-
Posts
645 -
Joined
-
Last visited
About rlb
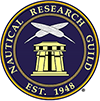
- Birthday 05/17/1960
Profile Information
-
Gender
Male
-
Location
Troy, New York
Recent Profile Visitors
-
rlb reacted to a post in a topic: Queen Anne’s Revenge by BETAQDAVE - CubicFun Toys – ~1:64 scale - CARD
-
rlb reacted to a post in a topic: Queen Anne’s Revenge by BETAQDAVE - CubicFun Toys – ~1:64 scale - CARD
-
chris watton reacted to a post in a topic: US Brig Oneida 1809 by rlb - The Lumberyard - 1:48 scale - POF - Lake Ontario Warship
-
chris watton reacted to a post in a topic: US Brig Oneida 1809 by rlb - The Lumberyard - 1:48 scale - POF - Lake Ontario Warship
-
rlb reacted to a post in a topic: US Brig Oneida 1809 by rlb - The Lumberyard - 1:48 scale - POF - Lake Ontario Warship
-
ccoyle reacted to a post in a topic: US Brig Oneida 1809 by rlb - The Lumberyard - 1:48 scale - POF - Lake Ontario Warship
-
JpR62 reacted to a post in a topic: US Brig Oneida 1809 by rlb - The Lumberyard - 1:48 scale - POF - Lake Ontario Warship
-
BETAQDAVE reacted to a post in a topic: US Brig Oneida 1809 by rlb - The Lumberyard - 1:48 scale - POF - Lake Ontario Warship
-
Roger Pellett reacted to a post in a topic: US Brig Oneida 1809 by rlb - The Lumberyard - 1:48 scale - POF - Lake Ontario Warship
-
rlb reacted to a post in a topic: LA CREOLE/ LA GUADELOUPE by matiz - 1:48 - by Tiziano Mainardi from Boudriot plans
-
rlb reacted to a post in a topic: US Brig Oneida 1809 by rlb - The Lumberyard - 1:48 scale - POF - Lake Ontario Warship
-
hamilton reacted to a post in a topic: Off Center Skiff by hamilton - FINISHED - 1:12 scale - SMALL
-
mtaylor reacted to a post in a topic: Off Center Skiff by hamilton - FINISHED - 1:12 scale - SMALL
-
bhermann reacted to a post in a topic: US Brig Oneida 1809 by rlb - The Lumberyard - 1:48 scale - POF - Lake Ontario Warship
-
bhermann reacted to a post in a topic: US Brig Oneida 1809 by rlb - The Lumberyard - 1:48 scale - POF - Lake Ontario Warship
-
It's definitely a "forest of frames"! She's going to be a beautiful model, John, as your others. Ron
-
rlb reacted to a post in a topic: Meteor by Jim Lad - Scale 1:96 - Immigrant Ship Of 1851
-
Boarding steps-- I would have made the steps the full width of the hammock opening, but the carronade position wouldn't allow it. The hammock position corresponds to Chappelle's sail plan drawing and also the location of the outboard boarding steps shown on the hull plan, but a little foresight may have warranted shifting the steps and opening just a bit. Ron
-
rlb reacted to a post in a topic: HMS Speedy by usedtosail - Vanguard Models - Scale 1:64
-
rlb reacted to a post in a topic: HMS Sphinx 1775 by mugje - Vanguard Models - 1:64
-
The capstan bars are roughed in-- I need to soften some of the transitions between the square end and the rounded part, but they are dry fit into the capstan head, and on deck-- They'll also need a coat of Tung oil finish when done. The list is getting smaller of what is still needed before stepping the masts and starting the rigging. At this point I still need some inboard boarding steps, and I think I'll make some mast collars. I am also contemplating redoing the gratings, with a tighter grid. All for now, Ron
-
rlb reacted to a post in a topic: HMS Portland 1770 by scrubbyj427 - 1:48 - 4th rate 50-gun ship
-
rlb reacted to a post in a topic: Sloop Speedwell 1752 by Rustyj - Syren Ship Model Company - 1:32 Scale - POF Sloop
-
Thanks Joe, and all looking in. The hammock cranes and cloth are done. It was more work than I anticipated, but I think it was worth it. I got some practice making jigs and drilling small holes on the mill, and I learned about Silkspan. Here one side is done, and the other has been "strung". I was tempted to leave it this way, but elected to complete both sides-- Done. Work on the capstan bars continues-- Knotted boarding ropes hang over the boarding steps. I don't know why Lieutenant Woolsey is falling all over the deck in the previous photos, but he's found his feet here. I'll secure the ropes with a dot of glue on one of the lower steps, but for now the clips make them hang straight and give the idea-- I am reminded of something I read about Oneida being reported by an early crew member (I think) as being a "warm cozy" ship. They were probably talking about below deck, but the more enclosed and protected feeling with the hammocks in place on the rails does give me that impression-- All for now, Ron
-
HMS EURYALUS by Matiz - FINISHED - scale 1:56
rlb replied to matiz's topic in - Build logs for subjects built 1801 - 1850
Congratulations, Matiz, on your beautiful model. I will look to it often for inspiration. Ron -
Just an additional note on the hammock cloth, and historical accuracy, since you don't see this black cloth depicted often. Usually you see some diagonal netting, and some folded over hammocks contained within. The netting is problematic for me. Whatever you can get "ready-made" is plastic and seems out of scale, and would be difficult to fasten realistically. So I liked Glenn Greico's black cloth--much simpler (I reference his model for the Institute of Nautical Archeology in Austin, Texas of the USS Brig Jefferson often, and in that context he HAS to be as historically accurate as possible.). But I am now realizing that I have seen it other places. A recent photo in archjofo's La Creole log led me back to post #783 where he shows his version of the black cloth. Very interesting that he used balsa (or similar soft wood) for the underlying form!! And then I remembered a black cloth in photos of Frolich's models of Swan and Cygne. I (we) look at so many sources for these details that I lose track of where I saw them, or even forget I even saw them. So I am feeling good about the approach. The bigger question of whether this ship would have even HAD hammock cranes is unanswerable. We don't know much about Oneida beyond the basic lines. I wish I was building an Oneida that I know is accurate, but I will continue on building an Oneida that I hope is plausible, and in the end for me, is a beautiful model.
