-
Posts
1,303 -
Joined
-
Last visited
About Thukydides
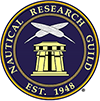
Profile Information
-
Location
Canada
Recent Profile Visitors
-
dunnock reacted to a post in a topic: HMS Harpy 1796 by dunnock - Vanguard Models - 1:64
-
Thukydides reacted to a post in a topic: 18th Century Longboat by Desertanimal - Model Shipways - 1:48
-
Thukydides reacted to a post in a topic: HMS Harpy 1796 by dunnock - Vanguard Models - 1:64
-
Thukydides reacted to a post in a topic: HMS Harpy 1796 by dunnock - Vanguard Models - 1:64
-
Thukydides reacted to a post in a topic: Worst Planking Job Ever
-
Thukydides reacted to a post in a topic: Chris Watton and Vanguard Models news and updates Volume 2
-
Thukydides reacted to a post in a topic: Bateau de Lanvéoc by JacquesCousteau - Scale 1:32 - From Ancre Plans
-
Baker reacted to a post in a topic: Type VIIC U-Boat by Thukydides - FINISHED - HobbyBoss - 1:350 - PLASTIC
-
Thukydides reacted to a post in a topic: HM Gun Brig Adder by ECK - FINISHED - Vanguard Models - 1:64
-
Log #30: Framing the Stern Part I As I alluded to in update 28, there were a few cases where I took too much off with the faring. One of those is visible in the last image in the post. I had been overzelous in my sanding around the reinforcement for the stern fastener and took too much off of one side. This was actually fixed just after I posted log 28, but I was waiting till my next progress post to show the correction. You can see I used a combination of scrap pear and wood filler to build up the area before sanding it back down. This time I paid careful attention to the run of the battons in the area and checked from the stern frequently to make sure the bulkheads were the same on both sides. With that correction done, it was time to turn my attention to the framing of the stern. I was pretty apprehensive about this part of the build as even slight issues are much harder to correct (can't just stick some filler on it). Cutting the stern framing pieces turned out to be much easier than I thought. I guess all my practice on the rest of the build has made me much more precise with the scroll saw, but I didn't have issues cutting them apart from the usual very small touchups needed with a file. I cut them out of pear for two reasons: Strength, the pear is much stronger than plywood of basswood. I have not yet fully decided what I am going to do finish wise around the stern galleries and so there is a chance that I might want to show bare wood. I tried to arrange them so as to minimize grain issues on the thin protruding parts of the pieces. You can see in the above picture me arranging the two inner frames. I have a basswood filler piece in-between them which represents the shape of the top of the transom. This serves two purposes. First, it will define the shape (though it will ultimately be covered by planking and a thin rail piece). Second, it helps me correctly adjust the spacing on the frames. I spent a long time getting these in just the right place. You can see how in the above picture I am using a square to make sure they are aligned properly with the build board. I would say I spent at least an hour making micro adjustments and looking at it from every angle. Once I was happy I then brushed watered down wood glue into the joints. I did this because I was not confident I could get the alignment done properly before the glue began to set, so it was better to get everything in place and then add the glue. And above you can see the state of affairs after the next two frames have been added. The filler pieces have not yet been thinned down for final installation, but they work fine as spacers for the moment. The process for adding all the subsequent frames was the same as the first and took place over multiple days. I waited for each set of frames to dry and brushed glue into the joints a second time for each to make sure there was no risk of things shifting. And here is the current state of affairs. I have added the final two frames, but they are not yet complete as I need to add some basswood filler pieces to the outside of them to represent the complex curve that the outer frames were made of. This technique I am copying from Chuck's Winchelsea instructions which I have relied on heavily in this structural phase of the project. You may also notice that the outer frames are slightly thicker. This is because they need to be sanded to have a slight curve, but this will not be done until the rest of the stern framing is complete. Thanks again to everyone who has stopped by to take a look and for all your encouragement.
-
Another fantastic model and build log complete. I really quite like the presentation you have gone for here with the topmasts struck.
- 332 replies
-
- Harpy
- Vanguard Models
-
(and 1 more)
Tagged with:
-
I used panty hoes. You can stretch it round the mouse to give a nice woven effect.
