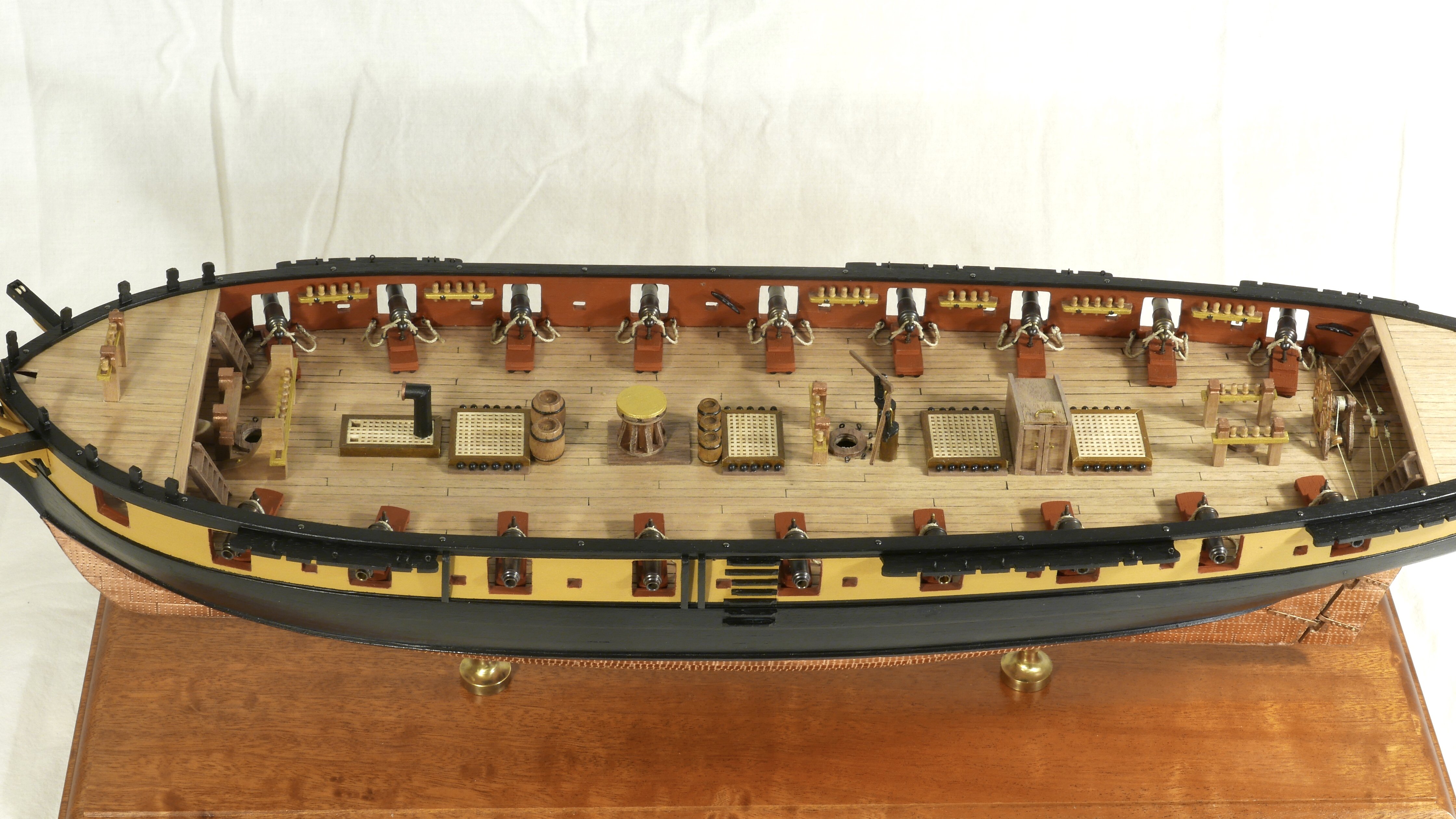
Mike_H
Members-
Posts
241 -
Joined
-
Last visited
Content Type
Profiles
Forums
Gallery
Events
Everything posted by Mike_H
-
I see you've painted the hull - and despite the excellent quality of your planking, I think that's the right decision. My alert, fully rigged, sits next to the shipyard, and seeing the contrast in the colours, alongside the exceptional scroll decorations brings me great joy. And isn't that what it's all about? Keep up the excellent work!
