-
Posts
363 -
Joined
-
Last visited
About CiscoH
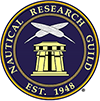
- Birthday 01/29/1973
Profile Information
-
Gender
Male
-
Location
Middletown, Delaware
Recent Profile Visitors
-
CiscoH reacted to a post in a topic: Chris Watton and Vanguard Models news and updates Volume 2
-
CiscoH reacted to a post in a topic: TFFM Swan Class Books
-
CiscoH reacted to a post in a topic: HMS Winchelsea 1764 by Edwardkenway- 1:48
-
CiscoH reacted to a post in a topic: HMS Winchelsea 1764 by Edwardkenway- 1:48
-
CiscoH reacted to a post in a topic: HMS Harpy 1796 by dunnock - Vanguard Models - 1:64
-
CiscoH reacted to a post in a topic: HMS Harpy 1796 by dunnock - Vanguard Models - 1:64
-
CiscoH reacted to a post in a topic: HMS Harpy 1796 by dunnock - Vanguard Models - 1:64
-
Desertanimal reacted to a post in a topic: 18th Century Longboat by Desertanimal - Model Shipways - 1:48
-
CiscoH reacted to a post in a topic: HMS Cumberland 1774 by Jack H - 1:36 &1:48 - POF - kit development for True Image Models
-
CiscoH reacted to a post in a topic: Sloop Speedwell 1752 by Chuck - Ketch Rigged Sloop - POF - prototype build
-
CiscoH reacted to a post in a topic: HMS Surprise 1796 (prototype) by James H - Vanguard Models - 1:64
-
CiscoH started following 18th Century Longboat by Desertanimal - Model Shipways - 1:48
-
yvesvidal reacted to a post in a topic: 18th Century Longboat by FarmerJon - FINISHED - Model Shipways - 1:48 Scale - first build
-
JLong reacted to a post in a topic: Speedwell Battle Station Kit 1752 by CiscoH - Syren Ship Model Company - 3/8" or 1:32
-
thibaultron reacted to a post in a topic: Syren Ship Model Company News, Updates and Info.....(part 2)
-
Ryland Craze reacted to a post in a topic: Speedwell Battle Station Kit 1752 by CiscoH - Syren Ship Model Company - 3/8" or 1:32
-
rcweir reacted to a post in a topic: Speedwell Battle Station Kit 1752 by CiscoH - Syren Ship Model Company - 3/8" or 1:32
-
bdgiantman2 reacted to a post in a topic: Speedwell Battle Station Kit 1752 by CiscoH - Syren Ship Model Company - 3/8" or 1:32
-
Rustyj reacted to a post in a topic: Speedwell Battle Station Kit 1752 by CiscoH - Syren Ship Model Company - 3/8" or 1:32
-
Jack12477 reacted to a post in a topic: Speedwell Battle Station Kit 1752 by CiscoH - Syren Ship Model Company - 3/8" or 1:32
-
Chuck reacted to a post in a topic: Speedwell Battle Station Kit 1752 by CiscoH - Syren Ship Model Company - 3/8" or 1:32
-
Good Thursday night MSW. A brief update tonight, more fine tuning than impressive progress. I finished the cap railing and moldings and sanded down the cross sections of the planking on the sides. Then I added the channel, which had to be sanded down thinner to match the width of the molding. I wasn't confident it would stay put with only glue so I pinned it as well. I managed to drill all the way through the bulwarks with all 3 pinning holes so beware future builders. I used epoxy and 20g brass wire which fit the holes loosely allowing me some wiggle room, and yellow glue. It's pretty solid now. After it was fully dry I realized I put the channel in upside down (the edge slots for the deadeye strops are not the same at each end, one is closer to the edge than the other) but I can't easily unattach the thing so its staying. I noticed in the Speedwell book (Vol II, pg 47) Greg and Gave show the deadeyes all the same size. They also chose to add a swivel mount directly over the channel, in between the 2 bolsters. I don't think I'm doing the swivel but maybe my brain will betray me. Again. We'll see. It might make the model a little too busy. Then I made the bolsters, which were straight-forward sanding exercises and pinned them as well. I used superglue for the pins. Both feel secure. And finally I manned up and attached the base pieces. They were not perfectly square to each other so I have some sanding in my future before I add the curved molding to ease the transition to the base. I also added the waterway piece, which in hindsight should have been holly so it matched the decking instead of the AYC i used but oh well. I also drilled out the scuppers and used #2 pencil to darken them as per the directions. They don't connect and you can't tell. and now I started on the cannon carriage. Thats it for tonight. Tomorrow the family and I are flying to not-sunny old England for a week of vacation. I bargained hard for a day to see the Victory and in return had to give up all control of the other 6 days. Pictures will be posted. thanks for reading, Cisco
- 17 replies
-
- Speedwell
- battle station
-
(and 1 more)
Tagged with:
-
Nothing is more rewarding than dealing with the public. And i too hope Chuck produces the Battle Station as a regular kit. Its small but packed with detail and perfect for introducing the use of Syren rope and other Syren materials to rig a practice cannon. I won mine at the CT conference and could have gotten a mini table saw but picked the kit instead. And I have so far really enjoyed building it.
