-
Posts
1,376 -
Joined
-
Last visited
About Snug Harbor Johnny
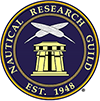
Profile Information
-
Gender
Male
-
Location
Southeastern Pennsylvania
-
Interests
history, craft projects
Recent Profile Visitors
The recent visitors block is disabled and is not being shown to other users.
-
Ryland Craze reacted to a post in a topic: Planking precision and wood filler
-
Paul Le Wol reacted to a post in a topic: Planking precision and wood filler
-
Snug Harbor Johnny reacted to a post in a topic: Golden Hind by Rock_From_Korea - 1:48
-
PVA craft glue is used in book binding where some flexibility is desired, e.g. the spine of the book. I tried it experimentally when 'layer caking' a solid basswood hull (from pieces pre-cut along plan view lines), and occasional glue-rich (yet cured) seams didn't sand as well as those glued with wood glue (aka Titebond - aliphatic resin, which dries hard). I've had good results from wood glue, quick set epoxy, and CA on wood-to-wood bonding or wood over filler. PVA can work when gluing wood decking over a plastic substrate, but this is a special application.
-
robert952 reacted to a post in a topic: First attempt at rope making
-
Snug Harbor Johnny reacted to a post in a topic: Mary Rose by Baker - scale 1/50 - "Your Noblest Shippe"
-
Snug Harbor Johnny reacted to a post in a topic: Cutty Sark by petervisser - Billing Boats - Scale 1:75
-
Snug Harbor Johnny reacted to a post in a topic: Staghound 1850 by rwiederrich - 1/96 - Extreme Clipper
-
ClipperFan reacted to a post in a topic: Staghound 1850 by rwiederrich - 1/96 - Extreme Clipper
-
Siggi52 reacted to a post in a topic: The Gokstad Ship 900 AD by Siggi52 - FINISHED - 1:50
-
Mr Whippy reacted to a post in a topic: Great Harry (Henry Grace A Dieu) by Robert Hamlin - Sergal - Scale ~1:64 - KIT RESTORATION
-
Snug Harbor Johnny reacted to a post in a topic: The Gokstad Ship 900 AD by Siggi52 - FINISHED - 1:50
-
GrandpaPhil reacted to a post in a topic: Great Harry (Henry Grace A Dieu) by Robert Hamlin - Sergal - Scale ~1:64 - KIT RESTORATION
-
Snug Harbor Johnny reacted to a post in a topic: Oryol 1902 by GrandpaPhil - Orel - 1/200 - CARD - Russian Battleship
-
sheepsail reacted to a post in a topic: Great Harry (Henry Grace A Dieu) by Robert Hamlin - Sergal - Scale ~1:64 - KIT RESTORATION
-
Fair points - and unless a well-funded effort to recover every possible scrap of surviving wreck can be done at some future time, we may never know the entire story. The CSS Alabama had a 'lucky shot' that lodged in the rudder post of the USS Kearsarge ... but 'unluckily' failed to explode. Imagine the outcome had the round gone off. History is full of 'what ifs'. With the Mary Rose, we're still short of evidence. And as the parents of most teenagers learn, "The absence of evidence is not evidence of abstinence. "
- 12 replies
-
- Great Harry
- Henry Grace a Dieu
-
(and 2 more)
Tagged with:
-
thibaultron reacted to a post in a topic: Dremel 4 inch table saw 588-2
-
Scrumpymanjack reacted to a post in a topic: Hi - first post here
-
Hi - first post here
Snug Harbor Johnny replied to Scrumpymanjack's topic in New member Introductions
'Looks like this would be a GREAT model to gently restore, and a good way to get some experience with rigging without first having to build a hull and outfit the deck. The paper flags have deteriorated, so you could re-create them. The rigging might also be on the weak side, so replacement with scale rope from Siren or Ropes of Scale can insure a long future life for the model. Take pictures so you can replace existing rigging the same way. There are fife rails near the base of the masts, but you can also add a few pin rails inside the bulwarks if you opt to add additional lines. The yards are tied to the masts, so that can be re-done, or you can opt to add yokes/parrels and add halyards. The sails can be replaced (if fragile) by finer material. Once the yards and rigging are cleared (the masts can be left in place if they won't pull out), dusting and perhaps a few touch ups will freshen the hull and deck. Then re-assemble and think about a case to limit future dust accumulation. Fair sailing !! Johnny -
Dremel 4 inch table saw 588-2
Snug Harbor Johnny replied to lynne's topic in Modeling tools and Workshop Equipment
Someone with access to a lathe and metal stock could turn their own pulleys to suit whatever non-toothed belt they have that will deliver approximately the same blade speed. -
Dremel 4 inch table saw 588-2
Snug Harbor Johnny replied to lynne's topic in Modeling tools and Workshop Equipment
With parts missing, can the condition be "great"? -
Now that you've stained the strakes, Pavel's scarf joints mostly 'disappear'. The finish on everything looks great !