-
And so here she is, and probably finished! So, first of all some pics of the full rigging. The instruction book is pretty clear - though you have to combine the information for with, and without, sails. I used the sails exactly as supplied and rigged them all hauled tight. I am aware that sails are often not installed because first of all they are very hard to do accurately at scale, and also because they hide much of the work of the builder. As a modeller I accept both of those points, but feel they really are issues for the cognoscenti, the average slightly interested friend or family member will assume that a sailing ship should have sails. So, first for that reason, I rigged 'em. A secondary consideration is that the running rigging is literally superfluous if no sails are present, and in that regard having the sails has been a joy. The sails also speak to the whole purpose of these craft: they were very fast and very weatherly, carrying a truly prodigious area of canvas for such small craft And some details Shortly after I had rigged the square sail I realised that the tacks and sheets and the foot of the sail would not hang as they should so reflected on how to stiffen the sail athwartships. A stall at a Christmas market was selling florists wire for building wreaths, I bought a roll but it was shiny black. A few minutes of googling found the perfect refinement - white coated wire for sugar flowers. I was able to thread a wire - athwartships - through the hem along the foot of the sail. It works a treat in providing shape and stiffening. Sheets and tacks now run outboard as they should - though hardly along the graceful curves that they should. Given my time again I would think about stiffening along foot and leach of all the sails and perhaps more. But not this time. And a little reflection: She's a beautiful small vessel, showing a style quite different from the square-rigged ships we so often model from the late 18th and early 19th centuries. I think a single-masted rig should be on everyone's list to build and this kit worked ideally for me. The materials are beautiful to use and plentiful in quantity (though why anyone would dye their own 0.25 mm thread is beyond me - fortunately I had a large supply). The large A3 instruction manual is beautifully conceived and magnificently clear. It suffers a little in clarity through the revisions to the model, but the revisions are all welcome. The sails were provided for free, and apart from being slightly miss-cut, I was happy to use them as provided, and I really do think the sails are worth having My biggest uncertainty in the whole project concerned attachment of the lower yards to the mast, and of some of the rigging, all lower than the gaff. With sails rigged it's obvious that if the gaff is to be raised or lowered at any speed then for the rings holding the spanker to be able to descend or rise, the mast must be free of rigging. And surely it must be possible to deploy the spanker in a hurry - to chase or flee abruptly to windward, for example. I couldn't find an image of the Alert model in the Science Museum - but all the cutter rigs I could find online showed no obvious attachment of the lower yards to the mast - so I've not added any. I used simple trusses for the topsail and t'gallant yards, and I suppose the lower yards could have had light trusses swiftly removed before deploying the spanker, but I cannot see how parrels could have been used on those two. But in fact, one of the alleged defects of rigging sails - they hide details - is a virtue in that they hide the attachment of the yards. They also hide details I chose not to add - hanks and coils of rope attached to all the belaying points. The pins just struck me as too small to take hanks of rope, and the decks too crowded already with sails, for coils to look right. Some things in modelling just don't scale well - mainly things to do with rigging thread, in my experience! This was meant to be a sort of infill project before HMS Surprise hoves into view, where I could try a few things out (sails, bare planking) - and hone some skills (too many to mention). It was all that, but much more: rich in features, novel in rig, but above all, beautiful.
