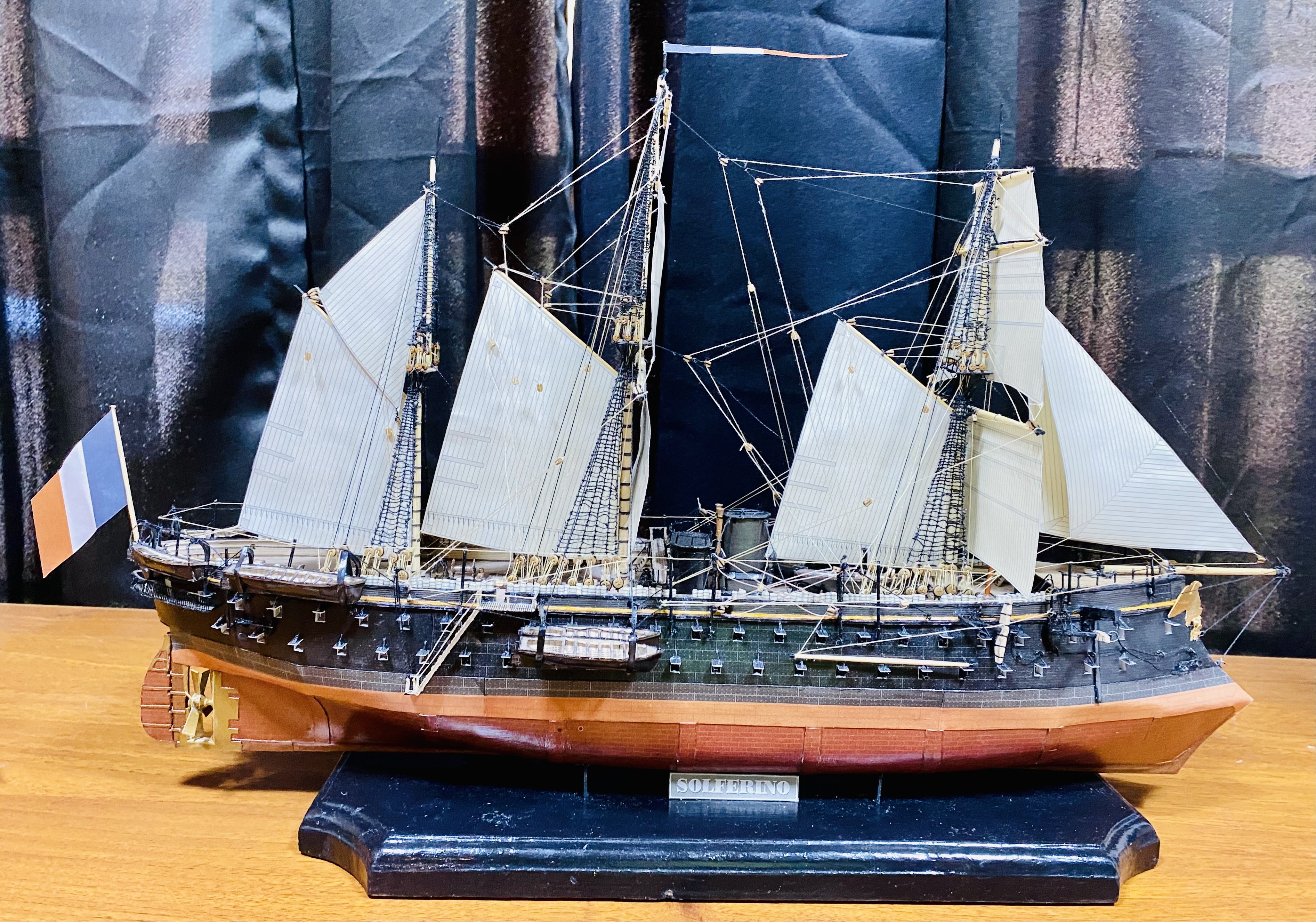
GrandpaPhil
NRG Member-
Posts
5,779 -
Joined
-
Last visited
Content Type
Profiles
Forums
Gallery
Events
Everything posted by GrandpaPhil
-
Greetings! Orel makes a card kit of the Brooklyn. Their kits are really nice. According to this picture off the Naval Encyclopedia website, there is a canvas cover over the boat.
