-
Posts
1,115 -
Joined
-
Last visited
About JacquesCousteau
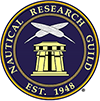
Profile Information
-
Location
Mexico City
Recent Profile Visitors
The recent visitors block is disabled and is not being shown to other users.
-
JacquesCousteau reacted to a post in a topic: HMS Sphinx by KurtH - Vanguard Models - 1/64 - First POB Model
-
JacquesCousteau reacted to a post in a topic: HMS Terror by Greg Davis - OcCre - 1:75 scale
-
JacquesCousteau reacted to a post in a topic: HMS Pegasus 1776 by Knocklouder - Amati/Victory Models - 1:64
-
JacquesCousteau reacted to a post in a topic: Sloop Speedwell 1752 by Chuck - Ketch Rigged Sloop - POF - prototype build
-
JacquesCousteau reacted to a post in a topic: J H Crawford by LJP (Lawrence Paplham) - Scale 1:64 - an 1894 to 1898 Wisconsin sternwheeler
-
JacquesCousteau reacted to a post in a topic: Sternwheeler From the Susquehanna River's Hard Coal Navy by Keith Black - 1:120 Scale
-
JacquesCousteau reacted to a post in a topic: HM Cutter Sherbourne 1763 by Pinenuts - Vanguard Models - 1/64
-
palmerit reacted to a post in a topic: HM Armed Cutter Sherbourne 1763 by palmerit - FINISHED - Vanguard Models - 1:64 - First Build
-
Congratulations, it looks great! Very nice work for a first or a seventh model, you clearly built a lot of skills over the course of the build.
- 172 replies
-
- Sherbourne
- vanguard models
-
(and 3 more)
Tagged with:
-
JacquesCousteau reacted to a post in a topic: HM Armed Cutter Sherbourne 1763 by palmerit - FINISHED - Vanguard Models - 1:64 - First Build
-
JacquesCousteau reacted to a post in a topic: HM Armed Cutter Sherbourne 1763 by palmerit - FINISHED - Vanguard Models - 1:64 - First Build
-
JacquesCousteau reacted to a post in a topic: Sloop Speedwell 1752 by Chuck - Ketch Rigged Sloop - POF - prototype build
-
Mike Y reacted to a post in a topic: Bateau de Lanvéoc by JacquesCousteau - Scale 1:32 - From Ancre Plans
-
wefalck reacted to a post in a topic: Bateau de Lanvéoc by JacquesCousteau - Scale 1:32 - From Ancre Plans
-
Paul Le Wol reacted to a post in a topic: Bateau de Lanvéoc by JacquesCousteau - Scale 1:32 - From Ancre Plans
-
chris watton reacted to a post in a topic: Bateau de Lanvéoc by JacquesCousteau - Scale 1:32 - From Ancre Plans
-
Keith Black reacted to a post in a topic: Bateau de Lanvéoc by JacquesCousteau - Scale 1:32 - From Ancre Plans
-
Thukydides reacted to a post in a topic: Bateau de Lanvéoc by JacquesCousteau - Scale 1:32 - From Ancre Plans
-
Thukydides reacted to a post in a topic: Bateau de Lanvéoc by JacquesCousteau - Scale 1:32 - From Ancre Plans
-
Thukydides reacted to a post in a topic: Bateau de Lanvéoc by JacquesCousteau - Scale 1:32 - From Ancre Plans
-
Harvey Golden reacted to a post in a topic: Bateau de Lanvéoc by JacquesCousteau - Scale 1:32 - From Ancre Plans
-
Two more frames--II and III--glued up and dry-fit. At this point, only the cant frames are left. The shape of the hull is really starting to come together by now. But, an issue. Looking at the side view in the plans, you can see that several frames are supposed to extend beyond the sheer. But of the frames I've made so far (II-XV), only II extends beyond the sheer. XII, XIV, and XV all end at the sheer, following the frame sheet of the plans, when the side plans show them as extended. It's a little hard to tell because I've left all frames a little long, which I suppose means I can try to extend them a bit, but maybe not quite as much as given in the plans. I have to admit that this is very frustrating--part of the point of buying a plan set like this, instead of developing this all from scratch, is that you assume the plans will be consistent between sheets. Ah well, I guess that the extensions will just be a little stumpy compared with the plan sheet.