- 34 replies
-
- Alert
- Vanguard Models
-
(and 1 more)
Tagged with:
-
Have been back building - but not posting. So here is the first of a couple of updates. The standing rigging was reasonably straightforward . I built a jig to line the dead-eyes up while tensioning the shrouds, which meant I could tie throat seizings. Naturally managed to rig at least two of them with the eyes the wrong way round, but spotted it pretty quickly After about 100 clove-hitches my mojo returned and I rattled down the shrouds in a a couple of sittings. Am I weird for enjoying that? I space the ratlines at 5 mm, so 32 cm or 12.5" IRL. I've previously persuaded myself that that follows historical precedents. But I think 7 mm might look better. Once the stays are in you get some perspective of just how much sail these relatively small ships carried. And sails are the subject of the next post.
- 34 replies
-
- Alert
- Vanguard Models
-
(and 1 more)
Tagged with:
-
Just had a couple of weeks back in the shipyard, and made myself some spars. All pretty straightforward using the Proxxon mill and lathe. Only challenge of note is that the heel of the bowsprit is specified as 6 mm square but the opining in the bitts is 5 mm. Just meant I had to machine the bowsprit twice. I opted to paint the yards, booms and gaffs black and stain the masts with three coats of oak wood dye - these rather poor photos don't really show that , but I like the effect. Shrouds and standing rigging next - and a couple of hundred clove hitches for the ratlines. But that will wait until we find some sun. So more later.
- 34 replies
-
- Alert
- Vanguard Models
-
(and 1 more)
Tagged with:
-
This being summer - so not ship-building season for me, I've not been on MSW for a while. I came here on spec - and wow!! What a build. Many congratulations Mike
- 562 replies
-
- vanguard models
- alert
-
(and 2 more)
Tagged with:
-
What great progress since Christmas - and magnificent painting. Rigging for small guns is always a challenge - I chose to do none on Alert. Best of luck!
-
Well, it has been a while... But we've been home for about three weeks, and after 10 weeks of marvellous sunny, dry warm wether in Australia we have returned to truly abysmal spring weather here: 6ºC, constant northerly wind and nearly continuous rain - interrupted by sleet and hail. So perfect modelling weather! The hull is now finished, with scarcely a problem - beyond periodic lapses of competence. This iteration of the Alert kit has some documented, and perhaps some less-documented differences from the manual. The first I noticed in recent work is that the cap squares are provided as small PE parts, but are also laser-cut into the sides of the gun carriages. The laser-cut detail is astonishingly high resolution so I wanted to use it, but that means the build order of assemble and glue carriage, paint carriage, add gun barrel, won't work since the barrel needs to be included before the gluing. I felt that painting the components and then assembling would not work well as the tolerances on the carriage are very fine and the paint would mess that up. But in any event, I was inclined to stain the carriages oak-brown, so I did. The results, I think are remarkable. Note the detail of the laser-cut cap square - including the tiny rebates that mean that it takes paint without it running all over the place. For scale, the lines on the cutting mat are on a 1 inch grid. A less-pleasant experience was the discovery that the chain (plates) sit lower than shown in the drawings - indeed they sit exactly on the water-line, which is not all that plausible IRL, and very inconvenient in that I had added a waterline batten. A simple lesson learnt: where relative positions are going to be important, measure the parts! But anyway, she looks OK! I've got the mill and the lathe set up, so mast and spars, here I come.
- 34 replies
-
- Alert
- Vanguard Models
-
(and 1 more)
Tagged with:
-
My word, this is beautiful work! I must commit to giving this much attention to detail (on some future model!)
- 562 replies
-
- vanguard models
- alert
-
(and 2 more)
Tagged with:
-
Final post for a while while I, the Admiral and one of my bikes seek a couple of months of winter sun. The hull and deck furniture are pretty-well complete - apart from guns, channels and one or two other things. No major traumas (that I can remember). Opted for the PE gratings, as the rebates in the coamings were sized for them, rather than the laser-cut pear wood. As a piece of painterly whimsy I decided the sky-light is glazed and the glazing bars are painted white. And as I have before, I fitted a copper rain cap on the galley flue That's it for now. Back in the spring.
