-
Posts
883 -
Joined
-
Last visited
About robert952
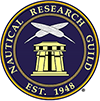
- Birthday 09/27/1952
Profile Information
-
Gender
Male
-
Location
Aberdeen, North Carolina, USA
-
Interests
American Civil War era ironclads, small work boats, nautical history. Other: 3D CGI (still images) and too much game playing on the PC.
Recent Profile Visitors
-
robert952 reacted to a post in a topic: Calypso by mandolinut - Billing Boats - 1:45
-
robert952 reacted to a post in a topic: Calypso by mandolinut - Billing Boats - 1:45
-
robert952 reacted to a post in a topic: Calypso by mandolinut - Billing Boats - 1:45
-
robert952 reacted to a post in a topic: Calypso by mandolinut - Billing Boats - 1:45
-
robert952 reacted to a post in a topic: Calypso by mandolinut - Billing Boats - 1:45
-
robert952 reacted to a post in a topic: Calypso by mandolinut - Billing Boats - 1:45
-
robert952 reacted to a post in a topic: Calypso by mandolinut - Billing Boats - 1:45
-
robert952 reacted to a post in a topic: Calypso by mandolinut - Billing Boats - 1:45
-
robert952 reacted to a post in a topic: Calypso by mandolinut - Billing Boats - 1:45
-
robert952 reacted to a post in a topic: Calypso by mandolinut - Billing Boats - 1:45
-
robert952 started following First attempt at rope making , Calypso by mandolinut - Billing Boats - 1:45 , Chesapeake Bay Crabbing Skiff by palmerit - Midwest Products - 1:20 and 4 others
-
Paul Le Wol reacted to a post in a topic: Muscongus Bay Lobster Smack by JacquesCousteau - Model Shipways - 1:32 - Rescaled and Modified
-
JacquesCousteau reacted to a post in a topic: Muscongus Bay Lobster Smack by JacquesCousteau - Model Shipways - 1:32 - Rescaled and Modified
-
Keith Black reacted to a post in a topic: Muscongus Bay Lobster Smack by JacquesCousteau - Model Shipways - 1:32 - Rescaled and Modified
-
Baker reacted to a post in a topic: Golden Hind by Rock_From_Korea - 1:48
-
Desertanimal reacted to a post in a topic: 18th Century Longboat by Desertanimal - Model Shipways - 1:48
-
Thanks for the detailed log. You have a great build here with this gem.
- 86 replies
-
- Model Shipways
- Norwegian Sailing Pram
- (and 3 more)
-
First, thanks for the build log and details. Great progress and commentary. One of the great things about these build logs comes from seeing different aspects of the modeler's setup. For example, they're workbench setup. I looked again at your paint booth set up (post 73 edited June 5). The hose goes into a bucket in what looks like a piece of filter paper. Is that correct? Do you have a top for the bucket with a center hole for the vent and some smaller holes in the top, hence the dark spots that we see? The filter would cover the holes, it appears. I am looking at a similar set up since the temperature in my garage varies so much (like up to 100 degrees this week) and I need to bring my painting operation into a more controlled environment. Thanks for taking a side trip in your build to answer these questions.
-
Nice model. Superbly executed.
- 34 replies
-
- muscongus bay lobster smack
- Model Shipways
-
(and 1 more)
Tagged with:
-
Welcome to the wooden side of modeling. Looking good. Following along to watch the progress.
- 33 replies
-
- Model Shipways
- 18th Century Armed Longboat
-
(and 1 more)
Tagged with:
-
Looks good! Thanks for sharing your adventure of this build.
- 53 replies
-
- norwegian sailing pram
- model shipways
-
(and 1 more)
Tagged with:
-
I keep forgetting to mention this. Olha Batchvarov is posting a complete video build log on this model. Recent post is number 32 from a day ago. I 'scanned' (as in fast forwarded through) a couple of them. Look great. Not sure what the colaboration efforts were but Model Expo ran a deal (aren't they always?) on the model and promoting her doing the video log. Most of the videos are 2 hours (one is over 3). Easy to search for since not a lot of YouTubers post 'Muscongus Bay build' for the subject. (A lot of videos to look through if you go the her YouTube channel.) Definitely in my notes to review more when I dig down into my stash and work on this model.
About us
Modelshipworld - Advancing Ship Modeling through Research
SSL Secured
Your security is important for us so this Website is SSL-Secured
NRG Mailing Address
Nautical Research Guild
237 South Lincoln Street
Westmont IL, 60559-1917
Model Ship World ® and the MSW logo are Registered Trademarks, and belong to the Nautical Research Guild (United States Patent and Trademark Office: No. 6,929,264 & No. 6,929,274, registered Dec. 20, 2022)
Helpful Links
About the NRG
If you enjoy building ship models that are historically accurate as well as beautiful, then The Nautical Research Guild (NRG) is just right for you.
The Guild is a non-profit educational organization whose mission is to “Advance Ship Modeling Through Research”. We provide support to our members in their efforts to raise the quality of their model ships.
The Nautical Research Guild has published our world-renowned quarterly magazine, The Nautical Research Journal, since 1955. The pages of the Journal are full of articles by accomplished ship modelers who show you how they create those exquisite details on their models, and by maritime historians who show you the correct details to build. The Journal is available in both print and digital editions. Go to the NRG web site (www.thenrg.org) to download a complimentary digital copy of the Journal. The NRG also publishes plan sets, books and compilations of back issues of the Journal and the former Ships in Scale and Model Ship Builder magazines.