-
Posts
130 -
Joined
-
Last visited
About MAGIC's Craig
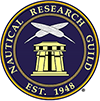
- Birthday 02/14/1949
Profile Information
-
Gender
Male
-
Location
Los Osos, CA
-
Interests
Yacht design, sailing, model-making, recumbent trikes and velomobiles
Recent Profile Visitors
-
MAGIC's Craig reacted to a post in a topic: Steam Schooner Wapama 1915 by Paul Le Wol - Scale 1/72 = From Plans Drawn By Don Birkholtz Sr.
-
MAGIC's Craig reacted to a post in a topic: Steam Schooner Wapama 1915 by Paul Le Wol - Scale 1/72 = From Plans Drawn By Don Birkholtz Sr.
-
Keith Black reacted to a post in a topic: TWILIGHT 2007-2009 by MAGIC's Craig - Scale 1:16 - RADIO - Pacific Northwest cruising powerboat
-
MAGIC's Craig reacted to a post in a topic: Cutter Luisito by GioMun - 1/48 - A small cutter built to survive a shipwreck in southern seas
-
MAGIC's Craig reacted to a post in a topic: NORDKAP 476 by _SalD_ - Billing Boats - 1:50 - RADIO
-
MAGIC's Craig reacted to a post in a topic: TWILIGHT 2007-2009 by MAGIC's Craig - Scale 1:16 - RADIO - Pacific Northwest cruising powerboat
-
Keith Black reacted to a post in a topic: TWILIGHT 2007-2009 by MAGIC's Craig - Scale 1:16 - RADIO - Pacific Northwest cruising powerboat
-
MAGIC's Craig reacted to a post in a topic: Sternwheeler From the Susquehanna River's Hard Coal Navy by Keith Black - 1:120 Scale
-
Welcome aboard, James! Thank you for the compliments and I am (of course) delighted that TWILIGHT has appealed to your eyes as a worthwhile model to build. As you may have noted by the dates of the postings, I tend to update the build log on a more or less monthly basis, but please feel free to drop by anytime. Craig
-
Jimbo1963 reacted to a post in a topic: TWILIGHT 2007-2009 by MAGIC's Craig - Scale 1:16 - RADIO - Pacific Northwest cruising powerboat
-
Jimbo1963 reacted to a post in a topic: TWILIGHT 2007-2009 by MAGIC's Craig - Scale 1:16 - RADIO - Pacific Northwest cruising powerboat
-
Jimbo1963 reacted to a post in a topic: TWILIGHT 2007-2009 by MAGIC's Craig - Scale 1:16 - RADIO - Pacific Northwest cruising powerboat
-
Jimbo1963 reacted to a post in a topic: TWILIGHT 2007-2009 by MAGIC's Craig - Scale 1:16 - RADIO - Pacific Northwest cruising powerboat
-
Jimbo1963 reacted to a post in a topic: TWILIGHT 2007-2009 by MAGIC's Craig - Scale 1:16 - RADIO - Pacific Northwest cruising powerboat
-
Jimbo1963 reacted to a post in a topic: TWILIGHT 2007-2009 by MAGIC's Craig - Scale 1:16 - RADIO - Pacific Northwest cruising powerboat
-
Jimbo1963 reacted to a post in a topic: TWILIGHT 2007-2009 by MAGIC's Craig - Scale 1:16 - RADIO - Pacific Northwest cruising powerboat
-
Jimbo1963 reacted to a post in a topic: TWILIGHT 2007-2009 by MAGIC's Craig - Scale 1:16 - RADIO - Pacific Northwest cruising powerboat
-
MAGIC's Craig reacted to a post in a topic: Loreley 1884 by Ilhan Gokcay - 1/75 - Scale Steam Yacht
-
MAGIC's Craig reacted to a post in a topic: USS Cape (MSI-2) by Dr PR - 1:48 - Inshore Minesweeper
-
MAGIC's Craig reacted to a post in a topic: Sternwheeler From the Susquehanna River's Hard Coal Navy by Keith Black - 1:120 Scale
-
MAGIC's Craig reacted to a post in a topic: Sternwheeler From the Susquehanna River's Hard Coal Navy by Keith Black - 1:120 Scale
-
Ah ha! I must be doing something right, then! These are dream ships in their own ways. The late Bill Garden in his senior years, would carve 4 identical half hulls, complete with cockpits and cabin shapes. He would then send 3 of them off to some of his far-away close friends and on some cold, wet winter night, the 4 of these geezers would hook up on a group-call to share their impressions of how those craft would sound...and sail or motor... and then come to an anchor in a sheltered cove while the winds overhead rattled the branches in nearby trees. They would hoist a tot to each other and their long friendships. If one's time at sea has passed, this is a fine way to still dream yourself aboard. Thank you for your compliments and the tips, Keith.