- 70 replies
-
- ancre
- Bateau de Lanveoc
-
(and 2 more)
Tagged with:
-
Model shipways HMS Vanguard
JacquesCousteau replied to jefferyconley038's topic in Wood ship model kits
I wasn't aware that Model Shipways had ever offered that model, but it looks like they did for a short time. You might want to check out this build log for the kit: -
- 70 replies
-
- ancre
- Bateau de Lanveoc
-
(and 2 more)
Tagged with:
-
Well, once again I said I was looking forward to getting back to work on this build, and then made very little progress. I made a few more frames, and, while working on autopilot, accidentally trimmed one futtock at the wrong point, as seen below, and had to remake the piece. Despite that, yesterday I reached an important milestone: upon cutting out the frame pieces below, I have now finally finished sawing out all the frame parts! (Unless I have to remake more...) It certainly took a while to reach this point, and indeed, pretty much every aspect of this build is going slowly. There are a few reasons for this. I can only access the fretsaw in the carpentry workshop. I've only been able to attend a few times over the past month, and have been focused there on making a tea box, so I haven't had much time for sawing. The plan sheet takes up pretty much all my workspace at home, making it a bit of a hassle to glue up the frames, and the sanding generates a ton of dust--even with a mask on, I prefer to do it on out balcony, but that means I can only sand during the day when it's not raining (and when we haven't hung laundry there to dry). Not to mention that slowly sanding the frames is pretty tedious work. But this build is more of a marathon than a sprint. Two more frames were glued up last night: At the moment, I have ten frames glued up and dry-fit, although they'll need a lot more shaping before they can be glued. I'll also need to figure out the cant frames soon.
- 70 replies
-
- ancre
- Bateau de Lanveoc
-
(and 2 more)
Tagged with:
-
Congratulations, very nice job! I love the look of lateen-rigged vessels, and it's been interesting to follow your build log. The model fits well alongside the rest of the fleet. Looks like you may need another shelf soon!
- 62 replies
-
- sultan
- Artesania Latina
-
(and 2 more)
Tagged with:
-
Thanks! There will be some much more substantial modifications to come, but I'm still figuring them out. For example, Chapelle's plans don't specify how far below deck the floors or seats should be, to my eyes the kit design looks a little short so I'm considering deepening the cockpit a bit (which Dee Dee, in his build log, seems to have done, but most of the photos don't load for me). So I'll need to work that out before I glue anything into place.
-
Given that the backbone is slightly wider, proportionally, than in the kit design, I needed to do some reshaping to get the bulkheads to properly fit. This was actually a very straightforward process. I used sanding sticks and mini files to slightly widen the slots. Bulkhead five, which has a narrowed slot at the top for the centerboard, especially needed shaping. In order to avoid removing too much material from the bulkheads, which would screw up the bottom edge where bulkhead meets keel, I also thinned the backbone at each slot. Thankfully my square mini-file is 1/8-inch square, the same thickness as my bulkheads, so this was simple to do. They aren't the straightest file lines, as the file sometimes skated across the surface rather than registering properly, but everything will be covered. Bulkhead 4, which is built in two parts around the centerboard, was a little tricky to properly fit due to its complex design. I had to trim the supports back a bit. For whatever reason, it didn't seem to need a groove filed in the backbone to fit properly--I filed more of a groove on the port side, but the bulkhead half just kind of hovers above it. It may need a little more fairing compared with the other bulkheads, but it should be fine and seems to line up pretty well with the other bulkheads. I also accidentally widened the slots for bulkhead 10, the transom, a little too much, making a very loose fit. I think the transom itself, which I still need to make, should hold it in place well, though. In any case, here is the backbone with all slots prepared: And here, the bulkheads dry-fit in place.