- 34 replies
-
- Alert
- Vanguard Models
-
(and 1 more)
Tagged with:
-
Done some decorating - of the hull that is. Fitted the rough tree rail, and the rather beautiful scroll decorations. As an original act, I chose to paint the outboard edge of the rail in yellow ochre to match the other embellishments. To good effect, I think. I found the rough tree rail rather challenging - mainly because the cut-outs in the capping rail were smaller that the size of the various inserts. I thought I could just trim these latter with a scalpel, but it ended up a bit rough and ready. Should have used my Proxxon mill. Installing the decorative scrolls was time consuming but went well. The manual suggests spraying the paint on while the parts are still attached to the PE sheet to avoid getting dobs of paint on the reverse. Spraying paint in the the spare bedroom was never going to happen, so I did as follows Stuck the unpainted PE parts on masking tape, painted the PE pieces, sliced the tape around one piece, pulled that tape off (revealing the unpainted reverse - success!), trimmed the paint with a small scalpel I attached the PE to the hull using @James H's floor polish method. Works astonishingly well.
- 34 replies
-
- Alert
- Vanguard Models
-
(and 1 more)
Tagged with:
-
And so, I have progress to report. Let me show you where I am up to. As you can see, the hull is painted and substantially complete. Given how many blunders and the odd challenge, I'm amazed how well she passes the "30cm test" - in fact I think she looks drop-dead gorgeous with beautiful lines and very fetching paintwork - all credit to the designers. In the blunders camp, despite the clear instructions to the contrary, I used satin varnish to seal the the woodwork, having done so in all my previous models, but then neglected to either scratch or sand it when gluing further components - they fell off - a lot. I also discovered subtle variations in the shape of the hull which meant fitting the transom proved a right royal pain. I think those arose because I didn't quite get the sanding of the frames right, and because I chose minimal bending of the 1st and 2nd planks, I ended up sanding a lot of planking off. Essentially I rushed. Still, lesson worth learning. The biggest challenge can be seen here: There is a gap between the counter (attached weeks ago) and the transom attached just before the first photo (I knocked it off about 30s later - learnt my lesson and stuck it on properly). I cannot work out what, if anything I did wrong, but a little seam of Milliput sorted things out. When sanded and painted, the stern looks fine. I was also rather perplexed over where to fit the side counter timbers. The fig on p24 (and later) of the manual, and the photo on p 32 show different things. I opted for the latter, as can be seen in the opening pics. Had I known I was going to do that, I wouldn't have tapered the main wale at the stern, but I think I will leave it as it is, now. Hope to get a little more done before Christmas, but the full Admiralty Board will be in residence, with a supernumerary flag officer arriving this week, so that might slow the work of the shipyard (not to mention make it off-limits to all those below the rank of captain), and have the shipyard Matey too busy swabbing and knuckling his forehead to get any useful work done. So Merry Christmas one and all - or Happy Holidays, if you'd rather.
- 34 replies
-
- Alert
- Vanguard Models
-
(and 1 more)
Tagged with:
-
My word, she’s a beauty. I following along.
- 122 replies
-
- Artesania Latina
- Pen Duick
-
(and 1 more)
Tagged with:
-
There is some beautiful rigging to be seen here. Will certainly study it in due course.