-
August 18, 2025 update: The handrails for the ladder up to the roof deck were bent and fitted to the ladder which was then positioned on the aft deck. The mast installation began with the layout for the mast support beam. This structure was built up as a hollow box beam spanning the width of the main cabin top. A soldered brass mast step was fabricated to hold the base of the mast and after being filed smooth, was painted and installed on the support beam. Fittings were also fabricated to fit the ends of the support beam to provide pivots for a pair of boat booms, port and starboard. The mast was tapered and then rounded from spruce square stock. The round forebraces to the top of the mast were fashioned from birch dowel stock as well as was the necessary bracing for the radar mount. A kind friend printed up a set of water-slide decals for TWILIGHT's name placements. Fortunately, he made spares because I had to go "back to school" on how to properly install and seal the slippery critters. After they were thoroughly dry, they were (later) sprayed with flat, clear acrylic to better blend them in to the existing paint job. The upper "Maneuvering Station" pedestal and a searchlight were installed atop the pilothouse. A pair of pivoting boat booms were made from spruce square stock, tapered and rounded. Goosenecks were soldered for the forward(inboard) ends and brass sleeves were positioned on the aft ends of the booms for later rigging connections. The boom crutches were bent from 1/16" rod and padded with split pieces of black wire insulation. The basis for the elliptical-shaped funnel supporting the exhaust stacks was laminated from small pieces of AYC, then band-sawed to a close tolerance. Once sanded to the final section shape, a piece of AYC was cut to tightly fit around the top of the funnel and this was beveled to give the desired upper flange shape. The shaped funnel was placed on top of the removable main cabin top hatch to check clearances whenever the hatch was to be lifted clear in order to avoid future conflict with the mast's fore-braces. Card was used to create the two portions of the deck flange for the funnel. Suitable sized pieces of brass tubing were beveled and then soldered together to represent the tubes of the dry exhausts exiting up through the funnel. These tubes were glued into the funnel after also checking that they would not hinder the hatch removal (and in the real world, not send the diesel exhaust directly up into the bottom of the radar). A non-skid "grating" was glued together and the bottom beveled to level out the slope of the pilothouse roof in order to provide secure footing whenever the "maneuvering station" was to be utilized. A brass safety railing was soldered together and bent to the necessary shape for security on top of the pilothouse. (I see that I will have to go back to slightly torque the alignment of the steering pedestal.) A "hinged" hatch cover above the access ladder to the roof decks was the next item on my list. This was glued up from 1/16" birch ply and trimmed with mahogany to match the hatch coaming. I decided that it would be mounted in the braced open position. Joinery "cabinets" have been constructed to contain the 3 VDC and 6 VDC battery holders out of sight in the pilothouse and the main cabin. And that will bring us current. As with nearly all boats, there remains a list of projects/tasks yet to be completed. My heartfelt thanks to you for your all of your suggestions, support (and patience). My best to you all, Craig
-
Jacques: This build has been a delight to follow and I have particularly enjoyed your explorations of the methods to secure the mainsail to the spars. One tiny point I would raise because of our own gaff cutter experiences is that the throat of the sail at the gaff (sometimes referred to as the "knock") will have a strong tendency in a breeze to want to sag away from the mast and move a bit up along the underside of the gaff if there is any slack in the throat halyard. Because of the taper to the gaff jaws, the line around the jaws would tend to slide aft and loosen a bit. This is the reason that some method of attaching a piece of line from the throat of the sail to well forward , either to an upper mast hoop or to thumb cleat on the underside of the gaff (or sometimes through holes going up through the gaff jaws) helped and was also simple. Do any of your photos show a method of keeping the throat of the sail forward toward the mast? I noted that on the enlargement of this photo: https://www.memoriasdelsigloxx.cl/601/w3-article-86076.html There appear to be one or maybe two lines involved at the throat. Unfortunately, I do not have a good image from our boat of that area. Craig
- 312 replies
-
- Chile
- Latin America
-
(and 6 more)
Tagged with:
-
Good morning, Gary: I do not think that I would have had it in me to have had to go back to start over. No, wait. Then I could have perhaps avoided some of the goofs I built into her... I am delighted that she is still here, teaching me new techniques as well as patience. Thanks for the compliment, Craig
-
Okay - Final segment to bring the log current is as follows: Brass foredeck handrails were soldered together from rod stock, laid over a developed pattern for alignment. I cobbled up a wooden bending jig in an effort to keep the bends smooth and the upright posts were coved to fit tightly to the underside of the long rails. The lower ends of the supporting posts were fitted into holes drilled in the forward caprail. These handrails were deliberately made stouter than scale might require in anticipation of possible rough handling when launching or retrieving TWILIGHT from the water on her working days. And, as you will notice, somewhen about this point, the cabin tops got painted. The aft overhang of the main cabin roof was intended to be supported on a pair of main deck-mounted upright posts, which were also braced to the aft face of the after cabin. The assembly of these posts took a couple of tries to get the fussy soldering to cooperate, but with guidance from Ken Forem's book, the task was ultimately accomplished. The port and starboard running light mounts were glued up from basswood (and the outboard faces painted black). The light fixtures are outfitted with the appropriate colored LED's and the assemblies were then affixed onto the permanently mounted after portion of the