-
Posts
871 -
Joined
-
Last visited
About JerryTodd
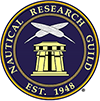
- Birthday 09/20/1960
Contact Methods
-
Website URL
http://todd.mainecav.org/model/
-
Skype
geraldatodd
Profile Information
-
Gender
Male
-
Location
Severna Park Maryland USA
-
Interests
Astronomy, sailing, horse riding, motor cycle riding, wood working, living history and reenacting, wargaming, ship modeling, history, maps, reading, ice cream, animals in general but cats especially, a lady named Daphne
-
egkb reacted to a post in a topic: Constellation 1856 by JerryTodd - 1:36 scale - RADIO - First Class Sloop of War
-
Ian_Grant reacted to a post in a topic: Constellation 1856 by JerryTodd - 1:36 scale - RADIO - First Class Sloop of War
-
A long time ago, the Naval Academy had the Macedonian figurehead scanned to create a 3D model. The people that did the scan found my, and my Macedonian model and offer to 3D print one for me for $250. I couldn't justify $250 for a 2 inch tall bit of plastic, so I declined. Years later, having my own 3D printer, I contacted these people hoping to may get a file I could accurately scale and print. They replied after several attempt to contact them, that they could not distribute the file because it was US Navy property. Then I found it posted on a public site, not downloadable, and with no contact information. Still there: https://sketchfab.com/3d-models/usna-macedonian-monument-uwSAs3DI5gtIRlQtrtFYfUcJbp6 Constellation's been without her head ornamentation for some time now. Figuring they're looking to replace it with reproductions and would have it scanned much how the USNA did with Macedonian's figurehead, I contacted Historic Ships Baltimore to inquire if that's the case, if so, was there a chance of getting copies of the files, and explained why I was asking. In short, the answer was "I don't know, but I presume NO." Out of curiosity, I checked my bookmarks to see if the Macedonian figurehead was still on SketchFab, and it was. Interestingly, on the right column was a "Billet_head" posted by the same Direct Dimensions only a month ago! Well if it isn't a scan of Constellation's billet-head, but wait, there's more... Going to their Sketchfab page, to see all their 3D model uploads, I found scans of Constellation's trail-boards! None of this is downloadable, and there's still no contact information, so... Billet-head: https://sketchfab.com/3d-models/billet--head-3mill-mm-d1422e4df6454a3dbea26ea5058d7109 Trail-boards: https://sketchfab.com/3d-models/us-constellation-filligree-43b0610e75c5460ea3661a33b92a79ec There's functionality in the Blender software to basically make a contour model from a shaded image, just like these. I hope using the best screen-shots I could manage will allow me to use that feature to finally produce Constellation's head ornamentation.
- 553 replies
-
- sloop of war
- constellation
-
(and 3 more)
Tagged with:
-
JerryTodd reacted to a post in a topic: Friendship Sloop by gsdpic - BlueJacket Shipcrafters - 1:12
-
JerryTodd reacted to a post in a topic: Friendship Sloop by gsdpic - BlueJacket Shipcrafters - 1:12
-
JerryTodd reacted to a post in a topic: Friendship Sloop by gsdpic - BlueJacket Shipcrafters - 1:12
-
JerryTodd reacted to a post in a topic: Friendship Sloop by gsdpic - BlueJacket Shipcrafters - 1:12
-
JerryTodd reacted to a post in a topic: Friendship Sloop by gsdpic - BlueJacket Shipcrafters - 1:12
-
JerryTodd reacted to a post in a topic: Friendship Sloop by gsdpic - BlueJacket Shipcrafters - 1:12
-
JerryTodd reacted to a post in a topic: Friendship Sloop by gsdpic - BlueJacket Shipcrafters - 1:12
-
egkb reacted to a post in a topic: Constellation 1856 by JerryTodd - 1:36 scale - RADIO - First Class Sloop of War
-
Ian_Grant reacted to a post in a topic: Constellation 1856 by JerryTodd - 1:36 scale - RADIO - First Class Sloop of War
-
Put ledgers, clamps, cleats, or whatever term is correct in this situation, in the head and made new templates from chipboard From which I modeled and printed new grates.These had a tendency to try to curl, so I attached wood strips to the underside to resist that. They then got primed and painted. There's vertical rub rails on the hull's side. In the 1856 portrait, I con only verify 3 at the main hatch, though more show up in photos from 1879 on, when she carried more boats as a training ship. I'm only adding the three per side I can verify. These were cut to shape to fit the hull, rather than try to spring a straight stick into place, and pinned with 1/16" brass rod; then they got some quick paint. The hull will get a proper paint job just before the chain-plates get installed.
