
clarkt
NRG Member-
Posts
53 -
Joined
-
Last visited
About clarkt
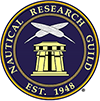
- Birthday 09/13/1948
Profile Information
-
Gender
Male
-
Location
Astoria, Oregon
-
Interests
history, reading,
Recent Profile Visitors
-
clarkt reacted to a post in a topic: Footropes, Flemish Horses and Stirrups
-
thibaultron reacted to a post in a topic: A bit of research into navy warship paint 1775-1815
-
Linus Spjutsberg reacted to a post in a topic: A bit of research into navy warship paint 1775-1815
-
uss frolick reacted to a post in a topic: Unusual wood used in model building
-
druxey reacted to a post in a topic: Unusual wood used in model building
-
grsjax reacted to a post in a topic: Unusual wood used in model building
-
clarkt reacted to a post in a topic: Framing Gun Ports - USF Essex - Model Shipways
-
Ryland Craze reacted to a post in a topic: Rope serving machine
-
Knocklouder reacted to a post in a topic: Rope serving machine
-
I've had the Serv-o-matic for a few years, now and use it often. I was surprised how easy it was to get good results.
-
Canute reacted to a post in a topic: pin vise and drill bits
-
Ryland Craze reacted to a post in a topic: pin vise and drill bits
-
palmerit reacted to a post in a topic: pin vise and drill bits
-
The best source for numbered , very small bits I've found is Pan American Tool Corp. (https://www.panamericantool.com/?srsltid=AfmBOoplf2XnA9dfRlNIRURelQxlEWf62EiS9mcYw94EGpbstN0N6A4) But I mostly use the carbide bits from the electronics industry, available from Amazon and others, in the Dremel flexshaft and drill press. It's true they break easily, but they don't cost very much, work better than the ordinary bits and don't wobble when mounted in the drill press That set of pin vises seems pretty expensive. Rio Grande, https://www.riogrande.com/?srsltid=AfmBOopFq7WQdEg-QU2eeaqm3EfZdG7B5DlhxjtTsZD61lKD-Zv2c5Ni has several for a lot less. As for other tools, a broken bit can be ground on an angle and mounted in the pin vise to make a mini chisel, great for forming the sheave on a small block. a broken carbide bit can be used in the same way to make a reamer.
-
I agree with Bill Hudson about Gilmer Wood in Portland. They are aware of modeler's needs, are knowledgeable and easy to work with.
-
clarkt reacted to a post in a topic: Where to buy wood
-
clarkt reacted to a post in a topic: To varnish copper plates or not to varnish?
-
Need AL HMS Bounty rigging instructions
clarkt replied to Willem Basson's topic in Wood ship model kits
I used the book "The Armed Transport Bounty" by John McKay from the Anatomy of the Ship series to rig my model of Columbia Rediviva, a similar vessel. It is quite detailed; better than other AOTS books. -
Laser cutting services?
clarkt replied to Jsk's topic in CAD and 3D Modelling/Drafting Plans with Software
I have also wondered about custom laser cutting, but of sheet brass rather than wood. I'm thinking particularly of preventer links for the chains (on deadeyes) and swivel gun yokes. But if I was making an order I could probably think of other parts. Are such services available? -
Looking for plans or possible models of Magellan's ships.
clarkt replied to J11's topic in Nautical/Naval History
I built a model of Victoria, based largely on the plans for Santa Maria in Xavier Pastor's "Ships of Christopher Columbus" in the Anatomy of the Ship series, but with some significant alterations. According to my research, the stern construction had changed from the "stern tuck" to a transom style. There was a substantial main topsail and a fore topsail. (Elcano's log records that the fore topsail was carried away off the coast of West Africa on the last leg of the circumnavigation.) The ships had cressets, rather than lanterns on the stern. A boat on the Victoria normally had a crew of twelve. These are some of the best items I found while researching the ship, in S. E . Morison"s "The Great Explorers," J. H. Parry's "The Age of Reconnaissance" (Parry has written several good books on the subject,) Joseph Wheatley's "Historic Sail," and many others. I also read the Pigafetta account but it has virtually no information about the ships. Of course, there is a lot of conjecture but you can make a reasonable representation and learn a lot about the ships in the process. -
You might try using the Sculpy to make a "maquette," to get an idea of how your figure will look and to become familiar with the body proportions. Then make the piece out of boxwood. David Antscherl describes the process very well in The Fully Framed Model, HMN Swan Class Sloops 1767-1780, Vol. II, pp 243 to 255. I think the Sculpy is too gooey to make a finished piece that you will want to display. I also tried to shape a piece of Corian countertop material, thinking that it would be easier with no wood grain issues, but it was too hard and didn't work well. The boxwood is, of course, great to work with. While it is a difficult project, the results can be rewarding. All this at 1:48 scale. Smaller might be unrealistically challenging, although I'm sure it's been done.
-
Phoenician ships were known to be, at least partially, black. They had the great good fortune to have access to natural (petroleum ) tar, still a good sealant, if you have nothing else. I think paint in the early days of sailing was used solely to change color and add decoration. At some point, as quality improved, they realized that it could also seal the wood against the deteroriating effects of the weather and seawater. It would be natural for captains to protect whatever they could, that way, and I imagine that some went pretty far with the technique. The idea of painting anything not moving, I believe, came along with the all steel ships.
-
Santa Maria detailed rigging plans needed
clarkt replied to Richard Moise's topic in Wood ship model kits
The Anatomy of the Ship series book The Ships of Christopher Columbus by Xavier Pastor has a fairly comprehensive rigging plan for Santa Maria, although any plan from this period has got to be speculative. It would probably be worth it to use more than one source. -
The corded Dremel was one of the first tools I got when I started building models and I still use it almost every day. It is hung from the ceiling along with a flex shaft. I use most of the same bits and heads as Mr. Bordelau shows in his post, especially drill bits, mostly the carbide type, lately. I have thought of replacing it with a Foredom if the Dremel ever wears out. Still going strong after about 25 years. Also, the Dremel handpiece seems to be smaller and handier than any of the ones available from Foredom. A friend gave me a small rechargeable Dremel but it has no power at all.
About us
Modelshipworld - Advancing Ship Modeling through Research
SSL Secured
Your security is important for us so this Website is SSL-Secured
NRG Mailing Address
Nautical Research Guild
237 South Lincoln Street
Westmont IL, 60559-1917
Model Ship World ® and the MSW logo are Registered Trademarks, and belong to the Nautical Research Guild (United States Patent and Trademark Office: No. 6,929,264 & No. 6,929,274, registered Dec. 20, 2022)
Helpful Links
About the NRG
If you enjoy building ship models that are historically accurate as well as beautiful, then The Nautical Research Guild (NRG) is just right for you.
The Guild is a non-profit educational organization whose mission is to “Advance Ship Modeling Through Research”. We provide support to our members in their efforts to raise the quality of their model ships.
The Nautical Research Guild has published our world-renowned quarterly magazine, The Nautical Research Journal, since 1955. The pages of the Journal are full of articles by accomplished ship modelers who show you how they create those exquisite details on their models, and by maritime historians who show you the correct details to build. The Journal is available in both print and digital editions. Go to the NRG web site (www.thenrg.org) to download a complimentary digital copy of the Journal. The NRG also publishes plan sets, books and compilations of back issues of the Journal and the former Ships in Scale and Model Ship Builder magazines.