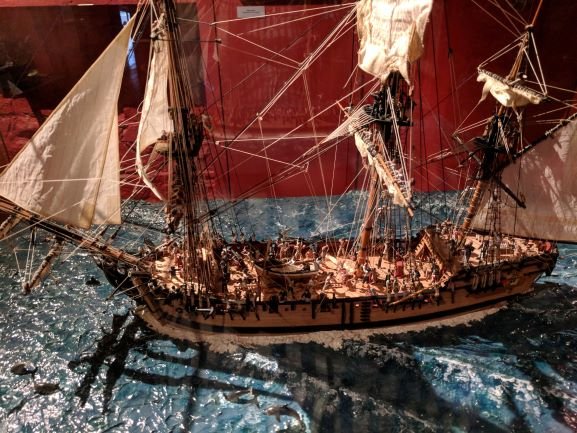
Fernando E
-
Posts
242 -
Joined
-
Last visited
Reputation Activity
-
Fernando E reacted to TK1 in HMS Sirius by TK1 - Modeller's Shipyard - 1:48 - Cross-section
Right, finally on to the build!
A delayed start, since I'm away from home caring for my parents, but got my wife to bring me a care package including the kit. And fitting as my father was a great wooden model ship builder, and this will be the last one built in his house and using some of his tools. But, I digress...
The first few steps see you building up the keel from 3 pieces, then attaching the 3 frames and longitudinal beams. Finally, bulwarks with gunport cut-outs are attached to each side. All pretty simple so far, but without an alignment jig or proper baseboard, it was all a bit fiddly and required a couple of squares, a drill-press vise, a couple of levels, lots of measurements, and even more clamps.
Here's the photos of the first few steps - apologies for the messy work area (he was recently doing plastic models so it's been a hunt for ship/wood tools but I'm making do!); and the large pics, I couldn't edit on his PC.
Next up, the first layer of planking and on to the lower decks.
Thanks for looking - early days but it'll get more interesting soon, I promise!
-
Fernando E reacted to Vinnie in Greek Bireme by Vinnie - Amati - 1:49
Well it’s been too long…
hello all who are interested …this will technically be my second build…however my last build (Hms Bounty) very sadly 😢…suffered a catastrophic accident and now no longer exists…no matter…I will build another better one…I learned a lot on my last build and intend to reach for higher levels of craftsmanship in the future on another bounty, but in the meantime while I considered which one to buy. I started work on this little Bireme. I’ve been at it for about 2 months now, but from this point hopefully I’ll post smaller more regular posts…
so, like several other past logs I’ve read, I’ve noticed the usual disappointments. The instructions are very vague, and some of the laser cutout pieces are inaccurate. However, the fun of model ship building is sometimes, problem-solving…so let’s do this.
at a snails pace, I added one bulkhead each day, obsessing over, trying to make it as square as possible. I end up being mostly satisfied with results, but I think next time, I could probably find tool that would do a better and easier job.
trying to fix some of the inaccurate frames… ended up being quite happy with my efforts…
The admiral took a photo of me using some tracing paper to trace off the plans for the stern cut out section… the balsa that is essential to complete this kit is not included. This is another criticism I have of this kit many parts that you need to finish simply aren’t inside the kit. Anyway…went out and have got a nice stash for my future balsa needs
a lot of the frames will still be quite visible when the model is finished…so I ordered some mahogany strips to cover up exposed areas…stern section all smooth and shaped.
