-
Posts
1,860 -
Joined
-
Last visited
About Glen McGuire
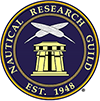
Contact Methods
-
Website URL
https://texasbottleships.com/
Profile Information
-
Gender
Male
-
Location
Austin, Texas
Recent Profile Visitors
-
Glen McGuire reacted to a post in a topic: HMS Pegasus 1776 by Knocklouder - Amati/Victory Models - 1:64
-
Glen McGuire reacted to a post in a topic: HMS Pegasus 1776 by Knocklouder - Amati/Victory Models - 1:64
-
Glen McGuire reacted to a post in a topic: Sternwheeler From the Susquehanna River's Hard Coal Navy by Keith Black - 1:120 Scale
-
Glen McGuire reacted to a post in a topic: Steam Schooner Wapama 1915 by Paul Le Wol - Scale 1/72 = From Plans Drawn By Don Birkholtz Sr.
-
Glen McGuire reacted to a post in a topic: Steam Schooner Wapama 1915 by Paul Le Wol - Scale 1/72 = From Plans Drawn By Don Birkholtz Sr.
-
Glen McGuire reacted to a post in a topic: Steam Schooner Wapama 1915 by Paul Le Wol - Scale 1/72 = From Plans Drawn By Don Birkholtz Sr.
-
Glen McGuire reacted to a post in a topic: Astrolabe 1812 by Knocklouder - Mantua - 1:50
-
Keith Black reacted to a post in a topic: Astrolabe 1812 by Knocklouder - Mantua - 1:50
-
Knocklouder reacted to a post in a topic: Astrolabe 1812 by Knocklouder - Mantua - 1:50
-
Paul Le Wol reacted to a post in a topic: Astrolabe 1812 by Knocklouder - Mantua - 1:50
-
Glen McGuire reacted to a post in a topic: Oryol 1902 by GrandpaPhil - Orel - 1/200 - CARD - Russian Battleship
-
Glen McGuire reacted to a post in a topic: Steam Schooner Wapama 1915 by Paul Le Wol - Scale 1/72 = From Plans Drawn By Don Birkholtz Sr.
-
Glen McGuire reacted to a post in a topic: Astrolabe 1812 by Knocklouder - Mantua - 1:50
-
GrandpaPhil reacted to a post in a topic: Sternwheeler From the Susquehanna River's Hard Coal Navy by Keith Black - 1:120 Scale
-
Cathead reacted to a post in a topic: Sternwheeler From the Susquehanna River's Hard Coal Navy by Keith Black - 1:120 Scale
-
Canute reacted to a post in a topic: Ferrari 288 GTO by gsdpic - FINISHED - Fujimi - 1/24 - PLASTIC
-
yvesvidal reacted to a post in a topic: Sternwheeler From the Susquehanna River's Hard Coal Navy by Keith Black - 1:120 Scale
-
Canute reacted to a post in a topic: Sternwheeler From the Susquehanna River's Hard Coal Navy by Keith Black - 1:120 Scale
-
Javelin reacted to a post in a topic: Sternwheeler From the Susquehanna River's Hard Coal Navy by Keith Black - 1:120 Scale
-
MAGIC's Craig reacted to a post in a topic: Sternwheeler From the Susquehanna River's Hard Coal Navy by Keith Black - 1:120 Scale
-
The rope work on the rustic base is a really nice touch. It complements the ship quite well. Great job, Bryan!
- 44 replies
-
- Nave Egizia
- Amati
-
(and 1 more)
Tagged with:
-
She turned out to be a real beauty, JC. An enjoyable build to follow. Congratulations on your fine work!
- 312 replies
-
- Chile
- Latin America
-
(and 6 more)
Tagged with:
About us
Modelshipworld - Advancing Ship Modeling through Research
SSL Secured
Your security is important for us so this Website is SSL-Secured
NRG Mailing Address
Nautical Research Guild
237 South Lincoln Street
Westmont IL, 60559-1917
Model Ship World ® and the MSW logo are Registered Trademarks, and belong to the Nautical Research Guild (United States Patent and Trademark Office: No. 6,929,264 & No. 6,929,274, registered Dec. 20, 2022)
Helpful Links
About the NRG
If you enjoy building ship models that are historically accurate as well as beautiful, then The Nautical Research Guild (NRG) is just right for you.
The Guild is a non-profit educational organization whose mission is to “Advance Ship Modeling Through Research”. We provide support to our members in their efforts to raise the quality of their model ships.
The Nautical Research Guild has published our world-renowned quarterly magazine, The Nautical Research Journal, since 1955. The pages of the Journal are full of articles by accomplished ship modelers who show you how they create those exquisite details on their models, and by maritime historians who show you the correct details to build. The Journal is available in both print and digital editions. Go to the NRG web site (www.thenrg.org) to download a complimentary digital copy of the Journal. The NRG also publishes plan sets, books and compilations of back issues of the Journal and the former Ships in Scale and Model Ship Builder magazines.