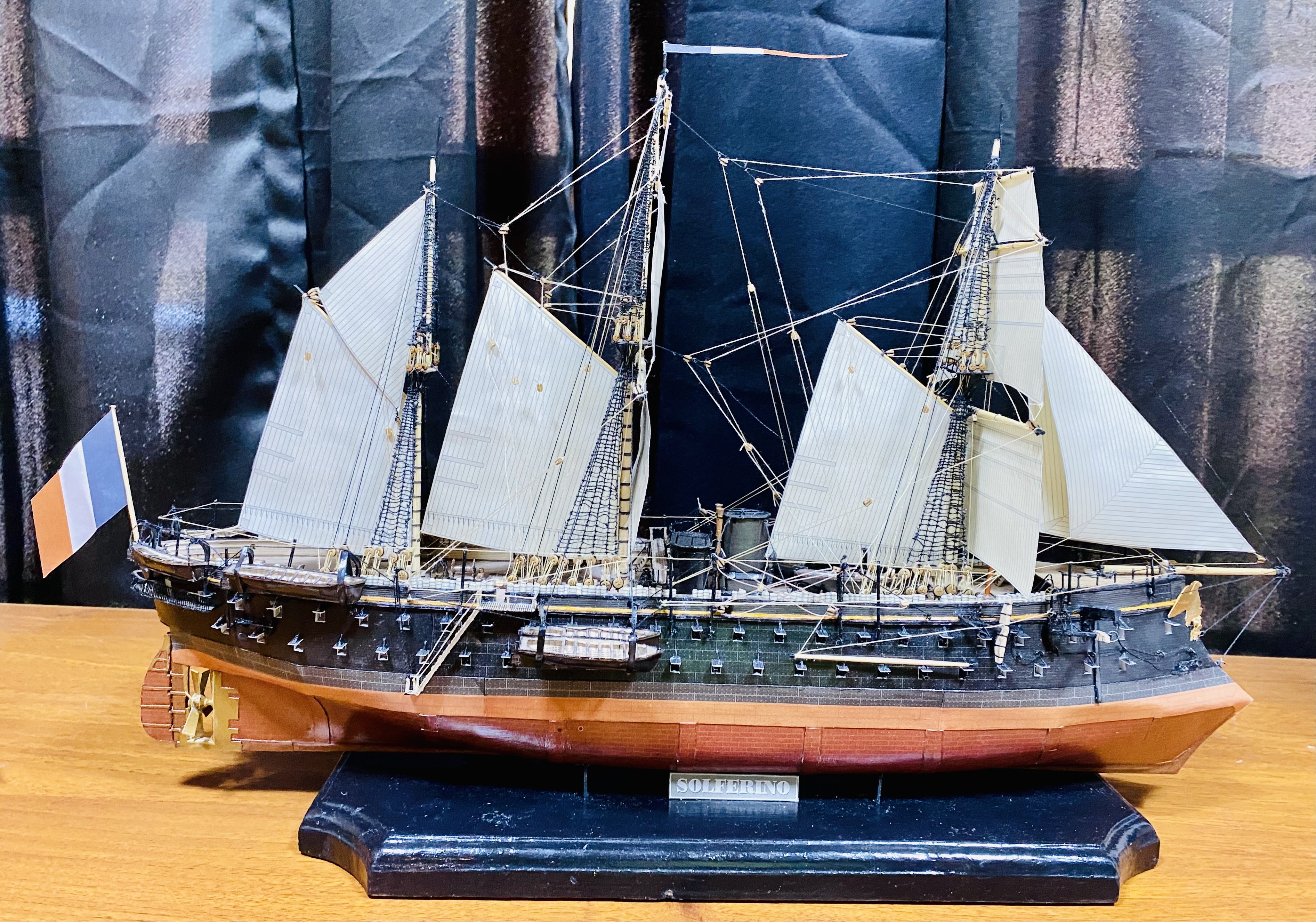
GrandpaPhil
NRG Member-
Posts
5,716 -
Joined
-
Last visited
Content Type
Profiles
Forums
Gallery
Events
Everything posted by GrandpaPhil
-
The lower hull is now assembled and ready to paint: The props are assembled too: I’m going to paint them also.
- 180 replies
-
- Card
- Pre-Dreadnought
-
(and 2 more)
Tagged with:
-
The Oryol is sitting in its cradle now: Working on the fittings for the lower hull before I seal and paint everything below the waterline. I’ll paint the cradle at the same time and then glue the ship to it.
- 180 replies
-
- Card
- Pre-Dreadnought
-
(and 2 more)
Tagged with:
-
Here’s the cradle: I modified the end pieces to fit the Oryol. It still needs painted, and will be painted a dark brown before being glued. I’m going to go with gloss black, like I did Solferino for the actual base. I like gluing my models to their bases for structural integrity reasons.
- 180 replies
-
- Card
- Pre-Dreadnought
-
(and 2 more)
Tagged with:
-
Glen, The Constitution is looking good! A set of ratlines usually takes me a week or two on a warship. I may or may not have been known to take a week of vacation specifically for tying ratlines, lol.
