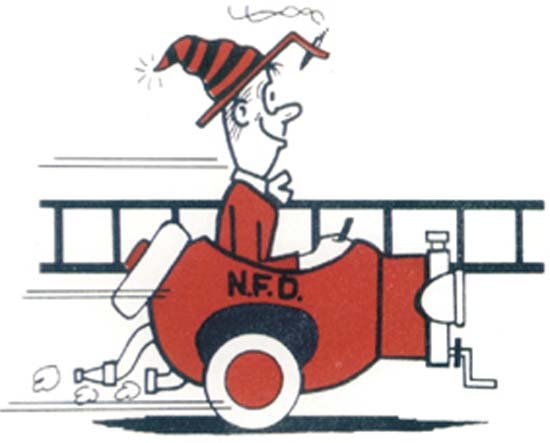
Estoy_Listo
-
Posts
83 -
Joined
-
Last visited
Reputation Activity
-
Estoy_Listo got a reaction from Glen McGuire in Sea of Galilee Boat by Knocklouder - FINISHED - SE Miller - 1/20 scale
Smashing build, Bob. And thanks for the log. It's helped me a lot.
-
Estoy_Listo got a reaction from Knocklouder in Sea of Galilee Boat by Knocklouder - FINISHED - SE Miller - 1/20 scale
Smashing build, Bob. And thanks for the log. It's helped me a lot.
-
Estoy_Listo got a reaction from Jeff preisler in Skiff by dcicero - FINISHED - Bluejacket Shipcrafters - 1:12
Sweet build: simple and elegant; featured as the "Model of the Month" in Blue Jacket's monthly newsletter.
-
Estoy_Listo reacted to Cathead in A method for making panelled sails using paper
Part III: Adding reef points
Reef points add a lot of visual interest to sails, and they're easy to add in the paper-sail method.
The reef bands were glued on in Part I. Where to place the reef points is something of an uncertain topic; I found references for a variety of options, including one point on each seam, one point within each panel, and two points within each panel. I chose to use the first approach. Because the paper layers were extra thick here, due to the seam and reef bands, I used a small drill bit to open up a hole rather than trying to drive a needle through.
For the reef points, I cut a series of rigging rope a bit longer than I needed. I wanted my reef points 2 scale feet long, so I cut the rope 5' long to allow for trimming, then used a deadeye/block threader to run each line through the sail. The threader creates a strong crimp in the line, so I tried to center each line in the threader before pulling it back through; the crimp then becomes a natural reference point holding the line in place where it passes through the sail.
When all the lines for a given band were threaded, I clamped a piece of wood across the sail 2 scale feet below the reef band as a reference marker. You can get the length right here in two ways: either trim each line to the right length relative to the crimp, or don't worry about the crimp and pull each one back through the sail until only 2' are left on the side you're working on. I then used a fine brush to gently apply a bit of glue to a line, then pressed it into place on the sail with its tip against the wood. You only have to hold the line in place for maybe 10-15 seconds for the glue to take hold, before moving on to the next one. I like to get glue from the tip to about 2/3 to the sail, not all the way to the sail. This means the line naturally bows out a bit where it comes out of the sail, giving it some 3D texture. Don't overdo the glue or you'll get weird stains on the paper. Also, don't worry about trying to get each line perfectly straight; they're going to want to curve this way and that, and buckle a bit, and that's exactly what you want because that really makes them look like loose lines dangling down. You want just enough glue to hold them relatively flat so they look like gravity is working. If you glue them too flat or perfect, they'll look glued on and artificial.
Once one side is done, it looks something like the image above. Then you just turn the sail over, clamp the wood at 2' again, trim the remaining lines to length, and glue them in the same way.
If there is more than one reef band, do the upper one first, since you're overall working on the lower side. Above, you see the same process being repeated for a lower line of reef points.