-
Thanks, Paul! The makerspace was really a lot of fun. The one I used had a lot of other equipment, too, including a CNC machine, a 3D printer, and a Cricut machine. If I had had more time, I would have loved to experiment with more of the tools there. I've progressed a bit more on the backbone. I'm still working out exactly how the centerboard pull will work, as it seems like a more accurate option may be a jointed or chain pull running through a small hole rather than a rigid rod running through a slot, as the kit would have it. At least, that's how I read Chapelle's diagram, which seems to have a small block or something for a rope or chain pull to run through? I could be wrong, though, I'm still considering my options. In any case, I'll be able to add the centerboard pull a little later, so I went ahead and glued on the starboard backbone piece. Despite using the spacers, I somehow got it a little high foreward. The backbone is straight, though, and I'll be adjusting the slots anyway to accommodate the slightly thick bulkheads. The only problem I can see this causing is that the backbone side pieces provide extra gluing surface to affix the ends of the planks, but I can always add an extra piece to build this up if necessary. In any case, I trimmed the top flush. I then drilled the new hole for the centerboard pivot through the starboard side, and added a length of copper wire for the pivot point. Next up, the reinforcing pieces. When prepping these in Lightburn, I left these parts with the doubled cut line I mentioned above, as it seemed fine if they turned out slightly undersized. After adding them, the backbone is pretty solid. Next up, I'll be attacking the bulkheads and backbone with files to get the slots properly sized.
-
Welcome! Very nicely done on the Lobster Smack, and great job on the full-scale boats! Starting a build log is the best way to get answers to any questions you have.
-
After finishing my build of a Lancha Chilota about a month ago, I thought that my next build would be a Brazilian Jangada fishing raft. However, as I began reading for it, I realized that it would take a lot longer than I expected before I could start making sawdust. I would need to do a fair bit of research up front, which is a hard to do right now as my job is currently in a busy period. So, I decided to put the Jangada on the backburner for now, and start a new build that I've already done a lot of the background research for: a Muscongus Bay Lobster Smack, based on the Model Shipways Shipwright Series. I had originally planned on building this way back in 2023, but my kit never arrived in Mexico, and by the time I finally was able to get it in the US, I was focused on other builds. Despite putting it off for a while, though, I'm looking forward to this model. I quite enjoy building these sorts of fishing boats. This one has very nice lines, and being based on a kit, it should be a bit of a more straightforward build with less time and effort up front to figure out the underlying structure. This is quite a popular model with a lot of excellent build logs, for both the Model Shipways kit (which I have) and the Midwest kit, many of which have personalized it by diverging from the kit in some way. I also hope to do something a little different with it. First, I decided to rescale the kit from 1:24 to 1:32, making for a smaller, easier-to-display model in the same scale as most of my other builds. This will really highlight the design differences between the Lobster Smack and the Lancha Chilota--both gaff sloops of similar lengths, but meant for totally different purposes. Rescaling the kit means not using any of the kit materials. In theory I could have just gone with a totally different scratch-build, but as will be seen, the rescaling process was pretty quick, and (as long as I didn't screw up) should result in a nice model without needing to do all the work of developing the hull from scratch. Rescaled, the model has a total hull length of about 8.5 inches, corresponding to a vessel a bit over 22.5 feet long. The second big difference is that I will be diverging from the kit design to follow other sources in a number of aspects. Although the kit uses carvel planking and has stays, most Muscongus Bay Lobster Smacks used lapstrake planking and lacked stays, for example, and many seem to have lacked the beakhead on the kit version. I'll discuss this in more detail later, but the kits is heavily based on Chapelle's plans for the vessel, yet the vessel that he drew plans for seems slightly atypical in some respects. I'm still working out exactly how I'll modify the design, but the basic framework will be the same, so I've begun work on that. (I'm not really sure if this log should be in the kit or scratch-build section, as it's an oddity. I seem to remember seeing builds based on kit plans located in the scratch section, hence my decision. Moderators, please feel free to move it if necessary. Thanks!) Rescaling I started this model in late 2024 while visiting family in the US. When I moved to Mexico and had limited space in my luggage, they kindly offered to hold onto the kit for me until I could take it later. While visiting, I realized that I could use the local public library's free makerspace to rescale the kit. I began by scanning all the part sheets, and the very friendly makerspace staff were able to show me how to import the files into Lightburn and set them up for laser cutting. (Here I should probably note that the scans and files are strictly for my personal use, not for the