- 341 replies
-
- Sophie
- Vanguard Models
-
(and 1 more)
Tagged with:
-
You have made a good start. Take it slow and careful with the faring. The bow looks like it could do with a bit more sanding. You essentially want only a thin line of the char on the one edge of each bulkhead. If you still see black all over then you have not taken enough off. Make sure you are careful not to sand the keel now that you have it on the model. One trick is to take some of the thin strips and hold them against the line of the hull at various angles. They should lie flat against the bulkheads in a smooth curve. If there are any air gaps it probably means you took too much off or the bulkheads on either side don't have enough taken off. Good luck.
-
Those are some super cool options. I appreciate @chris wattonhow you are giving modelers flexibility. She is going to be quite the model. Just to add an interesting anecdote on gun carriage colours. I have even found some evidence which suggest that the one ship (mid 1770s) may have had guns in both colours. Those on the forecastle were painted red, but those on the main gun deck painted yellow. So I suspect there was a fair bit of variation.
-
Welcome to MSW. Sherburne is a great choice for a first model. Good luck.
-
Log #29: Researching the Figurehead As the structure of the model gets closer and closer to being done, I have been turning my attention to trying to finalize my research on the things that will impact the next stage of the build. Much like my post on the wales, I am documenting the current state of my thoughts now to see if anyone has anything to add before I make firm decisions. In the background I have also been working on revising the research document to include parts of Chapter III (which will discuss the bow of the ship) as well as revisions and corrections to the already released sections incorporating feedback I have received as well as more information I have discovered. I am planning on releasing this revised version in the next week or two. The Figurehead Figureheads are in many ways one of the most striking parts of the 18th century sailing vessel. In the 17th century the majority of Royal Navy ships had a lion as a figurehead, but towards the later part of the 17th and into the 18th century the figures began to increase in complexity. By the late 18th century figures relating to the name of the vessel were the predominant choice, but at times the relationship to the name was tenuous at best. This was sometimes the result of renaming, but in other cases it is unclear why a particular figure was chosen. In his book Old Ship Figureheads & Sterns Carr Laughton recounts one particularly egregious example where the frigate Blonde was given a figurehead of a bearded warrior. Figureheads in the late 18th century were looked on with great pride by their crews. Even during the economy of Lord Spencer in 1794, when most new construction received only scrollwork in place of a figurehead, crews often took it upon themselves to add figureheads to their ships. There are accounts of crews adding painted detail to their figures with one captain writing that the figurehead of another sloop was “painted in colours with a bloody nose and a real broomstick in her hand.” National Maritime Museum, Greenwich, London. FHD0120. Despite the prevalence of figures, the lion remained common and there is no definitive evidence in the primary record to indicate what sort of figurehead Perseus was given. The contract for Perseus and Unicorn states that the ships were to receive figureheads, but does not specify beyond stating that they should be “lion or figure with a double trailboard as shall be directed.” Lion figureheads had a long history in the Royal Navy by the time Perseus was constructed and there are numerous examples in the historical record documenting them. One of the few figureheads that have been preserved from the 18th century is of a lion, likely the figurehead of an English 4th or 5th rate circa 1720. National Maritime Museum, Greenwich, London. FHD0088. A similar depiction can be seen in a 1741 model of a 24 gun sixth rate sloop. Most contemporary models seem to have depicted the figureheads painted gold or unpainted. However, many of these models were created by the shipwrights and the painting of the figureheads in more realistic colours was often done upon request or after launch by their crews. National Maritime Museum, Greenwich, London. SLR0461. Only four of the ten Sphinx class ships launched have their figureheads documented by the Admiralty. Plans for Sphinx, Camilla, Daphne and Vestal all show the carved decorations including the figurehead. In each of these cases, the figureheads are unique to the vessel and relate to their name. Though Perseus and Unicorn were not built in Navy Yards, it does seem to suggest that it is more probable that the figurehead related in some way to the name of the ship. Launched 85 years after Perseus 1776 at the end of the sailing era, Perseus 