Planked and sanded the inferior deck. Thought long and hard about whether or not to simulate tree nails. Did research on whether they where historically accurate…apparently a resounding yes…did a few test samples…I used toothpicks as the tree nails…
they seem less visible than what I imagined…however I still think they will add some nice details…so I’m going to go ahead with tree nails…
Will probably do tree nails on the walnut hull planking also…
in the process of doing the garboard plank…
and that is where I’m up to…please let me know if there are any suggestions or pieces of advice
-
Fernando E reacted to yvesvidal in HMS Bellona by yvesvidal - CAF Model - 1:48
As indicated before in my response to Kevin, I have been working on multiple fronts:
Making a bowsprit and its associated rigging. This is not part of the CAF model kit, but I wanted to present a little bit more than the traditional Admiralty Model approach and wanted to play with some lines and ropes. I have quickly came to the conclusion that I suck at rigging and my utter admiration goes to these magnificent models depicted with their full rigging. The second front has been building a stand to display this large (and very heavy...) model. I needed to do that before finishing all the details of the hull and in particular the gun port lids, which are very fragile when manipulating a massive hull of more than 22 pounds heavy. In addition, the bowsprit was necessary to calculate the dimensions of the stand. For the stand, I decided to copy somewhat, the display presenting the 1/32th - 1/36th scale model from the Royal Museum in Greenwich, UK. The display of the original model is composed of a drawer that can be pulled from the rear and which extends the ramps, and allows the sliding of the massive model for inspection. Exactly the way it should be done to convince a set of tight-fist admirals and finance comptrollers in ancient British times. My stand will not be so sophisticated but I wanted to replicate the shipyard ramps used to assemble and build these magnificent vessels.
After measuring the "beast", I ended up with some inside dimensions of 60" by 16". A friend helped me cut the wooden parts (poplar and plywood for the most part) and I started assembling and painting the display stand:
Priming that large box required a few cans of Primer and a lot of sanding. Each corner will see some modern handles (this stand has no pretensions to mimic the old cabinet or museum stands) installed to help with the handling of that large display.
The bottom of the box is covered with a piece of dark blue velvet fabric. An edge has been created to support an acrylic cover if I ever get a chance to buy one custom made.
Yves
-
Fernando E reacted to James H in HMS Indefatigable 1794 (prototype) by James H - Vanguard Models - 1:64
Some work has started on making mast parts.
At the moment, it's anything but tapering! I've just set up my lathe to make a start on the various dowel sections. In the meantime...
-
Fernando E reacted to AON in HMS Bellerophon 1786 by AON – scale 1:64 – 74-gun 3rd Rate Man of War - Arrogant-Class
Finished this on May 3rd. Should have posted earlier but jobs around the house have been keeping me busy and I plum forgot!
My sweeps or oars were made in one piece from Castello boxwood on my wood lathe using files and sand paper to shape the grip and shaft.
At 1:64 they measure about 2-3/8” long.
I found that when I noticed the shaft beginning to flex I was very near the proper diameter of 1/16”.
Shafts have been sanded to 0.059" diameter and grips to 0.03" diameter.
My sources for dimensions are the Specifications for Oars of the US Navy for the year 1900 published in the Nautical Research Journal and provided on the Model Ship World Forum, and also a formula provided by DRUXEY on the Model Ship World Forum with his build of the 28 foot American Cutter.
I have gone back to my ship build.
-
Fernando E reacted to kiwiron in HMS Victory 1805 by kiwiron - Caldercraft - 1:72
Coppering done. Re work on the keel with the spare plates, a bit better now. I'll miss the slithers of copper sticking into my fingers. Onto deck work now, my favourite part of the build.
-
Fernando E reacted to yvesvidal in HMS Bellona by yvesvidal - CAF Model - 1:48
I realized that I have not provided an update in a long time. Most of the time has been spent doing non-related model building activities and trying to replicate on the starboard side, what was done on the port side, during a previous post: Overall, a lot of the same thing....
The quarterdeck is now complete with all the guns in place:
Decals are delicately set along the side of the hull:
As usual the hull is prepared with multiple coats of Future Floor Gloss. Then the decals are installed with SOL (by Micro-scale), followed by one or more applications of SET (also by Micro-scale) ...or is it the other way around....SET and then SOL....and finally sealed with multiple coats of Future Floor Gloss. I like the glossy results but if I get tired of it, a coat of mate clearcoat can always be added, to tone down the numerous paintings done on the hull.
A few more pictures....
With the exception of the railing on each side and rear of the poop deck, the stern is pretty much complete.