- 562 replies
-
- vanguard models
- alert
-
(and 2 more)
Tagged with:
-
It's been a while. But I have some progress to share after a fantastic late summer of travel and cycling (sometimes combined!) Anyway, I've finished the second planking (give or take a rub-down with some 320 grit, and another coat of varnish). I set myself the challenge of getting a respectable result with no soaking/heating of the pear strip wood, or use of pins. The test being: would I be will just to varnish the hull, and not paint most of it (though I do plan to paint her)? I followed the usual advice and divided the hull into three zones - two initially and then a third - built myself a spreadsheet and shaped the planks as I went. I find shaping the planks with a knife and a ruler very hit and miss so instead marked up the cut lines and then held them in a plank clamp with the cut lines aligned with the tops of the jaws. I then simply planed off the waste - typically at the forward end and at the aft. I could clamp 6 strips together so shaping was relatively quick (once I got the hang of it). I chamfered each plank on one edge by mounting the strip in the clamp and then inclining the plane. Annoyingly I forgot to do this bit for the first few planks. Holding the planks in place while the CA set was 80% trivial, 10% challenging and 10% near impossible. Got better at it but future projects will require a bit of thought. For sanding the hull, I started with 80 grit paper using a set of Occre sanders. Slow process. I happened to be in B&Q and saw they had Black and Decker "Mouse" palm sanders for £11!! I recalled @James H saying that @chris watton had talked him into buying a palm sander, so thought I could risk £11 on (yet another) power tool. It was transformational! Particualrly after I had finished the first cut and then applied a small amount of acrylic filler - which, as I have said before, sets rock hard. After that second sanding at 80, I went up through the girts to 240 just using the Occre tools. And here she is after that sanding I struggled to get the planks to fit well at the prow and the stern. Almost inevitably getting a good fit at the prow and then cutting them short at the stern. If you zoom in on the last pic, above, there's quite a lot of filler on show. A rather greater challenge arose with the top planks at the stern. They are essentially unsupported and one of them was not well attached to the first planking beneath. Some overzealous (hand) sanding knocked it loose. A little very thin CA reattached it, and I then put in a bracing strut, visible athwartships at the stern here, that I will remove shortly. While sanding I noticed the familiar protruding-plank-that-doesn't-sand-down. That is, a plank not attached to the 1st planking beneath it. Fortunately I noticed this before I sanded it through and could anchor it using the very thin CA again. Turns out that there was a handful of such defects, all on the port side. Perhaps I held the planks differently on port and starboard sides while gluing them And so here she is with one coat of varnish applied And so would I be willing to display this varnished and unpainted? No, not quite. There are two flaws that annoy me but I could live with : first, and most annoyingly , not bevelling some of the upper planks, resulted in some noticeable gaps between planks (filled with CA and so not now fillable) and second, the lay of some of the planks is not quite as natural as would be desired. But the real killer is that I needed to colour the filler and made the rookie error of matching that colour to dry, unvarnished planks. As the aft view shows, that's not great. But when all is said and done, I'm pleased with the overall job.
- 34 replies
-
- Alert
- Vanguard Models
-
(and 1 more)
Tagged with:
-
By an extraordinary coincidence, I finished the second planking on Alert today. So I can say with fresh expeience under my belt - well done. That's a neat job!
-
I will follow with interest, Andrew. We are both doing VM cutters and both intending to add sails! Enjoy your holiday. Mike
About us
Modelshipworld - Advancing Ship Modeling through Research
SSL Secured
Your security is important for us so this Website is SSL-Secured
NRG Mailing Address
Nautical Research Guild
237 South Lincoln Street
Westmont IL, 60559-1917
Model Ship World ® and the MSW logo are Registered Trademarks, and belong to the Nautical Research Guild (United States Patent and Trademark Office: No. 6,929,264 & No. 6,929,274, registered Dec. 20, 2022)
Helpful Links
About the NRG
If you enjoy building ship models that are historically accurate as well as beautiful, then The Nautical Research Guild (NRG) is just right for you.
The Guild is a non-profit educational organization whose mission is to “Advance Ship Modeling Through Research”. We provide support to our members in their efforts to raise the quality of their model ships.
The Nautical Research Guild has published our world-renowned quarterly magazine, The Nautical Research Journal, since 1955. The pages of the Journal are full of articles by accomplished ship modelers who show you how they create those exquisite details on their models, and by maritime historians who show you the correct details to build. The Journal is available in both print and digital editions. Go to the NRG web site (www.thenrg.org) to download a complimentary digital copy of the Journal. The NRG also publishes plan sets, books and compilations of back issues of the Journal and the former Ships in Scale and Model Ship Builder magazines.