- 301 replies
-
- Constitution
- Bluejacket Shipcrafters
-
(and 1 more)
Tagged with:
-
Welcome!
-
Donald McKays GGGGreat Grandson
GrandpaPhil replied to Clan McKay's topic in New member Introductions
Welcome! -
Also, I feathered out the remaining lumps in the hull. There’s glue drying on the bottom where I made those repairs, so I’ll seal again tomorrow.
- 180 replies
-
- Card
- Pre-Dreadnought
-
(and 2 more)
Tagged with:
-
I used my light table for the first time tonight: I traced the cradle from my Orel Tsarevich. The Borodino-class battleships were direct derivatives of the Tsarevich so it stands to reason that they probably shared a similar hull shape. If not, I have a scalpel to reshape the cradles, lol. They are laid out on basswood from a basswood value pack that I got a while back.
- 180 replies
-
- Card
- Pre-Dreadnought
-
(and 2 more)
Tagged with:
-
Making progress on the lower hull: I still need to make a couple minor repairs then I’ll add the rest of the lower hull fittings and paint everything below the waterline. I really regret not doing this on Solferino so I’m not making that mistake again.
- 180 replies
-
- Card
- Pre-Dreadnought
-
(and 2 more)
Tagged with:
-
New Member - Some modeling experience
GrandpaPhil replied to Dave Wells's topic in New member Introductions
Welcome! -
Recommend Model Shipways kit to buy (with my new credit)
GrandpaPhil replied to palmerit's topic in Wood ship model kits
I really liked their kit of the Sultana. It’s a great intro to a lot of skill sets that you will use a lot of later on, and a good step up from the smaller boats. -
Thank you very much, OC! The lower hull is on: I filled the gaps so I can sand with some 220 grit sandpaper, seal and paint. The instructions are pretty vague and assume that you’ve done this before. They recommend not adding the bilges at this point, but don’t say when to, so I’m going to fully assemble the hull below the waterline and paint everything. I am also going to make a permanent cradle prior to adding the props and disassemble the temporary cradle. The cradle will be glued to the hull like I have done before to assist in handling the model. At that point I’ll also start prepping the actual base and move back above the waterline.
- 180 replies
-
- Card
- Pre-Dreadnought
-
(and 2 more)
Tagged with:
-
The decks are on: The lower hull covering is progressing: Those strips that Orel recommends putting on the two upper faux decks are working wonders for ensuring that there is plenty to glue to. They will also help with the appearance of armor bands later on. I adjusted my temporary stand to allow for the skin of the hull. I’ll make an actual cradle and permanently mount it to the base after I finish the lower hull fittings, which will be after I finish completely covering the hull, including the upper hull.
- 180 replies
-
- Card
- Pre-Dreadnought
-
(and 2 more)
Tagged with:
-
I made a temporary cradle: Using Legos for jigs and cradles is one of the things I learned about, on this forum. The Oryol sits relatively flat and level on the cradle. After skinning, I will probably modify the cradle and use it until I make an actual base for the Oryol. The forward most decks are on now:
- 180 replies
-
- Card
- Pre-Dreadnought
-
(and 2 more)
Tagged with:
-
All parts are sealed now. Found a few parts that I missed on the first round of laminating, so they’ll need to be laminated up and sealed on the back. Getting the first round of decks prepared: And fairing the hull for covering (as with all POB models). I am also going to add thin card strips to the bulkheads and faux decks to have more to glue the hull covering to.
- 180 replies
-
- Card
- Pre-Dreadnought
-
(and 2 more)
Tagged with:
-
The framework is pretty much done now: I believe that everything that needs laminated is now laminated. It is about time to seal all the parts in advance.
- 180 replies
-
- Card
- Pre-Dreadnought
-
(and 2 more)
Tagged with:
About us
Modelshipworld - Advancing Ship Modeling through Research
SSL Secured
Your security is important for us so this Website is SSL-Secured
NRG Mailing Address
Nautical Research Guild
237 South Lincoln Street
Westmont IL, 60559-1917
Model Ship World ® and the MSW logo are Registered Trademarks, and belong to the Nautical Research Guild (United States Patent and Trademark Office: No. 6,929,264 & No. 6,929,274, registered Dec. 20, 2022)
Helpful Links
About the NRG
If you enjoy building ship models that are historically accurate as well as beautiful, then The Nautical Research Guild (NRG) is just right for you.
The Guild is a non-profit educational organization whose mission is to “Advance Ship Modeling Through Research”. We provide support to our members in their efforts to raise the quality of their model ships.
The Nautical Research Guild has published our world-renowned quarterly magazine, The Nautical Research Journal, since 1955. The pages of the Journal are full of articles by accomplished ship modelers who show you how they create those exquisite details on their models, and by maritime historians who show you the correct details to build. The Journal is available in both print and digital editions. Go to the NRG web site (www.thenrg.org) to download a complimentary digital copy of the Journal. The NRG also publishes plan sets, books and compilations of back issues of the Journal and the former Ships in Scale and Model Ship Builder magazines.