At that stage, I need to now shift my focus and work, on the bow:
Yves
-
Fernando E reacted to James H in 1:25 Drakkar ‘Oseberg’ - Ships of Pavel Nikitin
1:25 Drakkar ‘Oseberg’
Ships of Pavel Nikitin
Catalogue # DROS002
Available direct for approximately £160 (7400 ₴) at time of writing
History
It is believed that the word “drakkar” originates from the Old Norse words “dreki” and “kar,” which mean “dragon” and “ship,” respectively. The warship acquired this name because the head of a dragon or another mythical creature (like Jormungandr) usually adorned the ship’s bow. The shape of the ship was also long and narrow, resembling a sea serpent. The Vikings constructed drakkars out of pine, oak, or ash wood. They used a special technique for splitting trees along the grain. They then watered the planks and held them above a fire to make them more flexible. The shipbuilders put the parts of the ship together with iron rivets and nails and bound them with cords and ropes. After that, they tarred the whole structure and caulked it by plugging holes and gaps and making the seams watertight. The sail was rectangular or square. It was made of sheep’s wool and covered with grease so that it didn’t get drenched. If there wasn’t a fair wind, the Vikings used oars – 20 to 35 pairs of them.
In the Viking age, few ships could compete with a drakkar in terms of sheer speed, but drakkars were also very nimble. Thanks to the drakkar’s shallow draft, the Northmen could easily sail along rivers and fjords. They could land in places that were very difficult to access and attack their enemies unexpectedly. These warships were also barely visible between the waves because of their low sides. This helped the Vikings catch their enemies unawares, even in the open sea. Drakkars were created for more than just war, however. They were solid and capacious, so the Vikings sometimes used them for trade and to transport goods, but more often these ships were used for sailing long distances. How far did the Vikings travel? They reached the shores of Iceland, Greenland, and North America, to name but a few destinations.
(Abridged from Vikings: War of Clans)
The kit
We’ve not exactly been awash with good kits of what we would call a typical Viking drakkar, or ‘longship’ as it’s more commonly known, despite the actual ancient translation. The Amati and Dusek are the kits which most come to mind. Pavel Nikitin’s new kit is also the largest in scale of this iconic vessel, weighing in at a whopping 1:25 scale! That equates to the following sizes:
Length: 865mm Width: 430mm Height: 480mm
Like the San Bartolome kit I recently looked at, the Drakkar is a second reworking, bringing a number of improvements over the original release, such as laser engraved ‘carved’ details on the bow and stern, including the ‘curls’ at each of those points. On other kits, this is where you would normally see such things as a dragon’s head, but this ship does not carry them, as per the actual recovered ship. I think in some respects, this was perhaps not as per a normal drakkar, but I could be wrong. The kit itself is packed into a slender but heavy corrugated box with a flap-opening lid depicting the finished model in all her glory, fitted with striped sail and 28 shields of varying décor. Inside the box, the various sheets are grouped into packages that are wrapped in cellophane, or ‘clingfilm’ as we know it in the UK. This keeps the sheets very tightly together. There are around 40 sheets of materials to build the drakkar. But that’s not all. Included with the ship is a very sturdy MDF jig which will most certainly aid those tasks that would otherwise be difficult, such as adding those clinker planks.
As with other Pavel kits, this one also includes a homemade MDF and acrylic parts box, with the part numbers clearly engraved on the sliding lid. This box includes different sizes of high-quality rope in differing sizes (no fuzz!), 3d-printed boss heads for the many shields, cleats etc.
The first task for the builder is to assemble the jig before then embarking on building the bulkheads. The bulkheads consist of a lower half into which a dovetailed upper half is fitted. The most outboard parts of each bulkhead are also separate parts. On the sheet, these are shown adjacent to their position on the uppers, with arrows depicting the location. This will add a little strength to the outer bulkheads, plus that change in grain direction at that point, will also help. There are also engravings on the completed bulkheads which denote where you need to pre-bevel the bulkheads prior to installation on the keel. The keel itself is a multipart assembly, with dovetail connection points.
