-
Posts
6,030 -
Joined
-
Last visited
About Keith Black
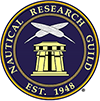
- Birthday 03/23/1947
Profile Information
-
Gender
Male
-
Location
Grass Lake, Michigan
-
Interests
Model Ships, History, Pool, Clocks
Recent Profile Visitors
-
Keith Black reacted to a post in a topic: Flying Fish by Rick310 - Model Shipways - 1/96
-
Keith Black reacted to a post in a topic: Muscongus Bay Lobster Smack by JacquesCousteau - Model Shipways - 1:32 - Rescaled and Modified
-
tmj reacted to a post in a topic: Sternwheeler From the Susquehanna River's Hard Coal Navy by Keith Black - 1:120 Scale
-
Cathead reacted to a post in a topic: Sternwheeler From the Susquehanna River's Hard Coal Navy by Keith Black - 1:120 Scale
-
Cathead reacted to a post in a topic: Sternwheeler From the Susquehanna River's Hard Coal Navy by Keith Black - 1:120 Scale
-
kurtvd19 reacted to a post in a topic: Sternwheeler From the Susquehanna River's Hard Coal Navy by Keith Black - 1:120 Scale
-
Keith Black reacted to a post in a topic: Flying Fish by Rick310 - Model Shipways - 1/96
-
Keith Black reacted to a post in a topic: Flying Fish by Rick310 - Model Shipways - 1/96
-
Keith Black reacted to a post in a topic: Flying Fish by Rick310 - Model Shipways - 1/96
-
Keith Black reacted to a post in a topic: Flying Fish by Rick310 - Model Shipways - 1/96
-
Keith Black reacted to a post in a topic: New member saying hello
-
Keith Black reacted to a post in a topic: New member saying hello
-
Keith Black reacted to a post in a topic: New member saying hello
-
clearway reacted to a post in a topic: Sternwheeler From the Susquehanna River's Hard Coal Navy by Keith Black - 1:120 Scale
-
gsdpic reacted to a post in a topic: Sternwheeler From the Susquehanna River's Hard Coal Navy by Keith Black - 1:120 Scale
-
gsdpic reacted to a post in a topic: Sternwheeler From the Susquehanna River's Hard Coal Navy by Keith Black - 1:120 Scale
-
Knocklouder reacted to a post in a topic: Sternwheeler From the Susquehanna River's Hard Coal Navy by Keith Black - 1:120 Scale
-
ccoyle reacted to a post in a topic: Sternwheeler From the Susquehanna River's Hard Coal Navy by Keith Black - 1:120 Scale
-
ccoyle reacted to a post in a topic: Sternwheeler From the Susquehanna River's Hard Coal Navy by Keith Black - 1:120 Scale
-
Keith Black reacted to a post in a topic: Sternwheeler From the Susquehanna River's Hard Coal Navy by Keith Black - 1:120 Scale
-
Welcome to MSW. Do we need another....you bet! Glad to have you aboard.
-
Thank you to all for the comments and likes. Quick update... The knee braces and winches have been added and that completes the bow face except for the deckhand and he will be the last piece added to the model. With the exception of the water and steam pipes the boiler is done and glued in place Next on the list is the steam engine. Thank you for the support and for being part of the journey. Keith
-
Thank you, Keith. I just asked Mr Google how many homes in Britain are still heated with coal and the answer was 30,000. I then asked how many narrowboats and wide beam boats there are in Britain and the answer was 35,000. I watch several YouTube videos on canal boating and several use coal to heat their boats. I would think coal usage is declining but you and the canal boats seem to be hanging on.
-
Crank up some Pink Floyd for Mrs Knocklouder and see how she likes them apples.
- 135 replies
-
- Victory Models
- Pegasus
-
(and 2 more)
Tagged with:
-
Thank you guys for your kind and informative comments and the likes. I appreciate your support so very much. The first time i saw the photos of this push boat I was smitten with the ugly, dirty, quirkiness of her but I had serious reservations when I started the build not knowing if I was going to be capable of doing her justice. It's only been in this last week that I've really warmed to the build as the work has finally developed a rhythm and flow and now I'm having a ton of fun, let the devil take the hind quarter. First off, I want to apologize for the following photos.......bad camera day. The steel plate is painted but not yet glued down. I looked at beads and a whole slew of other options for lightbulbs but nothing worked as well as the belaying pins. I did try filing and sanding the shape from egg to ball, they're now acceptable. I added coal to the coal crib and the auto stoker's conveyer belt. Coal has a slight gleam to it so I lightly patted poly on top of the coal to give it just a hint of shine. I also got the conveyer belt tail rigged through the blocks. The stern maintenance hatch is made and glued in place. The coal crib and stoker are glued to the steel plate but the boiler is not yet glued to the plate as I have more work to do on it which is next on the list. Thank you for following along and being part of the journey. Keith
About us
Modelshipworld - Advancing Ship Modeling through Research
SSL Secured
Your security is important for us so this Website is SSL-Secured
NRG Mailing Address
Nautical Research Guild
237 South Lincoln Street
Westmont IL, 60559-1917
Model Ship World ® and the MSW logo are Registered Trademarks, and belong to the Nautical Research Guild (United States Patent and Trademark Office: No. 6,929,264 & No. 6,929,274, registered Dec. 20, 2022)
Helpful Links
About the NRG
If you enjoy building ship models that are historically accurate as well as beautiful, then The Nautical Research Guild (NRG) is just right for you.
The Guild is a non-profit educational organization whose mission is to “Advance Ship Modeling Through Research”. We provide support to our members in their efforts to raise the quality of their model ships.
The Nautical Research Guild has published our world-renowned quarterly magazine, The Nautical Research Journal, since 1955. The pages of the Journal are full of articles by accomplished ship modelers who show you how they create those exquisite details on their models, and by maritime historians who show you the correct details to build. The Journal is available in both print and digital editions. Go to the NRG web site (www.thenrg.org) to download a complimentary digital copy of the Journal. The NRG also publishes plan sets, books and compilations of back issues of the Journal and the former Ships in Scale and Model Ship Builder magazines.