And here are the two completed lines of reef points. They have a nice randomness that looks like loosely dangling lines. Note that, once again, I slightly messed up this demonstration by not cutting the upper line of reef points quite evenly (they're too short on the left). It figures that my demonstration sail would be the sloppiest of any I've made so far, but I hope the idea comes across. And, as above, this sort of things fades away when the sail is placed in the full context of a rigged model.
I'm quite happy with this method. I've now made all six of the sails for my topsail schooner this way and feel that they have a strong visual interest and a realistic (if not perfectly accurate) appearance. Moreover, the method uses cheap material that's easy to work with, and requires no special skills other than some patience and care when handling glued paper. It's easy to test on random scraps first before trying a full sail, and it's easy to customize. For example, you could skip the panels and just use a full sheet of paper, or skip the boltropes, and still use the rest of the approach to have a nice sail that holds it shape and can even be shaped to hold a curve. I hope others find some or all of this interesting and useful as a different way to produce interesting sails for nautical models. Thanks for reading.
-
Estoy_Listo reacted to David Lester in Rope Hanks Conquered!
I have always struggled making rope hanks. I've tried every method I can find on this forum and on YouTube, but it always boils down to the same problem. Every method seems to work for me until that point at the end when it calls for "a small dab of glue." Well, for me diluted PVA glue never seems to hold and a small dab of CA glue never seems to hold the whole thing together either. So I end up using enough glue to hold everything together, but the result is usually the glue wicking into the line, darkening and hardening it and it generally looking terrible. The best I have ever been able to do is to try to minimize this effect, which means that at least half of the hanks I make for every model end up in the garbage and I'm only somewhat happy with the ones I do use.
So here is the result of my experimenting yesterday and I think it just might be a good solution to my problem. I was trying (for the umpteenth time) the method outlined by Tom Lauria in his YouTube video. I was having the best luck with this method of any of the others I've tried, but still having the glue problem at the end, so here's how I adapted his method to try to avoid the glue problem.
I wrapped the line five times around three nails - two at the top, with a narrow space between them and one at the bottom. The distance apart is the length I need excluding the loop that goes over the belaying pin; in this case 3/8".
Tom outlines a perfect oval with a series of closely spaced nails, but I found it's not necessary to do that. The hank comes out more or less the same with the three nails as it does with several. Many methods only use two nails anyway, one top and bottom. However I found it necessary to have a space at the top, hence two nails at the top.
Then I wrapped a length of matching sewing thread around the coils at the top and tied a knot. I'm not worrying about the loop for the belaying pin at this point. This knot around the coils ensures that they will not come apart and it's actually easy to get a small dab of CA glue on this knot without touching the main line. The glue only has to hold the knot; the thread is holding the coils.
When the CA glue was set in a couple of moments, I trimmed the threads off, leaving just the knot.
Then I pulled one of the long ends of the line underneath the coil at the top and up through the centre -
Made a loop out of it and pulled the end back through underneath the coil at the top -
And then, just like Tom Lauria did, I secured the loop with a drill bit in a previously drilled hole and pulled the loop snug against the drill bit -
Here I took a length of matching sewing thread in a needle and stuck in down through the middle of the line on one side of the loop and through, at least part of, the coil below -
Then I transferred the needle to the other end of the sewing thread and did the same thing on the other side of the loop -
This ensures that when I tie the two ends together, the knot will be on the back of the hank -
Then I just tied the sewing thread into a knot on the back side of the hank. Just like before it's easy to put a small dab of CA glue on this knot without touching the main line.
When the CA glue sets, it's just a matter of trimming off all the lines -
This hank cannot come apart because the coils are tied together in a bundle and the loop for the belaying pin is sewn directly to the hank. There's no glue visible on the surface and the sewing thread is completely invisible. I think this is the best hank I've ever made and the process didn't end up with the garbage men wondering "what's with all the gluey coiled thread coming out of this house?"
So that's my good news for this weekend.
Happy Thanksgiving to the Canadians out there! ( or should I say "Happy Hanksgiving?")
