-
Posts
118 -
Joined
-
Last visited
About John Fox III
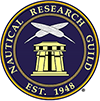
Profile Information
-
Gender
Male
-
Location
Ladysmith, WI
-
Interests
Miniature ship modeling, live music performing and fresh water fishing
Recent Profile Visitors
-
John Fox III reacted to a post in a topic: Oryol 1902 by GrandpaPhil - Orel - 1/200 - CARD - Russian Battleship
-
John Fox III reacted to a post in a topic: Kentoshi-sen by Glen McGuire - FINISHED - 1/400 - Bottle
-
John Fox III reacted to a post in a topic: Oryol 1902 by GrandpaPhil - Orel - 1/200 - CARD - Russian Battleship
-
John Fox III reacted to a post in a topic: Oryol 1902 by GrandpaPhil - Orel - 1/200 - CARD - Russian Battleship
-
John Fox III reacted to a post in a topic: Oryol 1902 by GrandpaPhil - Orel - 1/200 - CARD - Russian Battleship
-
John Fox III reacted to a post in a topic: Kentoshi-sen by Glen McGuire - FINISHED - 1/400 - Bottle
-
John Fox III reacted to a post in a topic: Oryol 1902 by GrandpaPhil - Orel - 1/200 - CARD - Russian Battleship
-
John Fox III reacted to a post in a topic: Oryol 1902 by GrandpaPhil - Orel - 1/200 - CARD - Russian Battleship
-
John Fox III reacted to a post in a topic: Oryol 1902 by GrandpaPhil - Orel - 1/200 - CARD - Russian Battleship
-
John Fox III reacted to a post in a topic: Kentoshi-sen by Glen McGuire - FINISHED - 1/400 - Bottle
-
Greetings, One doesn't have to use a funnel, a simple wooden plug in that shape would do. And that could be made to disassemble after the resin dries, with parts small enough to remove through the bottle neck. Anchor's A Weigh! John Fox III
- 185 replies
-
- Flying Dutchman
- Black pearl
-
(and 2 more)
Tagged with:
-
Greetings, What about using some sort of funnel inserted in the bottle, held in place while the clear water substitute is added. One could possibly then use something to create swirls and waves to the entire water surface? Anchor's A Weigh! John Fox III
- 185 replies
-
- Flying Dutchman
- Black pearl
-
(and 2 more)
Tagged with:
-
berhard started following John Fox III
-
While no expert on this subject, I see one problem with covering plastic decking, and that is thickness of the deck. It could mis-align parts that are later attached to/through the deck. I routinely plank solid hull and framed miniatures with maple veneer that I sand down to just 0.010" thick, which might work. Anchor's A Weigh! John Fox III
-
Help for blocks with hoop required.
John Fox III replied to Tony28's topic in Masting, rigging and sails
Tony, If I understand it correctly, take a piece of rope thread and seize it around the block for a short length, cut off one end of the rope thread,then wrap the other end around a drill bit shank that matches the diameter of the brass rod, then seize it towards the block. Hope that is what will help you. Anchor's A Weigh! John Fox III -
Greetings, Here are a few ideas I've used for case bases. First is a Lexington model in a glass case with a mirror for the bottom. I think it is sort of "airy" and shows the underside of the model too. The model was fastened to the base by scratching the mirror beneath the area with the wooden "waves" and then using epoxy to fasten them to the mirror. The second is a small scale model of a tahiti ketch model, with maple veneer "planking", minus any trunells, beneath the model. Anchor's A Weigh! John Fox III
-
Using a card-kit to ¨scratchbuild¨ a ship?
John Fox III replied to ubjs's topic in RC Kits & Scratch building
Greetings, Assuming the kit is a card model kit, then I would guess you could scan the pages and increase their size to meet the scale you desire. And use the results to make the various parts out of whatever material you wish. Anchor's A Weigh! John Fox III -
Greetings Glen, What a great idea and prosecution!! I had a ball following along, looked forward for each update, thanks! Anchor's A Weigh! John Fox III
- 290 replies
-
- Quinquereme
- Finished
-
(and 1 more)
Tagged with:
-
Greetings Glen, I enjoy your updates, often look forward to seeing them. When I've had to insert masts with rigging separate from other parts I usually wrap the mast/rigging in tissue paper. It helps keep things from getting too tangled, and is easily cut off later, though one has to be careful not to cut rigging when doing that. Anchor's A Weigh! John Fox III
- 290 replies
-
- Quinquereme
- Finished
-
(and 1 more)
Tagged with:
-
Greetings Glen, All I can do is echo the others, an outstanding job with this model! Besides being extremely creative, you did an excellent job! Anchor's A Weigh! John
-
Greetings, For many years I've used an aquarium pump to air out my light bulbs and bottles, no need to refill a tank or run a major compressor. Anchor's A Weigh! John Fox III
-
Greetings John, Depending on how much work you might want to do, I've used aluminum rod and tube to make railings, stanchions, cleats, ladders, masts and booms. One can find very small diameter tubing, and I also used both the aluminum wire and pour spouts from salt containers. The two images attached show my results using these materials. I used CA to glue the parts together. For the mast and boom I squeezed the tubing carefully, with another smaller brass tube inside it, to obtain the oval shape. Hope that helps! Anchor's A Weigh! John Fox III
-
Not to "bad mouth" Boudriot, however I purchased the ancre plans for BonHomme Richard from them of his drawings and found several errors. I later found in an NRJ article that he often made assumptions that were not correct as well. I was a draftsman for many years, before CAD, and know what Boudriot did. He re-used drawings already done for other vessels, without checking to make sure that the time periods of vessels matched, something that saves a lot of time when hand drafting. He also did not keep in mind that unlike the British, each yard building a ship was allowed to do things differently, there was no definitive plans for various ship parts that were adhered to. Not meaning to make your decisions more difficult, just pointing out facts I have learned. Anchor's A Weigh! John Fox III
-
Greetings Glen, Glad you found the info on my hidden hinges useful. That's what it's all about posting things here on MSW. It is indeed a wonderful place to find info and help. Anchor's A Weigh! John Fox III
- 194 replies
-
- Bottle
- Treasure Fleet
-
(and 3 more)
Tagged with:
-
Greetings George, Absolutely well done sir!! I make miniatures as well, and considering the materials you worked with you did an amazing job! Anchor's A Weigh! John Fox III
About us
Modelshipworld - Advancing Ship Modeling through Research
SSL Secured
Your security is important for us so this Website is SSL-Secured
NRG Mailing Address
Nautical Research Guild
237 South Lincoln Street
Westmont IL, 60559-1917
Model Ship World ® and the MSW logo are Registered Trademarks, and belong to the Nautical Research Guild (United States Patent and Trademark Office: No. 6,929,264 & No. 6,929,274, registered Dec. 20, 2022)
Helpful Links
About the NRG
If you enjoy building ship models that are historically accurate as well as beautiful, then The Nautical Research Guild (NRG) is just right for you.
The Guild is a non-profit educational organization whose mission is to “Advance Ship Modeling Through Research”. We provide support to our members in their efforts to raise the quality of their model ships.
The Nautical Research Guild has published our world-renowned quarterly magazine, The Nautical Research Journal, since 1955. The pages of the Journal are full of articles by accomplished ship modelers who show you how they create those exquisite details on their models, and by maritime historians who show you the correct details to build. The Journal is available in both print and digital editions. Go to the NRG web site (www.thenrg.org) to download a complimentary digital copy of the Journal. The NRG also publishes plan sets, books and compilations of back issues of the Journal and the former Ships in Scale and Model Ship Builder magazines.