-
Posts
382 -
Joined
-
Last visited
About davec
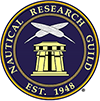
Profile Information
-
Gender
Male
-
Location
Richmond, VA
-
Interests
Scratch built plank on frame
Recent Profile Visitors
-
davec reacted to a post in a topic: Brabham BT45 by DocRob - Model Factory Hiro - 1/12 - multimedia
-
davec reacted to a post in a topic: KC-135R Stratotanker by GrandpaPhil - 1/32 - 3D Printed
-
davec reacted to a post in a topic: KC-135R Stratotanker by GrandpaPhil - 1/32 - 3D Printed
-
davec reacted to a post in a topic: HMS Bellona 1760 by SJSoane - Scale 1:64 - English 74-gun - as designed
-
davec reacted to a post in a topic: HMS Echo by Hamilton - Admiralty Models - 1:48 - cross-section
-
davec reacted to a post in a topic: HMS Echo by Hamilton - Admiralty Models - 1:48 - cross-section
-
davec reacted to a post in a topic: HMS Echo by Hamilton - Admiralty Models - 1:48 - cross-section
-
davec reacted to a post in a topic: HMS Echo by Hamilton - Admiralty Models - 1:48 - cross-section
-
Javlin reacted to a post in a topic: F4F-3 and F4F-4 by davec - Eduard - 1/48 - PLASTIC
-
Mike Collier reacted to a post in a topic: East Coast Oyster Sharpie 1880-1900 by davec - FINISHED - 1/16 scale
-
Mike Collier reacted to a post in a topic: East Coast Oyster Sharpie 1880-1900 by davec - FINISHED - 1/16 scale
-
Mike Collier reacted to a post in a topic: East Coast Oyster Sharpie 1880-1900 by davec - FINISHED - 1/16 scale
-
John Cheevers reacted to a post in a topic: East Coast Oyster Sharpie 1880-1900 by davec - FINISHED - 1/16 scale
-
egkb reacted to a post in a topic: 18th Century Longboat 1750-1760 by davec - Model Shipways - 1/48
-
AJohnson reacted to a post in a topic: F4F-3 and F4F-4 by davec - Eduard - 1/48 - PLASTIC
-
davec reacted to a post in a topic: '34 Ford Chopped Top Coupe by CDW - 3D Resin Printed - 1/25 Scale
-
yvesvidal reacted to a post in a topic: F4F-3 and F4F-4 by davec - Eduard - 1/48 - PLASTIC
-
Egilman reacted to a post in a topic: F4F-3 and F4F-4 by davec - Eduard - 1/48 - PLASTIC
-
Ryland Craze reacted to a post in a topic: 18th Century Longboat 1750-1760 by davec - Model Shipways - 1/48
-
My next project is the Eduard 1/48 F4F. I wanted to try some of their 3D printed parts, so went a little overboard and got most of the add-ons for the early F3F. I’m not including a lot of pictures of kit contents as there are professionally done photos on the eduard website. I will include some along the way showing the incredible detail in the printed parts and their comparison to the merely superb detail in the kit parts. I really like the prewar yellow wing paint schemes and wanted to build option A. The kit comes with parts for both an F4F-3 and F4F-4. I bought the double kit with two thoughts: 1- Most of the parts are the same. If I was struggling with the modifications for the 3d printed parts, I could use the extra parts to make sure I had was able to finish one model. 2- If I got past the big part modifications without problem, I could build both models. This would give me a chance to compare using the printed parts with building the kit out of the box (which in this case includes photo etch). The biggest modification to use the printed engine is to cut off the firewall from the kit parts and get the 3d printed firewall to fit in its place. I’ve included pictures of the new firewall and the unmodified fuselage. I cut off part of the old firewall with a razor saw, used a sanding drum on a rotary tool to remove much of the rest of it, then used sandpaper glued to a board to remove the rest really slowly, being careful to sand parallel to the panel line that I was aiming for. It came out OK, so I think I am OK for two models. The second one will be Lt Cdr John Thach’s plane as it was marked at Midway – seems appropriate as this is the anniversary of the battle. I’ve been incredibly impressed at the detail in the printed parts. I’ve just started on the two cockpits and will post pictures of them side by side as work continues.