-
Making progress on the bulkheads and the doors: I’m sort of working on the doors assembly line fashion. I am cutting out the fronts, including the slots in the doors, layering them onto a piece of a box and then cutting out the backs and then layering that onto the door panels after I cut them out. After I get all of them cut out like that, I’ll paint them all forest green. Next, I will make handles and hinges, which are already transferred to cardstock. I’ll make the rivets by indenting them with a pick. Then I’ll paint them black and install them. All doors will be shown open, since I already took the time to make an interior. I’ll finish carving all the door frames after that.
-
Do you have a copy of Zu Mondfeld’s Historic Ship Models? If so, there is a great jig detailed in there for making ladders. I have used it in the past with great success. I have also duplicated the Amati method of making ladders in my current build. It has worked quite well for me. Both have some setup, but both are conducive towards making ladders that are evenly spaced and properly squared up.
-
Here are the end pieces of the decks, some painting and detailing still pending, and all door/window frames, in cardstock, glued to 1/16 basswood, as well as the majority of the quarter badges and Elizabeth I’s monogram: From the scroll work left over from when I did the learn to carve tutorial on this site, you may assume that I have had this piece of basswood for several years. By the way, if you would like to learn to carve, the learn to carve tutorial group on this forum is a most excellent resource and way to learn to carve. It is how I learned to carve. For the doors, I am cutting out the slots on the cardstock and gluing to thin card from a box, cutting it out and gluing another slotted piece to the back of it. The handles will be shaped annealed steel wire and the hinges will be cardstock that has already been copied directly from the plans. The frames and badges will be antique gold by Delta Ceramcoat and the doors will be painted forest green like the ones below deck.
-
Many things are slow to change, especially if it works well.
- 508 replies
-
For small lines like that, I have used sewing thread treated with beeswax, or with thinned down PVA glue added after installation. For small lines that don’t have attachment points and you don’t want tension on, I have prestretched sewing thread on a building board and treated it with thinned down PVA glue, before cutting to length and installing. Both methods have worked well for me in the past.
-
HMS SUSSEX by KarenM - FINISHED - 1:48
GrandpaPhil replied to KarenM's topic in - Build logs for subjects built 1501 - 1750
Congratulations! Very well done! -
How to measure masts for Sovereign of the Seas
GrandpaPhil replied to Andy Whincup's topic in Masting, rigging and sails
Which plans of the Sovereign of the Seas? -
Congratulations! Very nicely done! Excellent work!
- 589 replies
-
- le gros ventre
- cargo
-
(and 1 more)
Tagged with:
About us
Modelshipworld - Advancing Ship Modeling through Research
SSL Secured
Your security is important for us so this Website is SSL-Secured
NRG Mailing Address
Nautical Research Guild
237 South Lincoln Street
Westmont IL, 60559-1917
Model Ship World ® and the MSW logo are Registered Trademarks, and belong to the Nautical Research Guild (United States Patent and Trademark Office: No. 6,929,264 & No. 6,929,274, registered Dec. 20, 2022)
Helpful Links
About the NRG
If you enjoy building ship models that are historically accurate as well as beautiful, then The Nautical Research Guild (NRG) is just right for you.
The Guild is a non-profit educational organization whose mission is to “Advance Ship Modeling Through Research”. We provide support to our members in their efforts to raise the quality of their model ships.
The Nautical Research Guild has published our world-renowned quarterly magazine, The Nautical Research Journal, since 1955. The pages of the Journal are full of articles by accomplished ship modelers who show you how they create those exquisite details on their models, and by maritime historians who show you the correct details to build. The Journal is available in both print and digital editions. Go to the NRG web site (www.thenrg.org) to download a complimentary digital copy of the Journal. The NRG also publishes plan sets, books and compilations of back issues of the Journal and the former Ships in Scale and Model Ship Builder magazines.