-
More hammock crane work. I decided I needed a better way to make the modeling clay form for the hammock covering cloth. I had just kind of rolled it out and mashed it into rough shape, but it was a little TOO rough and varied in height and thickness. So I made a mold out of scrap wood. This is the length I need for the forward sections. The previous clay form and removed covering paper are above it-- Then I mashed the clay into one side of the mold-- And clamped the outer mold piece against it. There are spacers at the end to make the right thickness, and I used my calipers to make sure it was the same width at the middle. They also worked as a clamp. I mashed additional clay into the top where needed-- Then scraped the top smooth-- This gave me a piece of clay that was uniform in height and thickness-- I ran a finger along each side of the top to round and smooth it-- New pieces of Silkspan were moistened and folded around it-- When this dried, I tucked and glued the loose ends at the bottom, and let that dry-- Here it is fit into place-- I am much happier with this attempt. It may be more uniform than it really should be, but it will be easy to go back and make it a little "lumpy" if I decide it needs it. Here's a view from inboard-- As I finish up the hammocks I'm adding the capstan bars to the capstan. It's always one of the things on a model that catches your eye, and I've been waiting a long time to add this touch! I cut some blanks, and test fit a few times to get the length I thought was appropriate. They look pretty chunky, but they haven't been tapered or rounded yet, hence they are also not glued to the capstan yet-- I numbered each hole and bar on the underside just in case it matters which one goes where-- As the afternoon light starts to fade-- That's all for now. Ron
-
Continuing with hammock cranes. I was able to thread the three outboard lines and test the hammock covering cloth. I'm not truly happy with the covering cloth, I may redo that, but I do like the overall look-- It was blackening residue in the holes that was making it so hard to thread the line. And the end caps were clogged with Tung oil finish. I had to carefully try and get the drill bit through the holes and clean them out. The angle wasn't exactly right, and I probably should have just twisted everything out and re-glued them. Some became loose anyway (and many bent this way and that-thankfully none broke). But after clearing the holes, I found that I could get the thread through. By the last one, I found that with the tip just stiffened by wax, rather than CA glue, I could get them through quite well--didn't need to push and pull with the tweezers. The CA, though it stiffened the end, did increase the diameter a smidge. Here are the first set of lines through, and the next set of hammock cranes glued in. After all the lines are threaded, and the cloth in, I'll knot off the ends of the lines-- Now I'm off with my daughter to my parents' house in Rochester to try and see the eclipse. It's supposed to be cloudy, but maybe we'll get lucky. If not, we'll still have a nice, if brief, visit with my folks. Hoping the traffic will be manageable, but it probably will be pretty bad. All for now, Ron
-
Congratulations, B.E. She looks great. Ron
- 614 replies
-
- Indefatigable
- Vanguard Models
-
(and 1 more)
Tagged with:
-
Thanks Mike! Continuing on with the hammocks, I made a line of clay, which fit between the hammock cranes-- I wrapped this in the black painted Silkspan and tested the fit. It looks just okay. I may work a bit on the "wrinkles"-- I removed the clay/paper, realizing it would be much easier to run the line through all the hammock cranes without having it in the way. And it was FAR more difficult than I anticipated. I spent hours trying to come up with a way of stiffening the end of the line with superglue, and cutting a point on it, but the holes in the cranes were just too small, and some had become partially blocked with blackening deposits (I think). I spent a lot of time with a pin trying to open the holes--very awkward with them glued in place. Some cranes came loose from the rail, or bent (though easily re-straightened). I even tried supergluing a strand of fly tying thread to the end of the line to lead it through the holes, but that failed like all the other attempts. I finally searched for a thinner line in my stock, and found one. It was just enough thinner to work-- Hopefully I can get through the rest of the holes, and finally see what this looks like with the hammock paper inside. Also, trying to finish everything on the deck before rigging begins, I glued some eyebolts and rings to the deck binding strakes, and some to the channels, which can be seen in the photos. All for now, Ron
About us
Modelshipworld - Advancing Ship Modeling through Research
SSL Secured
Your security is important for us so this Website is SSL-Secured
NRG Mailing Address
Nautical Research Guild
237 South Lincoln Street
Westmont IL, 60559-1917
Model Ship World ® and the MSW logo are Registered Trademarks, and belong to the Nautical Research Guild (United States Patent and Trademark Office: No. 6,929,264 & No. 6,929,274, registered Dec. 20, 2022)
Helpful Links
About the NRG
If you enjoy building ship models that are historically accurate as well as beautiful, then The Nautical Research Guild (NRG) is just right for you.
The Guild is a non-profit educational organization whose mission is to “Advance Ship Modeling Through Research”. We provide support to our members in their efforts to raise the quality of their model ships.
The Nautical Research Guild has published our world-renowned quarterly magazine, The Nautical Research Journal, since 1955. The pages of the Journal are full of articles by accomplished ship modelers who show you how they create those exquisite details on their models, and by maritime historians who show you the correct details to build. The Journal is available in both print and digital editions. Go to the NRG web site (www.thenrg.org) to download a complimentary digital copy of the Journal. The NRG also publishes plan sets, books and compilations of back issues of the Journal and the former Ships in Scale and Model Ship Builder magazines.