David
-
Estoy_Listo got a reaction from Sam A in BlueJacket Shipcrafters Lobster Boat: A Review
Thanks for an excellent review. I learned a lot from it. I saw your lobster boat earlier, nice build, great colors.
-
Estoy_Listo reacted to wefalck in How to seize a block to an iron band
I would recommend to ignore instructions in kits - sometimes they are good, sometimes they are bad, but in most cases they provide simple solutions that are often far from what the real thing would have looked like.
The guys of old knew what they were doing and their methods have been tested and refined over the centuries. So, within the limits of materials availability and your own capabilities, it is always a good idea to follow prototype practice as closely as possible.
Perhaps also a word of clarification: 'seizing' means to attach something with a thin rope, similar to sewing. This is not normally done with blocks at all ! What you are interested in is 'stropping', which consists of making a loop of rope and putting it closely around items such as blocks or also spars. These strops are usually tightened with the help of 'seizing', but the seizings go around the rope, not around blocks or spars.
I am not an expert on 18th century rigging, but have the strong feeling that the kit instructions are not quite correct. The masts on such 'long-boats' are rigged only temporarily and were easy to strike. In the 18th century wrought-iron bands with eye-bolts were not very commong and I would not expect such fitting on a relatively thin mast as that of the long-boat. It would have been more likely that the mast was provided with shoulders at the locations, where the standing rigging would attach and where any blocks would attach. A spliced strop would fit tighly around the mast and block forming a figure of eight, being tied down in the middle with a seizing.
It is quite easy to form such strops from rigging thread (or better real 'rope') using a fake splice, i.e. pushing the ends through each other with the help of a sewing needle. The fake splice then is secured with a drop of varnish. With a much thinner thread you tie the strop to a figure of eight going around the block and the mast. The whole thing then is secured again with a drop of varnish.
Such an arrangement would also prevent the eye sticking too far out as in the kit instructions.
-
Estoy_Listo got a reaction from Knocklouder in Sea of Galilee Boat by LyleK1 - FINISHED - SE Miller - 1/20 scale
I've read a lot of build logs, Lyle; but I've never seen one with a better ending.
-
Estoy_Listo got a reaction from Spellapeaka in Sea of Galilee Boat by LyleK1 - FINISHED - SE Miller - 1/20 scale
I've read a lot of build logs, Lyle; but I've never seen one with a better ending.
-
Estoy_Listo got a reaction from EricWilliamMarshall in Oxford Companion to Ships and the Sea
This book is mentioned elsewhere in the forum, but it wasn't until I was snooping through my party host's bookcase that I discovered this gem. What a book! 3700 articles arranged from Aalesun, a seaport on the Norwegian coast, to Zulu, a type of fishing vessel peculiar to the NE coastal ports of Scotland. (We learn here, among much else, that carvel hull had a pronounced rake and that they were rigged w/ a dipping lug foresail and a standing lug mizzen. The model pictured in the book is a beauty.)
Copyright 1988. High quality paper, crisp text, with binding that makes it a pleasure to hold. Bought it used online from you-know-who.Com. $4.99.
Can you beat that?
Merry Christmas, all
-
Estoy_Listo got a reaction from Louie da fly in Sea of Galilee Boat by LyleK1 - FINISHED - SE Miller - 1/20 scale
I've read a lot of build logs, Lyle; but I've never seen one with a better ending.
-
Estoy_Listo got a reaction from LyleK1 in Sea of Galilee Boat by LyleK1 - FINISHED - SE Miller - 1/20 scale
I've read a lot of build logs, Lyle; but I've never seen one with a better ending.
-
Estoy_Listo reacted to LyleK1 in Sea of Galilee Boat by LyleK1 - FINISHED - SE Miller - 1/20 scale
Well, between a busy month of August and a minor health issue for my dad, I was late in delivering his gift.
All is well and he finally received it over the weekend:
I caught him completely off guard! And he was very surprised!
That will conclude this build log!