purposes of piracy.) Despite my lack of experience, I found Lightburn pretty easy to use, but there were a couple things to be aware of. I had to rearrange a lot of parts to fit on the basswood sheets I used. When I imported the scan, I needed to do a fair bit of cleaning and removing artifacts, as it interpreted a lot of darker spots in the wood as lines to cut. It also generated a double line around all parts, because it traced both sides of the laser cut, so I needed to erase one of the lines to avoid double-cutting. For my test piece, I chose to use the inner line, which (as I should have realized) led to a slightly undersized piece. For the actual parts, I used the outer line, except for in the slots in the backbone and bulkheads. This is because I was not able to scale down the thickness of all the wood, so the bulkheads and keel are slightly thicker, proportionally, than they are on the actual kit. Before too long, I had the full rescaled "kit" ready to go. I was not able to figure out the exact settings to minimize burning, so quite a few of the cuts have some scorching around them. As I'll be painting the model, this won't be a problem. The makerspace staff were really friendly and helpful, and a lot of people were interested in the project. This was definitely a lot faster than trying to cut all the parts by hand, and I would definitely be interested in using a laser cutter again if possible (it certainly would make my Bateau de Lanvéoc build a lot faster...). As can be seen, the rescaled model will be a good bit smaller than the kit. Kit deck above, rescaled version below. Framework After traveling back to Mexico, the parts sat around while I worked on other builds, until yesterday night, when I began building the backbone structure. It fits together well. It's a great idea to include spacers in the kit to align the backbone parts while gluing, as I often find that parts slide a bit when clamping. I should note that, while the kit uses slightly different shapes above the centerboard slot for each side of the backbone, I just copied one side to reduce my workload in Lightburn. It's interesting to see how well the backbone matches up with the plans included in Howard I. Chapelle's American Small Sailing Craft (1951). To simplify the laser cutting and use only readily-available wood thicknesses, I made the centerboard of the same 1/16‐inch thick basswood as the central backbone part. Of course, it needed to be thinned to allow for movement, so I planed it and sanded it thinner. I then ran into a slight problem. Lining up the pivot point, the centerboard would not be able to be fully raised as it contacted the backbone at several points. The centerboard pull rod also wouldn't be aligned with the slot. This was easy to fix. I trimmed a bit off the top of the centerboard and relocated it a bit forward, drilling a new pivot hole. This allowed it to fit and aligned the pull rod hole with the slot. I decided to paint the hull red below the waterline, so I painted the visible portion of the centerboard. I'm still deciding on the above-water hull color. I like the look of a darker hull, so I'm thinking either black or a sort of bottle green, both of which seem to have been common enough fishing boat colors in the US northeast in the period (although it's hard to tell which is which from black-and-white photos). I also used a dab of superglue to reinforce the area around the centerboard pull hole. That's where the build's at, very enjoyable so far. In future posts, I'll discuss a bit more about the history of this vessel type, sources, and the changes I'll be making.
-
It looks great! The sails really add something.
- 62 replies
-
- sultan
- Artesania Latina
-
(and 2 more)
Tagged with:
-
hull finishing
JacquesCousteau replied to serpe's topic in Painting, finishing and weathering products and techniques
Sounds like an interesting plan! You may want to consider using wooden treenails, instead, as they can be made in scale and are more accurate than brass. Searching a bit on this site should bring up lots of examples and instructions.
About us
Modelshipworld - Advancing Ship Modeling through Research
SSL Secured
Your security is important for us so this Website is SSL-Secured
NRG Mailing Address
Nautical Research Guild
237 South Lincoln Street
Westmont IL, 60559-1917
Model Ship World ® and the MSW logo are Registered Trademarks, and belong to the Nautical Research Guild (United States Patent and Trademark Office: No. 6,929,264 & No. 6,929,274, registered Dec. 20, 2022)
Helpful Links
About the NRG
If you enjoy building ship models that are historically accurate as well as beautiful, then The Nautical Research Guild (NRG) is just right for you.
The Guild is a non-profit educational organization whose mission is to “Advance Ship Modeling Through Research”. We provide support to our members in their efforts to raise the quality of their model ships.
The Nautical Research Guild has published our world-renowned quarterly magazine, The Nautical Research Journal, since 1955. The pages of the Journal are full of articles by accomplished ship modelers who show you how they create those exquisite details on their models, and by maritime historians who show you the correct details to build. The Journal is available in both print and digital editions. Go to the NRG web site (www.thenrg.org) to download a complimentary digital copy of the Journal. The NRG also publishes plan sets, books and compilations of back issues of the Journal and the former Ships in Scale and Model Ship Builder magazines.