- 553 replies
-
- sloop of war
- constellation
-
(and 3 more)
Tagged with:
-
Nirvana reacted to a post in a topic: America 1851 by Caferacer - Mamoli - Scale 1:66
-
JerryTodd reacted to a post in a topic: HMS Victory by dafi - Heller - PLASTIC - To Victory and beyond ...
-
JerryTodd reacted to a post in a topic: Amanda F Lewis 1884 by SardonicMeow - Scale 1:48 - Chesapeake Bay pungy
-
JerryTodd reacted to a post in a topic: HMS Diana by dunnock - FINISHED - Caldercraft - 1:64
-
egkb reacted to a post in a topic: Constellation 1856 by JerryTodd - 1:36 scale - RADIO - First Class Sloop of War
-
The crew got some touch up, and I tried a "wash" on them which wasn't all I hoped it would be, but I kept it and gave the a couple of coats of clear-coat. Ivan's blue uniform was certainly slimming, he's looking quite Stan Laurel-ish in white. I made a pattern for the head gratings from chip-board, scanned it and used the image to make 3D models. Went away for the weekend, and printed them when I got home. I need to install cleats (like seat cleats in a boat) for them to sit on along the spray-screens and hull. Then I can more accurately see how the shape may need adjusting, which may mean printing again, which didn't use much resin, but did take 4 hours.
- 553 replies
-
- sloop of war
- constellation
-
(and 3 more)
Tagged with:
-
3D Naval Guns 1850s ~ 1870s
JerryTodd replied to JerryTodd's topic in CAD and 3D Modelling/Drafting Plans with Software
Took three tries before the guns printed well in 1:100. Using thicker supports seemed to do the trick. I went back to the first version I started of this gun, with the taller carriage, to finish it. I used plate #7 of LaFay's, which had measurements, rather than the model plans I had used. Both are modeled in 1:36 scale and posted on Thingiverse. Two of the delivered guns sitting on the model -
3D Naval Guns 1850s ~ 1870s
JerryTodd replied to JerryTodd's topic in CAD and 3D Modelling/Drafting Plans with Software
le canon est complet! Loaded in the slicer, re-scaled to 1:100, copied to make 7 tubes and carriages, sliced and sent to the printer. Fingers are crossed! -
3D Naval Guns 1850s ~ 1870s
JerryTodd replied to JerryTodd's topic in CAD and 3D Modelling/Drafting Plans with Software
I got this far on it before I had to do other things today and tomorrow. Comparing the tube height to the sailor figure, this carriage is definitely a better match for the model it will be living on. I'm modeling it in 1:36 scale, but I'm printing them in 1:100. Besides what I print for my friend building the model, it'll get posted on Thingiverse when it's done -
3D Naval Guns 1850s ~ 1870s
JerryTodd replied to JerryTodd's topic in CAD and 3D Modelling/Drafting Plans with Software
I found I could download the PDF of Lafay, so now I have a reference if another French gun shows up on my inbox -
3D Naval Guns 1850s ~ 1870s
JerryTodd replied to JerryTodd's topic in CAD and 3D Modelling/Drafting Plans with Software
The Lafay link goes to the same carriage that I made, which I'm thinking is for a smaller gun, abiet very similarly shaped; but Douglas shows... which specifically says is for the gun I'm doing, so I think I'm going that route. Thank you very much Lieste, for pointing out a document I already had -
3D Naval Guns 1850s ~ 1870s
JerryTodd replied to JerryTodd's topic in CAD and 3D Modelling/Drafting Plans with Software
As usual, I have very few clues what the carriage for this gun would look like, so I have to conjecture it. This image is part of a set of drawings of the L'Agile (I think) which was a later ship. The drawing is 1:100 scale but there's no reference on the portion I got, so who knows what "scale" it might be. I modeled the carriage to this drawing and wound up with the tube six feet in the air; that couldn't be right, so I scaled the carriage down to the height of my 8 inch shell-gun. This is still top-heavy to my eye, but I don't think it would have been the low-slung Marsilly the IX Dahlgren had 10+ years later. I'm gonna dig around some more before I call this one done. -
