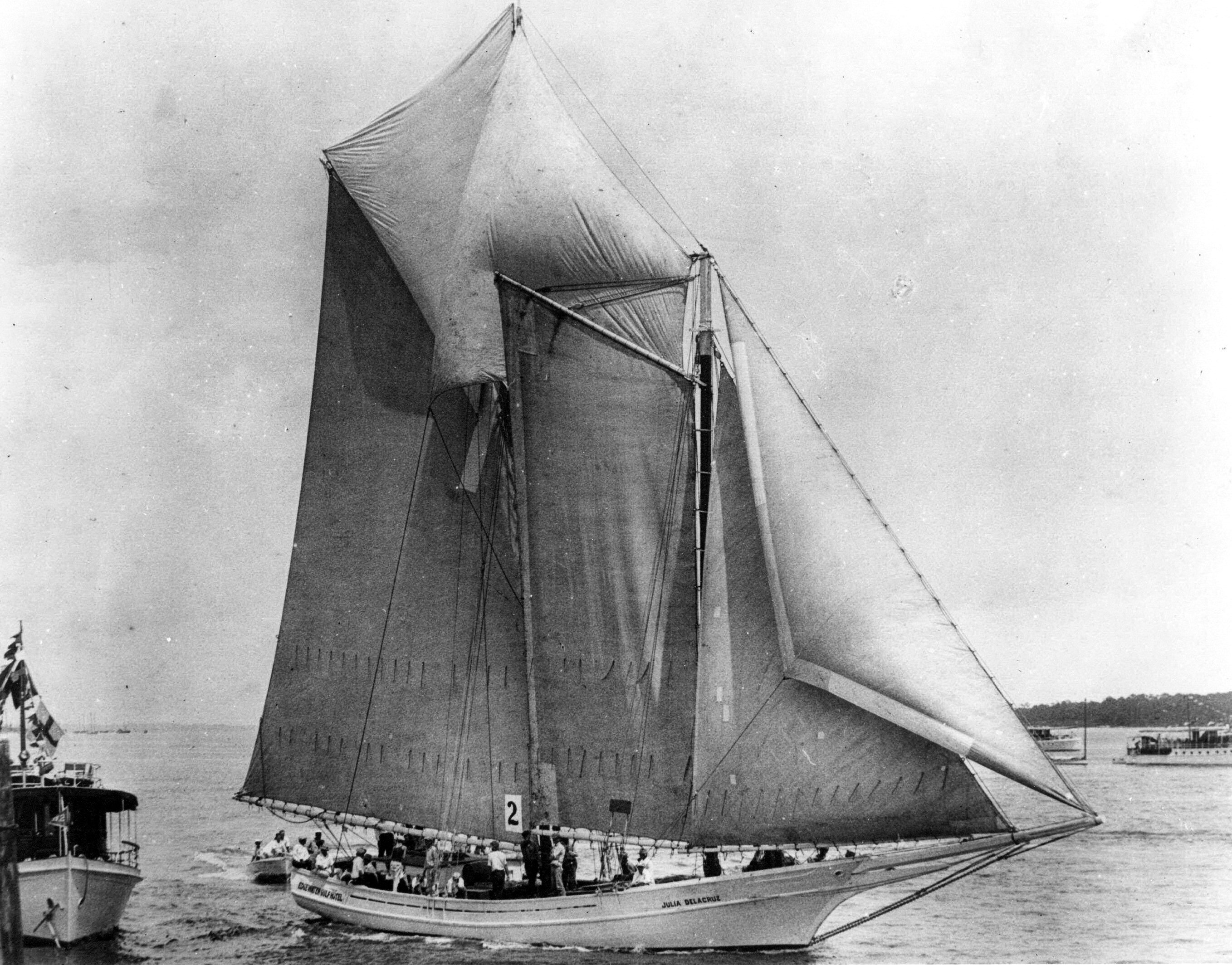
russ
Members-
Posts
3,086 -
Joined
-
Last visited
Content Type
Profiles
Forums
Gallery
Events
Everything posted by russ
-
Those ratlines look pretty good. Like they say, practice makes perfect. I agree about the white glue. You can water it down a slightly as well. It will soak in and it dries clear. Russ
- 64 replies
-
The deck looks great. Nice work on a BIG model. Russ
- 2,207 replies
-
That is quite good. The color on the plates is very nice. Good work. Russ
- 773 replies
-
- san francisco ii
- artesania latina
-
(and 1 more)
Tagged with:
-
Robbyn: I thought it was for one sheet. Ooops. On the hinges, try making each one in one piece. Curve over the corners of the "arrows". For the bolts, try a very small dab of CA on the end of a toothpick and see if that works. Russ
- 773 replies
-
- san francisco ii
- artesania latina
-
(and 1 more)
Tagged with:
-
This is a very interesting subject. Nice build. Russ
- 208 replies
-
- john cudahy
- finished
-
(and 1 more)
Tagged with:
-
Okay, I see what has happened. The false keel should have been thinned slightly in the after section so that the planking would sit lower and then the keel and sternpost would match up. In any event, I would have attached the keel, sternpost and stem before planking. It would have made it easier to account for this situation beforehand. The only remedies I see right now, without totally remaking the pieces in thicker wood, is to 1) use some left over planking material to pad them on either side so that it matches up, or 2) sand down the planking next to the keel and see if you can get it to the same thickness as the keel. I am not at all certain that 2 will work though, if the difference is that much. Russ
-
Alfons: You need to create clean surfaces by filing them up good and bright. I would make your wye or lug as it sometimes called, on the end of a brass strip. Create a pin on the end of the lug and drill the lug for its eye. Now, drill a hole into the band to receive the pin. It should be a snug fit, just enough to create some contact inside the hole and with the edge of the lug against the band. Now apply your solder and make the joint. After the joint is made, trim the lug to size and shape if with a file. Here are a couple of bands I made for the Ketch model. These all had the joints made first and the pieces trimmed to size afterwards. The first lug is made from the stem of the band after that first joint was sodlered to make the band. The rest had pins inserted into holes drilled into the band. Hope this helps. Russ
-
Solder brass rod for deadeye
russ replied to cog's topic in Metal Work, Soldering and Metal Fittings
Dida: When soldering the deadeye strops, do the soldering before the deadeyes are inserted. That way, they do not get burned. The strops should be flexible enough after annealing and soldering that you can easily slide the deadeye into the strop and then squeeze the strop around the deadeye. Russ -
Hull Planking questions
russ replied to fnkershner's topic in Building, Framing, Planking and plating a ships hull and deck
Floyd: The basswood sheets usually come 2 or 3 inches wide. I think mine were 3 inches wide. They come in regular thicknesses from 1/32" and up. You will need to decide what thickness you need for your model. I cut just a little fat and then sand down using an emory board. Russ -
Copper Plating Pattern
russ replied to capnharv2's topic in Building, Framing, Planking and plating a ships hull and deck
