-
Posts
4,364 -
Joined
-
Last visited
About Egilman
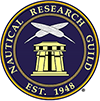
- Birthday 07/11/1957
Profile Information
-
Gender
Male
-
Location
The Great Pacific NW
-
Interests
Computing, Historical Research, Model Building
Recent Profile Visitors
-
Egilman reacted to a post in a topic: Fordson N roadless tractor by RGL - Plus Model - 1/35 - RESIN
-
Egilman reacted to a post in a topic: D-51 Slug Type Locomotive by Greg Davis - Arii / Micro Ace - 1/50
-
Egilman reacted to a post in a topic: Fordson N roadless tractor by RGL - Plus Model - 1/35 - RESIN
-
Egilman reacted to a post in a topic: Fordson N roadless tractor by RGL - Plus Model - 1/35 - RESIN
-
Egilman reacted to a post in a topic: Woodwork/Model making workshop by Charter33 - FINISHED - Scale 1:1
-
Egilman reacted to a post in a topic: Woodwork/Model making workshop by Charter33 - FINISHED - Scale 1:1
-
Egilman started following Non-ship/categorised builds
-
mikegr reacted to a post in a topic: A34 Comet by king derelict - FINISHED - Vespid - 1/72 - PLASTIC
-
mikegr reacted to a post in a topic: A34 Comet by king derelict - FINISHED - Vespid - 1/72 - PLASTIC
-
Canute reacted to a post in a topic: A34 Comet by king derelict - FINISHED - Vespid - 1/72 - PLASTIC
-
AJohnson reacted to a post in a topic: A34 Comet by king derelict - FINISHED - Vespid - 1/72 - PLASTIC
-
Old Collingwood reacted to a post in a topic: A34 Comet by king derelict - FINISHED - Vespid - 1/72 - PLASTIC
-
Hey Brother, Tank Tracks? Painting.... A long sinuous discussion track... First off, what you paint them depends... Yes it depends on when in the tanks life you want to represent... A new on the ramp tank, a recently issued tank, (Baker gave you a GREAT shot of a recently issued tank, which means original manufacturers tracks) or an old road or battle worn veteran tank... They all look different.. A new tank on the delivery ramp? Same color as the tank with bare metal cleat bottoms.... A new issued tank just out on manuevers? As I said, Baker gave you an exemplar photo... Perfect, the sprocket ends show the same color as the tank, the track bodies have picked up a coating of dust and the Cleats have almost worn off the initial paint coat on their bottoms showing plain steel.... Perfect for a well maintained or newly issued tank... A note: Tank tracks wear out quickly... One of the major supply issues with tanks is not only fuel and ammo, but replacement tracks... Especially in WWII, all metal tracks were painted in their tanks base color... For a British tank would be British Army Green... A battle worn tank? I would start by black basing the track overall then using dry brushing and washes bring out the rust browns and dirt browns remembering to leave patches of the green showing, for a tank that has really seen the muck then you can go the mucky dirty look with hard basing some kind of medium on the track to show the lumps then the browns and greys to represent the colors of muck... the world of track painting is just as varied as WWII camuflage, get a few decent color pics and experiment until you gat the look you like... Backer's pic of the late war newly deployed Comet is priceless in this regard... Personally I would go with it.... EG
-
Gloster Meteor F8 by AJohnson - Airfix -1/48- PLASTIC
Egilman replied to AJohnson's topic in Completed non-ship models
Well they tested them in an F8, that's why I said generally... which is true.. But as always, there are exceptions to general rules... Elmer -
Gloster Meteor F8 by AJohnson - Airfix -1/48- PLASTIC
Egilman replied to AJohnson's topic in Completed non-ship models
ARI 5849 or Rebecca Mk.7. (also known as TANCAN) you will find them on Meteors F13 & 14's late in their lives... I believe it was a radar homing device of some type.... They were tested in a Meteor Mk.8 in 1953.... https://apps.dtic.mil/sti/tr/pdf/AD0020257.pdf Note the transmitting antenna on the bottom of the fuselage as well.. You will also see these on Vampire T11's as well... EG Also note: F8's generally didn't carry them.... -
F-84G by Javlin -Tamiya - 1/48 - PLASTIC
Egilman replied to Javlin's topic in Completed non-ship models
Future/Pledge also needs a wet coat brother, on everything/place your going to put it... So plan on complete coverage and do your setup accordingly... It dries very thin so the only real complication is handling run off... (thinned wet coats tend to run) What I do is keep a pile of absorbent material next to where I'm clear coating and when the future runs enough to start collecting on the low spot, touch it to the absorbent material to wick off the excess... You only want the droplet that forms to touch the wick, do not allow the surface to touch otherwise you will have a touch up to do... Definitely needs a wet coat to work properly... EG -
Modular layouts have been around for about 70 years, and yes it is the way to go when building larger layouts... And OSB, (oriented strand board) makes a great foundation for a layout... Doesn't have to be perfect and is almost as strong as plywood... (besides being about a third the cost of good plywood) Nice progress, watching with interest... EG