pilothouse, with wires fed down and inboard in small holes into the upper corners of the house. While the forward removable portion of the pilothouse was lifted away, a mahogany and AYC vertical "trunk" was fashioned (in the location where the originally planned dry exhaust stack for the Gardiner diesel would have risen through the main cabin. The trunk permits necessary wires for the various R/C switches to be led to the pilothouse roof for convenient shoreside access. Before securing the main cabin roof to the house, the necessary preliminary (hopefully unobtrusive) wiring runs for the stern light and some interior lights needed to be developed. Additionally, a change in location of the ladder access to the cabin and pilothouse roofs was made from that drawn on the original drawings. The ladder was moved from a position partially obstructing the helm's view to a location at the aft end of the boat. A rectangular access hole was cut through the main house roof with my usual method and then faced with mahogany trim. Also visible are: the stern light and flag pole socket, the black-capped top of the (hydraulic) warping capstan and a stout double "H" bitt for the occasional towing opportunities/requirements which might well arise. The access ladder has been fabricated ( for the fun of it) from hollow rectangular brass stock, 3/32" dia. tube rungs and closely fitting brass brads. It does still need a pair of handrails for safety before installation. The final 4 photos of this segment will bring us current with TWILIGHT's build to date (7/7/25). A fair amount of work remains to be done above the roofs as well as with the finalizing of the topside R/C mountings. I am also hoping to to build the main cabin joinery as removable modules later this year. Until again, my heartfelt thanks to all of you for following along with the progress of this build. Your comments and suggestions are appreciated and always welcome. Craig
-
Part the next: Back to working on the roof panels. A laminating form was fashioned from scrap blocks to provide clamping positions when steaming and laminating the 1/16" thick basswood layers which formed the main cabin top fascia trim. The cured, slightly over-height fascia was glued and nailed to the outside vertical edge of the cabin top roof. After the glue hardened, the upper and lower edges were then planed to the desired profiles in elevation. Margin pieces (covering boards) were then glued to the cabin top surface, overhanging the flush roof-to-fascia seam. The outer edges of these covering boards were fair flush with the outer face of the fascia and the upper corners rounded off. The pilothouse roof was built up in a similar manner. An access hatch down through the main cabin was necessary and was cut out by first drilling #55 vertical holes at each corner, then scoring the upper and lower skins with a sharp scalpel. I used the fine teeth at the tip of a small pull saw, riding in the scored lines and braced by clamped-on guides to cut through the skins into the spaces between the interior pairs of carlins and beams. The piece of roof removed was then slightly smoothed up and given upper flanges to serve as the hatch body. The heads of the Anchorfast copper boat nails, which were used to pin the fascias to edges of the roofs, had been set flush and they were now covered by the installation of glued half-round bead trims. These trims will ultimately be painted a contrasting color. A forward-projecting "brim" was carefully shaped to attach to the lower edge of the pilothouse fascia, supported by small knees. A 1/32" x 1/32" mahogany strip was smoothed to a half-round shape and glued to upper side of the brim at its lower edge to serve as reinforcement. The extent of the deck areas which would receive a non-skid treatment could now be discerned and the finicky task of masking off the rest of the nearby surfaces followed. After experimenting with a variety of compounds, the best results (to my eyes) at this scale was developed by stippling on this pumice gel. When dried, the the non-skid was given a coat of the Tamiya (AS-26) Light Ghost Grey, which has been used for the majority of the topsides painting. The taffrail was scarfed together from suitable thickness teak stock, using card patterns to define the segments. The glued-up taffrail was mounted atop 1/8" diameter brass tube segments and secured in place with 3/4" long Anchorfast nails driven into pilot holes drilled in the main rail below. Temporary spaces blocks were taped between the two rails to help maintain the 1/2" high rail separation. The heads of the nails were slightly countersunk and later filled with colored epoxy. Once this was faired smooth, Vicky began brushing on varnish to protect the taffrail. ************* I will again pause the log at this point to keep the number of pictures in this segment reasonable. The final segment which will bring us current will be added soon. Craig
About us
Modelshipworld - Advancing Ship Modeling through Research
SSL Secured
Your security is important for us so this Website is SSL-Secured
NRG Mailing Address
Nautical Research Guild
237 South Lincoln Street
Westmont IL, 60559-1917
Model Ship World ® and the MSW logo are Registered Trademarks, and belong to the Nautical Research Guild (United States Patent and Trademark Office: No. 6,929,264 & No. 6,929,274, registered Dec. 20, 2022)
Helpful Links
About the NRG
If you enjoy building ship models that are historically accurate as well as beautiful, then The Nautical Research Guild (NRG) is just right for you.
The Guild is a non-profit educational organization whose mission is to “Advance Ship Modeling Through Research”. We provide support to our members in their efforts to raise the quality of their model ships.
The Nautical Research Guild has published our world-renowned quarterly magazine, The Nautical Research Journal, since 1955. The pages of the Journal are full of articles by accomplished ship modelers who show you how they create those exquisite details on their models, and by maritime historians who show you the correct details to build. The Journal is available in both print and digital editions. Go to the NRG web site (www.thenrg.org) to download a complimentary digital copy of the Journal. The NRG also publishes plan sets, books and compilations of back issues of the Journal and the former Ships in Scale and Model Ship Builder magazines.