1861, a 17 gun Camelion-class wooden screw sloop, includes an image of the figurehead in the Admiralty plans. The figure is the upper half of a Greek warrior with the traditional forward curve on the helm seen on many contemporary statues depicting Perseus. He is clean shaven, wearing scale mail and is depicted without any limbs. The figure is in the style of other mid 19th century figureheads which dispensed with the full figures from the time of Perseus 1776. National Maritime Museum, Greenwich, London. DIC0111. Probably the most compelling evidence for a figure of Perseus is the blurry figure visible in the image of Perseus on a bowl from 1790. Though it is impossible to say definitively, the figure in the image appears to have an extended arm. Classical depictions of Perseus tend to depict him with the head of Medusa held out in front of him. It should be noted that the idea of having a figure with an extended hand was not uncommon in the period. Termagant, a 22 gun ship launched in 1780 , features a figure with their left hand extended forward as did Leopard 1790. National Maritime Museum, Greenwich, London. AAA4434. Perseus was a Greek mythical hero who is most famous for killing the gorgon Medusa using a polished shield given to him by Athena and winged sandals lent to him by Hermes which allowed him to fly. Perseus cut off Medusa’s head and Pegasus (a winged horse) and Chrysador (either a giant or a flying bore) were born from the severed neck. Perseus rescued Andromeda the daughter of Cepheus, the king of Aethiopia from being sacrificed to the sea monster Cetus before marrying her and founding the Mycenaean kingdom. Pegasus is often associated with Perseus as many later depictions show Perseus riding to Andromeda’s rescue on Pegasus. Contemporary artwork available from the period appears to universally portray Perseus holding the head of Medusa. In most of these examples he is portrayed as clean shaven. The stern carvings for Pegasus 1776, a 14 gun sloop launched the same year as Perseus, portray Perseus as a clean shaven man with a sword in his right hand and the head of Medusa in his left. National Maritime Museum, Greenwich, London. ZAZ4782. A statue depicting Perseus from the mid 19th century is held at the Victoria & Albert Museum. The statue shows Perseus in armour with a sword in his right hand and the head of Medusa held out in his left. Perseus can also be seen in a set of constellation cards dating from approximately 1825. Perseus is depicted again holding a sword in his right hand and the head of Medusa in his left. Victoria & Albert Museum. Mvsei Vaticani. Cat 969. National Maritime Museum, Greenwich, London. AST0049.
-
I also struggled with how to splice smaller lines and what I ended up doing was adding dowels to the end of two alligator clips. The dowels can then be slid through the holes and the second set of clips can then be used on the dowels to hold them the correct distance apart. I made a short one and a long one so I could use one or both of them depending on how much line I needed to serve. This allowed me to serve very small pieces that I needed to have the holding points much closer together. I was looking through my alert album and I don't seem to have a picture of it. I can take a picture later if you really want to see the actual setup, but the below drawing should illustrate it pretty well. The blue is the dowels, the red, the alligator clips and the green the line being served.
- 341 replies
-
- Sophie
- Vanguard Models
-
(and 1 more)
Tagged with:
About us
Modelshipworld - Advancing Ship Modeling through Research
SSL Secured
Your security is important for us so this Website is SSL-Secured
NRG Mailing Address
Nautical Research Guild
237 South Lincoln Street
Westmont IL, 60559-1917
Model Ship World ® and the MSW logo are Registered Trademarks, and belong to the Nautical Research Guild (United States Patent and Trademark Office: No. 6,929,264 & No. 6,929,274, registered Dec. 20, 2022)
Helpful Links
About the NRG
If you enjoy building ship models that are historically accurate as well as beautiful, then The Nautical Research Guild (NRG) is just right for you.
The Guild is a non-profit educational organization whose mission is to “Advance Ship Modeling Through Research”. We provide support to our members in their efforts to raise the quality of their model ships.
The Nautical Research Guild has published our world-renowned quarterly magazine, The Nautical Research Journal, since 1955. The pages of the Journal are full of articles by accomplished ship modelers who show you how they create those exquisite details on their models, and by maritime historians who show you the correct details to build. The Journal is available in both print and digital editions. Go to the NRG web site (www.thenrg.org) to download a complimentary digital copy of the Journal. The NRG also publishes plan sets, books and compilations of back issues of the Journal and the former Ships in Scale and Model Ship Builder magazines.