The bulkheads will be installed to the keel, inverted upon the building jig, and here is where the hull will sit until fully planked.
A drakkar has a single mast and spar. These are provided as laser-cut/tapered parts that you will need to round off. Looking at the shape of these parts, then this is a welcome touch. Strips of dowel are also provided for the numerous oars. The paddles for these are pre-cut.
For display purposes, a stand is also included, as is an engraved plate with a serial number. The kit is 00009. I am informed that the timber for this kit is a combination of walnut, cherry, alder, and beech.
The instruction book is 28-page spiralbound A4 production with a protective plastic cover. The first part of the manual is text which relates to the numerous stages. Those stages are presented in drawing form in the second half of the manual. The drawings do appear to be nice and clear, and construction takes place over 68 stages. Inside the sleeve of the manual is a piece of laser-cut paper which contains three profiles which are designed to lay against the laminates that form the ‘fish’ or mast base. These are laid on at various stages and shaped to them.
One plastic sleeve contains three nicely printed plan sheets which show the drakkar in various profiles, and in rig etc. The second wallet contains a single printed piece of material for the sail. You will obviously need to cut and stitch this yourself. The photos show this brightly painted, but I’d read that these were usually quite dark as protected with tar due to the expense of the sails back in days of yore. I do admit that the painted sail looks beautiful, and I’d probably go with that. The size of the sail is really quite an indicator at the size of this model in a large 1:25.
Conclusion
From both appearance and materials, this kit stands head and shoulders above other contemporary kits of Viking drakkar, by a very wide margin. Being based on the Oseberg remains, she also appears to be the most accurate of all of them too. The timbers used in the kit are stated as imitating those of the real vessel, which may have been the case, but the ships themselves were coated in tar and would’ve been quite dark. I suppose the final choice would be for the modeller. I would probably go for the tarred look. In all, I’m seriously impressed with this kit and Pavel’s determination to improve what already looked like the best kit available for this subject. All the small touches like the 3D shield bosses and the highly detailed laser carvings instead of the usual white metal fayre, really sets this apart. If you’ve ever had a thing about Viking ships or just want to build something a little different, then I really recommend this new release.
*It was found that the kit had planks which were slightly too narrow to overlap properly. Pavel is now sending over replacement plank sets so I can eventually have a shot at building this lovely model kit.
My sincere thanks to Pavel Nikitin for sending this kit out for review on MSW. To buy directly, click the link at the top of this article.
-
-
Fernando E reacted to JamesBhm in HM Cutter Mermaid 1817 by JamesBhm - Modellers Shipyard - Scale 1:48 - first build
I won’t lie…the shrouds and deadeyes just about broke my will. Just a clear weak spot in my skill set. I almost took a hiatus from the build, but I promised Rick I’d get this done so we can both move on with our lives! I read up (and watched a video or two) on the wire jig technique for deadeye spacing, but it was just a struggle with everything moving, rotating, falling, etc. I finally ended up using a couple of tiny globs of polymer clay to help stabilize the wire jig while I got the shroud attached to the deadeye in the right orientation. If I had more of them (or two masts), I might explore some alternate jig engineering.
There was a little bit of a learning curve with the lanyards, but they weren’t as bad. My seizings are enough to cost a bosun his warrant, so I “tarred” them with a little flat black paint. I read on a post that someone liked lines and seizings of contrasting colors because they highlighted the detail. I’m definitely NOT looking to highlight my seizings just yet. I think I may also have a barely perceptible rake in my mast (to port, unfortunately…lol) Not really discernible unless you’re turning the model and scrutinizing carefully.
Also…not clear why the kit has the channels placed above the wale/wale trim with such long lanyards, when in King’s sketch, the channels are below the wale and the upper deadeyes are maybe just below the cap rail. My channels are below the wale. For my wire jigs, I spaced them exactly 3 deadeye widths apart and the upper deadeye height seems right (slight variations notwithstanding).
