-
Posts
2,425 -
Joined
-
Last visited
About dvm27
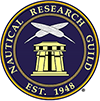
- Birthday 04/05/1954
Profile Information
-
Gender
Male
-
Location
Baltimore, MD
-
Interests
17th and 18th century naval architecture
-
dvm27 reacted to a post in a topic: Fair American by JLong - Model Shipways - 1:48
-
CiscoH reacted to a post in a topic: Fair American by JLong - Model Shipways - 1:48
-
Chuck reacted to a post in a topic: Fair American by JLong - Model Shipways - 1:48
-
Those are fantastic upgrades Jason. The appearance of the rigging is greatly enhanced by the upgrade in blocks. For the fuzz, try flicking a Bic lighter over them very them briefly. The fuzz will quickly melt away. Do some practice ones off the model first though. After a while you'll get comfortable enough to do this on the model.
-
dvm27 reacted to a post in a topic: Sloop Speedwell 1752 by Chuck - Ketch Rigged Sloop - POF - prototype build
-
dvm27 reacted to a post in a topic: HMS ANSON 1781 by albert - 1/48 - 64 guns
-
dvm27 started following Loreley 1884 by Ilhan Gokcay - 1/75 - Scale Steam Yacht
-
dvm27 reacted to a post in a topic: Le Rochefort by No Idea - 1/24th Scale - First POF Build
-
dvm27 reacted to a post in a topic: L'Amarante by marsalv - 1:36 - POF
-
dvm27 reacted to a post in a topic: HMS Winchelsea by Greg M - 1/48 scale
-
dvm27 reacted to a post in a topic: HMS Cumberland 1774 by Jack H - 1:36 &1:48 - POF - kit development for True Image Models
-
CiscoH reacted to a post in a topic: Syren Ship Model Company News, Updates and Info.....(part 2)
-
dvm27 reacted to a post in a topic: HMS Thorn by Kevin Kenny - 1:48 scale - Swan-class - David Antscherl practium
-
KentM reacted to a post in a topic: HMS Thorn by Kevin Kenny - 1:48 scale - Swan-class - David Antscherl practium
-
mort stoll reacted to a post in a topic: HMS Bellerophon 1786 by AON – scale 1:64 – 74-gun 3rd Rate Man of War - Arrogant-Class
-
AON reacted to a post in a topic: HMS Thorn by Kevin Kenny - 1:48 scale - Swan-class - David Antscherl practium
-
If I'd taken the time to blog in addition to building the prototype Swan class model I'd still be building her! Not only have Kevin's modeling skills improved dramatically but his video work has progressed from amateur to pro.
- 1,082 replies
-
hollowneck reacted to a post in a topic: HMS Harpy 1796 by Blue Ensign – FINISHED - Vanguard Models - 1:64 scale
-
thibaultron reacted to a post in a topic: Syren Ship Model Company News, Updates and Info.....(part 2)
-
Canute reacted to a post in a topic: Syren Ship Model Company News, Updates and Info.....(part 2)
-
Congratulations on the completion of yet another fine build, B.E. A very clever presentation as well, saving you a lot of vertical space!
- 332 replies
-
- Harpy
- Vanguard Models
-
(and 1 more)
Tagged with:
-
For anyone else enchanted by this lovely model feel free to check out this video on YouTube https://www.youtube.com/watch?v=GPCAArQ7APY. It depicts both of the Phil Reed's Speedwell models (Chuck's version and a Speedwell on a roiling sea). Notice the lovely catenary of the rigging, something I believe you can only do with wire rigging.
-
I have no dust collection system either Shawn so I typically do my fairing ourdoors. Obviously not ideal for your Nebraska winters but anything above 50 degrees was fine with me. If you're using cedar I think 40 grit is a bit aggressive and I'd start with 80. Repeatedly applying pencil marks to the frames will show you the low spots. Ultimately, the sound of the fine paper (220 grit) and running your hands over the surface will tell you when you are done. Start by fairing the midships frames then proceed to the fore and aft frames. If one frame still has pencil marks while those fore and aft of it are faired then re-evaluate the frame. If it was installed with an inward cant then all the other frames could be affected. In my Speedwell model I had to replace a fore frame for this reason during the fairing process.
-
Sovereign of the Seas 1637 by Tuvok - 1:78
dvm27 replied to Tuvok's topic in - Build logs for subjects built 1501 - 1750
That's fifteen years well spent Alessio! Welcome aboard and I look forward to future updates.
About us
Modelshipworld - Advancing Ship Modeling through Research
SSL Secured
Your security is important for us so this Website is SSL-Secured
NRG Mailing Address
Nautical Research Guild
237 South Lincoln Street
Westmont IL, 60559-1917
Model Ship World ® and the MSW logo are Registered Trademarks, and belong to the Nautical Research Guild (United States Patent and Trademark Office: No. 6,929,264 & No. 6,929,274, registered Dec. 20, 2022)
Helpful Links
About the NRG
If you enjoy building ship models that are historically accurate as well as beautiful, then The Nautical Research Guild (NRG) is just right for you.
The Guild is a non-profit educational organization whose mission is to “Advance Ship Modeling Through Research”. We provide support to our members in their efforts to raise the quality of their model ships.
The Nautical Research Guild has published our world-renowned quarterly magazine, The Nautical Research Journal, since 1955. The pages of the Journal are full of articles by accomplished ship modelers who show you how they create those exquisite details on their models, and by maritime historians who show you the correct details to build. The Journal is available in both print and digital editions. Go to the NRG web site (www.thenrg.org) to download a complimentary digital copy of the Journal. The NRG also publishes plan sets, books and compilations of back issues of the Journal and the former Ships in Scale and Model Ship Builder magazines.