-
Usually they have a platform that allow the grain to be shoveled off the wagons into a hopper that gravity feeds the elevator... The elevator, (think bucket chain hoist) lifts the grain into the top of the silo which is gravity fed into the hopper cars when loading the train... The doors, (usually two) were there for elevator chain replacement, these elevators were used continuously during harvest season 24/7... The chain lifts would wear out in a single season in an area of large farms... There was equipment in the machinery room to effect the swapping of the lift chains, and it could be done in two days... They would actually use grain loaded in the buckets to balance the weight so it was a simple low tech hand operation to change them... Otherwise, the doors remained closed at all times.... This is why you don't see them open in period pics... (usually taken during harvest season when the elevator is in operation) EG
-
BR-18 Locomotive by Greg Davis - OcCre - 1/32
Egilman replied to Greg Davis's topic in Non-ship/categorised builds
They were flush riveted on the boiler plates, the bands reinforced & covered the riveting.... They were also built during the end of WWI thru approximately 1928 in several variations.... There is one still in operation today... Plate arc-welding as a manufacturing process didn't come into use until 1932, and even at that time was limited to the shipyards building warships... It's became widespread during WWII... -
You know, they lived with it on the real car... The door windows were plexi on the real car and the parts for the slider were as well just glued together... The rivets were for reinforcement... A few minor scratches adds to the authenticity... This is my opinion of course, but they are there on the real thing... Absolute fact... So, nothing to be sad about, an inadvertent detail added by accident, but very very realistic... (especially since you have to be on top of it to see them) Perfection I say... EG
-
You know, I've been debating whether I should mention this or not... The idea is to scale down the car, NOT scale up the lumber it's sitting on... Where on god's green earth you obtained in scale metal flake blue paint? They don't make such an animal... So you see my point.... So please stop scaling up the wood... {chuckle} It confuses us.... EG PS: very nicely done Brother... VERY VERY NICELY DONE...
-
The X1C and it's clones are a tool... fire and forget, load your file and print right out of the box... They are so good that both Anycubic and Prusa cloned it... It's the future of FDM... Resin still has it's place, but for some things FDM is now the turn to....... This is an excellent project YES, and I don't want to take it off course, if you want to discuss it, hit me up with a PN brother... Gladly share what I know... EG
-
Ron, Brother, FDM printing has come a long way in the last few years... My X1C will produce parts that are just as smooth as most Resin printers... I suspect the Clones by Anycubic and Prusa will as well... I've actually gotten bead lines from the X1C at .007" off the build plate... Structural parts like he's proposing are no longer the private purview of SLA printers, they can be readily printed on a filament printer.... That's at 1/72 scale from a Bambu labs X1C.... That part in the upper right corner of the pic is the cowling section of the nose part for a '77 Pontiac Freeway Enforcer (Buford T Justice's car) printed off the X1C at 1/25th scale in ABS... Resin isn't the only option for fine details anymore...
About us
Modelshipworld - Advancing Ship Modeling through Research
SSL Secured
Your security is important for us so this Website is SSL-Secured
NRG Mailing Address
Nautical Research Guild
237 South Lincoln Street
Westmont IL, 60559-1917
Model Ship World ® and the MSW logo are Registered Trademarks, and belong to the Nautical Research Guild (United States Patent and Trademark Office: No. 6,929,264 & No. 6,929,274, registered Dec. 20, 2022)
Helpful Links
About the NRG
If you enjoy building ship models that are historically accurate as well as beautiful, then The Nautical Research Guild (NRG) is just right for you.
The Guild is a non-profit educational organization whose mission is to “Advance Ship Modeling Through Research”. We provide support to our members in their efforts to raise the quality of their model ships.
The Nautical Research Guild has published our world-renowned quarterly magazine, The Nautical Research Journal, since 1955. The pages of the Journal are full of articles by accomplished ship modelers who show you how they create those exquisite details on their models, and by maritime historians who show you the correct details to build. The Journal is available in both print and digital editions. Go to the NRG web site (www.thenrg.org) to download a complimentary digital copy of the Journal. The NRG also publishes plan sets, books and compilations of back issues of the Journal and the former Ships in Scale and Model Ship Builder magazines.