
jfhealey
NRG Member-
Posts
359 -
Joined
-
Last visited
About jfhealey
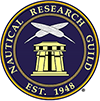
Recent Profile Visitors
-
bdgiantman2 reacted to a post in a topic: HMS Winchelsea by jfhealy - Fred's W2
-
FrankWouts reacted to a post in a topic: HMS Winchelsea 1764 by Matt D 1:48
-
jfhealey reacted to a post in a topic: La Créole 1827 by archjofo - Scale 1/48 - French corvette
-
Matt D reacted to a post in a topic: HMS Winchelsea 1764 by Matt D 1:48
-
scrubbyj427 reacted to a post in a topic: HMS Winchelsea 1764 by Matt D 1:48
-
I did exactly the same thing. I was able to prise the offending part away with a sharp blade without causing any damage - or at least any damage that was not easily repaired. I had glued the part with CA onto a previously painted surface so I guess there was more limited adhesion than might have been the case had I glued to unpainted wood. I don't think you can leave it in the wrong place - it will surely always bug you and, I suspect, cause more problems down the line. Good luck whatever choice you make.
-
FrankWouts reacted to a post in a topic: HMS Winchelsea 1764 by Matt D 1:48
-
FrankWouts reacted to a post in a topic: HMS Winchelsea by jfhealey - fully rigged version
-
FrankWouts reacted to a post in a topic: HMS Winchelsea by jfhealey - fully rigged version
-
FrankWouts reacted to a post in a topic: HMS Winchelsea by jfhealey - fully rigged version
-
FrankWouts reacted to a post in a topic: HMS Winchelsea by jfhealey - fully rigged version
-
FrankWouts reacted to a post in a topic: HMS Winchelsea 1764 by woodartist - 1:48
-
jfhealey reacted to a post in a topic: HM Cutter Cheerful 1806 by Erik W - 1:48 scale
-
Fascinaing - and a great deal of thoughtful engineering. I'm following with keen interest. Fred
-
jfhealey reacted to a post in a topic: Le Rochefort by No Idea - 1/24th Scale - First POF Build
-
jfhealey reacted to a post in a topic: LA CREOLE/ LA GUADELOUPE by matiz - 1:48 - by Tiziano Mainardi from Boudriot plans
-
Beautiful ship, beautifully made and so nicely set off in its case.
- 399 replies
-
- winchelsea
- Syren Ship Model Company
-
(and 1 more)
Tagged with:
-
jfhealey reacted to a post in a topic: Fokker D.VI by ccoyle - MPModel - 1/33 - CARD - TERMINATED
-
jfhealey reacted to a post in a topic: HMS Tiger 1747 by Siggi52 - 1:48 - 60 gun ship from NMM plans
-
jfhealey reacted to a post in a topic: La Créole 1827 by archjofo - Scale 1/48 - French corvette
-
jfhealey reacted to a post in a topic: HMS Winchelsea 1764 by Trussben - FINISHED - 1:48
-
jfhealey reacted to a post in a topic: Sloop Speedwell 1752 by Rustyj - Syren Ship Model Company - 1:32 Scale - POF Sloop
-
A beautiful model beautifully displayed. What next? Fred
- 840 replies
-
- winchelsea
- Syren Ship Model Company
-
(and 1 more)
Tagged with:
-
Good afternoon all. Here is an update on my Winnie build. It feels like a significant milestone because at last the bowsprit - that I made such a long time ago - is in. I had to fix it in permanently as I wanted to both glue and peg it to the gundeck and I could not plank the centre of the fo'c'sle until that was done. Here she is in the garden on a rare day when the sun has shone. Two things in the picture below. First I placed railings around the headwork. I guesss there must have been railings. Using the heads without would have been a very precarious occupation - certainly not a place to skive off work for a cigarette break. But should the railing extend all the way back to the main rail I wonder? Secondly I placed a little chock on the outboard end under the boomkin. I appreciate the contemporary model does not have one but had I been the builder (of the real thing) I'd have put one there for support and stability, so my model is getting one. I turned the boomkins incidentally and the bent them with heat. I thought that easier than shaping the Syren parts. Cutting the fancy rail was not a job I looked forward to - but it went ok. I used pins and epoxy for a relly secure fix. I can see my gammoning chocks are too big but I can live with them. One, I suspect, of a litany of historical errors that I shall make with the masting/rigging. Lovely lines fore and aft. I think I will finish up the fo'c'sle area/bow end and then work my way back. In fact there are only a few detail bit and pieces to go. The end of the Syren bit is in sight - the masts are largely made so I hope to see real progress by the year end. Best wishes Fred
About us
Modelshipworld - Advancing Ship Modeling through Research
SSL Secured
Your security is important for us so this Website is SSL-Secured
NRG Mailing Address
Nautical Research Guild
237 South Lincoln Street
Westmont IL, 60559-1917
Model Ship World ® and the MSW logo are Registered Trademarks, and belong to the Nautical Research Guild (United States Patent and Trademark Office: No. 6,929,264 & No. 6,929,274, registered Dec. 20, 2022)
Helpful Links
About the NRG
If you enjoy building ship models that are historically accurate as well as beautiful, then The Nautical Research Guild (NRG) is just right for you.
The Guild is a non-profit educational organization whose mission is to “Advance Ship Modeling Through Research”. We provide support to our members in their efforts to raise the quality of their model ships.
The Nautical Research Guild has published our world-renowned quarterly magazine, The Nautical Research Journal, since 1955. The pages of the Journal are full of articles by accomplished ship modelers who show you how they create those exquisite details on their models, and by maritime historians who show you the correct details to build. The Journal is available in both print and digital editions. Go to the NRG web site (www.thenrg.org) to download a complimentary digital copy of the Journal. The NRG also publishes plan sets, books and compilations of back issues of the Journal and the former Ships in Scale and Model Ship Builder magazines.