-
Posts
605 -
Joined
-
Last visited
About tmj
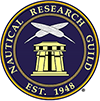
Profile Information
-
Gender
Male
-
Location
: Sailing the trail upon the Dusty Ol' Seas of "Texas"
Recent Profile Visitors
-
tmj reacted to a post in a topic: Sternwheeler From the Susquehanna River's Hard Coal Navy by Keith Black - 1:120 Scale
-
tmj reacted to a post in a topic: Sternwheeler From the Susquehanna River's Hard Coal Navy by Keith Black - 1:120 Scale
-
tmj reacted to a post in a topic: Sternwheeler From the Susquehanna River's Hard Coal Navy by Keith Black - 1:120 Scale
-
tmj reacted to a post in a topic: HMS PEGASUS by giampieroricci - Scale 1:36 - Swan-Class Sloop from plans by David Antscherl & Greg Herbert
-
tmj reacted to a post in a topic: HMS PEGASUS by giampieroricci - Scale 1:36 - Swan-Class Sloop from plans by David Antscherl & Greg Herbert
-
tmj reacted to a post in a topic: HMS PEGASUS by giampieroricci - Scale 1:36 - Swan-Class Sloop from plans by David Antscherl & Greg Herbert
-
tmj reacted to a post in a topic: Sternwheeler From the Susquehanna River's Hard Coal Navy by Keith Black - 1:120 Scale
-
tmj reacted to a post in a topic: Sternwheeler From the Susquehanna River's Hard Coal Navy by Keith Black - 1:120 Scale
-
tmj reacted to a post in a topic: Sternwheeler From the Susquehanna River's Hard Coal Navy by Keith Black - 1:120 Scale
-
billocrates reacted to a post in a topic: HMS PEGASUS by giampieroricci - Scale 1:36 - Swan-Class Sloop from plans by David Antscherl & Greg Herbert
-
tmj reacted to a post in a topic: Sternwheeler From the Susquehanna River's Hard Coal Navy by Keith Black - 1:120 Scale
-
FriedClams reacted to a post in a topic: Sternwheeler From the Susquehanna River's Hard Coal Navy by Keith Black - 1:120 Scale
-
Canute reacted to a post in a topic: Sternwheeler From the Susquehanna River's Hard Coal Navy by Keith Black - 1:120 Scale
-
Keith Black reacted to a post in a topic: Sternwheeler From the Susquehanna River's Hard Coal Navy by Keith Black - 1:120 Scale
-
ChefEd reacted to a post in a topic: Shot Garlands
-
About the weathering. I have to go back to one of your first images. It appears as though the pilot house is darker and dirtier than the deck house/engine room. Could this be from soot and winds/breezes up high blowing that smoke more onto the pilot house walls than onto the engine room walls? Other than this one tiny observation, I think your weathering looks 'GREAT' and close to 'PERFECT'! It could be the light also. You've already mentioned that the photos of your work look different than the real thing, due to lighting. Looking at the location of that 'smokestack'... that pilot must have been hating life if the wind blew in the wrong direction! 🫤
-
This is a chunk of Black Mesquite. I love Mesquite in my BBQ pit and now I'm going to see how much I like it on my modeling bench. I have an upcoming build and want to use this for my keel, sternpost, stempost, deadwood and rising wood components. It's some hard stuff for sure. It's going to give my tools a good workout, offering lots of sharpening opportunities in my future! 😬
-
... all being said. Just how far would 'any' true attempt at litigation be allowed to proceed, while in discovery it became 'obvious' that no mal intent, nor any desires or methods to profit from said, used 'image(s)' ever existed? Sure, there is legal 'precedence everywhere you look, but that's not the "Be All" of the laws of our land! "I object!" Perry Mason
-
Perhaps you can simply modify more popular, easy to obtain blades via a rotary tool, so they will fit? Dunno, just tossing that out there. You could also just re-sharpen the existing blade via stones and a strop, just like a straight razor... Option #3... buy some thin 01 tool steel off of Amazon and make a new, better blade, harden it with a propane torch and canola oil and hone a scary sharp edge on it. You'll have all the blades you'll ever need then! 😁
About us
Modelshipworld - Advancing Ship Modeling through Research
SSL Secured
Your security is important for us so this Website is SSL-Secured
NRG Mailing Address
Nautical Research Guild
237 South Lincoln Street
Westmont IL, 60559-1917
Model Ship World ® and the MSW logo are Registered Trademarks, and belong to the Nautical Research Guild (United States Patent and Trademark Office: No. 6,929,264 & No. 6,929,274, registered Dec. 20, 2022)
Helpful Links
About the NRG
If you enjoy building ship models that are historically accurate as well as beautiful, then The Nautical Research Guild (NRG) is just right for you.
The Guild is a non-profit educational organization whose mission is to “Advance Ship Modeling Through Research”. We provide support to our members in their efforts to raise the quality of their model ships.
The Nautical Research Guild has published our world-renowned quarterly magazine, The Nautical Research Journal, since 1955. The pages of the Journal are full of articles by accomplished ship modelers who show you how they create those exquisite details on their models, and by maritime historians who show you the correct details to build. The Journal is available in both print and digital editions. Go to the NRG web site (www.thenrg.org) to download a complimentary digital copy of the Journal. The NRG also publishes plan sets, books and compilations of back issues of the Journal and the former Ships in Scale and Model Ship Builder magazines.