-
I've restarted work on the long oat. I'm not sure how it sat for an entire year. Somehow the rhythms of my work and personal life made it a lot easier to migrate to my plastic models. I've added the two upper non-tapered planks and the first of the garboard planks. I'm happy with how the garboard runs looking at it from the top and bow. This is the first time I've seen it from the side without clamps obscuring most of it. I'm not sure about how the lower planks will run viewed from the side and will need to see after a couple are in place.
-
davec reacted to a post in a topic: 1955 Chevy Convertible Indy 500 pace Car by CDW - Revell - 1:25 Scale - PLASTIC
-
Looks great! Congratulations on finishing! Dave
- 16 replies
-
- dory
- Model Shipways
-
(and 2 more)
Tagged with:
-
Thanks everyone for the very kind and appreciated likes and comments. I think I am in a better place than I was preop, and once I catch up on 6 weeks of my regular job, will be back in the workshop more regularly. I plan to get back to work on the long boat and start Echo (I haven't forgotten that this is a model ship website). In the interim, I'm almost done with the P51. I had a little setback - I experimented with some panel line wash and don't 100% like the effect. I'm trying to decide whether to reprime and paint, or just finish the model so I can start from the beginning on something that won't feel like a recovery project.
-
I had my surgery and when I started feeling better started work back on the Halberstadt. I was already a little frustrated with it, which was why after I ran into problems with the decals on the upper wing I didn't just strip them and order new ones, so I didn't feel to bad working on it while not at my best. The spinal surgery was very successful, so my left hand and forearm are back to 100% for the first time in two years. Trying to rig a biplane while wearing a cervical collar is not something I recommend, but I did get a lot of peace when I was able to get down into my workshop again. Not my best work, but the whole point is to have fun, and it was really helpful with the rest of my recovery. I'm working on a Tamiya p-51 that my son had barely started prior to giving up building. It was started under the same recovery conditions with the same goal of keeping me sane. He had purchased decals for the P-51C Excalibur III in the NASM, so I'm working on that plane. I disassembled what he had started so I could use the Eduard photo etch set. I don't plan a build log for it.
-
Beautiful work - congratulations on finishing!
- 142 replies
-
- alfred
- solid hull
-
(and 2 more)
Tagged with:
-
Welfalck- again, many thanks. I have some small rotary cone bits, although I don't know about quality. I just had some surgery , so it will be about a month before I get back to my workshop. Will give it a try then. Looking forward to seeing if seating 30 4 mm tubes in the pin vice for using the rotary tool is easier or harder than holding them by hand and using a hand held drill. Dave
-
The tube segment that need deburring are .5 mm tube (.3 inner diameter) and are 4 mm long. Is there a rotary cone bit small enough? I can see using a rotary tool on the free end before cutting the segment, but any suggestions for holding the short tube to use a rotary bit on the second end once the segment is down to 4 mm? thanks!