-
Fernando E reacted to DaveBaxt in HM Bark Endeavour 1758-61 by DaveBaxt - Caldercraft - 1:64
Lower Stays completed . I have fitted the Main & Fore lower Stays on top of the Preventer stays as per the Endeavour replica. Also Lees book states that a lot of small ships during this period carried the stays this way too. I think I will now adjust the tension on the lower shrouds before fitting the futtock shrouds and then the upper shrouds can be fitted before the upper stays and back stays are fitted. Here are a few more photos of the work so far. I also need to do a bit of work on the top masts and lower mast heads before the top masts are fitted.
-
Fernando E reacted to DaveBaxt in HM Bark Endeavour 1758-61 by DaveBaxt - Caldercraft - 1:64
I made a a start on the lower stays and preventer stays.I attempted to make the mouse using fabric sticking plaster over small wood bobbin pieces turned on a lathe.I then blacked these using Indian ink to ensure the pattern remaind I thought these turned out reasonably well but slightly on the large side. I also used thread supplied by Ropes of scale to get the correct size threads for 1:64 scale and sizes were taken from Lees book 'The masting and rigging of english ships of war'
Next up will be the top mast and their stays and shrouds. Once these are properly adjusted and the masts are in their correct positions, the long task of fitting their ratlines. Which is something I am not particularly looking forward to. Almost forgot the futtock shrouds so still got a long way to go.
-
Fernando E reacted to DaveBaxt in HM Bark Endeavour 1758-61 by DaveBaxt - Caldercraft - 1:64
Continuing the shrouds with only the Mizzen of the lower shrouds to do. Then onto the lower stays and back stays.
-
Fernando E reacted to Steve Anderson in HMS Victory c.1765-1791 by Steve Anderson - FINISHED - 1:64 scale
After installing four sets of guns I went ahead and finished off the forecastle fittings.
A closer look at the belfry. The ship's bell was turned on my Atlas lathe. The structure is painted in real gold leaf powder mixed with Damar varnish to a "whipping cream" thickness. Used on the ship carvings also.
Side note;
My wife's grandfather was an artisan/craftsman/sculptor at MGM Studios. He worked on many of the miniatures of the 1906 earthquake scenes for the movie "San Francisco", starring Clarke Gable. A lot of his work can also be seen in the interior of Grauman's Chinese Theatre. I was given the two full pint cans of Fuller gold leaf and bronze leaf that belonged to him. Also his naval bronze drafting set, sculpting tools, etc..
Amidships gun installation went much faster. The gangways were not in place until later, and no gunport doors were needed. At the quarter deck break guns and framing continued on to the stern. In the last picture you can get glimpse of the Admiral's dining and day cabin bulkheads. Sections of these were hinged to swing up to overhead when the ship was cleared for action.
All said and done, the long twelves were finished before Christmas, with time to spare. I had exceeded my expectations. I now went into full burner seven days a week, with a few exceptions, for a year.
The scary part... not to get in a rush and forget some important element.
Next Part 10 the Quarter Deck: Complex problem solving but fun.
-
Fernando E reacted to Nearshore in HMS Bellona by Nearshore - Corel - 1:100
Well, it has been a while since I've posted anything. I have not had much to post. I took a break from the Bellona and have not done anything with her since October 22. Have had lots of other projects to work on around the house. So, after reorganizing my modeling space, I started to fiddle around with where I left off in October. I completed most of the planking on the wales and have started to line off the hull for the first layer of planks. I cut out the false ports for the cannons and squared them off. I laid out the bearding and rabbet lines and carved them out. I have begun laying out and installing the temporary battens for lining out the hull planking. I installed the temporary garboard planks, and I am using them for my initial measurements. I pinned the battens in place but am not happy with the way they line up. I have redone one side and took a pic to show what looks to me as the right alignment verse the wrong alignment. The planks on the left are lining up the way I think they should lay. The planks on the right look to be a problem waiting to happen. Anyway, that's where I am at right now on the Ballona. I will post another update when I actually start installing the first layer. I will also provide a pic of the temporary battens once they are all lined up properly and pinned down.