- 52 replies
-
- Oseberg
- Pavel Nikitin
-
(and 1 more)
Tagged with:
-
One can use 'natural', but I still think it seems vey light - and may 'read' nearly white in photographs. Brand new full-size rope starts out on the light side, but it doesn't take long under use to darken into a medium tan. Builders can used their own judgement, as the whole point is to please oneself with any build.
-
Of course, it is white thread (the only kind I've seen), so the resultant scale rope will have to be dyed to the desired color. The classic linen fishing line was also white, but vintage examples are now slightly off-white. White rigging on model ships just doesn't look right anyway. Standing rigging should be either black or a very dark brown - that includes the lacing for the deadeyes and ratlines. Running rigging should be tan - but not too light or it looks "whitish" in photographs.
-
When using polyester thread, the scale rope made can have a tendency to unravel when cut. Baking (and note that this for a limited time at a moderate temperature 5 - 7 min at 300 deg. F ... to avoid melting) seems to 'set' the rope better and the raveling is far less. Cotton (or linen) scale rope can ravel also, but does not need heat setting. Cotton can weaken over decades, and that used on my Dad's clipper crumbled after 70 years. Heat, pollutants and UV exposure will affect this - as well as for many materials. No doubt, making scale rope from multiple cotton strands should be more durable - but linen is better a s natural material. The old-timers used linen fly fishing line (known as Old Cuttyhunk) and linen does stand the 'test of time' for rigging as well as sails. The indications are the Polyester scale rope will also hold up over the decades. BTW for either scale rope making or with full size rope (and I've demoed making some of that), one first spins the rope - and the trick is to balance the number of turns v/s counter turns in step one and step 2 of the process. If you've done that, the rope won't 'kink up' on itself. If nearly in balance, the rope will only kink slightly. The solution is to 'whip' the rope around so that it will get rid of any excess counter-twist. Then with one end fixed to something or restrained as convenient, you pull on the run (not too hard) to get the twist to meld to itself better. Stretching a few times will give a little more length and reduce the tendency to ravel when cut. The poly gets heat-set as noted above. Those who don't want to make their own can buy good scale rope from Syren or Ropes of Scale, as scale rope is far better than what is supplied in most kits. You'll notice that kit rope has a lot of 'fuzz' in close up shots. Poly has the least fuzz. Cotton rope will have some fuzz, but then what I've made from cotton has been QUICKLY passthrough a (relatively) low temp flame of an old-fashioned alcohol burner. This 'singes' off most of the fuzz, but if you don't move the scale rope fast enough - the line will catch fire and part. DON'T do this with polyester scale rope. Old linen fly fishing line doesn't have much fuzz because of the long fibers (cotton is short fibered), but it is VERY hard to find, since it was not made since the 1940s - and because some people collect spools of it, Old Cuttyhunk is very expensive. The rope size is also larger - for 1:48 scale models.
-
Your rig is similar to Syren's Rope Rocket - the videos on scale rope making on the Syren website are very instructive. The consensus is the Guterman poly sewing thread makes the best rope (oven 'set' 5 -7 minutes in a 300 degree F oven after winding and stretching), with Mettler a close second. I've used both, and the standard sewing thread has been available in sewing retailers (those that have not closed) or on line. Its best to buy in person to judge the color. The thread is aprox .006" in diameter, and using a single thread on the rig set up for three strand rope yields scale rope about .010 in diameter - that represents 1" rope at 1:100 scale (or thereabouts). Using 2 threads on each of the 3 strand setup (6 threads in all) yields scale rope about .020 in diameter. 3 treads on each of the 3 strands to wind (as I recall) yields closer to .030 scale rope. By experimenting (e.g. first making .010 rope and using THAT on each of a 3 strand set up - mind how the twist runs - can make thicker rope for larger scales). You get to control the product as needed.
-
Glad to have you aboard, mate! Johnny
About us
Modelshipworld - Advancing Ship Modeling through Research
SSL Secured
Your security is important for us so this Website is SSL-Secured
NRG Mailing Address
Nautical Research Guild
237 South Lincoln Street
Westmont IL, 60559-1917
Model Ship World ® and the MSW logo are Registered Trademarks, and belong to the Nautical Research Guild (United States Patent and Trademark Office: No. 6,929,264 & No. 6,929,274, registered Dec. 20, 2022)
Helpful Links
About the NRG
If you enjoy building ship models that are historically accurate as well as beautiful, then The Nautical Research Guild (NRG) is just right for you.
The Guild is a non-profit educational organization whose mission is to “Advance Ship Modeling Through Research”. We provide support to our members in their efforts to raise the quality of their model ships.
The Nautical Research Guild has published our world-renowned quarterly magazine, The Nautical Research Journal, since 1955. The pages of the Journal are full of articles by accomplished ship modelers who show you how they create those exquisite details on their models, and by maritime historians who show you the correct details to build. The Journal is available in both print and digital editions. Go to the NRG web site (www.thenrg.org) to download a complimentary digital copy of the Journal. The NRG also publishes plan sets, books and compilations of back issues of the Journal and the former Ships in Scale and Model Ship Builder magazines.