures at Ages of Sail. I’ve checked this site before numerous times and even got the 25mm figurines for my Rattlesnake (1:64) from them some 8 or 9 years ago, but I never saw the 22mm ones until now. Strangely enough, the two sizes do not have the same figures, and are totally different from each other. Still, I immediately bought all five and it may be years (at my rate of speed) before I’ll need them. Who knows how long they will be available?
-
USS Constitution by mtbediz - 1:76
JSGerson replied to mtbediz's topic in - Build logs for subjects built 1751 - 1800
Those pumps are coming along real nice Jon -
I grew up in the Boston area and left to follow the paycheck in 1977, but I was fortunate to have visited the Constitution a couple of times before I left. I now reside in South Carolina where the paychecks ended, and I retired. My last visit to the ship was in November 2015, just before her last restoration which ended in 2017. I have mentioned in several other builders’ logs, that I had been collecting photos of the ship starting a couple of years even before started building the model. They range from the very earliest images (1857) to the present. Obviously, most of the 4,000 odd images I have, accumulated from a variety of sources, are not of the post 2017 restoration. The few photos you posted of your recent visit to the ship are wonderfully taken. They are sharp, clear, and well composed. (I was a serious amateur photographer in an earlier life). So, if I may impose on you to share any more photos, it would be greatly appreciated. If you (or anyone else) need an image(s) of something and can’t find it on the internet, I may have the image you’re looking for. Most times when you put in a search request for “A.” you may also get “B,” or “C.” If they are remotely relevant to the ship, I collect them because should I need to find them later, searching for “B” or “C” may not give me those particular images. Hence, I’ve got some rare or difficult to find detail images. If I may offer one critique with the photo of painting the waterways, if possible try to make sure you background is unobtrusive. Now I know you are a food and wine aficionado.🤫 Keep up the good work. Jon
-
USS Constitution by mtbediz - 1:76
JSGerson replied to mtbediz's topic in - Build logs for subjects built 1751 - 1800
Now I know, thanks! Jon -
USS Constitution by mtbediz - 1:76
JSGerson replied to mtbediz's topic in - Build logs for subjects built 1751 - 1800
Looks great! How did you tie off the rope at the bottom of the stairs as access is quite limited. If it's doable for me, I may attempt it myself. Jon
About us
Modelshipworld - Advancing Ship Modeling through Research
SSL Secured
Your security is important for us so this Website is SSL-Secured
NRG Mailing Address
Nautical Research Guild
237 South Lincoln Street
Westmont IL, 60559-1917
Model Ship World ® and the MSW logo are Registered Trademarks, and belong to the Nautical Research Guild (United States Patent and Trademark Office: No. 6,929,264 & No. 6,929,274, registered Dec. 20, 2022)
Helpful Links
About the NRG
If you enjoy building ship models that are historically accurate as well as beautiful, then The Nautical Research Guild (NRG) is just right for you.
The Guild is a non-profit educational organization whose mission is to “Advance Ship Modeling Through Research”. We provide support to our members in their efforts to raise the quality of their model ships.
The Nautical Research Guild has published our world-renowned quarterly magazine, The Nautical Research Journal, since 1955. The pages of the Journal are full of articles by accomplished ship modelers who show you how they create those exquisite details on their models, and by maritime historians who show you the correct details to build. The Journal is available in both print and digital editions. Go to the NRG web site (www.thenrg.org) to download a complimentary digital copy of the Journal. The NRG also publishes plan sets, books and compilations of back issues of the Journal and the former Ships in Scale and Model Ship Builder magazines.