Cheers!!
-
Fernando E reacted to AKRYPTO in HMAS AUSTRALIA II by AKRYPTO - FINISHED - 1:72 - PLASTIC - Tribute build.
So met with Bill Harris of Temora Gunnery rate HMAS Australia 39-45 Yankee turret then a couple of days later met up with Bruce crowl of lakes entrance both 98 years old and sharply dressed strong and healthy telling war stories like it was yesterday, you could Smell the cordite in their stories, both very proud Veterans
-
Fernando E reacted to DaveBaxt in HM Bark Endeavour 1758-61 by DaveBaxt - Caldercraft - 1:64
Moving on to the Fore lower mast shrouds using 0.75mm black thread . I made a jig for each shroud port and stbd as I found this method kept the upper dead eyes a the same hieght rather than the traditional brass wire which did not work to well on my last model. There are signs of one or two lower dead eye securing wire come loose and have always found this a problem of the upper chain plates. I will have to try something better on my next ship.
-
Fernando E reacted to yvesvidal in HMS Bellona by yvesvidal - CAF Model - 1:48
The poop of the ship is almost completed:
Lots of small details went into it. The assembly is done bottom to top, starting with the rear balcony:
First, the foot space rail is glued all around the platform (above). The curve is obtained after soaking it in the alcohol and bending carefully with some heat. To prevent the decorative railing from going in all directions, I have placed five tiny strips of wood, to retain it. These helps immensely the positioning and gluing of that delicate and wild resin part:
Gluing is done carefully, one side at a time, using slow curing CA glue, to keep a hand in the position of that delicate and reluctant part.
The breast rail is then placed and that strengthen considerably the railing, overall. The breat rail is treated with some oil, to give it that nice dark and deep color.
Next is the complex assembly of the taffrail going on top of the stern. This part is a royal pain in the **** as we need to bend cherry wood (which is never easy). The taffrail is made of three layers of strips to be glued with two curved planes. Not an easy thing to do. Again, CA glue is your best friend.
A little bit of paint:
We can move on with the decorative gold leafed parts on the stern. All parts are fist painted matte black (Tamiya) and then airbrushed with Gold Leaf (Tamiya). All the parts are made of resin.
The first part to be positioned is the "necking of the taffrail" if I am not mistaken.
Then we assemble the pilasters on each side of the rear windows. And we can then place all the decorative sculptures, munnions and carvings.
Overall view of the PORT side:
Of course, I still have to do the starboard side: It looks quite bare in comparison.....
That's all for today, folks.
Yves
-
Fernando E reacted to JamesBhm in HM Cutter Mermaid 1817 by JamesBhm - Modellers Shipyard - Scale 1:48 - first build
I think I have blocks and attachments done for masts and spars. My knots and seizings are still a little awkward and inconsistent, but it’s a first model and there’s a learning curve developing. As I had mentioned before, I repurposed the upper yard dowel to make studdingsail booms. I ended up using a method that is a hybrid between the kit instructions and Chuck Passasro’s article on yard details. I tried using the 28 guage wire he recommends, but realized it was wrong for the scale of the model (and ended up breaking it from metal fatigue as I fiddled with it). The studdingsail boom irons are painted strips of thick artist’s watercolor paper. The booms are attached to the yard with bent, cut, and painted brass pins (I have some that are a bit thinner and more malleable than the ones that came with the kit). The stirrups are brass pins with a (somewhat) more natural loop in the end, a faux seizing with rigging cord, and painted flat black. All in all, a good skill building experience, but I can’t imagine repeating this process for multiple yards/masts!
-
Fernando E reacted to Penfold in HMS Beagle by Penfold - OcCre - 1/60
So here’s how the little boats are coming along. Some still need a little varnish and the block and tackles but they’re pretty much there.
-
Fernando E reacted to yvesvidal in HMS Bellona by yvesvidal - CAF Model - 1:48
Wow, times flies. It has been a month already.