-
Hi Rob - I think it was you who gave me the idea for using the bigger drill bit. I couldn't remember where I saw it or the specific size. I'll experiment with some other sizes, but am already really happy with the improvement with the size I am using. I made a jig for cutting the microtube: The horizontal slot is a few thousandths wider than the .5 mm microtube so it can roll while I am cutting with the scalpel. The scalpel fits in the vertical slot. The brass pin is 4mm from the scalpel cut. This gets me equal sized 4 mm tubes (I had a hard time getting them the same size when I was rolling them on the mat), is quick, and keeps the tube from flying away at the end of the cut. I think because the boxwood is a firmer backing than the mat, it gives me a little better cut. I don't have to do a ton of clean up, but the small amount makes a big difference in threading the line. I was planning to leave the sharp demarcation between the green insignia field and bordering camouflage. I don't have a good photo of the original airplane, but the Ronny Barr drawing shows it sharp. My best guess is that the field was painted over the camouflage, likely with a brush, so a sharp line feels right. The colors are awful bright which does give more contrast than it probably should have. I'm open to suggestions. I have so many things on this model that I'd like to cover over that I've given some thought to trying to weather it, although that's not something I usually do. Dave
-
I've added landing gear and rigging. I can't remember where on this site I read about using a .35 mm drill to clean the ends of the microtubing after passing a .3 mm drill through it, but I am very grateful to whoever suggested it. It turned threading the fishing line through the tube from almost impossible to just a little bit tedious. I also added the other pieces to the bottom of the plane. After knocking the upper wing loose a few times, the repetitive reattachment of the struts led to it being pretty crooked. I was able to break the glue joints where the struts met the fuselage and realign them. I'm hoping with a little touch up and clear flat the areas where they were reattached and the decals were disturbed won't be too distracting. The build has had a series of frustrations, but I'm glad I've kept working on it. It's beginning to look like an airplane and the color and camouflage overall effect is pretty good.
-
Windscreen, exhaust, and upper mid wing section added. This was the last part I anticipated problems with and it went OK. I'm glad I added the midsection before assembling the rest of the upper wing. It was a lot easier to manage aligning all the struts. When I took the picture I saw a band of exposed primer that I missed on the leading edge of the wing. I'll paint it the same color as the bottom of the wing. I just need to be really careful that the masking doesn't lift the decal.
-
She came out great! Congratulations on finishing!
- 39 replies
-
- Norwegian Sailing Pram
- Model Shipways
-
(and 1 more)
Tagged with:
-
Thanks everyone for the likes and the comments. I really appreciate them. Robert - next up is finishing the two projects I have on the bench (longboat and Halberstadt airplane). The Halberstadt is close. Once I finish the longboat, I will start the fully framed Echo that I have been planning for a few years. Thanks! Dave
- 32 replies
-
- Grand Banks Dory
- Model Shipways
-
(and 2 more)
Tagged with:
-
The decal issues are touched up as well as I can do and I’m moving ahead to finish the model. I’ve added the kit decals, applied micro crystal clear to the lenses, done more touch up, attached the rudder and a few other parts, and sprayed everything clear flat. I also spent an evening twisting 40 eyelets for the rigging. The cartograph decals felt much different than the aviatic ones – much thicker and took longer to soak before they were workable. It was a lot easier to deal with the smaller decals.
About us
Modelshipworld - Advancing Ship Modeling through Research
SSL Secured
Your security is important for us so this Website is SSL-Secured
NRG Mailing Address
Nautical Research Guild
237 South Lincoln Street
Westmont IL, 60559-1917
Model Ship World ® and the MSW logo are Registered Trademarks, and belong to the Nautical Research Guild (United States Patent and Trademark Office: No. 6,929,264 & No. 6,929,274, registered Dec. 20, 2022)
Helpful Links
About the NRG
If you enjoy building ship models that are historically accurate as well as beautiful, then The Nautical Research Guild (NRG) is just right for you.
The Guild is a non-profit educational organization whose mission is to “Advance Ship Modeling Through Research”. We provide support to our members in their efforts to raise the quality of their model ships.
The Nautical Research Guild has published our world-renowned quarterly magazine, The Nautical Research Journal, since 1955. The pages of the Journal are full of articles by accomplished ship modelers who show you how they create those exquisite details on their models, and by maritime historians who show you the correct details to build. The Journal is available in both print and digital editions. Go to the NRG web site (www.thenrg.org) to download a complimentary digital copy of the Journal. The NRG also publishes plan sets, books and compilations of back issues of the Journal and the former Ships in Scale and Model Ship Builder magazines.