-
Posts
1,196 -
Joined
-
Last visited
About Stuntflyer
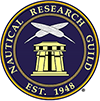
- Birthday 07/23/1944
Profile Information
-
Gender
Male
-
Location
Mount Vernon, NY
Recent Profile Visitors
-
Stuntflyer reacted to a post in a topic: Mayflower by Tigersteve - Model Shipways
-
Stuntflyer reacted to a post in a topic: Mayflower by Tigersteve - Model Shipways
-
FrankWouts reacted to a post in a topic: HMS Winchelsea by Greg M - 1/48 scale
-
dvm27 reacted to a post in a topic: Sloop Speedwell 1752 by sfotinos - Syren Ship Model Company - 1:32 Scale - POF Sloop
-
FrankWouts reacted to a post in a topic: Sloop Speedwell 1752 by Chuck - Ketch Rigged Sloop - POF - prototype build
-
Stuntflyer reacted to a post in a topic: Sloop Speedwell 1752 by Chuck - Ketch Rigged Sloop - POF - prototype build
-
Stuntflyer reacted to a post in a topic: Sloop Speedwell 1752 by Chuck - Ketch Rigged Sloop - POF - prototype build
-
Stuntflyer reacted to a post in a topic: HMS Bellona 1760 by SJSoane - Scale 1:64 - English 74-gun - as designed
-
Stuntflyer reacted to a post in a topic: Sloop Speedwell 1752 by baribeaujm (Jean-Marc) - Syren Ship Model Company - 1:32 Scale - POF Sloop
-
Stuntflyer reacted to a post in a topic: HMS Winchelsea 1764 by Frank Wouts 1/48
-
Stuntflyer reacted to a post in a topic: HMS Bellona 1760 by SJSoane - Scale 1:64 - English 74-gun - as designed
-
Stuntflyer reacted to a post in a topic: HM Cutter Cheerful 1806 by Erik W - 1:48 scale
-
Stuntflyer reacted to a post in a topic: Sloop Speedwell 1752 by baribeaujm (Jean-Marc) - Syren Ship Model Company - 1:32 Scale - POF Sloop
-
FrankWouts reacted to a post in a topic: HMS Bellona 1760 by SJSoane - Scale 1:64 - English 74-gun - as designed
-
GioMun reacted to a post in a topic: Sloop Speedwell 1752 by Stuntflyer (Mike) - Ketch Rigged Sloop - POF
-
GioMun reacted to a post in a topic: Sloop Speedwell 1752 by Stuntflyer (Mike) - Ketch Rigged Sloop - POF
-
tmj reacted to a post in a topic: The Hayling Hoy by jpalmer1970 - 1:48 scale - First POF build
-
daHeld73 reacted to a post in a topic: HMS Bellona 1760 by SJSoane - Scale 1:64 - English 74-gun - as designed
-
altor reacted to a post in a topic: The Hayling Hoy 1760 by Stuntflyer (Mike) - 1:48 scale
-
daHeld73 reacted to a post in a topic: HMS Bellona 1760 by SJSoane - Scale 1:64 - English 74-gun - as designed
-
I have a few sources for the case that I want to use on Cheerful. They offer a plexi box with a round over across the top length of the box. Thanks reweir, Bob and Tigersteve for that. https://www.ttplasticland.com/products/acrylic-display-case# https://pkcustomacrylics.com/ Any suggestions on what the overall dimension of the box should be? The ship dimensions are L 29.5", W 12.5", H 27"
-
I have a few sources for the case that I want to use on Cheerful. They offer a plexi box with a round over across the top length of the box. Thanks reweir, Bob and Tigersteve for that. https://www.ttplasticland.com/products/acrylic-display-case# https://pkcustomacrylics.com/ Any suggestions on what the overall dimension of the box should be? The ship dimensions are L 29.5", W 12.5", H 27"
- 452 replies
-
- cheerful
- Syren Ship Model Company
-
(and 1 more)
Tagged with:
-
Wasn't quite sure where to post this question. Does anyone know where I could purchase a plexi box case that has rounded edges across the top of the case? Basically it's one piece of plexi for the front, top and back. Two separate pieces for the other two sides. I had two sources that are now no longer in business. Thanks, Mike
-
Beautifully done, Ben and a very unique build as well. Love the case too. Mike
- 399 replies
-
- winchelsea
- Syren Ship Model Company
-
(and 1 more)
Tagged with:
About us
Modelshipworld - Advancing Ship Modeling through Research
SSL Secured
Your security is important for us so this Website is SSL-Secured
NRG Mailing Address
Nautical Research Guild
237 South Lincoln Street
Westmont IL, 60559-1917
Model Ship World ® and the MSW logo are Registered Trademarks, and belong to the Nautical Research Guild (United States Patent and Trademark Office: No. 6,929,264 & No. 6,929,274, registered Dec. 20, 2022)
Helpful Links
About the NRG
If you enjoy building ship models that are historically accurate as well as beautiful, then The Nautical Research Guild (NRG) is just right for you.
The Guild is a non-profit educational organization whose mission is to “Advance Ship Modeling Through Research”. We provide support to our members in their efforts to raise the quality of their model ships.
The Nautical Research Guild has published our world-renowned quarterly magazine, The Nautical Research Journal, since 1955. The pages of the Journal are full of articles by accomplished ship modelers who show you how they create those exquisite details on their models, and by maritime historians who show you the correct details to build. The Journal is available in both print and digital editions. Go to the NRG web site (www.thenrg.org) to download a complimentary digital copy of the Journal. The NRG also publishes plan sets, books and compilations of back issues of the Journal and the former Ships in Scale and Model Ship Builder magazines.