-
Posts
893 -
Joined
-
Last visited
About No Idea
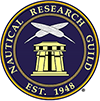
- Birthday 08/10/1967
Profile Information
-
Gender
Male
-
Location
Dudley Black Country England
Recent Profile Visitors
-
Tobias reacted to a post in a topic: LE ROCHEFORT 1787 by Tobias - 1:36 - Harbor Yacht from ANCRE monograph
-
No Idea reacted to a post in a topic: LE ROCHEFORT 1787 by Tobias - 1:36 - Harbor Yacht from ANCRE monograph
-
No Idea reacted to a post in a topic: Sloop Speedwell 1752 by Chuck - Ketch Rigged Sloop - POF - prototype build
-
No Idea reacted to a post in a topic: Sloop Speedwell 1752 by Chuck - Ketch Rigged Sloop - POF - prototype build
-
Scottish Guy reacted to a post in a topic: Type of glue to use planking a hull
-
No Idea reacted to a post in a topic: HM Sloop Echo 1781 by VTHokiEE - 1:48 - Cross-Section
-
No Idea reacted to a post in a topic: Sloop Speedwell 1752 by Chuck - Ketch Rigged Sloop - POF - prototype build
-
cotrecerf reacted to a post in a topic: Le Rochefort by No Idea - 1/24th Scale - First POF Build
-
No Idea reacted to a post in a topic: HMS PEGASUS by giampieroricci - Scale 1:36 - Swan-Class Sloop from plans by David Antscherl & Greg Herbert
-
No Idea reacted to a post in a topic: HMS PEGASUS by giampieroricci - Scale 1:36 - Swan-Class Sloop from plans by David Antscherl & Greg Herbert
-
No Idea reacted to a post in a topic: Le Rochefort by No Idea - 1/24th Scale - First POF Build
-
No Idea reacted to a post in a topic: La Mahonesa by KLarsen - Scale 1/48 - stern cross-section
-
Beef Wellington reacted to a post in a topic: Le Rochefort by No Idea - 1/24th Scale - First POF Build
-
Beef Wellington reacted to a post in a topic: HMS Jason by Beef Wellington - Caldercraft - 1:64 - Artois-class frigate modified from HMS Diana 1794
-
Tobias in hindsight I should have used your method as it's far more accurate than the way I made these parts. When it came for me to apply the planking to the dogs legs I had to thin them out to get the correct hull shape. This pretty much showed my errors in the way that I made them. I can see by the way that you have made yours you will not have the same experience as me. I shall be using your method on my next build and thanks for sharing how you did these difficult parts. Cheers Mark 😃
-
I have to say that your work is fantastic - Great joints and it's so symmetrical too. I found that making the fashion pieces correctly to fit the wing transom and filler pieces was particularly difficult and you have smashed it - top job!
- 54 replies
-
- ancre
- La Mahonesa
-
(and 1 more)
Tagged with:
-
No Idea started following Bonhomme Richard by BlockPlane - Scale 1/48 - ANCRE and Hello from Leicester, England
-
Hi Nic and welcome - thanks for showing your grandfathers build that really is a lovely ship. If you would like to get into ship building get in touch with @chris watton as he supplies the most beautiful kits. He's based not far from you in Gloucester
-
I've spent the last few days marking out the strakes which is pretty time consuming. I wanted to stay as close to the plans as possible and try and achieve a nice even look too. I like to use automotive lining tape as it's nice and flexible - the only issue with this sort of tape is that it doesn't stick very well to the wood. So after using tick tape and a planking fan to mark out the master frame I started the job. My planks work out to be 9.9mm wide on this frame so I'll cut them to 10mm as my measurements are probably out a bit. Lining the stern Then the Bow I have one stealer in the stern straight off of the garboard plank and one drop plank towards the bow. So it's just as the plans suggest. I had better start cutting some planks now and get on with the job Mark
-
My build is out of square by roughly the same amount as yours. It won't notice as it doesn't on mine - keep going as your work looks great!
- 54 replies
-
- ancre
- La Mahonesa
-
(and 1 more)
Tagged with:
-
Hi Brian and thanks for your really nice comments. You're spot on about how people have no clue about how ships were made and they probably have no interest either nowadays. I too really like the frames of this ship but this little vessel has always been a learning curve for me. I need to know that I can plank the hull as it should have been and I would like one side finished so that my family can see the ship without having to imagine it. The port side however will stay bare from the whale down so that the frames will always be visible. Cheers Mark
About us
Modelshipworld - Advancing Ship Modeling through Research
SSL Secured
Your security is important for us so this Website is SSL-Secured
NRG Mailing Address
Nautical Research Guild
237 South Lincoln Street
Westmont IL, 60559-1917
Model Ship World ® and the MSW logo are Registered Trademarks, and belong to the Nautical Research Guild (United States Patent and Trademark Office: No. 6,929,264 & No. 6,929,274, registered Dec. 20, 2022)
Helpful Links
About the NRG
If you enjoy building ship models that are historically accurate as well as beautiful, then The Nautical Research Guild (NRG) is just right for you.
The Guild is a non-profit educational organization whose mission is to “Advance Ship Modeling Through Research”. We provide support to our members in their efforts to raise the quality of their model ships.
The Nautical Research Guild has published our world-renowned quarterly magazine, The Nautical Research Journal, since 1955. The pages of the Journal are full of articles by accomplished ship modelers who show you how they create those exquisite details on their models, and by maritime historians who show you the correct details to build. The Journal is available in both print and digital editions. Go to the NRG web site (www.thenrg.org) to download a complimentary digital copy of the Journal. The NRG also publishes plan sets, books and compilations of back issues of the Journal and the former Ships in Scale and Model Ship Builder magazines.