-
Estoy_Listo reacted to LyleK1 in Sea of Galilee Boat by LyleK1 - FINISHED - SE Miller - 1/20 scale
Thanks Chuck, Steven, Moab and Tom.
Appreciate your stopping in from time to time and your comments.
Looking forward to dad's birthday!
Stop by my Bounty log!
-
Estoy_Listo reacted to Louie da fly in Sea of Galilee Boat by LyleK1 - FINISHED - SE Miller - 1/20 scale
Beautiful work, Lyle.
Steven
-
Estoy_Listo reacted to Chuck Seiler in Sea of Galilee Boat by LyleK1 - FINISHED - SE Miller - 1/20 scale
Lyle,
Looking good. I like the finish.
The excavation report indicates that there may have been floor boards/deck boards as you have modeled. Floor boards were not found with the wreck, but this is easily explained since they would have been salvaged before the boat was abandoned.
-
Estoy_Listo reacted to LyleK1 in Sea of Galilee Boat by LyleK1 - FINISHED - SE Miller - 1/20 scale
Getting down to the nitty-gritty!
Stern cap installed:
Mast work is pretty simple on this build. The mast was preformed and required nothing except sanding and a couple of holes drilled near the top to handle the rigging later on. I added a halyard cleat to the aft side of the mast. I made it out of walnut because every time I tried making it with the stock wood, it would split! After the fourth one... I switched wood!
I also added the mast step and used a piece of brass rod to ensure a solid joint:
And then glued it into place. On my build, I measured forward 7.5 inches from the stern and cut away some of the partial ribs to make room for the mast step and mast. Double-checked the alignment on both axis:
Any minor adjustments can be done with the rigging. But actually it's pretty well aligned.
Mast done!
Looking at another build log awhile back, I saw some deck boards that I think would have been appropriate for the time period and the boat. I decided to use a similar pattern but maybe a bit more primitive than his work. If I can find it again, I'll give credit.
Used some Basswood just for a bit of change for the deck:
Time for a coating of the finish. I followed the advise of the kit designer and used Amber Shellac. I've never worked with it but found it to be really easy to use:
I like the look and after some rubbing with steel wool, I like it even more!
Now that the main structure is done, it's time to get busy on the bits and pieces:
Pictured above are the oars, rudders, seats, oar locks and davit pieces. I started by sanding all the pieces and then went on to assembly the 4 oar locks:
Some shaping with a round file and these will be ready for a little touch-up sanding and shellac and then be ready to install.
Work continues tomorrow and through the weekend!
-
Estoy_Listo reacted to LyleK1 in Sea of Galilee Boat by LyleK1 - FINISHED - SE Miller - 1/20 scale
Thanks Chuck! I’m pleased with look of the model.
I’m sure yours will be beautiful!
I just finished the cap rail… done for the night:
-
Estoy_Listo reacted to Louie da fly in Sea of Galilee Boat by LyleK1 - FINISHED - SE Miller - 1/20 scale
Beautiful work, mate!
Steven
-
Estoy_Listo reacted to LyleK1 in Sea of Galilee Boat by LyleK1 - FINISHED - SE Miller - 1/20 scale
Lots accomplished over the last few days...
I finished the ribs. I found it to be very difficult to bend some of the ribs in the sharper corners near the bow and stern. Since they will be covered by the decks, I gave them less worry below the deck line. Overall, a tedious task working with 1/8 x1/8 wood:
The inner wales were next. I let the pieces soak in hot water for about an hour before bending them by hand... no heat. The bend was not sharp and actually shaped easily. I used clamps and made sure the wales were in the right position along the entire length of the hull. Once the inner wales were in place and still wet, I clamped them down ensuring that they touched each rib at the top and bottom. Once dried, I used the the thin CA glue and glued them in place while still clamped, resulting:
The cutwater was a bit of a conundrum for me. There are no real instructions that were helpful on this part of the build. Fortunately, I found a couple of pictures and build logs that gave me a good view and idea of what I needed to make. It started with several 1/4 x 1/4 wood pieces glued together:
I laid the bow down and used my pencil to trace the curvature of the bow. The pieces were glued together to match the curve. I used my scroll saw and cut the shape out and then cut the leading edge. Finally, I sanded and glued it onto the bow:
Still need to sand the cutwater at the keel flat to properly receive the false keel but I am really pleased with the outcome!