-
excellent planking Jeff! the Confederate is a big ship and your smooth run of planking looks very even and tight. i’ve only planked one ship so far so i’m no expert but like you i had numerous re-dos. i felt like i didnt get better at planking, instead i got better at fixing mistakes. keep up the great work cisco
-
CiscoH started following Modelers Sawmill??
-
I was thinking of trying to start a Northern Delaware club in the next year. The closest club I'm aware of is in Philly but thats too far for me. Also, its in Philly. I saw the post about a southern Delaware club and was thinking about it but realistically I would never go because its 1.5 hrs away. When/if I finally free up the time I'll post here and see if it gets any traction. My shipmodeling buddy Jason (JLong) lives in Newark DE and we hang out every month or two so I guess its already a club of 2 people.
- 17 replies
-
- Speedwell
- battle station
-
(and 1 more)
Tagged with:
-
Mike- the Conference was in April in New London, CT. About 6 hrs from here.
- 17 replies
-
- Speedwell
- battle station
-
(and 1 more)
Tagged with:
-
Well Howdy MSW. Its hot and humid here in Middletown Delaware on Sunday afternoon. Most of this post is fixing my last post, oh well. I was not fully satisfied with my previous attempts at making moldings. The process was fine and good practice, but the wood I used (I think maple?) had a mottled pattern. It looked ... ok. After staring at it for a while I decided to hold off on making the upper molding until inspiration struck. In every misfortune lurks opportunity; this was the perfect excuse to order some wood. I'd heard good things about Modelers Sawmill in New Jersey so I gave it a try and ordered 2 billets of AYC and 2 of Boxwood (which I have never used before). Joe, the owner, was excellent and provided good communication and suggestions. The order took a few days to show up, was nicely wrapped on the outside, celophaned on the inside (to limit moisture exchange -> which leads to warping). An excellent experience - highly recommended. Joe even included 2 extra billets of AYC because of some discoloured areas. I normally assume 25% wastage from imperfections so this was above and beyond. Now that I had the wood I had to do it justice. I cut a strip from the boxwood and used the same scraper as before to remake the lower molding. Once it was scraped I trimmed it down to size. It was definitely better. Below the old molding is on the left. You can see the mottling/spots it has. The boxwood on the right is much cleaner. The old lower molding popped off distressingly easily. I changed from white glue to yellow in hopes the boxwood version would stick better. Next I made the scraper for the upper molding. My interpretation of the Battle Station plans indicated a double bead, the upper one bigger than the lower, with a small fillet at the bottom. This scraper took a lot more time to construct versus the lower molding; every time I had it almost right I tended to over-file. Here is the final result - the profile I used is on the bottom left side. The profile is cut pretty deep into the hacksaw because i had to redo it so many times. Then the same process as before. Scrape the boxwood, plane it down to the correct thickness, and yellow glue it in place. The upper molding sticks up a bit so next I added a strip (the cap rail?) to bring it flush. Now that I have my finished height I can make the inner molding next. And thats where we are. While waiting for my wood to arrive I had started on the cannon carriage but it can wait for my next post. I like Boxwood. Its hard, a bit stringy, and on the billets you can see the grain pattern but its not obvious once cut into strips. It will be my molding material of choice in the future on any AYC projects. Happy 4th of July weekend for those of you that celebrate thanks for reading Cisco
- 17 replies
-
- Speedwell
- battle station
-
(and 1 more)
Tagged with:
-
CiscoH started following HMS Winchelsea 1764 by Frank Wouts 1/48
About us
Modelshipworld - Advancing Ship Modeling through Research
SSL Secured
Your security is important for us so this Website is SSL-Secured
NRG Mailing Address
Nautical Research Guild
237 South Lincoln Street
Westmont IL, 60559-1917
Model Ship World ® and the MSW logo are Registered Trademarks, and belong to the Nautical Research Guild (United States Patent and Trademark Office: No. 6,929,264 & No. 6,929,274, registered Dec. 20, 2022)
Helpful Links
About the NRG
If you enjoy building ship models that are historically accurate as well as beautiful, then The Nautical Research Guild (NRG) is just right for you.
The Guild is a non-profit educational organization whose mission is to “Advance Ship Modeling Through Research”. We provide support to our members in their efforts to raise the quality of their model ships.
The Nautical Research Guild has published our world-renowned quarterly magazine, The Nautical Research Journal, since 1955. The pages of the Journal are full of articles by accomplished ship modelers who show you how they create those exquisite details on their models, and by maritime historians who show you the correct details to build. The Journal is available in both print and digital editions. Go to the NRG web site (www.thenrg.org) to download a complimentary digital copy of the Journal. The NRG also publishes plan sets, books and compilations of back issues of the Journal and the former Ships in Scale and Model Ship Builder magazines.