3D Naval Guns 1850s ~ 1870s
JerryTodd replied to JerryTodd's topic in CAD and 3D Modelling/Drafting Plans with Software
I'm still looking for data on the 68# smooth-bore's carriage, without any luck. I contacted the folks at HMS Warrior to see if they had drawings for what was on the ship, but they said their system was hacked and a lot of data was lost. Recently, I was asked to do a Canon-Obusier of 80 pounds for a 1:100 scale model of the French L'Orenoque (1848). I modeled it in 1:36, and will scale it down in the slicer to print at 1:100. The carriage is two-truck type, and I'm working on that now. -
Print a few more stock figures, but only 7 came out. In the meantime I altered a couple of others; I put straw hats on two, and changed a rammer to a sponger. I apparently made the brims too thin, and they didn't print well, so I made new brims from paper, and painted them in resin from the printer, then zapped them with UV to plasticize them. Painting then commenced on this batch of 15 crew who will all be in white jumpers. I got to fiddling with the davits again by mocking up a brace with chipboard; thinking that would work, applied it to the 3D model, as well as putting a proper double-block on the end, with a ring. I printed a pair to test, and 6 hours later, I'm pretty happy with the results.
- 553 replies
-
- sloop of war
- constellation
-
(and 3 more)
Tagged with:
-
JerryTodd started following Friendship Sloop by gsdpic - BlueJacket Shipcrafters - 1:12
-
All the figures I have are now painted. Not my best work, but I'm not my best self anymore either 😕 I think I got a decent shade for the Black fella,and the rest are the darkest "fleshtone" I have without darken it more. I need to modify several poses to get men climbing the rig, standing on foot-ropes. sitting, squatting, and so on. Also, I want to put straw hats on a few I also have one officer to try to work into 3 or 4 poses. Then there's the Marines, I want 6 or 8 in different poses standing and sitting on the main hatch cleaning their gear.
- 553 replies
-
- sloop of war
- constellation
-
(and 3 more)
Tagged with:
-
Welcome aboard!
About us
Modelshipworld - Advancing Ship Modeling through Research
SSL Secured
Your security is important for us so this Website is SSL-Secured
NRG Mailing Address
Nautical Research Guild
237 South Lincoln Street
Westmont IL, 60559-1917
Model Ship World ® and the MSW logo are Registered Trademarks, and belong to the Nautical Research Guild (United States Patent and Trademark Office: No. 6,929,264 & No. 6,929,274, registered Dec. 20, 2022)
Helpful Links
About the NRG
If you enjoy building ship models that are historically accurate as well as beautiful, then The Nautical Research Guild (NRG) is just right for you.
The Guild is a non-profit educational organization whose mission is to “Advance Ship Modeling Through Research”. We provide support to our members in their efforts to raise the quality of their model ships.
The Nautical Research Guild has published our world-renowned quarterly magazine, The Nautical Research Journal, since 1955. The pages of the Journal are full of articles by accomplished ship modelers who show you how they create those exquisite details on their models, and by maritime historians who show you the correct details to build. The Journal is available in both print and digital editions. Go to the NRG web site (www.thenrg.org) to download a complimentary digital copy of the Journal. The NRG also publishes plan sets, books and compilations of back issues of the Journal and the former Ships in Scale and Model Ship Builder magazines.