Next, deck beams were installed at the bow and stern:
And the decking begins... simple but a little work to cut around the ribs:
Finally:
Some sanding on the end to even up the deck ends... I decided that I wanted a more finished look. So, I cut pieces to put between the ribs and then placed a piece of trim around the hull. Also added an end cap to the deck:
A better look to me... what do they call it........ artistic freedoms! Hopefully, not too far off base!
The fore deck, cap rails and the false keel are next!
-
Estoy_Listo reacted to LyleK1 in Sea of Galilee Boat by LyleK1 - FINISHED - SE Miller - 1/20 scale
Half the ribs done:
A month and five days until dad's birthday! Gotta get busy!
Summer makes it harder to work... boating, gardening, etc!
Still think I can make it without having to rush.
-
Estoy_Listo reacted to LyleK1 in Sea of Galilee Boat by LyleK1 - FINISHED - SE Miller - 1/20 scale
The next several planks need to be carefully bent/twisted and sanded to meet the very sharp curve of the hull.
As I mentioned above, this wood is much softer than what I'm working with on the Bounty (Walnut). It's very easy to shape. Especially, if you soak it a few minutes. I used my hands to make the bends and twists. Once the shape is close, I beveled the edge butting into the next plank by sanding. Also, I'd clamp the plank to the forms to let it completely dry while clamped in place.
Here's a few pictures of the progress:
It has taken a lot of clamps to hold the shape while the glue dries. Making the turn to bottom of the hull is quite sharp.
Gonna try to get out on the big boat this weekend!
So, I'll get back to this next week.
BTW, I just finished reading the book mentioned in the first post of this log.
If you're interested about the possible histories of this boat and the region in general, it's worth the read. I enjoyed it and gained a lot of insight on the history too.
-
Estoy_Listo reacted to Jaager in Clear Shellac Sanding Sealer
I think of sanding sealer as being a thick product. Useful on open pore wood like Black Walnut, Oak, and A finish plywood to fill the pores and give a smooth even finish. Intended more for full size furiture.
Shellac is an excellent traditional finish. It can be as thick or thin as you wish. It is not good for applications where it can come in contact with water. It hydrates and turns white. It can be easily repaired, but do not use it to finish a coffee table.
A shellac finish can be removed with alcohol.
The material can be preextracted and purified and comes as Orange (probably straight from the beetle) to Super Blonde - almost water clear. The solvent is alcohol (methyl, ethyl, 2-propanol, probably propanol if you can find it). You can buy it in flakes and make up your own solution as needed. The more purified are the flakes, the lower the maximium concentration you can make. The impurities increase solubilitiy in alcohol. The more volatile is the alcohol (Me>Ethyl>Prop) the less working time if you are using a cloth for application. Dilute shellac is a good first coat for most any other finish. It is very compatible with other finishes. French polish seems to be multiple layers of shellac applied with a cloth that has a bit of Linseed oil in the cloth. I would guess that Tung oil or Walnut oil might work as well.
-
Estoy_Listo reacted to Bill Hime in Clear Shellac Sanding Sealer
I think shellac has a nice antique feel and look to it. I think I would lightly sand the finish coat and apply a good wax. IMO,oil would tend to attract dust and be difficult to clean on the details of a model.
Sincere Regards,
Bill
-
Estoy_Listo got a reaction from Blackreed in Skiff by dcicero - FINISHED - Bluejacket Shipcrafters - 1:12
Sweet build: simple and elegant; featured as the "Model of the Month" in Blue Jacket's monthly newsletter.