So far as I know they did not use the wooden batten when they added the plates along the waterline. I know there is a chapter on coppering etc in Brian Lavery's The Arming and Fitting of English Ships of War 1600-1815. I find this book to be very useful on many areas of period ship modeling. Russ -
Robbyn: You can cut that .005" thick sheet material with a pair of scissors. I do that all the time. That is how I make my strips for everything I need. However, I do not pay $15 a sheet. Check your local crafts store. Russ
- 773 replies
-
- san francisco ii
- artesania latina
-
(and 1 more)
Tagged with:
-
Hull Planking questions
russ replied to fnkershner's topic in Building, Framing, Planking and plating a ships hull and deck
Floyd: First of all, spiling is nothing more than transferring the curve of the edge of the previous plank onto the edge of the next plank so that they make a tight joint along their length. Because of the curves involved, this usually means using wider stock from which to make planks. Once you create that spiled edge, then you measure off the tapers at each bulkhead and create the tapered edge on your plank opposite the spiled edge. To plank with the strips in the kit, you would need to do some careful tapering on each plank and probably use some stealers or drop planks as necessary to get the hull planked. Other than that, just let the planks lay as they want and fill in the area to be planked as best you can with all sorts of pointy ended planks etc. I would buy 5-6 sheets of basswood from the LHS or crafts store and spile, but that is me and what I know best. I planked my current project like that and it cost very little and was very satisfying. Russ -
You can paint it with a brass color if you like. See what the crafts store has in artist's acrylics. They are usually 40-50 cents for a bottle that will last forever. Russ
- 773 replies
-
- san francisco ii
- artesania latina
-
(and 1 more)
Tagged with:
About us
Modelshipworld - Advancing Ship Modeling through Research
SSL Secured
Your security is important for us so this Website is SSL-Secured
NRG Mailing Address
Nautical Research Guild
237 South Lincoln Street
Westmont IL, 60559-1917
Model Ship World ® and the MSW logo are Registered Trademarks, and belong to the Nautical Research Guild (United States Patent and Trademark Office: No. 6,929,264 & No. 6,929,274, registered Dec. 20, 2022)
Helpful Links
About the NRG
If you enjoy building ship models that are historically accurate as well as beautiful, then The Nautical Research Guild (NRG) is just right for you.
The Guild is a non-profit educational organization whose mission is to “Advance Ship Modeling Through Research”. We provide support to our members in their efforts to raise the quality of their model ships.
The Nautical Research Guild has published our world-renowned quarterly magazine, The Nautical Research Journal, since 1955. The pages of the Journal are full of articles by accomplished ship modelers who show you how they create those exquisite details on their models, and by maritime historians who show you the correct details to build. The Journal is available in both print and digital editions. Go to the NRG web site (www.thenrg.org) to download a complimentary digital copy of the Journal. The NRG also publishes plan sets, books and compilations of back issues of the Journal and the former Ships in Scale and Model Ship Builder magazines.