I have not worked much and was distracted by various things. However, I managed to make some progress on the Port side of the hull:
There are quite a few decals to install, after finishing all the woodwork with various small strips of wood (not provided in the kit). I debated using the 2 x 3 mm strips (included in the kit) and decided against them, as they are too large and too thick for some of the wood rails. Instead I went with 1.5 x 1 mm strips.
The decals are placed using MICROSCALE SET and SOL chemicals. Then, a couple of coats of Future Floor is brushed to seal the decals and to protect them from handling.
The surface is treated with Future Floor before applying the decals, since we need to have a glossy surface for optimal adhesion of the decals. Above, the Forecastle railing has almost been completed on the port side. I will work on the bow, before finishing the railing in the front.
The small pounder guns have been completed. A total of 70 guns were put together: it was quite tedious and there is no room for mistakes or losses. In fact, CAF Model does not provide a single spare parts for these guns: 280 wheels, 140 axles, 70 brass barrels and numerous other parts with absolutely zero spare parts. If you loose a wheel, you are on your own. If you break an axle while sanding them to make them fit into the wheels, you are on your own again. It is regrettable that on such kit, there is no room for errors.
Yves
-
Fernando E reacted to yvesvidal in HMS Bellona by yvesvidal - CAF Model - 1:48
So after a few weeks of work, the port side is pretty much completed. I still have some wood joinery to do and correct some painting mishaps, as well as installing the 18 gun port lids that are still missing.
The upper gun port lids have been built and installed: what a royal pain in the ****, to build them and install them correctly.
Overall view of the Port side of Bellona:
Now, the same has to be done on the starboard side..... Wish me luck !!!
Yves
-
Fernando E reacted to Penfold in HMS Beagle by Penfold - OcCre - 1/60
Been a while since I posted… I’ve been procrastinating and putting off attaching the rudder by doing the Little boats and other bits for the main deck (I’ll post some pics later)
I’d also managed the brasswork on the stern and painted it.
So…. The rudder then!
I have fed so many tiny bits of brass nail to the carpet monster today 😔 and managed to break the rudder twice in the process, but for a first time fitting a rudder this way, I’m happy enough!
I don’t really get the brass wire work at the stern or what it’s supposed to represent, but it’s what the instructions say, and mine looks pretty close to the pics on the instructions.
The gardens went in OK but needed some putty to fill underneath as the hull shape doesn’t really match the flatness of the die cast pieces. I also used putty to fill in the brass wire before painting. ( I Know… some touching up needed).
-
Fernando E reacted to DaveBaxt in HM Bark Endeavour 1758-61 by DaveBaxt - Caldercraft - 1:64
Prior to the fitting of the mast shrouds and after consulting Lees book 'The Masting and Rigging of ships of war 1625 to1860' on smaller ships there is only one pair of Pendant tackle per lower mast and one per of Burton pendants for the mizzen were fitted. The Pendant tackle having a single block on each end and an eye spliced at the top . According to lees the pendant tackle for the Endeavour period is fitted similar to Swifter and has single rope spliced at the top end and one for each side. Hope this makes sense. Both Burton pendant and pendant tackle are fully served . The runners for the tackle are not normally fitted on model, however there will be main stay tackle to fit at a later day for hoisting boats etc.
-
Fernando E reacted to DaveBaxt in HM Bark Endeavour 1758-61 by DaveBaxt - Caldercraft - 1:64
Completed Bobstays and horses .Hopefully better photos this time as I have managed to figure out my camera/phone.
Also I have added in the collar with closed heart for main preventer stay attached to lower fore mast also fully served as fore preventer stay collar. Next up moving onto the Mizzen stay collar which is atthached to the main lower mast and according to lees measurements about 28mm up from the deck and is a dead eye until a later date and will go with this. Also there is no preventer stay on the mizzen mast until a later date so will be going with that too I also need to find out which blocks /hearts are attached to the lower mast for the top mast stays before starting on the shrouds and whilst I have sufficient room a big mistake I made whilst building the Bounty. No doubt I will forget something.